赵有俊 仇久安 齐在伟
(天津职业大学,天津 300410)
摘要:文中详细介绍了一种塑料餐盒吸塑成型循环生产系统的工作原理和设备构成,且针对行业现有机型存在体积大、能耗高、成本及耗材成本高等问题,进行了分析并提出了改进办法。研发这款吸塑成型循环生产系统,旨在不降低制品品质的前提下解决上述问题,该生产系统操作、维护简便,适用于中小企业中、小批量实际生产。
关键词:塑料餐盒;吸塑成型;循环系统
引言
近年来,随着互联网时代的快速发展,各种外卖类APP雨后春笋般的涌现,促使外卖餐饮占据了大半个餐饮市场。外卖餐饮市场的兴起为广大消费者带来了就餐的便利,适应了快节奏生活。与此同时,外卖餐饮的发展也大大增加了对外卖饭盒的需求。目前外卖行业大多采用塑料餐盒,以PP、PS、PET等材质居多,该种餐盒无毒无害、耐热、耐腐蚀,可通过回收循环应用到其他领域。
目前塑料餐盒制作工艺多为热塑性塑料片材,经过高温加热软化,通过负压方式使软化片 材覆贴在模具腔内,冷却成型,再经由裁切工位进行裁切拾取以及废料整理。目前餐盒制造行业的生产设备大多采用国外的进口设备,设备庞大,价格昂贵、维修和维护费用高、原材料成本高。国内也有餐盒成型设备制造商,但设备生产工艺也大多沿用国外的工艺及技术。
本研究塑料制品吸塑成型循环生产系统突破现有生产工艺流程,实现从原材料颗粒到成型制 品的连续式规模化生产,避免了片材二次加热的高耗能加热工序,与现有设备相比,该机器的整体能耗大幅度降低,吹吸塑结合成型,使得制品高质量成型,提供了一种结构合理、劳动强度低、能耗低、安全可靠的全自动循环生产系统。该生产系统适用于批量化生产,其推广前景广阔。
一、塑料餐盒吸塑成型循环生产系统的工艺流程
(一)行业现有设备生产工艺流程
聚丙烯(PP)塑料的成型是近年来国外竞相发展的技术,由于PP制品具有耐高温蒸煮、阻湿、廉价等优点,以PP为基材的多层阻隔性实物容器发展极快,成为食品容器的重要发展方向[1]。行业现有设备均以PP等材质的外购成型片材作为原材料,片材上机固定在输送链后经过大幅面、高能耗的加热通道,将片材加热软化,达到成型温度后,成型模具上下模合模,通过负压抽取模内空气,将软化后的片材贴覆在模具内腔完成成型工序,上下模具分离,成型后的片材通过输送链间歇运行送至裁切工位,裁切模具合模裁切后输送链再次运行送至下一工位拾取出料。整个生产设备分为片材加热、负压成型、制品裁切、物料拾取等多个工位,采用间歇式运行方式。其缺点是原料片材成本高,为劳动密集型生产工艺,而且能耗高、生产效率低、科技含量低,并存在“多人一机、机器等人”的现象[2],且多工位设计设备占地面积大。其生产工艺流程分为:上料-片材进成型机-预热-加热-成型-冲裁-落料-成品-包装-边角料收卷[3]。其设备运行流程,如图1所示。
