倪培永,刘忠飞 ,白 龙
(南通大学 机械工程学院,江苏 南通 226019)
摘要:现有吸塑机成型机构的稳定性较差,严重影响了塑料制品等的加工质量。据此,设计了一种曲臂式成型结构。在分析现有成型机构的工作原理的基础上,运用 SolidWorks 软件设计三维模型并进行装配,建立曲臂的运动和受力方程。借助 Motion 模块对机构进行运动仿真,采用 Ansys 软件分别对起始位置与终止位置进行静应力分析。仿真结果表明,每个曲臂组需要的推动力为1724 N,空动作循环时间为 3.3 s,材料的变形结果符合设计要求。研究结果为该装置的研制提供了设计依据 。
关键词:吸塑机;成型机构;曲臂式;运动仿真;静态结构
吸塑机的成型部分决定了产品的形状 、质量和生产效率等,是吸塑机的关键组成部分。近年来,随着塑料行业的发展,吸塑也逐渐发展成为加工包装材料的最重要的方法之一[1-2] 。目前,自动一体化吸塑机基本上已经实现从送料到成品的高度自动化。作为吸塑机的重要组成部分,现有的成型部分仍存在一定的不足,如合模气压不足、材料形状复杂、加工困难等,不能满足实际的生产需要[3-5]。
本文针对设计要求的模具开合尺寸,重新设计曲臂长度,基于机构学原理建立了曲臂成型机构运动方程和受力方程 ,通过分析确定气缸的工作压力,为气缸选型提供依据,同时确定两曲臂相交位置水平初始和终了位移,为运动模拟提供初始和终了条件。对建模完成的曲臂式成型机构分别运用Motion 与 Ansys Workbench进行运动仿真与有限元分析,验证设计合理性。结合设计要求,完成曲臂式成型机构方案的理论设计,为下一步的试制提供有力的理论依据。
1 曲臂式成型机构设计
成型机构通过运动机构控制板的上下移动,来实现模具的开合,然后利用真空泵产生的真空吸力,将加热软化后的热可塑性塑料片材经过模具吸塑成各种形状的塑料制品等[6]。
由气缸驱动成型机构进行曲臂的张合,曲臂运动从而带动模具载台的上下运动,实现成型过程中的开模与合模过程 。曲臂式成型机构主要由上支承座、载台、光轴、下支承座、固定板、曲臂块、驱动支承座、驱动曲臂和气缸座等组成[7-8]。图1为结构示意图,图2为三维结构图。
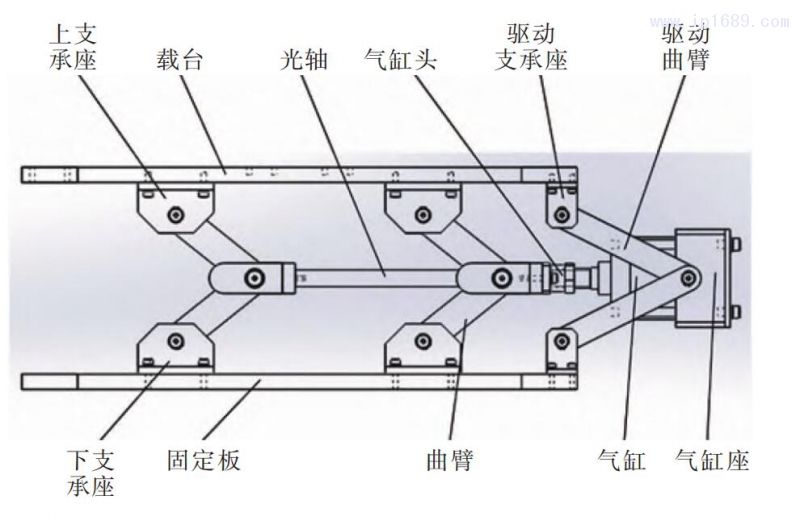
