石峰1,王伟伟2,邹锋1,朱超挺1,周天绮1
(1.浙江医药高等专科学校,浙江宁波 315100; 2.浙江工商职业技术学院机电工程学院,浙江宁波 315012)
摘要:使用聚砜 (PSU)塑料注射成型医疗干粉吸入器底座塑件。成型前,对PSU材料进行干燥处理的工艺参数为温度125~135℃,时间 4~6 h,平铺,铺料厚度 18~22mm,含水量控制在 0.1% 以下。针对塑件的注射成型设计了 1 副一模一腔热流道两板注塑模具,使用单点热浇口进行浇注; 模具分 2 次分型打开, 1次用于塑件定模侧斜孔的 抽芯脱模, 1 次用于塑件模腔的打开; 型腔的表面粗糙度为 0.4 以上,排气孔的深度应控制在 0.08 mm;针对塑件14个斜孔内壁的脱模,设计了定模斜杆复合顶出机构,针对14 个斜孔外壁的脱模,设计了动模“万能斜顶”复合机构。 运用 CAE 分析获得了模具中所需的成型时间为 1.542s,注塑压力为 58 MPa。塑件成型后须退火处理,控制参数为空气浴,温度 150℃,时间 2~4h。
关键词: 医疗塑件; 聚砜塑料; 热流道; 注塑工艺; 模具设计; 脱模
1 塑件分析
图1所示为一种医疗干粉吸入器底座塑件,塑件俯视外形呈葵花形状,侧视外形呈球冠形状。塑件外沿圆周上布置了 14 个斜圆柱孔 (简称斜孔),其内径为8 mm、外径为10 mm、高度为14 mm,斜孔轴心线与塑件中心线夹角为5º。中间直径127mm圆周内布置了 4 个内径为8mm 的直圆柱孔和6个内径为4mm小孔,直圆柱孔的外径为10mm,高度为12mm。塑件最小壁厚 1.8mm,最大2.4 mm,平均壁厚2mm。
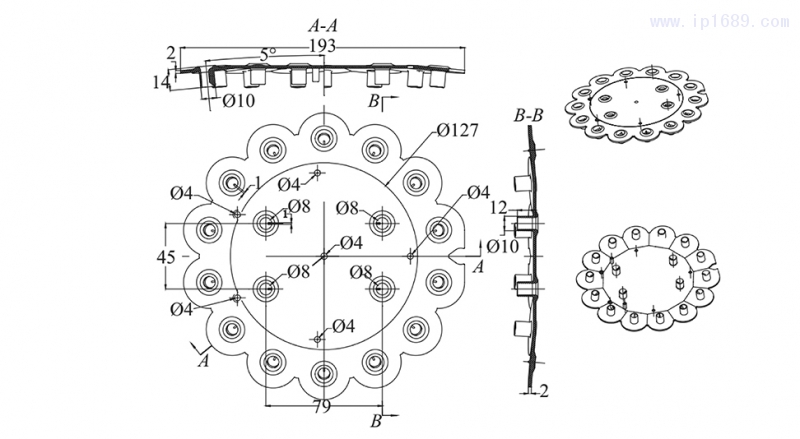
塑件
塑件使用聚砜 (PSU) 材料进行注射成型,该材料为一种坚韧且强度高的透明塑料,与聚碳酸酯相比能提供较高的耐热性和更好的水解稳定性 [1–3] ; 具有良好的力学性能和耐化学性能,与蒸汽、氧化剂等接触时具有优异的尺寸稳定性;有透明与不透明的各种彩色可供选择。PSU的收缩率为0.4%~0.8%,不同方向收缩差异小,塑件脱模斜度一般取0.02º。PSU材料在医卫器材零部件制造方面应用较为广泛,典型有外科手术盘、喷雾器、加湿器等塑件零件 [4–6]。