(二) 塑料餐盒吸塑成型循环生产系统工艺流程
塑料餐盒吸塑成型循环生产系统生产工艺采用PP、PS、PET等塑料颗粒作为原材料,通过外购塑料挤出机、辊筒压片机制作生产用片材,压片辊筒可控制片材成型温度,软化片材挂于双工位塑料吸塑成型机的连续输送链上进行片材输送;成型模具、制品裁切刀设置在同一工位,称为成型裁切机构,该机构通过丝杠传动沿片材行进方向做往复运动,与片材同方向运行时完成上下模合模、正负压同步成型、分模、制品裁切、制品顶出动作等多个动作,动作完成后机构快速反回设备指定原点位置等待下一循环过程,同时片材废料继续沿片材输送方向输送,废料经过外购破碎机破碎成塑料颗粒,再通过真空输送系统将破碎后的颗粒送至挤出机储料罐料斗,进行回收利用,裁切后的制品通过气动压料装置压落于收料皮带机进行制品堆叠,当成型制品数量达到额定数量后皮带机横向送出,工作人员进行人工整理装箱。其工艺流程,如图2所示。
二、塑料餐盒吸塑成型循环生产系统结构设计
(一)总体结构
如图3所示,塑料餐盒吸塑成型循环生产系统主要由外购塑料挤出机、塑料压片机、双工位塑料吸塑成型机、废料破碎机、颗粒原材料储料罐、颗粒真空输送系统等设备构成。塑料挤出机及破碎机选用市场上的现有设备。挤出机采用真空输送方式上料,高温加热,再通过输送螺杆将原材料塑料颗粒热熔挤压成高温半成品流体片材。
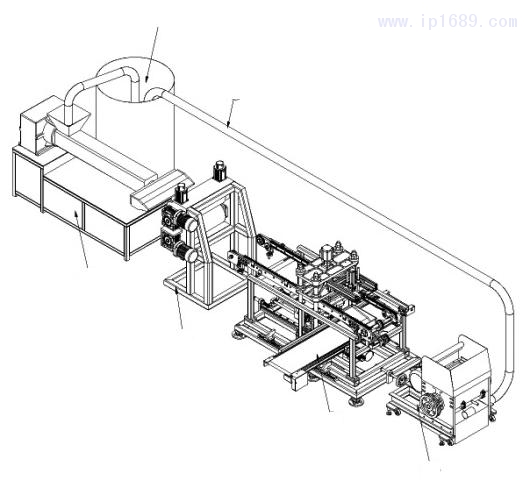
塑料压片机通过两个对滚的镜面辊筒,将流体片材压制成规定宽度的生产用片材,镜面辊筒 内装有温度控制及加热装置,可使成型片材达到生产温度,直接用于吸塑成型。
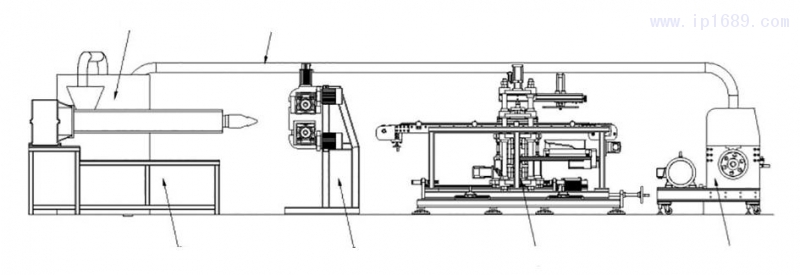
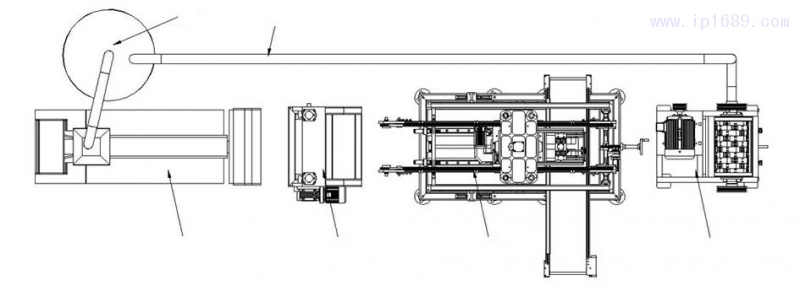
双工位塑料吸塑成型机为连续式运行方式,通过片材输送链将压片机压制的高温片材进行连 续输送,成型裁切机构在片材行进方向上做往复运动,与输送链同步运行,在片材行进的过程中完成吹吸塑成型及裁切工序,裁切结束后分模,成型裁切机构快速返回原点位置进行下一循环的生产。成型制品由于裁切时人为设置有连点,因而可以继续向前移动。当成型制品到达收料皮带机上方时,压料气缸下压,将成型制品连点撕裂,制品掉落到收料皮带机上,皮带机计数堆叠,达到额定数量时皮带机将堆叠好的制品送出,工作人员分拣装箱。
裁切后的废料输送至前段设置的废料破碎机,破碎成原始颗粒状,经由真空输送管路送回 至原材料储料罐内可循环利用。
(二)塑料压片机
