刘敬祺1,胡光良2,张跃飞1,严胜义2,朱少军2
(1.浙江工贸职业技术学院,浙江温州325003;2.浙江长江汽车电子有限公司,浙江温州325025)
摘要:汽车旋钮作为内饰面板上重要的功能零件,其操作表面常设计为多齿形结构并采用电镀后处理工艺,以赋予产品独特的人机交互体验。为了顺利成型脱模,齿形结构的成型应设计多向抽芯机构,并严格控制行位分型段差,以保证产品成型质量。以某汽车品牌内饰旋钮为例,分析建立了一套关于齿形结构与抽芯行位数量的计算方法,以此确定最优行位抽芯方案。行位成型齿面采用电火花放电成型工艺,根据加工对象离散程度,实际生产分为分体式加工和组合式加工。其中组合式加工需要五轴数控加工制备整体式电极,依赖模具装配关系组合行位实现一体化成型。通过合理拆分成型零件结构及加工定位孔系以实现行位成型过程的可靠定位,以此为基础设计了一套基于组合加工的多齿形汽车旋钮注塑模具,并详细叙述了模具结构设计方案。实践表明,组合式加工工艺比分体式加工在生产效率及质量方面均有明显提升,设计制造的模具安全可靠,塑件成型满足预期要求,分型段差明显改善,可控制在0.02mm以内,电镀表面质量良好,无积镀、毛刺、鼓包、起皮等缺陷。
关键词:汽车旋钮;多齿形结构;电火花放电;组合加工;多向抽芯
汽车旋钮作为汽车内饰面板上的一种交互装置,常被应用于车辆娱乐、空调、导航等多个系统,承担音量、温度、风速等参数的调节功能。在当今车辆设计日趋人性化、智能化的大背景下,汽车旋钮要求易于操作和辨识,以提高驾驶者在车辆控制过程的便利性和安全性。同时,不同品牌和车型旋钮要求具有个性化造型和设计风格,在保证其功能性的同时,需兼顾视觉效果和美学价值,以吸引用户的目光[1]。
因此,常见旋钮通常为圆柱形,并增加纹理设计及特殊表面工艺,以提供更好的人机交互体验。多齿形结构常见于旋钮操作表面,赋予其不同的触感及质感,提供产品防滑及防磨损功能[2]。随着加工技术的不断发展,齿形实现自由定制,产品样式及细节体现更为丰富,通过表面电镀进一步赋予塑件金属质感,增添产品的高级感和奢华感,传递精工细作的品牌价值,可帮助企业塑造市场竞争力和品牌形象[3]。
为保证塑件注塑后顺利脱模,多齿形汽车旋钮须采用行位多向同时抽芯成型,不同齿形抽芯难易程度各异,需要视结构具体分析,相关设计案例如图1所示。有的旋钮结构仅需3个行位即可成型,有的则需要6个,更多的甚至需要10个行位成型。基于电镀工艺的特殊要求,模具结构设计与成型质量的要求较高,尤其是成型零部件的加工及装配需保证极高质量及精度,不允许过大的分型段差以及锐边、棱角等缺陷[4]。笔者以某汽车品牌电镀操作旋钮为例,结合产品结构和设计要求明确了塑件多行位抽芯成型方案,分析了不同加工工艺路线下模具成型零件加工效率以及产品成型质量,最终确定了组合式加工工艺,并以此为基础详细阐述了模具总体设计方案。
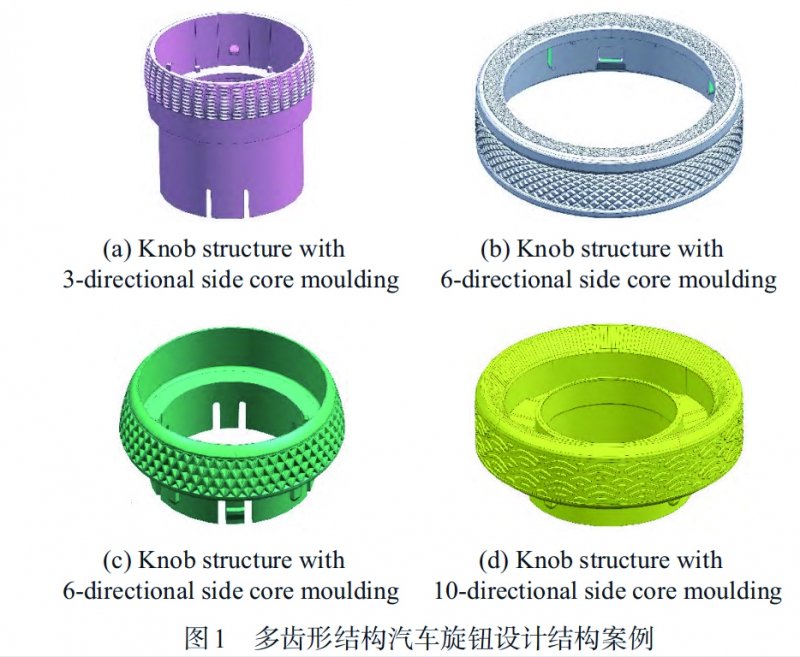
1塑件结构分析
研究对象为一个需六向抽芯成型的多齿形汽车旋钮,结构如图2a所示,外形尺寸为42.7mm×17.2mm,净重5.8g,年产量50000件,模具设计寿命30万次。塑件操作表面周向均匀分布着6行120列齿形纹理结构,齿形轮廓为四面等腰锥体,具体如图2b所示。齿底截面尺寸为0.9mm×0.9mm,齿顶截面尺寸为0.2mm×0.2mm,齿高0.6mm,同一圆周截面对立齿面夹角α为71.37°,相邻齿间中心线夹角Y为3°,齿根间距为0.125mm。
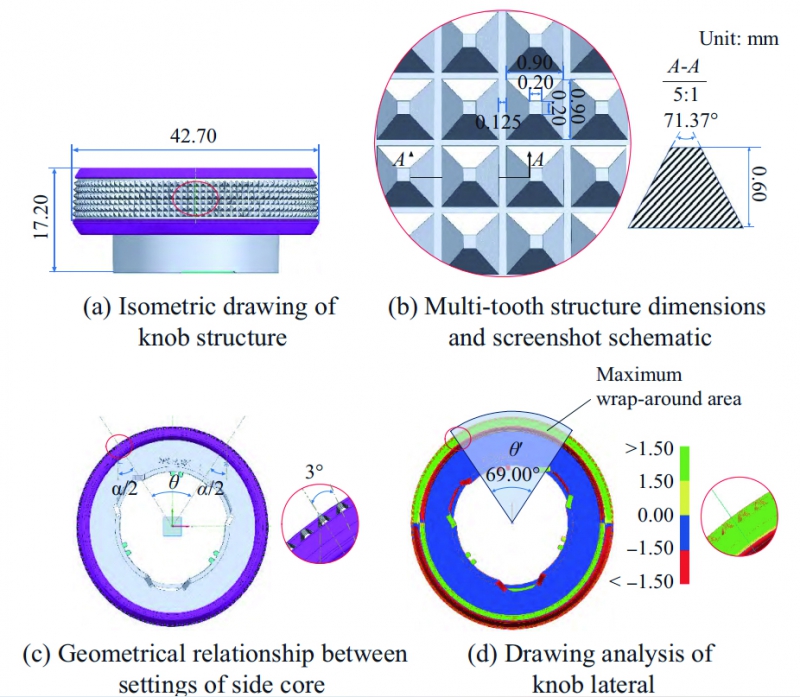
