丁永峰,龙婵娟
(重庆文理学院机电工程学院,重庆 402160)
摘要:以某畅销手机后盖为例,采用正交试验方法,应用 MoldFlow 软件模拟了注射时间、熔 体温度、模具温度、保压压力等对 PC+ABS工程塑料合金制件最大翘曲变形量的影响,得到最佳的注塑工艺参数;采用模拟得到的最佳工艺参数进行试制生产,以验证模拟结果的可靠性。结果表明:注塑工艺参数对手机后盖薄壁制件翘曲变形影响的主次顺序为注射时间、熔体温度、模具温度、保压压力;模拟得到制件的最佳注塑工艺参数为注射时间0.40s,熔体温度280℃,模具温度72℃,保压压力60MPa,此时制件的最大翘曲变形量最小,为0.5090mm,翘曲变形主要出现在手机后盖四角处,耳机插孔旁的翘曲变形量最大;在优化工艺参数下试制产品的最大翘曲变形量为0.530mm,翘曲变形位置与有限元模拟结果一致,这验证了模拟结果的可靠性。
关键词:翘曲变形;薄壁制件;注塑成型;正交试验;有限元模拟
0 引 言
随着5G 时代 的 到 来 以 及“智 慧 城 市”的 推 广,智能手机、超级本、智能家电等电子设备的设计更加 趋向于高质、轻薄、美观,产品的结构更趋于复杂,这对塑料制件的研发与应用提出了更为严格的要求,包括更高的零件材料性能要求,更苛刻的产品的尺寸精度要求。 塑料制件,特别是薄壁制件在生产过程中会出 现较大的翘曲变形、收缩等缺陷[1],这不仅会影响产品的外观,还会延长产品的开发周期。目前,国内外研究者对薄壁制件的工艺优化进行了大量的研究工作。蔡厚道等[2]利用有限元分析方法对液晶显示器(LCD)外壳进行了优化设计,提高了薄壁产品的成型质量。肖国华等[3]利用 MoldFlow 有限元软件对iPad平板电脑面壳的浇注系统、成型工艺等进行了分析及优化。孟兵等[4]以前风窗导流板为例,分析了角落效应对塑料制件翘曲变形的影响,并对零件的壁厚进行了优化。赵龙志等[5]利用 MoldFlow 软件对汽车卡扣座注塑塑成型过程中的材料种类、熔体 温度、模具温度等参数进行了分析及优化。江舜成等[6]利用 MoldFlow MPI软件建立了浇口宽度、制品壁厚、注射速度、制品直径等参数的函数关系式,通过分析各参数对能耗的影响规律,拟合出关于能耗的函数关系式。王树勋[7]对薄板零件在注射成型过程中出现翘曲的原因进行了分析,并改进了模具的结构。KITAYAMA 等[8]采 用 多 指 标 模 型 对 一 方 盒 零 件 的 成 型 过 程 进 行 了 分 析 与 优 化。KOVACS等[9]重点研究了在注射成型过 程 中 塑 料制件拐 角 处 的 冷 却 效 应。AZAMAN 等[10]对 以 木屑为填充物的薄壁零件在注射成型过程中的收缩与翘曲变形进行了研究。SINGH 等[11]通过多响 应 优化法降低了塑料零 件 在 成 型 过 程 中 的 耗 时 与 翘 曲 变形程 度。OKTEM 等