如图4所示,塑料压片机构由压片机架体、对滚式镜面压片辊筒、压片压力调节电机、片材输送电机、电气控制等多部分组成。压片机架体由槽钢、方管等材料焊接成型,结实耐用,能承载压片时的压力。两个压片辊筒采用镜面辊筒,可有效地避免片材压制过程中熔融制品的粘黏现象。且辊筒内部安装有温度传感器和加热冷却等温度调节装置,使压制的片材恒定保持制品成型所需的额定生产温度。通过压片压力调节电机可调节成型片材的材料厚度,片材输送电机可调节片材的压制速度。
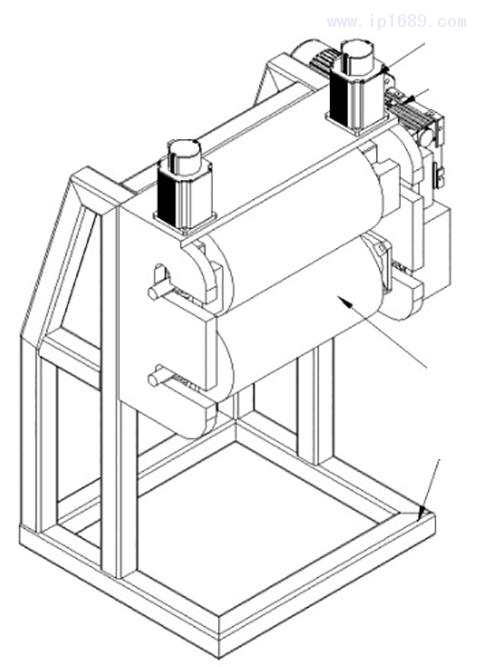
(三)双工位塑料吸塑成型机
双工位塑料吸塑成型机主要由底架组件、片材连续输送链机构、成型裁切机构、出料机构、收料皮带机构、气路系统、PLC控制系统等部件组成。该机器结构示意图和主视图如图5(a)、(b)所示。机器实际运行效率约为2~3秒/版,每版制品数量取决于模具的排版,最大制品尺寸:450长*330 宽*100深。整机功率9kw,机器外形尺3000mm*2200mm*1700mm。
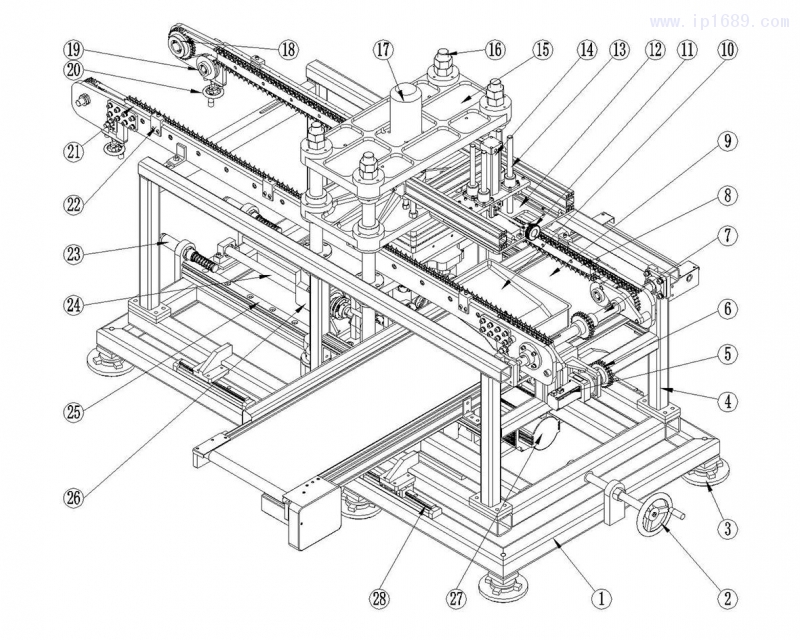
1.底架组件
底架组件承载机体重量,采用方管焊接成型,底部安装有机床垫铁便于调节设备水平。成 型裁切机构往复运行的丝杠、导轨及动力总成均安装在底架组件上,伺服减速电机为丝杠传递动力,成型裁切机构沿导轨方向往复运行,其正向行进速度与输送链同步,反向可快速回程。底架设有调节导轨及调节手轮,实际生产中可在线调节片材张力,以确保热熔片材挂链时不会被拉断或片材垂度过大脱离输送链。往复导轨两端设有缓冲器,有效减缓机构快速回程产生的惯性,保证了往复电机、滚珠丝杠的使用寿命。
2.片材连续输送链机构
片材连续输送链选用伺服电机作为传动动力,通过PLC使输送链及往复行进速度同步,使 得片材在成型裁切过程中不会发生相对位移。输送链条由左右两条链条组件构成,两链条组件宽度间距可手动调节,以满足不同宽度产品的需求。输送链条采用单边带刀尖附件形式的链条,热熔片材挂于链条刀尖处进行输送,链条两侧设有吹风冷却管,用于对链条降温,使片材挂链部分快速冷却定型。
3.成型裁切机构
成型裁切机构由底板、顶板、阳模组件、阴模组件、合模辅助气缸、裁切油缸、导向轴、合 模铰链、合模伺服电机等零部件构成。该机构结构示意图,如图6所示。
成型裁切机构采用四柱结构,导向轴起到引导作用,使阴模阳模组件沿轴向运动完成合模, 同轴运动保证合模精度。同时导向轴也起到支撑、连接顶板及底板的作用。底板、顶板及阴阳模固定板均采用铸钢材质,米字形加强筋结构增强了刚度,模具安装面经过精加工,确保了合模精度及裁切精度。