图1 曲臂式成型机构
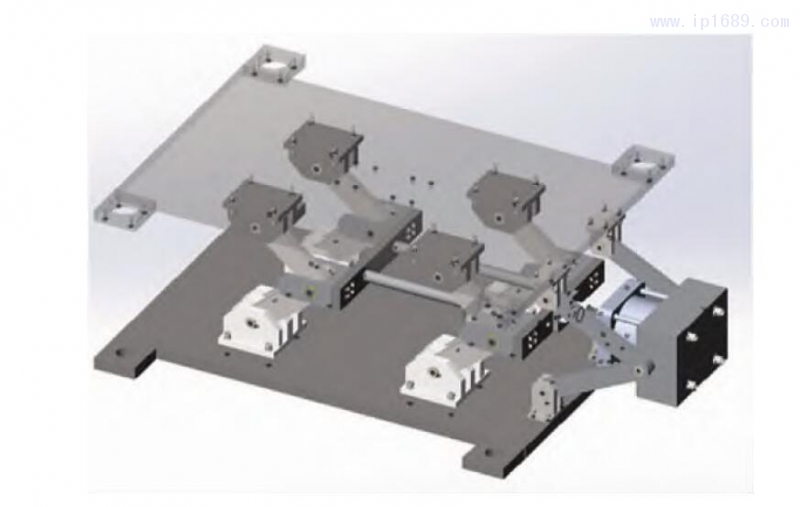
图2 曲臂式成型机构模型
为了验证曲臂长度是否满足设计要求,为运动仿真提供初始条件,必须确定两曲臂相交位置水平的初始和终了位移,因此需要建立机构的运动方程。另外,为了确定气缸输出压力,需要建立机构的受力方程 。根据实际情况,提出以下几点设计要求:开合尺寸为 300 mm;成型面积不得小于 750mm×600mm;合模压力不小于0.5 MPa;空动作循环小于 4s。载台位移简图与单个曲臂受力简图分别如图 3、图4 所示。
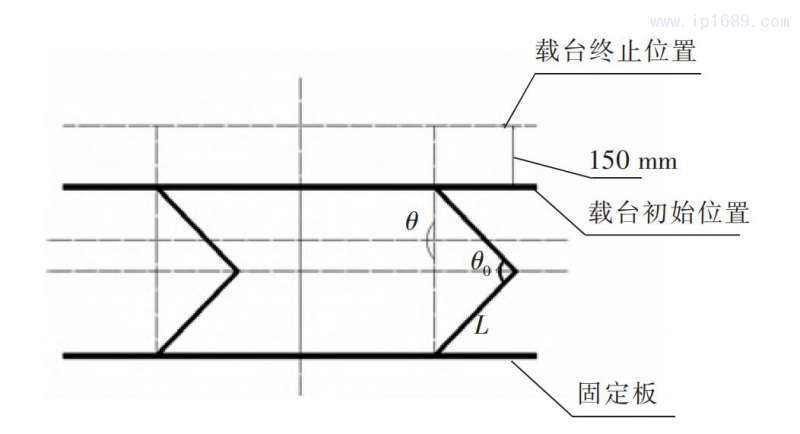
图3 载台位移简图
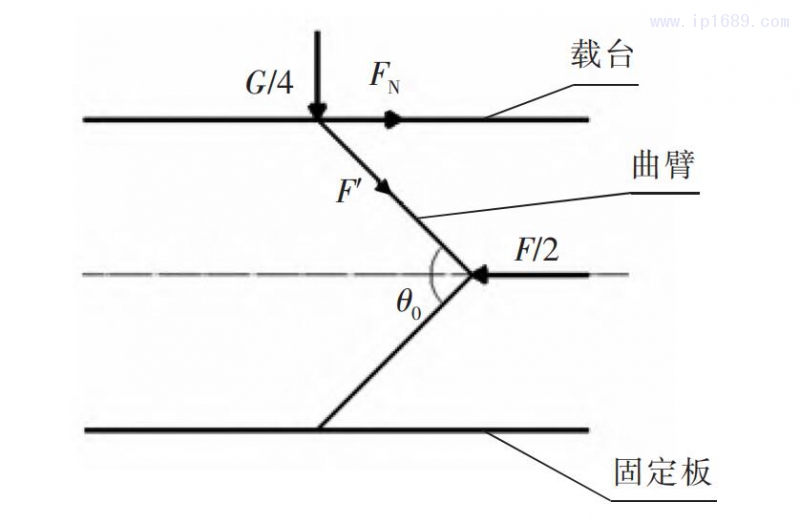
图4 单个曲臂受力简图
根据设计要求与图示得到各个参数关系式 ,其中:G为载台 、模具机构的重力之和;F为气缸输出力;F′为曲臂杆所受作用力。
载台行程需要满足
2Lsin() - 2Lsin()= 150, (1)
式中:L为曲臂长度;θ0、θ分别为两曲臂初始夹角和合模时的夹角。
曲臂块水平方向行程
Lcos()- Lcos() = S, (2)
式中S为两曲臂相交位置水平位移。
随着θ的增大需要推动曲臂机构运动的力逐渐减小,起始力为最大力 。当达到最大位置时,模具合模,产生合模压力P需达到0.5 MPa,接触面积A按照750mm x 600mm计算。
载台板材料选择Q235A,密度为7.858 g/cm3;模具结构材料为铝,密度为2.7 g/cm3,得G≈2 300 N,合模瞬间 G′ = PA + G = 227 300 N 。由式(5)中F与G的关系可知,合模时θ需足够大,才能承受 0.5 MPa 的合模压力。理想假设合模角最大状态时,θ = 180°。由受力可知,此时输出力为 0 N 时机构静 平衡 ,即气缸运动到最大位置 。假设θ =180°,L = 200 mm,由式(1)得θ0 ≈ 77.4°。将已知条件代入式(2)与式(5)中,求得 S=156 mm,F≈ 2 870 N。考虑气缸效率,实际气缸工作压力选择为 0.6 MPa,即工作压力为 0.6 MPa 时的伸缩力应大于 2 870 N。由气缸理论输出表,结合假设得到的已知条件与实际生产情况,选用 AirTAC(亚德客)SC100 x 100 气缸,该气缸理想工作气压为 0.7 MPa,速度为 30~500 mm/s。
