曾毅 汪祥 李军
(东风汽车公司技术中心,武汉 430058)
摘要:结合军车内饰开发的特殊要求,从吸塑成型工艺常用模具及其产品的试制工艺、产 品特点出发,阐述了吸塑成型工艺结合玻璃钢模具是应对军车新车型内饰开发的一种有效手 段,为后续军车项目内饰件试制 QCD 管控提供了有益的借鉴。
关键词:吸塑成型 军车内饰 玻璃钢模具
1 前言
一般来说,民用乘用车内饰开发流程比较完 善,往往需要商品企划部门对技术发展趋势进行 深入分析,并结合市场调研请况,才能形成商品概 念。然后从造型方案评审逐步过渡到详细工程设 计,最终进入样车制造阶段。而在军车开发过程 中,往往是军方提出关键技战术指标,汽车公司针 对性的开展车辆设计,并需要在最短时间内造出 样车供军方评价。这样的开发模式,汽车公司比 较被动,对于内外饰设计尤甚,不仅缺失了商品概 念研究阶段,造型设计及评审也很不完善,缺少必 要的整车内外饰评审以及工程可行性分析,导致 后期改动频繁且比较随意。
这些因素造成了在样车试制阶段,军车内饰 设计输入非常滞后,而且经常发生设计变更,相对 于其它零部件的试制,军车内饰零部件试制周期严重不足。因此,迫切需要找到一种合适的内饰 件试制工艺,既能在短时间内试制出样件,样件还 必须具有较高的性能,能够支持整车完成各种气 候、路况下的整车试验。吸塑成型工艺是一种简 单有效的塑料制品成型工艺,在客车/货车的仪表 板 、立 柱 护 板 、空 调 面 板 及 风 道 、进 气 格 栅 等 内 外 饰零部件制造方面得到了大规模成功的应用,非 常契合军车内饰样件的试制需求。
2 吸塑成型工艺介绍
2.1 吸塑工艺原理
吸塑成型也称真空吸塑成型,是将塑料片材 或板材加热到粘弹性状态,再通过真空吸引、与模 具表面贴合,冷却后获得所需要形状的成型方法, 其工艺原理如图 1 所示。
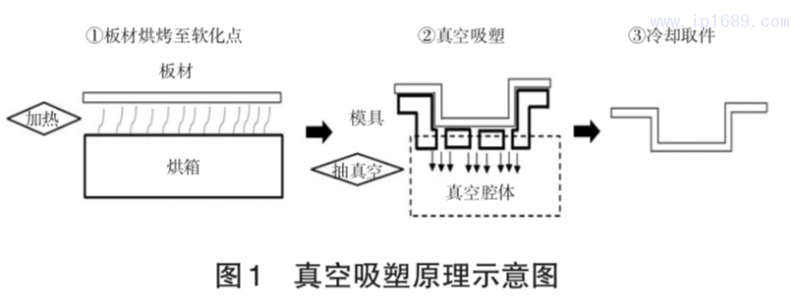
2.2 吸塑成型主要工艺步骤
吸塑成型的工艺步骤主要包括板材准备、板 材烘烤、夹持、真空成型、冷却定型、切边等主要工 序,其主要流程如图 2 所示。
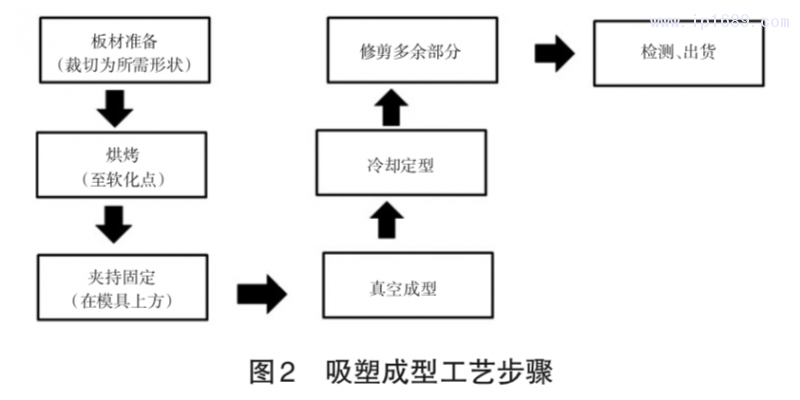
板材:用于吸塑成型的板材主要是热塑性塑 料,军车内饰最常用的是 ABS 板材或 ABS+PVC 革 复合板材。这种材料具有良好的机械性能,成型 温 度 宽 ,易 于 操 作 ,来 源 广 泛 ,是 汽 车 内 饰 件 吸 塑 产品的首选材料。
烘烤:板材加热最常用的加热方式为红外线 加热,要求上下两面受热均匀,确保板材均匀软 化。设备常见的温度设置如表 1 所示。