塑件材料选用电镀级聚碳酸酯/丙烯腈-丁二烯-苯乙烯共聚物(PC/ABS)(SABIC公司,MC1300100),要求齿形特征成型面为镜面,其余为光面;整体无毛刺、飞边,电镀后无积镀、毛刺、鼓包、起皮等缺陷,重点关注成型齿形的相邻行位分型处。实践表明,瓣合行位的成型段差直接影响电镀质量。较大分型段差或局部锐边、棱角会引起电荷集聚效应,段差现象进一步加剧,产生积镀、毛刺或烧焦现象,不仅大大影响产品美观,还会降低镀层结合强度进而出现鼓包、起皮、脱落等缺陷,严重影响产品的使用体验。因此,模具设计及制造过程多行位加工装配精度是保证其复杂多齿形外观面成型质量的关键[5],实际生产过程应控制段差小于0.02mm。因涉及曲面测量,采用显微放大镜目视观察控制成型段差。
据经验可知,行位设置越多,对模具装配及成型质量越不利,应根据塑件齿形参数确定所需最少行位数量[6-7]。为保证结构顺利成型,行位齿形的脱模斜角β为1.50°。根据图2c及图2d所示的几何关系可知,行位分型线应设置在齿形结构的齿根中心[8],并且满足式(1)~式(4)时,行位包覆塑件表面齿形结构,可顺利抽芯脱模。

式中:θ为行位包覆区域内相距最远两齿形的中心线夹角;n为行位最大包覆齿形数(向下取整);z为齿形总列数;θ'为行位最大包覆角;m为顺利抽芯所需的最少行位数(向上取整)。
本例α=71.37°,β=1.50°,γ=3.00°,z=120,联立各式计算得最大包覆齿数为23齿,对应最大包覆角为69.00°,因此可确定塑件顺利成型所需最少行位数为6块。
2多齿形结构行位加工工艺路线分析
随着现代模具制造工艺的不断发展,三维曲面在模具型芯型腔的应用日渐广泛。作为模具加工的主要手段,数控加工(CNC)和电火花加工(EDM)各有特色。CNC擅于加工较为平坦型腔面,加工质量及效率高,也可用于EDM电极的制造。对于模具复杂型面、夹角、窄缝、深坑等部位加工,必须由EDM完成。EDM成型几何形状虽不受限制,实际生产仍应考虑电极制造难易程度。对于本试验用多齿形旋钮塑件,按照最优行位抽芯方案成型需设置6个行位,因此单个行位成型面上均匀分布着20列齿形沟槽,如图3a所示。齿形结构中心线各异,考虑零件结构特征与成型技术经济性,宜采用EDM成型。实际生产时,根据加工对象离散程度,模具成型零件含有分体式加工和组合式加工两种工艺路线。
2.1分体式加工工艺
分体式加工即每次EDM放电面向单个行位加工,所有行位完成单体离散加工再行装配。电极成型面结构与塑件操作表面局部齿形类似。采用普通三轴CNC加工时,刀具侧刃加工齿形表面过程近似于行位抽芯,故同样遵循式(1)的几何关系。刀具侧刃角β’一般为5°~15°,远大于行位齿形脱模斜度β,故两侧边缘数齿实际加工会发生过切现象,如图3b所示。选用细长刀具虽可缩小刀具侧刃角避免过切,但存在断刀、弹刀风险及表面加工不良缺陷[9-10]。因此,包含单个行位完整齿形的电极受限于刀具及机床制约难以直接加工到位,采用五轴CNC加工同样不符合成型经济性的原则,故必须通过拆分电极结构以实现,具体如图3a及图3c所示。
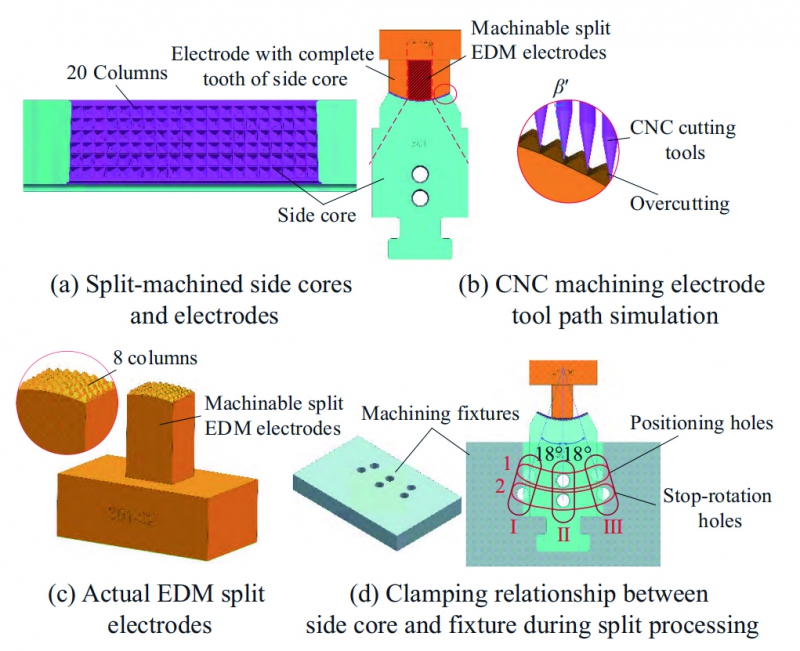
分体式加工即每次EDM放电面向单个行位加工,所有行位完成单体离散加工再行装配。电极成型面结构与塑件操作表面局部齿形类似。采用普通三轴CNC加工时,刀具侧刃加工齿形表面过程近似于行位抽芯,故同样遵循式(1)的几何关系。刀具侧刃角β′一般为5°~15°,远大于行位齿形脱模斜度β,故两侧边缘数齿实际加工会发生过切现象,如图3b所示。选用细长刀具虽可缩小刀具侧刃角避免过切,但存在断刀、弹刀风险及表面加工不良缺陷[9-10]。因此,包含单个行位完整齿形的电极受限于刀具及机床制约难以直接加工到位,采用五轴CNC加工同样不符合成型经济性的原则,故必须通过拆分电极结构以实现,具体如图3a及图3c所示。