2 成型机构运动仿真
为了方便研究,避免结构过于复杂而影响仿真计算速度 ,将结构等效简化 ,进行单个曲臂组的运动仿真[9-11] 。简化结构和运动简图分别如图 5、图 6所 示。设计空动作循环为 3.3 s,成型机构在初始位置时, 气缸做功,在1.5 s 时完成合模过程,1.5~1.8 s 内进行保压,3.3 s 时恢复至初始位置,完成一个吸塑产品的成型动作 。加载 SolidWorks Motion 插件,通过运动仿真分析研究该设计是否合理,运动是否干涉。
设定曲臂初始夹角为 77.4°,曲臂与曲臂轴 、曲臂轴与支承座 、三曲臂块与曲臂轴之间均为转动 副,设置接触类型为实体接触[12-14] 。同时设置马达参数函数为:STEP(time,0,0,1.5,155)+ STEP(time,1.5,0,1.8,0)+ STEP(time,1.8,0,3.3,-155)。设置
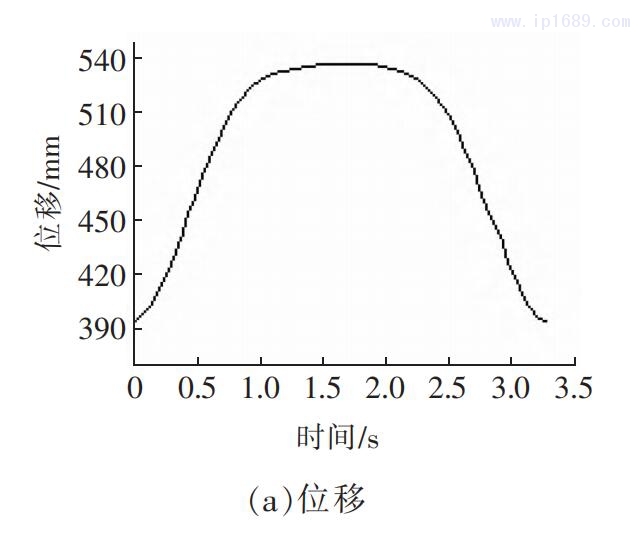
图5 成型机构简化结构
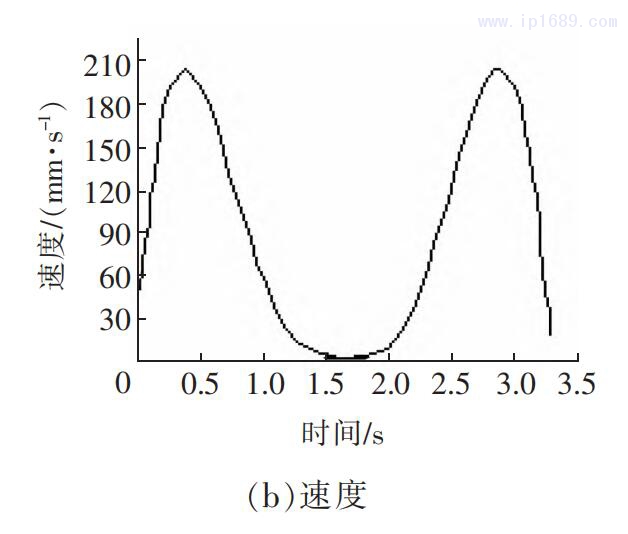
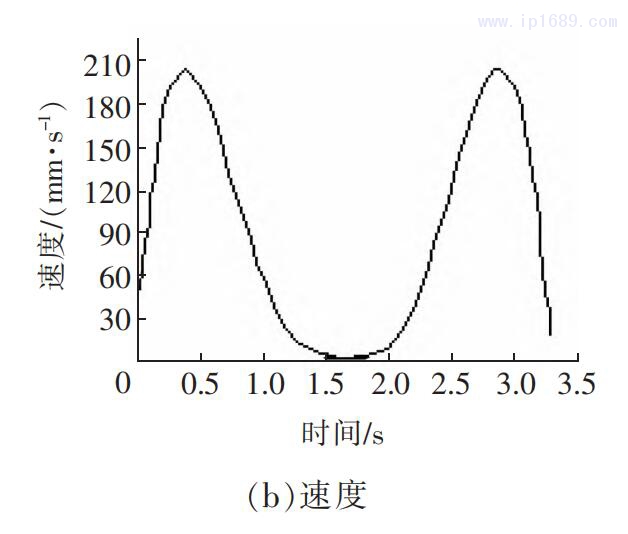
图6 曲臂运动简图
仿真时间为 3.3 s,仿真步数为 200 步 。后处理得到上支承座和曲臂运动曲线,如图 7、图 8 所示。
由图 7(a)可以看出,上支承座最大位移变化为148.4 mm,接近开合尺寸的一 半 。从图 8(b)可以看出 ,曲臂在运动过程中会发生速度突变 ,具有较大惯性 。与闭模过程相比 ,曲臂在开模的过程中,由于重力的作用其惯性更大 。针对这种情况 ,在实际使用中,可以适当增加成型结构的工作循环时间,即通过使用泄气阀适当减少气缸力的输出,辅助开合模过程 ,以减小机构惯性力 。如果从几何参数方面进行优化改进 ,相应的制造成本会增加 ,因此,适当减小气缸压力是较好的改进方法。模拟实验还发现,曲臂与气缸的夹角在 0~1.5 s 内从141.05°变成 90.24°, 符合设计要求。