阴模组件合模动作通过合模减速电机带动铰链动作完成,由于阴模组件重量较重,合模电机 的启动转矩要求较大,为了提高合模电机使用寿命,底板两侧分别安装辅助气缸,以减少电机的启动负荷,有效提高电机的使用寿命。
阳模组件配有正压吹风板组件,吹风板配有密封条、裁切刀模、孔板等。密封条用于确保成 型时模具的密封空间;裁切刀模用于裁切制品;孔板使正压空气充满模具腔体。吹风板结构如图7所示。
阴模组件配备有模具盒组件,模具盒采用钢板焊接成型,其上安装有承切板及模具。模具安 装后模具盒内形成中空腔体,成型过程中通过下置吸风孔抽真空,负压辅助成型。模具盒结构,如图8所示。
成型裁切机构工作流程为:
(1)阳模静止,启动合模电机,辅助气缸同时动作推动阴模完成合模;
(1)阳模静止,启动合模电机,辅助气缸同时动作推动阴模完成合模;
(2)阳模组件通入高压空气正压成型,同时阴模组件抽真空形成负压,正负压结合成型,使制品质量大幅度提升;
(3)阳模裁切液压缸下压,使合模密封条形变,置于阳模的裁切刀与阴模承切板接触以完成裁切动作,裁切刀采用定制激光刀模,刀条设有3~4处0.2mm缺口,使得裁切后制品既可与片材连接而不脱离,又能在气缸下压时顺利落料;
(4)裁切结束,阴模阳模同时返回原位,循环运行。
4.成品出料机构
成品制品采用下压出料方式,其结构包括铝型材框架、位置导向轴、位置调节螺杆、安装 板、压料气缸、压料导向轴等零部件组成。出料机构可安装在成型裁切机构上,随成型裁切机构同步往复运行,也可安装与设备架体上,固定位置下压出料。气缸下压出料,行程短,反应速度快,可使制品快速压出。
5.收料皮带机构
收料皮带机构采用食品级输送带,步进电机驱动。PLC采集出料机构气缸信号,进行计数堆 叠,达到额定值后收料皮带间歇运行将成型制品送出,人工收料装箱。
三、结语
塑料餐盒吸塑成型循环生产系统的开发不同于传统设备的生产工艺,实现了从原材料颗粒到成型制品的连续式规模化生产,避免了片材二次加热的高耗能工序,使机器的整体能耗低于现有设备,吹吸塑结合成型,自动化控制节省劳动力并降低人工成本,材料循环利用系统大幅提高了材料的利用率,降低了生产成本。该生产系统适用于批量化实际生产,其推广前景广阔。
参考文献:
[1]张根军. 台达机电产品在塑料杯热成型机上的应用[J]. 伺服控制. 2013(01):82-85.
[2]黄学佳,包能胜,谢荣生,蔡健伟.集成吸塑成型冲切一体化工艺的全自动片材设备的研制[J].包装工程,2011(07):72-75+121.
[3]余磊.四方伺服控制系统在成型机上的应用[J].伺服控制,2015(Z2):46-47+45.