2 注射成型方案及浇注系统设计
塑件的注射成型方案设计受两个因素的影响, 第一个是塑件的材料,第二个是塑件的结构。就材料而言,PSU是一种非结晶聚合物,成型温度 280℃以上,流动性差,流长比为 80左右,塑件的壁厚须 控制在 1.5 mm 以上,吸入器底座塑件的平均壁厚为 2mm,因而可以使用 PSU 材料进行注射成型。 PSU 材料对缺口较为敏感,塑件上的直角或者锐角都须使用圆弧过渡进行处理。PSU材料对含水量敏感,塑件成型前,须对材料进行干燥处理,尽可能降低材料中含水量,塑件加工前,材料含水量控制在0.1% 以下,以防高温下熔体降解。
就塑件结构而言,塑件整体形状为圆片状,其包容圆的外径为193 mm,为中等偏大型塑件。为保证注塑时浇口到各流动末端的长度接近,以保证塑件各局部位置的充填均衡性,塑件的最佳浇口位置以开设在塑件的几何中心位置为最佳。塑件模腔的冷流道设计要求高,流道设计时,其基本要求为:主流道尽可能短且粗,以利于熔体流动,主流道直径2mm以上,脱模斜度 3º~5º,分流道用圆形或梯形流道,流动路径避免采用弯道形式。
对于塑件的脱模,其上所设置的 14 个斜孔,需要使用14个抽芯方向不同的圆柱型芯镶件进行抽芯脱模,显然,塑件不宜采用多腔布局成型,采用单 腔布局既能保证塑件的成型精度,又能降低模具中 机构件的安装难度。
塑件的浇注系统设计方案为:使用 1 模 1 腔单 腔布局,使用单点热流道直接浇口进行浇注 [7],浇口设置在塑件的几何中央位置,这样可以避免冷流道的开设,以免影响模腔的充填。该方案的 CAE 流动分析如图 2 所示,CAE 分析中,塑件材料选用巴斯夫公司 (BASF) 牌号为 P1700 的 PSU,浇口为圆柱形 Ø1.2 mm 浇口,浇口长度 1.0 mm,进料口的位置设置在模腔几何中央厚壁处。模具温度设置为 140℃,熔体温度 360℃、最大温度 380℃,顶出温度 165℃。注塑速率采用中速,以免高速造成熔体破裂, 充模困难。
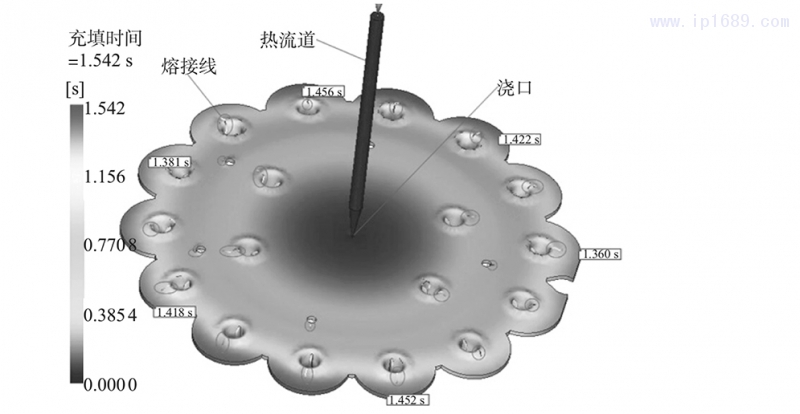
浇注系统 CAE 分析