[12]应用田口设计方法,以信噪比为手段,研究了在薄壁零件成型过程中各工艺参数对翘曲变形的影响规律。上 述工作主要从不同方面研究了 工 艺 参 数 对 薄 壁 制 件 翘 曲变形或收缩等缺陷的影响规律,但 综 合 采 用 试 验 设 计与有限元模拟方法 研 究 薄壁制件翘曲变形的报道较少。为此,作者以 某 畅 销 手 机 后 盖 为 例,采 用 正 交试 验 方 法,应 用 MoldFlow 软 件 模 拟 了 注 射 时 间、熔体温 度、模 具 温 度、保 压 压 力 等 对 制 件 最 大翘曲变形量的影 响,得 到 最 佳 的 注 塑 工 艺 参 数;采用模拟得到的最佳工艺参数对品进 行 试 制 生产,以验证模拟结果的可靠性。
试验设计方法
1.1 产品结构及成型工艺
某手机后盖产品模型如图1所示,产品外形尺寸为131MM×67MM×7.1MM,体积为10.22cm,最大投影面积为87.77CM2,平均壁厚 为1MM,最 小壁厚仅为0.4MM,属于典的塑料薄壁。该制件的尺寸公差为 MT3级,脱模斜度为30′~1°,外表面应光滑,不允许有斑及熔接痕,内表面无成型缺陷。塑料熔体充填流程较长,充填较困难,拟采用注塑成型工艺。将浇口位置设置在制件内表面,分模面为 制件最大投影处;脱模方式采用推板推出机构,以确保产品平稳可靠推出。
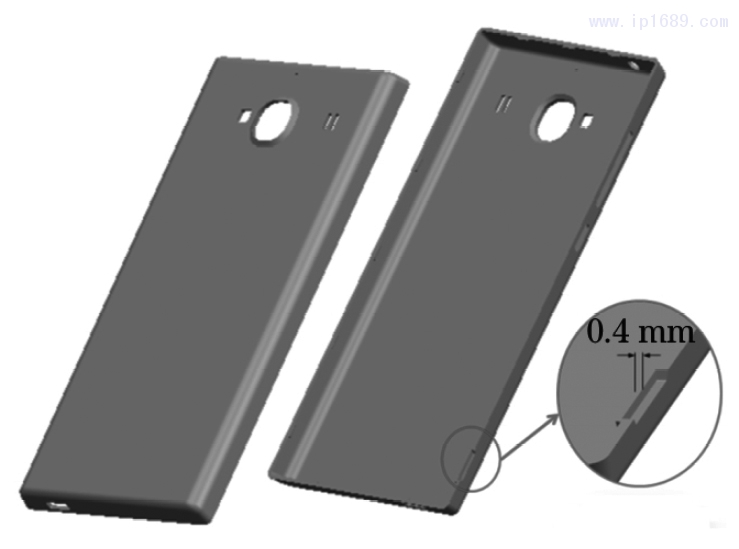
1.2 材料属性
为满足薄壁及复杂制件成型的要求,材料选用 DaiCElPolyMEr公司生产的工程塑料金 (PC+ ABS)。PC+ABS是 一 种 无 定 形 塑 料,兼 具 优 良 的尺 寸 稳 定 性 及 良 好 的 流 动 性,其 比 热 容 为1720J·Kg-1·K-1,熔体密度为0.98g·CM-3,固 体 密度为1.12g·CM-3,收缩率为0.5%~0.7%,熔点 为175~185 ℃。
研究表明,材料的 PVT(压力-体积-温度)关系是影响注塑产品体积收缩程度的主要因素[13],而因体积收缩产生的内应力会使产品产生翘曲、收缩等 缺陷[14-15]。材料的PvT 特性对于计算较宽温度和 压力范围内聚合物的体积性质有着重要的意义。由文献[16]可知,PC+ABS聚合物熔体的体积与温度为正相关性,与压力为负相关性。由文献[5]可知,PC+ABS为典型的假塑性流体,随着温度及剪切速率的增大,熔体的黏度降低。
1.3 有限元模型参数设计
1.3.1 模型网格划分
运用有限元分析工具可以较好地模拟整个制件 的成型过程[17]。将计 算 机 辅 助 设 计(CAD)模 型 导入 MoldFlow 软件中,并对模型进行网格划分及优化[18],网格类型为 Fusion网格,数量为8670个,节 点数为 4321,最 大 纵 横 比 为 9.7,平 均 纵 横 比 为 1.90,网格匹配率为92.8%。
1.3.2 成型窗口分析