3 静应力分析
在验证运动仿真符合设计要求后 ,再对设计方 案进行静应力分析 。由受力关系式可知 ,起始位置需要的力最大 。当达到终点位置时由于受合模压力的影响,曲臂受力发生变化,此时向下的力最大 。运用Ansys的Static Structure模块分别对曲臂起始位 置与终止位置进行静应力分析,考察零件是否发生严重变形等 。为了达到简化模型的目的 ,只对一个曲臂组进行静应力分析[15]。
在初始位置时,由运动仿真得到马达力为1500 N, 设定曲臂受到的水平力为1500 N,且上支承座受到575N的重力,同时设置重力等参数,对下支承座设置约束。在终止位置由受力可知,曲臂受到的水平力几乎可以忽略[16-17]。故只施加重力与合模压力 0.125 MPa作用在上支承座表面,对下支承座设置约束,得到起始位置 、运动终止位置曲臂机构的应力图 、应变图,分别如图9、图10所示。由图可以看出,曲臂组在起始位置时的最大应力为 63.07 MPa,未超过Q235A材料的屈服强度,其最大变形量为6.109 ×10-5 m,主要变形集中在上支承座与上曲臂之间。曲臂组在运动终止位置时,最大等效应力为 23.33 MPa,最大变形量为 2.366 × 10-5 m。由于随着曲臂运动过程中,马达力即气缸力逐渐减小,故在终止位置时变形与应力较起始位置都减小。
4 结论
结合现有机构的原理与设计参数 ,对吸塑机曲臂式成型结构进行了改进设计,建立了曲臂的运动和受力方程,确定了机构运动的初始和终止位置参数 。经过改进设计的曲臂,在合模夹角为180°时,模拟得到的开合尺寸接近设计要求的开合尺寸;通过软件进行运动仿真,得到每个曲臂组需要的推动力为1724 N,空动作循环时间为 3.3 s,该运动仿真结果基本符合设计要求。依据运动仿真得到的参数进行静力结构分析,得到起始位置与终止位置的等效应力图与形变图,静力结构仿真结果显示应力和变形大小均未超过材料极限,所选材料符合要求。在实际使用中,可以通过使用泄气阀适当减少气缸力的输出,辅助开合模过程,以减小机构的惯性力。
参考文献 :
[ 1 ]刘玮,郁舒兰,丁伟.真空吸塑机及其性能实验研究[J]. 包装工程,2011,32(18):34-37.