从图 2 可以看出,在该成型方案下,模腔的充填性能好,各末端能获得均衡充填,整体充填时间为1.542s 左右,能满足塑件的生产周期要求。充填所需压力为58MPa 左右,对注塑机的使用要求不高。流动路径上熔接线主要出现在孔的末端位置处,形态为熔合线,可以通过提高模具温度的方式来消除。 流动路径上气孔较多,需要增强模腔的排气来消除。 流动分析中,不利的结果为:塑件成型中所产生的 内应力难以消除,只能通过保压措施来尽可能减小。
3 分型及成型件设计
如前所述,塑件采用单腔模式成型时,将考虑 收缩率后的塑件表面作为成型件的成型面,选用外沿分型线、各内孔分型线以上的面作为型腔面,以下的面则作为型芯面,如图 3 所示。其中,型芯面中,各斜孔内侧的局部区域面必须分割出来,以用作斜顶的分型面,用于设计斜顶以实现斜孔内侧倒扣的成型和脱模 [8–12]。
图 4 为单个斜孔内侧局部区域面 ( 图 4 中倒扣区域 ) 的成型件设计。在图 4 中,针对 14 个斜孔的脱模,使用斜杆镶件成型斜孔的上端部分,这样可以将斜孔的下端设置成直杆镶件,从而可以最大限度 降低14个斜孔的脱模机构设计难度。因而,针对斜孔部位的脱模可以采用以下方式:斜孔内壁的成型 与脱模由位于型腔镶件一侧的斜杆镶件来实现,对于斜孔外壁倒扣区域的脱模,则使用斜顶顶出方式实现。

成型面分割
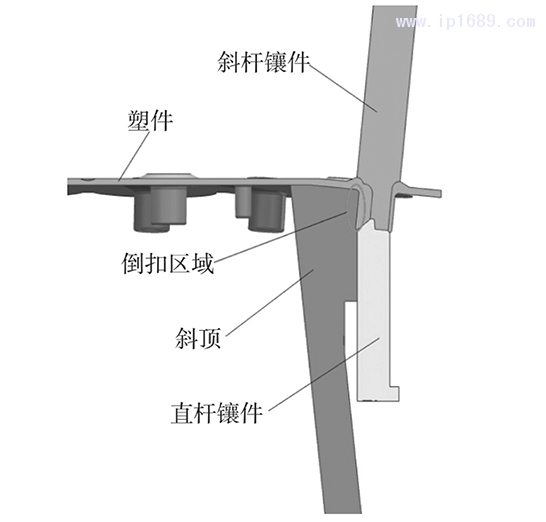
单个斜孔内侧局部区域面的成型件设计
使用图 3 中所示外沿分型线对模腔进行分型后,将所获得的型腔镶件、型芯镶件及斜孔的斜顶、 斜杆镶件和直杆镶件进行拼合组装,由此构成的模腔 (局部) 如图5所示。设计斜顶时,必须设置高度挂台、水平挂台两个限位措施以保证斜顶复位时在高度方向、水平方向都有定位。设置外沿分型面时,分型面设置为延拓面+水平面的组合形式,以便于排气槽开设、分型面的加工及模腔的闭合配 模。加工型腔镶件成型面时,表面粗糙度控制在 0.4
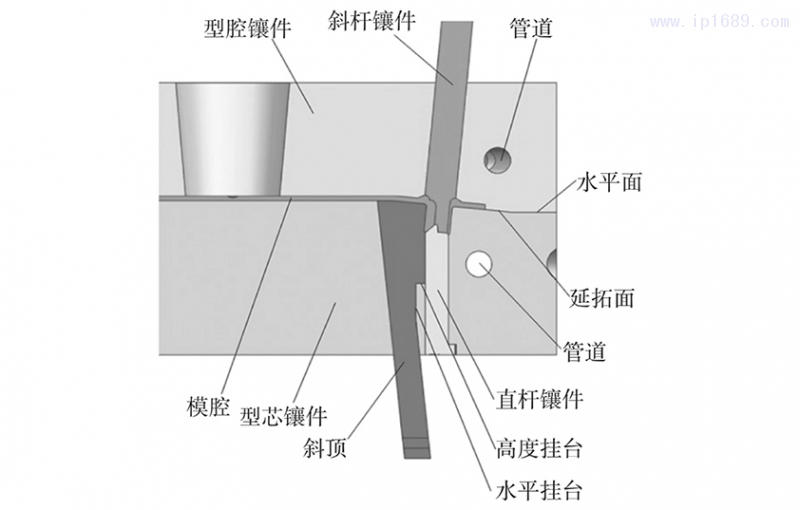
模腔成型件的构成
以上以确保塑件的表面光亮。中速注塑时,模腔分型面上须开设环绕型排气间隙及排气槽,排气间隙 0.02,用于引气的排气槽的深度0.08 mm。
综上所述,最终成型件的设置及组装如图 6 所示。
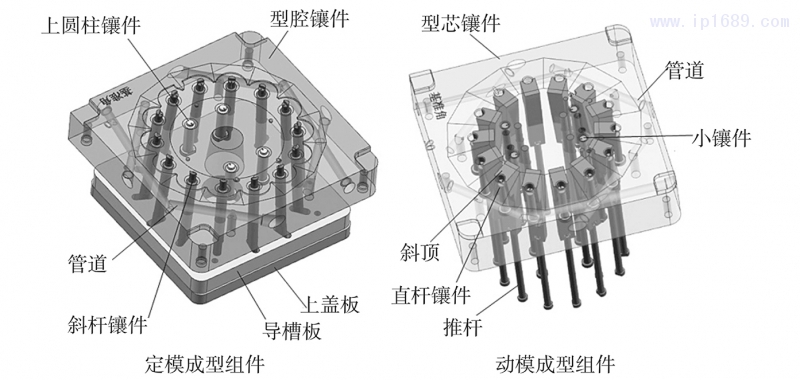
图 6 成型件设计