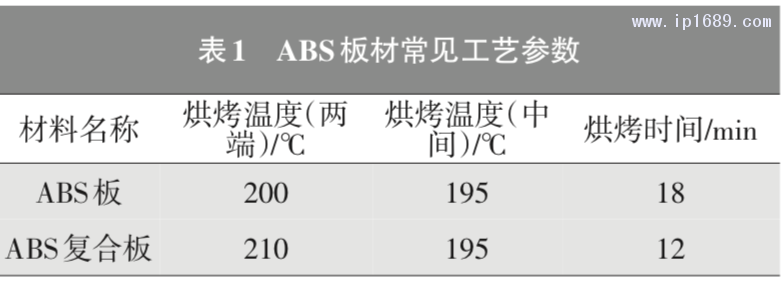
夹 持 \ 吸 塑 :大 规 模 生 产 时 ,在 吸 塑 过 程 中 ,一 般需要专用的工装对烘烤软化的板材进行夹持, 军车内饰开发样件试制数量少,一般为人工手持, 确保板材在吸塑过程中不漏气即可。
冷却:一般采用风冷模式,大型产品可喷淋冷 水进行快速冷却。
切边:大规模生产可采用数控激光切割或机 器人自动水切割等方式进行切边,小批量试制一 般采用人工切边(模具上制作有切边线等特征)。
2.3 吸塑成型模具
不同于其它工艺,吸塑成型只需要单边模具。 吸塑模具包含凸模和凹模两种形式,在成型过程 中,由于板材首先接触模具的部位不同,产品受拉 伸的情况也有所不同,图 3 展示了两种模具形式对应的产品厚/薄部位。由于模具上要开吸气孔,一 般紧贴模具的产品一侧较为粗糙,而另一面则很 光滑。在实际生产时,需要根据产品外观、性能的 具体需求,来选择合适的模具方案。
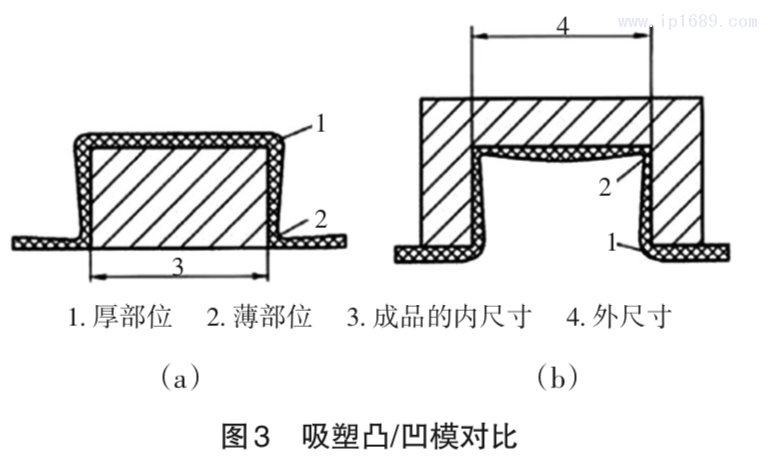
吸塑成型采用真空力作为成型力,相对于注
塑成型几十兆帕、模压成型十几兆帕的成型力,吸 塑成型模具在成型过程中受力较小,吸塑模具的 材质要求也较低。一般在大规模工业化生产中, 以铝合金模具为主,而在小批量生产和试生产过 程中,以玻璃钢模具为主。玻璃钢模具的主要制 作步骤如图 4 所示。
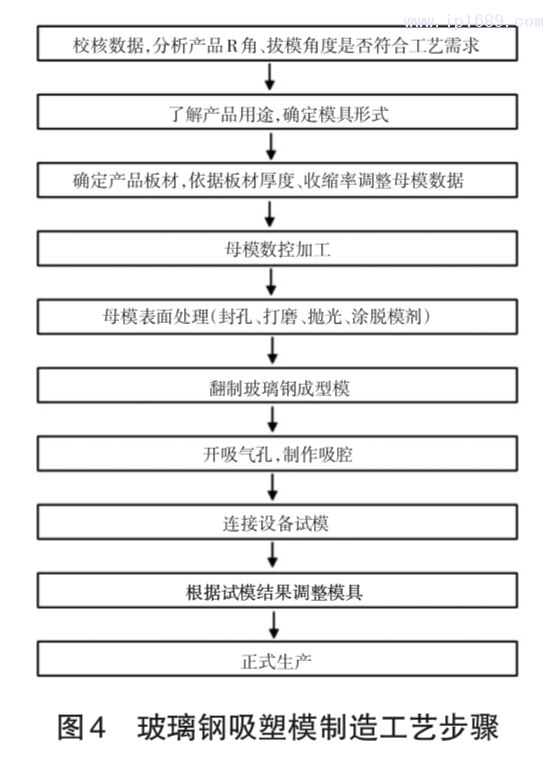
2.4 吸塑成型工艺的主要优点
a. 模具费用低。
吸塑成型只需要凸模或凹模单侧即可,模具 少了一半,自然成本低;
材质便宜:由于吸塑成型压力小,模具材质不 需要特别高的机械强度和表面硬度,选择范围广, 成本低;
模具结构简单:吸塑模具不需要定位、导向机 构,也不需要送料、顶出以及冷却机构,相比注塑模 具,吸塑模具结构要简单的多,从模具设计、制造、 装配各个环节都可以节省大量费用,因而成本低;
维护保养便宜:由于成型压力小,吸塑模具使 用过程中损耗小,维护保养便宜。
b. 产品开发周期短,改进方便
吸塑模具结构简单,设计制造方便,制造周期 一般不超过 20 天;
由于模具无导向机构、顶出系统、冷却水道,相比 于注塑成型,吸塑模具修模限制因素很少,修模方便;
c. 设备投资少
吸塑成型只需要加热设备、真空装置及其它 辅助设备即可,投资规模很小。对比之下,一台大 型产品的注塑成型机价格就是几百万甚至上千万 的设备投资,前者优势明显;