拆分电极共包含8列齿形,左右剩余6列齿形通过工件旋转完成加工,应定制配套专用夹具。夹具具体结构及加工原理如图3d所示。夹具加工两行三列共6个孔位:第1行为定位孔,第2行为止转孔;Ⅰ,Ⅱ,Ⅲ三列分别对应行位工件左偏18°、竖直状态及右偏18°三种装夹状态,行位上对应加工相应孔位。单个行位采用图3所示拆分电极,旋转3次完成EDM加工,每次旋转后用2组销钉将行位可靠固定以确保加工精度。为避免EDM放电过程的损公现象以保证所有齿形结构加工一致性,每块行位需要经历粗加工和精加工两道工序,粗加工每次旋转需更换一块电极,精加工仅需一块电极完成。
由于分体式加工工艺需加工多块电极,且加工过程涉及多次装夹、定位,加工累计误差较大。进一步考虑模具装配、磨损的累计误差,最终成型旋钮行位分型段差必超过0.03mm。因此,分体式加工工艺往往难以充分满足电镀齿形塑件较高的加工精度以及表面质量要求。
2.2组合加工工艺
组合式加工即每次EDM加工面向所有行位加工。行位事先按照模具装配关系组合,通过整体式电极在一次装夹中完成所有组合工件的放电成型[11-12]。该工艺方法精密、高效,但需要模具结构同步优化改善。采用整体电极结构以及工件组合关系如图4所示,其中电极外齿形结构与塑件操作表面基本一致,采用传统三轴CNC加工技术仍然难以完成。但随着加工技术日趋成熟,五轴CNC技术日渐普及,机床刀具包含x,y,z三个移动轴加任意两个旋转轴。相对于三轴CNC,五轴机床不改变工件相对位置即能实现空间任意角度的线性插补运动[13-14],不会发生刀具干涉过切现象,对上述结构整体式电极能够直接加工成型。
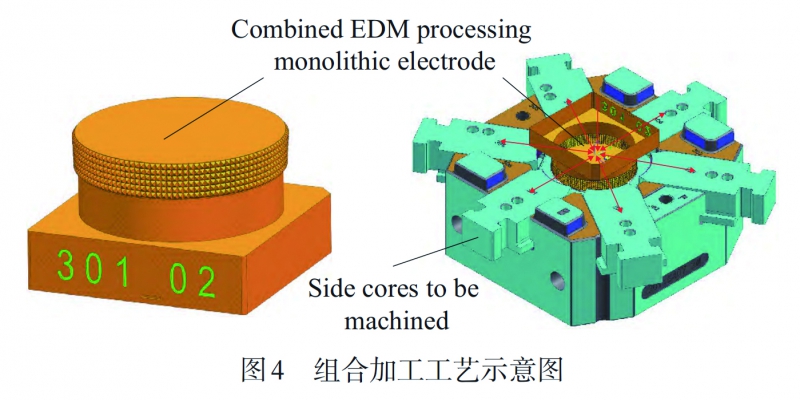
所有行位装配并精加工端面内圆后,同时后退一段电极放电安全距离,随后整体式电极沿z轴下移至行位同一水平面开始组合放电加工。加工任一行位时,电极通过x,y轴联动向该行位的后撤方向移动,完成对该行位独立加工。然后回到模具中心开始下一行位加工,直至所有行位齿面成型。通过整体式电极组合放电,所有行位仅需经历一次粗加工以及精加工即可完成,减少电极数量以及EDM放电次数,生产效率大幅提高。电极齿形轮廓与塑件齿形尺寸误差,即EDM加工放电间隙(又称火花位),粗加工放电间隙一般为0.2mm,精加工可达0.1mm。与此同时,采用组合式加工无需制作专用夹具,结合模具装配一次装夹成型,减小了累计加工误差,保证所有行位齿形的加工一致性,有利于提高后续塑件成型质量。组合加工工艺具体制造流程相对复杂,后续结合模具成型零件的结构设计进一步展开。
3基于组合加工的注塑模具结构设计
基于上述论述,组合式加工工艺一方面需五轴CNC加工的整体式电极,另一方面需要通过成型零件合理拆分设计以确保行位加工装配精度[15]。以本塑件为例,基于组合加工的注塑模具结构设计阐述如下。
3.1分型面及型腔布局
图5为塑件分型面及型腔布局示意图。如图5a所示,该塑件的成型需要1个主分型面和6个侧向抽芯辅助分型面,辅助分型面设在齿形结构齿根中心处。主分型面设置使塑件主体在动模模腔内成型,消除了模具合模精度影响,并且便于后续脱模。行位上表面与主分型面平齐,成型部分下表面紧贴图示滑动配合面,有利于模具组合加工的纵向定位。
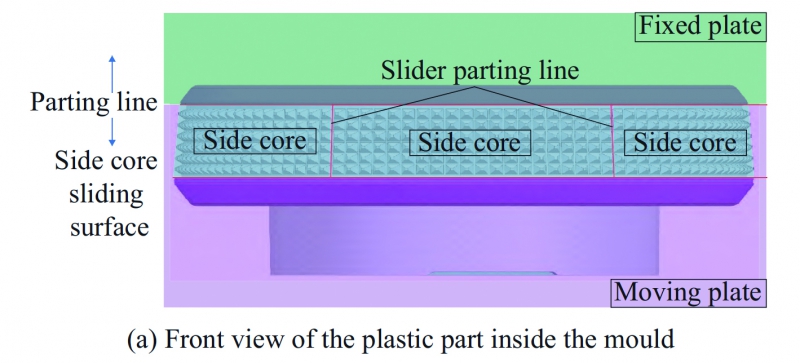