定模成型组件中,包括1个型腔镶件、14个斜 杆镶件、4个上圆柱镶件。14个斜杆镶件的上端通 过横位销安装在导槽板上对应的滑动槽内,导槽板上端用上盖板盖住,以防止斜杆镶件滑落。 14 个斜 杆镶件通过导槽板和上盖板组装后,构成定模斜杆 复合顶出机构,再插入型腔镶件中各自对应的斜孔 内。定模成型件的材料使用 M461 预硬镜面塑胶模具钢。
动模成型组件中,包括 1 个型芯镶件、14 个直杆镶件、14 个斜顶。14个斜顶采用“万能斜顶”结 构形式,由推杆推动其上端的斜顶顶出。14个直杆镶件采用肩台定位方式固定安装在型芯镶件内。 14个斜顶通过相应的14根推杆推动,推杆安装在模具的顶针推板上,构成动模“万能斜顶”复合机构。动 模材料成型件使用 Cr12MoV 模具合金钢。
4 模具结构布置
功能零部件在模具结构中的布置如图 7 所示,模具使用两板模结构,2次分型打开。所选用模架为一种非标准模架,由两板模模架改造而获得,改造的地方在于:定模板与定模座板之间增加 1 次分型打开,并增加 4 副模腔导柱进行导向。模具中的模腔布置为 1模1 腔。型腔镶件、型芯镶件均使用双边定位方式,通过楔紧块楔紧方式安装在定模板、动模板内。定模板、动模板的精确闭合定位由定模板导柱、模腔导柱、边锁共同实现 [13–14]。定模板导柱主要用于定模板打开/闭合时的滑动导向;模腔导柱主要用于定模板和动模板之间打开/闭合时的滑 动导向。定模板与定模座板之间的打开使用 4 根定距拉杆进行定距控制。定模板与动模板的临时闭合,使用模板锁控制。
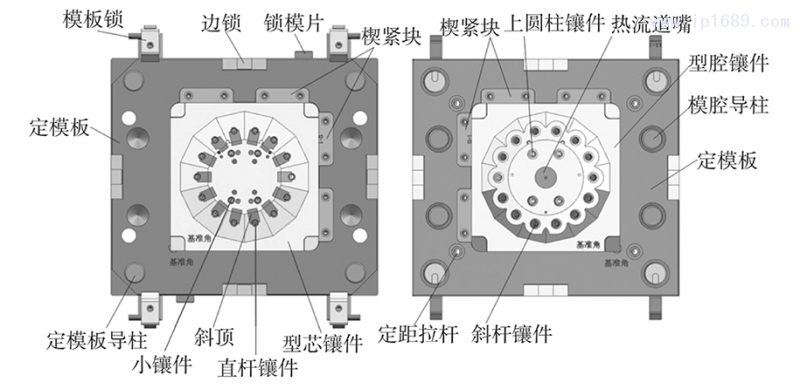
图 7 模具布局
5 模具机构件组装
机构件在模具上的组装如图 8 所示。模具的定模由定模座板 3、定模板 4 及附属机构零件构成,动模由动模板8、方铁 9、动模座板 10 等零件构成。盖板 11、顶针推板12等零件构成动模的顶出机构,注塑机顶杆通过顶杆套 13 推动顶针推板 12。定模板 4 和定模座板 3 之间的开模面为 P1,定模板 4 与定 模座板 3 之间的分离距离通过定距拉杆 5 限制;动 模板 8 与定模板 4 之间的开模面为 P2。开模面打 开的顺序为 P1 → P2,闭合顺序也为 P1 → P2。开模时,P1 面打开,P2 面闭合,该闭合控制由图 7 中 所示的模板锁进行控制,模板锁由锁钩杆 6 等 8 个零件组成。闭模前,P1,P2 面都处于打开状态,闭 合时,模板锁控制模具按 P1 → P2 顺序闭合。型芯 镶件 17、型腔镶件 18 分别通过螺钉紧固安装在动 模板8、定模板4 内。