[ 2 ]刘佳鸿,赵德权,田和保,等.碳纳米管透明导静电涂料制备及在吸塑上的应用[J].涂料工业 ,2015,45(8): 72-76.
[ 3 ]郑钧文.基于大工计控PLC的吸塑机控制系统设计与实 现[D].大连:大连理工大学,2014.
[ 4 ]JANSEN K M B,FLAMAN A A M. Construction of fast- response heating elements for injection molding applica- tions[J]. Polymer Engineering & Science ,1994 ,34(11): 894-897.
[ 5 ]张德海 ,马战胜 ,陈慧芳 ,等 . 一种单工位真空成型吸塑机的设计研究[J].机械制造,2008,46(9):10-14.
[ 6 ]郐红艺.自动下料机的机械结构设计与研究[D].太原:中 北大学,2017.
[ 7 ]GE C B,REN Q,WANG S P,et al. Steam-chest molding of expanded thermoplastic polyurethane bead foams and their mechanical properties[J]. Chemical Engineering Sci- ence,2017,174:337-346.
[ 8 ]GLODOVÁ I,LIPTÁK T,BOCKO J. Usage of finite ele- ment method for motion and thermal analysis of a specific object in SolidWorks environment[J]. Procedia Engineer- ing,2014,96:131-135.
[ 9 ]陈红,赵美宁.屋顶盒灌装机底部成型机构的设计及仿 真[J].包装工程,2017,38(7):164-168.
CHEN H,ZHAO M N. Design and simulation of the bot- tom forming mechanism of gable -box filling machine [J]. Packaging Engineering,2017,38(7):164-168.(in Chi- nese)
[10]PENNOCK G R ,ISRAR A. Kinematic analysis and syn- thesis of an adjustable six-bar linkage[J]. Mechanism and Machine Theory,2009,44(2):306-323.
[11]ERKAYA S,U S,UZMAY I. Dynamic analysis of a slid- er-crank mechanism with eccentric connector and plane- tary gears[J]. Mechanism and Machine Theory ,2007,42(4):393-408.
[12]李大磊 ,丁天涛 ,程建民,等 .基于SolidWorks Motion 的空间摆动机构的运动分析[J]. 制造业自动化,2011,33(22):70-71.
[13]韩庆红,张锁怀,陈香利. 基于SolidWorks Motion的灌 装机分瓶机构凸轮曲线设计[J].包装工程,2016 ,37(5):110-114.
[14]吴昊,童志伟,陈航 ,等.基于SolidWorks Motion与ADAMS 在改进型BW-280/12泥浆泵的动力学仿真 [J]. 制造业自动化,2014,36(5):65-66.
[15]QI X D,SHEN X L. Multidisciplinary design optimization of turbine disks based on ANSYS workbench platforms [J]. Procedia Engineering,2015,99:1275-1283.
[16]汪建新,郑小伟 . 基于 Workbench 的直线振动筛运动学和力学分析以及结构改进[J]. 机械强度,2014 ,36 (6):846-849.
[17]姜振廷,郑忠才,董旭 . 基于ANSYS WORKBENCH的六自由度机械臂有限元分析及结构优化[J]. 制造业自动化,2014,36(1):109-110.