吸塑成型设备适应性强,大/中/小产品均可制 作。而注塑成型不同设备只能适应对应重量的产 品:小设备无法生产大产品,大设备生产小产品则 很难控制工艺,而且经济上也非常不划算。
3 军车内饰开发特点
3.1 设计输入滞后
内饰装配以白车身作为基准,因此一般需要白车身边界条件冻结才能开展内饰设计;而白车身边 界冻结的前提是底盘、电器、发动机等各系统把装 配/固定需求全部明确之后才能开始设计。一般来 说,相对于其他系统,内饰设计是最后开展的。
3.2 设计缺乏校核
由于军车的开发极为紧张,一般从接到开发任务到出样车只有半年时间,留给设计开发的时 间不多,留给车身内饰件设计的时间更少。通常 设计部门只能尽量在样件制作之前完成产品 3D 数 据 的 设 计 ,尺 寸 链 的 计 算 、制 造 可 行 性 分 析 、装 配可行性分析都来不及开展,为后续样件制作埋 下大量隐患。
3.3 样件制造时间不足
为了满足军方评审、夏季高温试验、冬季寒区试验等硬性节点要求,在前述各种不利条件下,军 车内饰还必须在很短的时间内制造出合格样件。 一般留给包含仪表板总成、副仪表板总成、顶棚、 前围/侧围/后围护板以及车门护板等几十种大型 内饰部件实际制作时间都不足 45 天,有些项目甚 至只有 30 天左右。
3.4 样件性能要求高
由于军车需要在各种非铺装路面甚至无路情况下行驶、试验,军品内饰所要承受的各种颠簸、 震颤、大幅度横移/扭转是乘用车项目无法比拟的, 因而对于样件本身的机械强度、可靠性、耐久性提 出了很高的要求。通常用于乘用车试制的快速成 型工艺,如 CNC 快速成型、硅胶模真空浇注、3D 打 印等,不适合用于内饰大面积承力部位,只能用于 个别装饰性部件。
3.5 白车身精度较差
不同于乘用车试制,一方面,军车的外形尺寸要 大 的 多 ,成 型 困 难 ;另 一 方 面 ,军 车 即 便 是 批 量 生产以后订货数量也很少,军车白车身不会像乘 用车那样投入大量的冲压成型模具、焊接工装和 其它辅助工装。军车钣金件的试制一般采用少量 的 拉 延 模 、结 合 胎 模 、手 工 成 型 制 作 ,而 焊 接 夹 具 也仅限于重要大总成等关键部位和工序。所有这 些因素导致军车的白车身精度无法达到乘用车的 标准,导致后期内饰装配定位、间隙面差效果很难 令人满意。
3.6 固定方式多采用螺栓连接而非卡扣连接
内饰与白车身的固定,一般采用螺栓连接,而非 民用车的卡扣连接方式,主要是从可靠性和维修方 便性考虑。军车行驶路况多为非铺装路面,车身颠 簸、晃动幅度远大于民用车,塑料卡扣连接的可靠性