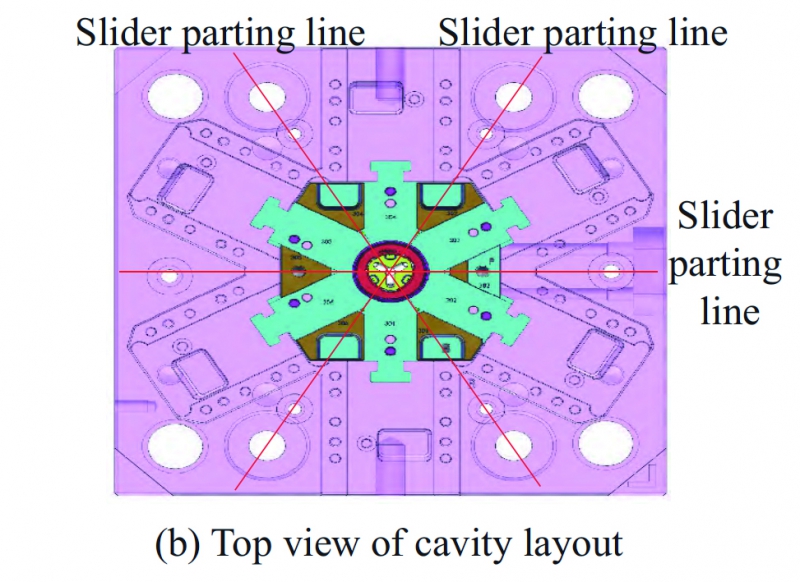
由于塑件成型需多向侧抽芯,齿形结构的成型精度要求较高,模具建议采用一模一腔。如图5b所示,型腔布置在模具中央,四周根据齿形结构保留滑块抽芯安全距离,模具内部空间有效利用,结构设计紧凑,模板尺寸已达300mm×300mm。若采用一模多腔方案,每增设一个型腔均需要配套加工单独型腔板,模具尺寸及修配难度大幅提高,因此采用一模一腔的方案对于模具制造更为经济。
3.2浇注系统及冷却系统设计
模具浇注系统设置如图6a所示。因模具采用一模一腔,故选用大水口进料。主流道长度由定模座板及定模板厚度确定,为避免凝料增多导致成型压力和温度损失过大,一般不宜超过60mm[16]。本例二板厚度和至少为95mm,故采用内径70mm的大定位圈G1,并在定模座板和定模板上分别加工出直孔G2和斜面G3,下沉浇口套G4缩短主流道长度。该类旋钮塑件尺寸较小,外表面为外观面,为保证零件的真圆度,浇口设置在内表面厚胶处,以三点潜伏式浇口进胶。为防止电镀类零件压力过大造成残余内应力,成型时尽量降低零件的注射压力及保压压力,一般不超过40MPa。滑块设计时考虑同步锁紧块锁紧,并设置凹槽限位,防止行位受力产生位移。行位在成型过程受力不平衡性较小且对后期成型塑件影响较小。
塑件属于回转体,熔体进入模腔后热量自模具中心向外发散,对动、定模均采用井字形循环水路进行冷却(如图6b所示),冷却水道直径为8mm,进水温度为80℃。为确保齿形成型精度,试模过程应对模温进行实时监控,确保其波动范围不大于±5℃。在满足整体功能结构布局的基础上,以不干涉为原则,模板上应加工出相应模温测试孔。
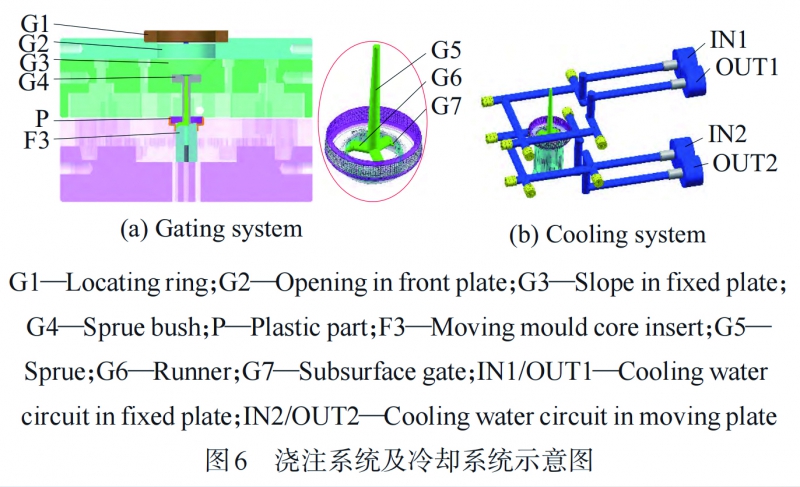
3.3成型零部件设计
考虑模具寿命,成型零部件采用强度高的SKD61,热处理硬度50~54HRC,表面氮化硬度高达60HRC,可保证滑块耐磨性,避免长期工作磨损影响齿形尺寸及表面质量。成型零部件的拆分与制造、定位与装配是模具组合加工设计任务的关键。如图7a和图7b所示,定模模腔可分为定模镶件F1及定模型腔板F2,通过中央镶件孔组合在一起,内部加工有模温监测孔G8,用于放置探针;动模模腔由6个侧型芯F4、动模型腔板F6以及动模拆分镶件F3,F7共同组成,组装后剖视图如图7c所示。6个行位分别安装于动模模腔板对应导滑槽F5。F7镶件横截面为正六边形,6条棱边正对6个行位,上表面高于行位滑动面10mm,与行位成型部分下表面平齐作为其滑动基准面,侧面6个台阶面F9作为行位径向定位基准面。F3镶件上额外设置胶位成型塑件夹持端,待后续电镀完成后去除。
行位设在动模模腔,组合加工关键亦在于动模成型零件制造。拆分后加工制造流程如下。
(1)成型部件离散加工。上述部件单独切割下料。行位成型端面仅加工切削圆弧并保留加工余量,之后模腔板中央镶件孔、T形导滑槽F5以及6个行位间配合斜面采用慢走丝成型,镶件F7上表面、侧面台阶及行位上对应配合面采用工艺磨加工,以确保后续配合精度。
(2)成型部件装夹定位。按上图完成装配,图7c所示即塑件成型位,行位沿各自滑槽后退安全距离即EDM位。为确保组合加工过程的定位需要,行位和动模模腔板上应加工定位孔系F8和F11。加工前,行位下部贴紧基准面F9,不存留任何间隙;利用激光点焊工艺与模腔板固定,随后采用慢走丝同步加工。定位孔位置任意确定,仅需不与其他特征发生干涉即可,但其轴心连线应与行位滑行方向一致,并且间距等于电极放电安全距离4mm。
(3)成型位组合加工。对齐1孔和1′孔轴线,并用定位销钉固定。移除镶件F3及F7,采用慢走丝对所有行位组合形成的完整圆弧面同时精加工,精度达0.01mm,尺寸环真圆度达0.03mm,即可满足后续齿形型面加工形位精度。