定模斜杆复合顶出机构中,上盖板 27、导槽板 28 用螺丝紧固组合在一起,再通过螺丝紧固安装在 定模座板 3 所开设的槽内,斜杆镶件 25 的上端通过横销 26 进行开模方向的限位后,安装在导槽板28开设的滑动槽内,下端插入型腔镶件 18 内的斜孔内。 P1 面打开时,定模板 4 往下运动,将塑件从 14 个斜杆镶件 25 上推出。
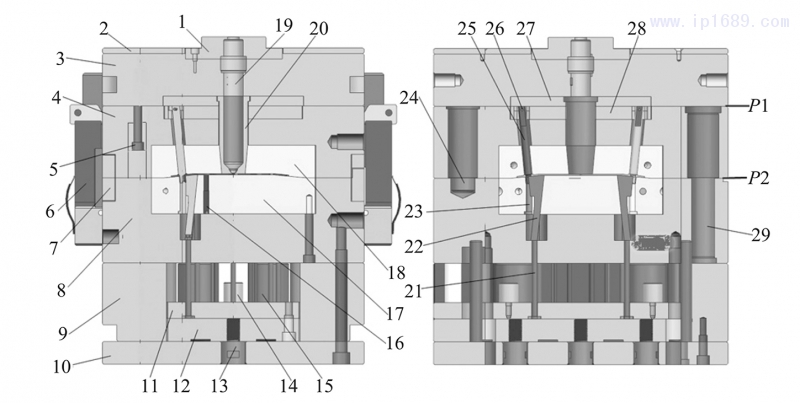
图 8 模具结构安装
动模“万能斜顶”复合机构中,斜顶 22 安装在 型芯镶件 17 内,其下端设置有 T 型槽,与顶杆21上端所设置的 T 型导轨滑动连接,顶杆 21 用顶针 推板 12 推动。 P2 面打开后,模腔打开,注塑机顶杆 通过顶针推板 12 推动斜顶 12 对塑件进行顶出。
模具中,模板锁机构为一种新型模板开闭控制 机构,如图9所示。机构的组成零件包括锁钩杆6,件30 ~件37。导动凸块 30 安装在定模座板 3 上,其上设置有导动销 31 的导动凸台;锁钩杆 6 与锁钩37用锁钩螺丝 38 组装在一起,锁钩杆6 用转动销 32 与底座 35 铰接在一起,底座 35 用螺丝紧固安 装在动模板 8 的侧边。耐磨锁块 36 用螺丝安装在定模板 4 上; 外簧片 33 和内簧片 34 叠装在一起, 用螺丝紧固组装在底座 35 上,用于阻挡锁钩杆 6 按T1 转动方向转动。锁钩 37 勾住耐磨锁块 36 用于锁紧动模板 8 和定模板 4。
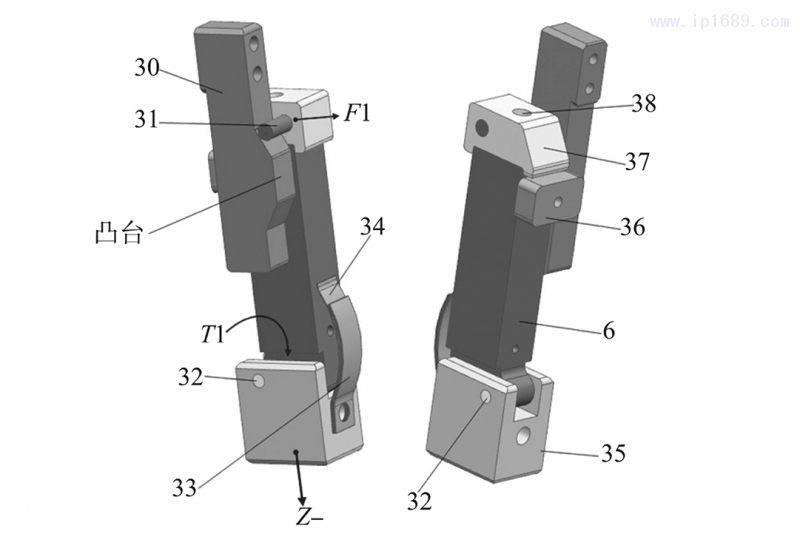
模板锁机构的动作原理为:当模具动模按 Z–向下行时,导动销31暂时不能接触导动凸块30上的导动凸台,因而,锁钩杆6 在外簧片33 和内簧片34 的弹压下,不能绕转动销 32 的中心按 T1 转动方向转动,此时动模板 8 和定模板 4 被锁钩37 和耐磨锁块 36 锁闭,模具只能在 P1 面打开;P1 面打开一定距离后,导动销 31 被导动凸块 30 上的导动凸台按F1 向推动,迫使锁钩37和耐磨锁块36脱离接触,从而,动模板 8 与定模板 4 分离,模具在 P2 面处打开。