不能满足需求;在拆卸时,由于需要采用强拔方式, 卡扣连接方式会对卡扣本体或与其连接的结构造成 损伤,多次拆卸后结构会损坏或失效。而采用螺栓 连接方式,取下螺栓外部的装饰帽后,可直接采用螺 丝刀取下螺丝,多次拆装,对紧固性能无影响。
3.7 变型车/改装车多
军车项目在研制一款车型时,会针对不同的作战需求或用户需求,出现大量的变型车、改装 车,又增大了内饰设计、制造及匹配的难度。
3.8 生产批量小
军车项目单次采购数量一般比较少,临时性 采购比较多,要求生产单位具有很强的灵活性,最 好能够将试制与小批量试生产结合在一起。
4 结束语
军车内饰试制的要求与大型客车/商用车的 内饰开发有一定相似度,而从吸塑成型工艺在客 车/商用车领域的成功应用经验来看,吸塑成型工 艺不仅可以满足样车试制阶段周期短、修模多的 特点,吸塑板材本身很高的强度、可靠性也可以满 足军车耐久试验的要求,从质量、周期、费用 3 个方 面,吸塑成型工艺完全满足军车内饰开发需要:
a. 试制质量方面
样件制作:军车内部一般比较规整,内饰护板 很少出现剧烈的曲面变化或是锐角、负角,适于吸 塑成型工艺;
样件装配:吸塑零部件一般采用自攻钉加堵盖 的方式装配,对于被装配零件的容差性、维修性好;
样件调整/改制:吸塑工艺采用单边模具,相对 于其它工艺少做半边模具,模具的改制、调整比较 容易。
b. 试制周期方面 模具制作周期:母模一般采用数控加工来制
作 ,在 不 考 虑 排 班 、排 产 的 情 况 下 ,加 工 周 期 一 般 为 1 周,一般为两周;翻制玻璃钢模具需 1 周,一套 吸塑成型玻璃钢模具的制作周期仅需 2-3 周;
产品制作周期:吸塑板材的采购可与模具制 作同步进行,吸塑产品的制作 1 天即可完成;
总的加工周期:在极限状态下,一个全新的产 品半个月之内就可完成制作,并可小批量生产。
c. 试制费用方面
模具方面:相对于其它塑料成型工艺,吸塑模 具只需要半套,因而成本较低;而玻璃钢吸塑模具 本身重量就相对较轻,主要依靠手工成型,设备投 入 极 少 ,在 相 同 的 使 用 寿 命 、可 靠 性 条 件 下 ,成 本 就更加低廉了;
产品方面:与注塑成型相比,吸塑产品自动化 程度较低,人工工时费用在产品中所占比重较高, 材料利用率较低,相同重量的塑料制品,单价略高;
总 体 成 本 :综 合 考 虑 模 具 、产 品 费 用 ,吸 塑 工 艺在小批量生产时具有明显的成本优势。
参考文献:
[1]欧永杰 . 吸塑成型在客车上的应用[ J]. 商用汽车杂志, 2006(1):104-105.
[2]黄怀安, 王国慧, 袁贵兵 . 吸塑工艺及在汽车上的应用 [ J] . 城市车辆, 1997( 2): 34- 36.