(4)EDM位组合加工。行位后退对齐1孔和2′孔轴线,并用定位销钉固定,如图7d所示。整体式电极移至模腔板中心并下降至指定高度,逐一对行位进行侧向放电加工,加工过程参见图4b。此时行位间配合斜面已分离,因电极放电影响,行位在T形槽配合间隙内存在旋转跳动,应进一步设置止转孔系F12,其位置在不发生干涉前提下任意确定,但需注意保持与定位孔系足够的安全距离。放电过程中,对齐行位与模腔板各自止转孔系轴线并用止转销钉加以固定,保证复杂齿形型面加工质量。
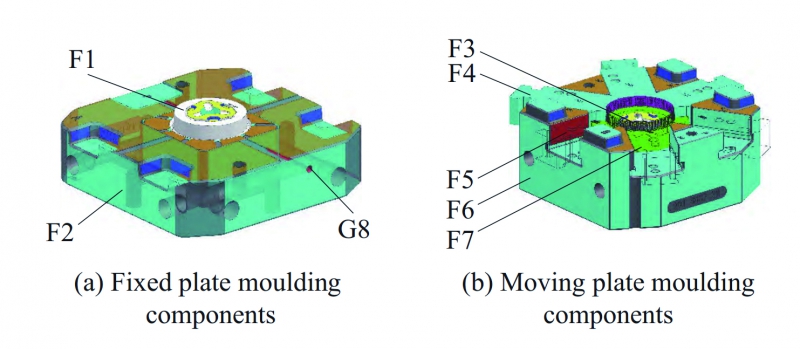
F3 is the same as Fig.6;F1—Fixed mould core insert;F2—Cavity plate;
F4—Side core;F5—T-type slide guide;F6—Core plate;F7—Moving
mould core splitting inserts;F8—Positioning holes inside cores;
F9—Positioning datum;F10—Cavity of electroplating bracket;
F11—Positioning holes in core plate;F12—Stop-rotation holes;
G8—Mould temperature test hole
3.4推出机构设计
该塑件底部壁厚较薄,平均壁厚仅为1.5mm,因此采用扁顶针推出机构。如图8所示,使用了2种截面共6根扁顶针。其中扁顶针E1截面为4mm×1mm,设置在底部壁厚较薄处;扁顶针E2截面为5mm×1.2mm,设置在塑件底部厚胶处(即潜伏式浇口进料的正下方)。两种扁顶针在塑件底部圆周交替对称分布,与行位在脱模方向上无干涉。由于设置电镀夹持胶位F10,该处推出力相对增大,故两侧扁顶针分布夹角应适当缩小以平衡受力。推出机构整体由推板E7驱动,推板导柱E3和推板导套E4导向,带动扁顶针顶出塑件,直至限位柱E12接触动模板,最大顶出距离为30mm。
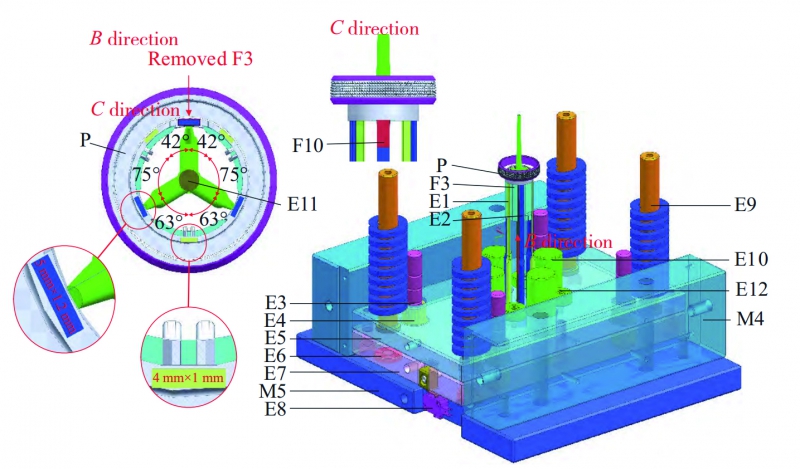
P,F3 are the same as Fig.6;F10 are the same as Fig.7;E1,E2—Ejector
blade;E3—Ejector guide pin;E4—Ejector guide bush;E5—Retaining
plate;E6—Stop pin;E7—Ejector plate;E8—Limit switch;E9—Return
pin with compressed spring;E10—Support pillar;E11—Z-shaped sprue
puller;E12 —Stop block;M4—Support blocks;M5—Back plate
3.5抽芯机构设计
针对上述设计,选用斜导柱抽芯机构驱动行位抽芯。根据模具整体装配和成型实际需要,斜导柱固定在定模一侧,滑块设置于动模一侧,整体结构如图9所示。