闭合时,P1 面先闭合,模具继续闭合过程中,锁钩 37 被耐磨锁块 36 先推开而后再勾住耐磨锁块 36,从而实现再次锁紧动模板 8 和定模板 4 的功能。
6 模具工作原理
结合图 8 所示,模具分 2 次分型打开,第一次打开在 P1 面处打开,该面打开时,14 个斜杆镶件 25 从模腔内塑件上对应的 14 个斜孔中抽芯抽出。第二次在 P2 面处打开,塑件从型腔镶件 18 内脱出并留于型芯镶件17 上。而后,随着模具动模的继续下行,注塑机顶杆顶住顶针推板 12,从而推动 14 根顶杆 21 和 14个斜顶 22将塑件从型芯镶件 17 上顶出,实现塑件的完全脱模。
模具复位时,顶针推板 12 先复位,确保动模“万能斜顶”复合机构先复位;模具闭合时,先在 P1 面处闭合,确保定模斜杆复合顶出机构先复位,而后在 P2 面处闭合复位,等待下一次注塑循环。
7 注塑工艺事项
注塑时,注塑工艺需要注意以下事项:
①注塑前,须对 PSU 进行干燥,干燥方式为热 风干燥,温度为 125~135℃,时间为 4~6 h,铺料方式为平铺,铺料厚度为 18~22mm,含水量控制在 0.1% 以下;
②不能使用脱模剂;
③ PSU 的成型温度较高,在注塑前必须将料筒 内清洁干净;
④成型后须对塑件进行退火处理,退火方式使 用空气浴方式,退火温度为 150℃,退火时间为 2~4h 。
8 结语
(1) 使用 PSU 塑料对医疗用干粉吸入器底座塑 件进行注射成型。运用 CAE 分析获得了塑件热流 道单腔模腔所需的成型时间为 1.542s,注塑压力为58MPa。
(2) 设计了塑件 1 模 1 腔两板热流道模具;浇注使用单点热浇口进行浇注;模具分 2 次分型打开, 1 次用于塑件定模侧斜孔的抽芯脱模, 1 次用于塑件模腔的打开。针对塑件 14 个斜孔内壁的脱模,设计 了定模斜杆复合顶出机构,针对 14 个斜孔外壁的脱 模,设计了动模“万能斜顶”复合机构。
(3) 模具型腔的表面粗糙度为 0.4 以上,排气间 隙 0.02 mm,排气槽的深度 0.08 mm。