为确保齿形结构的成型精度,由装配工艺销C1定位6个行位对齐至成型位后方可进行模具抽芯机构装配。滑块C6与侧型芯F4通过T形槽组合在一起,通过压板C3安装于动模一侧。滑块与压板之间采用间隙配合,双边配合间隙为0.02mm,并且滑块侧面增加油槽,确保滑块顺利滑动,不会因模具受热膨胀而出现卡滞。锁紧块C2与斜导柱C4安装于定模一侧,并在锁紧块斜面安装有耐磨块以减少磨损。滑块侧面加工有两条V形槽C10,中心距为5mm,恰好对应模具所需抽芯距。模具正式工作前应移除定位销钉。合模时,弹簧定位装置C11通过压板侧面孔插入图示左侧V形槽1锁定滑块成型位。开模时,斜导柱驱使滑块后退,定位装置滑出V形槽1,直至斜导柱脱离滑块,定位装置恰好滑入右侧V形槽2。在此基础上,滑道后端设置有安全限位螺钉C9,避免弹簧定位装置失效造成的风险。
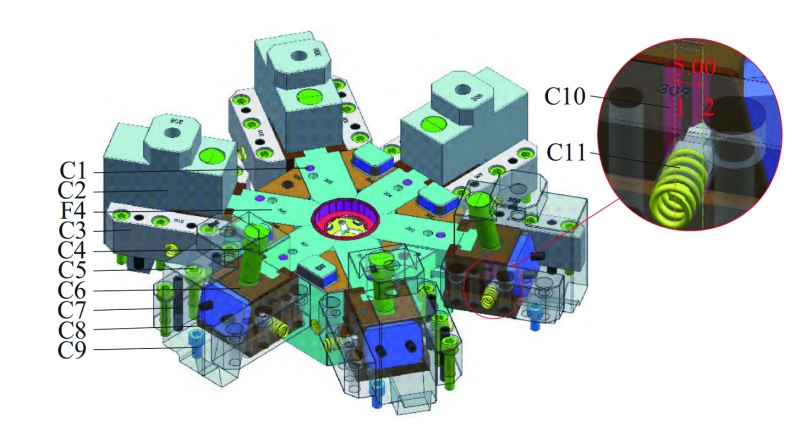
F4 is the same as Fig.7;C1—Side core locating pins;C2—Wedge block;
C3—Plate;C4—Angular pin;C5—Screw;C6—Core slide;
C7—Locating pin;C8—Wear-resistant block;C9—Limit nail;
C10—V groove;C11—Slide positioning device
4模具工作原理及成型效果
4.1工作原理
模具三维结构如图10所示,工作原理如下。
(1)合模注塑。模具通过动、定模座板M1,M5安装在注塑机上,接入冷却水以调节模温。注塑机熔化原料,锁紧模具,完成注塑过程。注射时,喷嘴前端球面紧贴浇口套G4,以保证无熔料积存。
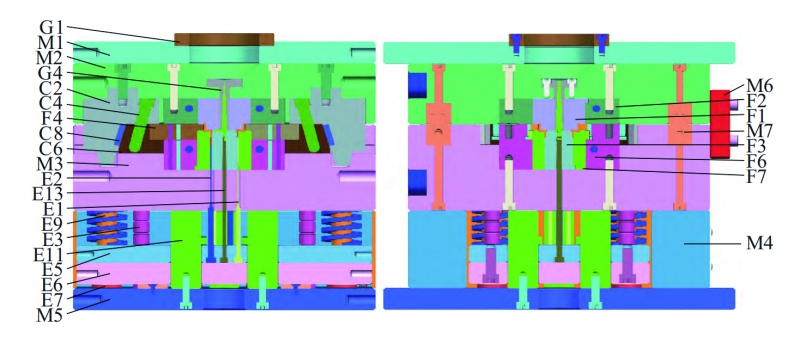
G1,G4 are the same as Fig.6;F1~F4,F6,F7 are the same as Fig.7;
E1~E3,E5~E7,E9~E11,M4,M5 are the same as Fig.8;
E13—Z-type pulling rode;C2,C4,C6,C8 are the same as Fig.9;
M1—Front plate;M2—Fixed plate;M3—Moving plate;
M6—Safety strap;M7—Precision positioning column
(2)开模抽芯。塑件充型并完全冷却固化后,注射机停止锁模并驱动动模M3后退开模。动模侧滑块C6在定模侧斜导柱C4的作用下,带动侧型芯F4后退完成塑件周圈齿形结构抽芯。凝料借助Z形拉料杆E13脱模浇口套,与塑件一同留在动模侧镶件F3上。
(3)脱模顶出。动模后退,注塑机驱动推板E7前移,带动扁顶针E1,E2以及Z形拉料杆E13共同顶出,潜伏式浇口自动切断实现凝料与塑件的分离。塑件顺利脱模,由人工或机械手取出塑件。
(4)复位合模。脱模后注射机顶杆后退,复位杆E9上压缩弹簧主动回弹,驱使推出机构复位,直至底部接触限位钉E7。同时动模M3前移重新合模,压实复位杆端面,触发到位信号,开始下一注射循环。
此外,模具的导向定位精度对于多齿形结构塑件的成型质量尤为关键。除常规导柱、导套以及模腔板F2,F6表面设置的虎口结构外,模具在动、定模板间配有6个锥形定位柱M7,按照行位布局对称布置,以提高模板间的配合精度以及模具的整体刚度。
4.2改善效果
相较于分体加工工艺,基于组合加工的多齿形汽车旋钮模具通过成型零部件合理拆分,借助五轴CNC加工整体式电极,实现所有行位组合件的同时加工,对模具加工制造以及产品成型均具有显著改善效果。
(1)生产效率:采用分体加工工艺,模具6个行位各自经EDM放电成型齿形面,电极受限传统三轴CNC技术需拆分结构。每个行位需4块电极,经历
6次放电完成齿形的粗、精加工。因此,每套模具共需加工电极24块,行位零件经CNC电极加工及EDM放电工时合计为96h。采用五轴CNC技术虽无需拆分电极,减小了电极加工数量,但提升了数控编程复杂程度,单件加工工时有所增加,加之设备昂贵,实际改善效果有限。采用组合加工,仅需五轴CNC加工2块整体电极经2次EDM放电即可完成所有行位加工,工时合计为12h,仅为分体式加工的12.5%,加工效率提升显著。基于组合加工生产的模具经小批量生产验证,动作可靠灵活,多向抽芯机构未出现卡滞、碰撞等问题;批量生产稳定可靠,配合机械手夹取料头,生产周期35s/模次,日产能达2260个,可满足汽车主机厂产量要求。
(2)成型质量:由于分体式加工行位为单体离散制造,加工、装配等多个环节累计误差较大,因此产品行位分型处存在明显段差,电镀后成型质量较差。相较之下,组合式加工利用模具自身结构结合先进加工技术可靠定位,实现模具关键零件加工装配一体化制造,在降低修配难度的同时保证了产品成型质量。采用基于组合加工工艺设计的模具,塑件表面经显微镜观察分型段差显著改善,产品电镀表面几乎不存在积镀、毛刺或烧焦等缺陷,成型质量显著提升,具体如图11所示。
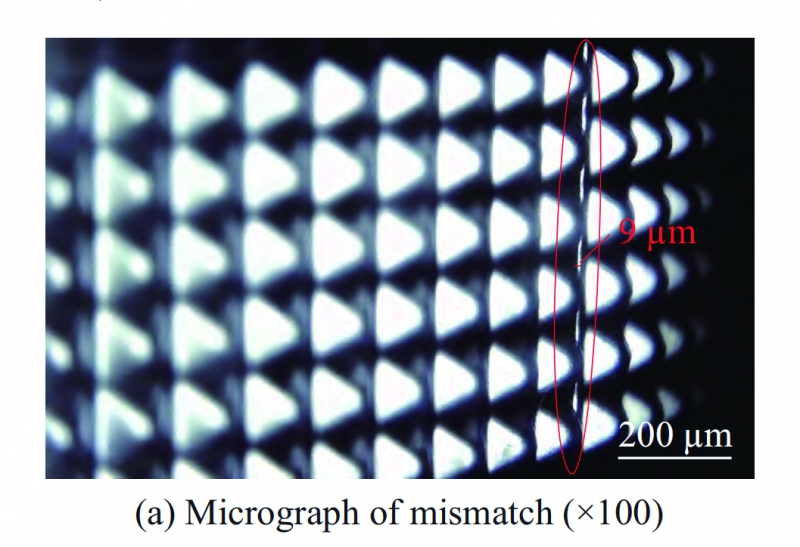
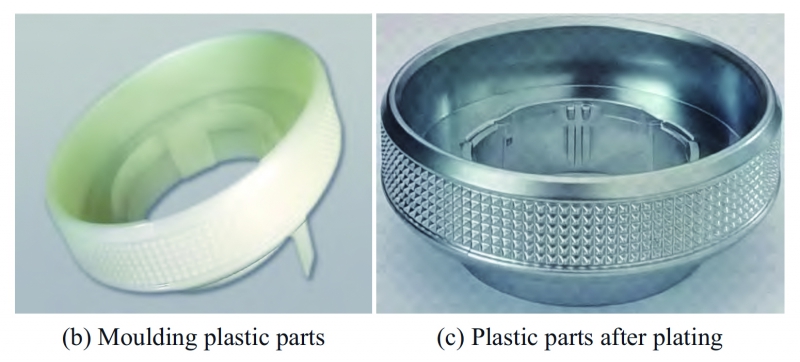
5结论
(1)对于多齿形结构塑件,通过分析其结构特征及参数,明确行位多向同时抽芯成型思路,建立了一套关于齿形结构与抽芯行位数的计算方法。该方法能够快速求解行位对齿形结构最大包覆齿数、包覆角以及所需最少行位数量,对模具抽芯行位设置具有指导意义。
(2)对于多齿形结构塑件,行位齿形面的成型应采用EDM加工。实际生产按照加工制造离散程度有分体式加工以及组合式加工两种工艺路线。研究表明,组合式加工利用模具自身装配关系装夹定位,实现行位加工装配一体化,大大提高了加工制造效率以及成型质量,对于多齿形结构电镀塑件成型具有显著优势。
(3)对于多齿形结构塑件,多向抽芯行位在塑件齿根间对称分型,并设置在动模侧以便于后续加工装配。成型零部件设计对于组合式加工尤为关键,通过拆分镶件以及定位孔系保证了行位与模腔板的可靠定位,并以此为基础详细阐述了成型零件的组合加工过程以及模具其余各系统的设计方案。
实践表明,基于组合加工设计的模具安全可靠,零件加工生产效率大幅提升,产品成型质量符合预期要求,尤其是操作表面齿形结构处的分型段差显著减小,电镀后无明显外观缺陷,证实该组合式加工工艺先进,配套模具结构合理,对同类型产品的模具设计及制造具有一定参考价值。1)对于多齿形结构塑件,通过分析其结构特征及参数,明确行位多向同时抽芯成型思路,建立了一套关于齿形结构与抽芯行位数的计算方法。该方法能够快速求解行位对齿形结构最大包覆齿数、包覆角以及所需最少行位数量,对模具抽芯行位设置具有指导意义。
(2)对于多齿形结构塑件,行位齿形面的成型应采用EDM加工。实际生产按照加工制造离散程度有分体式加工以及组合式加工两种工艺路线。研究表明,组合式加工利用模具自身装配关系装夹定位,实现行位加工装配一体化,大大提高了加工制造效率以及成型质量,对于多齿形结构电镀塑件成型具有显著优势。
(3)对于多齿形结构塑件,多向抽芯行位在塑件齿根间对称分型,并设置在动模侧以便于后续加工装配。成型零部件设计对于组合式加工尤为关键,通过拆分镶件以及定位孔系保证了行位与模腔板的可靠定位,并以此为基础详细阐述了成型零件的组合加工过程以及模具其余各系统的设计方案。