(4) 注塑前,PSU 材料热风循环干燥工艺参数为:温度125~135 ℃,时 间 4~6h,铺料厚度20mm 左右,确保含水量控制在 0.1% 以下。成型后塑件的退火工艺使用热风空气浴方式退火,温度150℃,时间2~4h。
参 考 文 献
[1] 魏柯,张道海,秦舒浩,等 . 聚砜分离膜的亲水改性研究进展 [J]. 高分子材料科学与工程,2018,34(8):179–183.
[2] 芦文慧,黄肖容 . 抗菌性聚砜超滤膜的制备与表征 [J]. 中国新技术新产品,2018(9):1–5.
[3] 姬春梅 . 超声波对聚砜酰胺结晶性能影响研究 [J]. 橡塑技术与装备, 2018,44(20):9–15.
[4] 项启生,肖国华,徐生 . 救护车医疗床方向舵外壳复合哈弗滑块模具设计 [J]. 模具技术,2020(5):28–32.
[5] 罗军 . 气辅注射技术在医疗分析仪器罩注射模设计中的应用 [J]. 模具制造,2009(3):54–57.
[6] 凌亮文 . 输液器挤出滴斗模具设计 [J]. 中国医疗器械信息,2018,24(23):18–19.
[7] Baranek S L. 延长模具寿命的热流道系统 [J]. 现 代 塑 料,2007(7):62–63.
[8] 杨志立,黄诚驹 . 斜滑块内侧抽芯注射模设计 [J]. 模具工业,2013(12):52–54.
[9] 于盛睿,曹利钢,冯浩,等 . 家用吸尘器盖板的侧轨道抽芯注塑模设计 [J]. 工程塑料应用,2010,38(4):65–67.
[10] 于同敏,刘铁山 . 注塑模脱模机构智能化设计系统及关键技术研究 [J]. 机械设计与制造,2004(2):72–75.
[11] 杨安,董扬德,胡宏伟,等 . 法兰盖滑块脱模机构及注塑模具设计 [J]. 工程塑料应用,2017,45(10):82–86.
[12] 石海水 . 双向卡扣脱模设计分析和创新 [J]. 模具制造,2012(4):55–57.
[13] 何柏海,何骏 . 一种带推管侧顶脱模机构的注塑模设计 [J]. 工程塑料应用,2016,44(2):92–95.
[14] 朱海旭,王金莲 . 基于 CAE 技术的餐盒盖叠层热流道注射模具设计 [J]. 装备制造技术,2016(8):241–243,246.