实践表明,基于组合加工设计的模具安全可靠,零件加工生产效率大幅提升,产品成型质量符合预期要求,尤其是操作表面齿形结构处的分型段差显著减小,电镀后无明显外观缺陷,证实该组合式加工工艺先进,配套模具结构合理,对同类型产品的模具设计及制造具有一定参考价值。1)对于多齿形结构塑件,通过分析其结构特征及参数,明确行位多向同时抽芯成型思路,建立了一套关于齿形结构与抽芯行位数的计算方法。该方法能够快速求解行位对齿形结构最大包覆齿数、包覆角以及所需最少行位数量,对模具抽芯行位设置具有指导意义。
(2)对于多齿形结构塑件,行位齿形面的成型应采用EDM加工。实际生产按照加工制造离散程度有分体式加工以及组合式加工两种工艺路线。研究表明,组合式加工利用模具自身装配关系装夹定位,实现行位加工装配一体化,大大提高了加工制造效率以及成型质量,对于多齿形结构电镀塑件成型具有显著优势。
(3)对于多齿形结构塑件,多向抽芯行位在塑件齿根间对称分型,并设置在动模侧以便于后续加工装配。成型零部件设计对于组合式加工尤为关键,通过拆分镶件以及定位孔系保证了行位与模腔板的可靠定位,并以此为基础详细阐述了成型零件的组合加工过程以及模具其余各系统的设计方案。
实践表明,基于组合加工设计的模具安全可靠,零件加工生产效率大幅提升,产品成型质量符合预期要求,尤其是操作表面齿形结构处的分型段差显著减小,电镀后无明显外观缺陷,证实该组合式加工工艺先进,配套模具结构合理,对同类型产品的模具设计及制造具有一定参考价值。
参考文献
[1]叶豪,郑永江,董少迪.车用旋钮的轨道设计、仿真分析与试验研究[J].机械设计,2019,36(2):27‒31.
[2]熊毅,冯啸霖.外侧整圈倒扣产品多向顺序抽芯注射模具[J].塑料工业,2021,49(8):81‒86.
[3]徐文庆,熊建武,陈黎明,等.汽车旋钮升举螺杆式推板同步推出机构注射模改进设计[J].工程塑料应用,2022,50(12):92‒96.
[4]刘庆东.汽车塑料电镀装饰条注塑模具设计[J].中国塑料,2020,34(12):88‒91.
[5]闫竹辉,刘斌.多向抽芯汽车空调出风口壳体注塑模具设计[J].工程塑料应用,2020,48(8):93‒98.
[6]曹洋,宁雪梅,秦剑,等.复杂多特征SR3薄壁塑料壳体多向抽芯注塑模具设计[J].塑料工业,2022,50(S1):76‒81.
[7]王静,刘雪敏,崔玉波.汽车方向盘盖板复杂多向抽芯二次顶出热流道注塑模具设计[J].塑料,2021,50(6):119‒122,128.
[8]雷小叶,杨幸雨,梅益.MP3089车载导航后盖壳体卡扣薄壁件多向侧抽芯注塑模具设计[J].合成树脂及塑料,2019,36(2):77‒81.
[9]李阳.微阵列结构的微铣削/微细电火花组合加工技术研究[D].哈尔滨:哈尔滨工业大学,2019.
[10]吉帅.微方孔电火花电解复合加工[D].南京:南京航空航天大学,2021.
[11]胡光良,严胜义,宋小尉,等.注塑模表面齿形花纹结构加工工艺的设计优化[J].工程塑料应用,2023,51(6):73‒79.
[12]严胜义,王甘平,胡光良,等.一种高效加工旋钮模具表面齿形花纹的方法:CN202110149783X[P].2022-06-17.
[13]张健,霍凤伟,徐金亭,等.小型推进器转轮五轴数控加工[J].工具技术,2024,58(7):86‒90.
[14]宋艳丽,麦丽菊,程俊.基于NX12五轴定位的分流器基座铣削加工工艺设计[J].机床与液压,2020,48(19):152‒155,169.
[15]林静财.高精度卸料板镶件组合加工工艺[J].模具工业,2022,48(12):58‒61,67.
[16]徐新华.操控旋钮双色注射成型热流道模具设计[J].中国塑料,2020,34(9):84‒89.