根据运算得到最佳浇口位置,建立浇注系统及冷却 系 统。 采 用 潜 伏 式 点 浇 口,冷 却 水 管 直 径8MM,单 面 冷 却 管 道 6 条,管道中心之间距离30MM,管道之间使用软管进行连接,冷却水温度为25 ℃,所得薄壁制件有限元模型如图2所示。根据有限元模型进行成型窗口分析,以确定最佳初步工艺参数,并用作后续步骤的初步输入参数。经成型窗口 分 析 得 到 最 佳 成 型 工 艺 参 数 为:注 射 压 力180MPa,模具温 度72.22 ℃,熔 体 温 度290 ℃,注射时间0.34s。
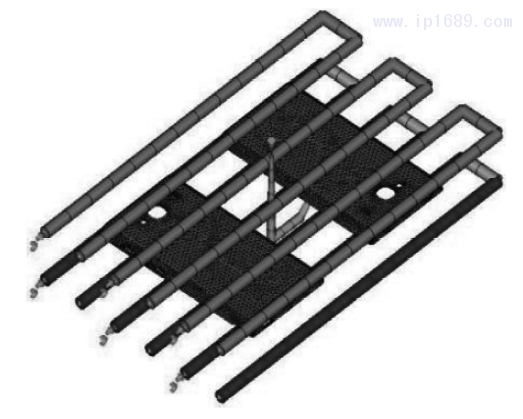
1.3.3 正交设计
采用正交设计来分析不同成型工艺参数下塑料制件因收缩 不 均[19]而 产 生 的 最 大 翘 曲 变 形 量。结合上 述 的 分 析 结 果,并 查 阅 相 关 文 献[20-22],综 合 确定注射时间、熔体温度、模具温度及保压压力为试验 因素。其中:注射时间应保证制件充填完全;熔体温 度应确保材料处于熔融状态且不会发生降解,同时在一定的成型工艺下不会发生短射;模具温度不应使材料熔融黏度增大;保压压力应使制件具有较好的尺寸稳定性及力学性能,同时不应使残余应力过大而造成脱模困难。由此设计出了如表1所示的4因素3水平的 L9(34)正交表。
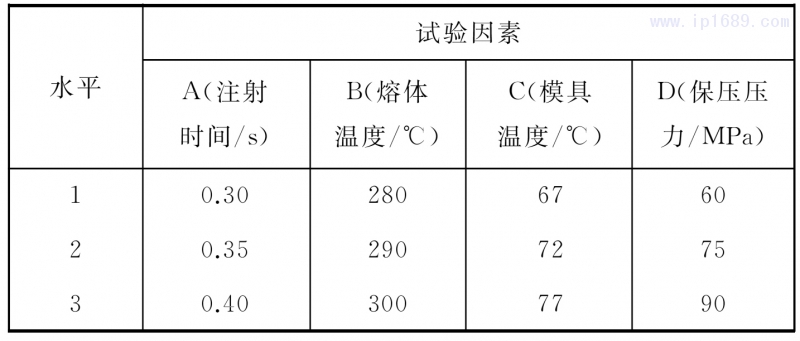
2模拟结果及分析
根据表1的因素水平,采用 MoldFlow 软件进行正交矩阵模拟,得到制件在不同工艺参数组合下的最大翘曲变形量,结果如表2所示。将所得结果进行分析计算,得出各因素在每个水平下的最大翘曲变形量均值K,并计算相应因素的极差 R。由表2可知:对 薄壁制件翘曲变形影响的主次顺序为 A,B,C,D,即注射时间、熔体温度、模具温度、保压压力,最佳工艺分散组合为 A3B2C1D3;随着注射时间的延长和熔体温度的降低,最大翘曲变形量降低;随着模具温度的增大,最大翘曲变形量先降低后增大;随着保压压力的增大,最大翘曲变形量先增大后降低。
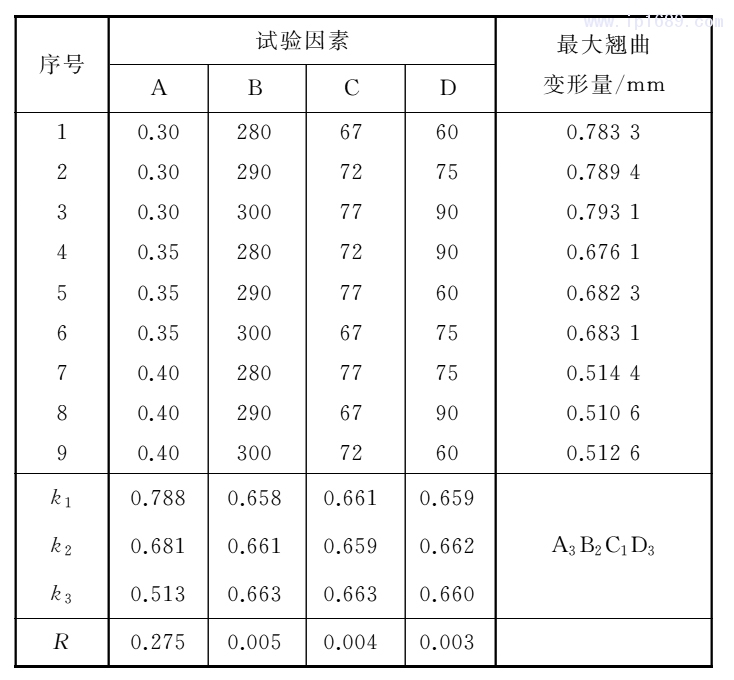
最佳工艺参数组合 A3B1C2D1未出现在正交表中,为验证其可靠性,在 MoldFlow 软件中再次运行该注塑模拟。由图3可以看出,最佳工艺参数下翘曲变形主要出现在手机后盖四角处,且耳机插孔旁的翘曲变形量最大,为0.5090 MM,小 于 表2中 的所有数据。同时,对制件结构进行分析后,发现此处也是塑料熔体流动最为复杂的区域,且位于注塑模具的拐角部位,散热条件较差,极易发生翘曲变形。
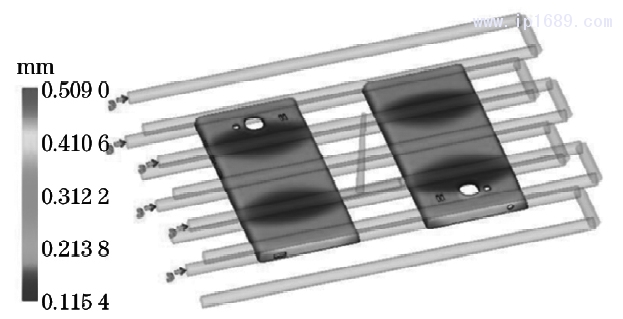
综上,模拟得到此薄壁制件的最佳工艺参数为:注射时间0.40s,熔体温度280 ℃,模具温度72 ℃,保压压力60MPa。
3试验验证
采用上述优化的工艺参数对薄壁制件进行生产试制,得到的手机后盖的外观如图4(a)所示。采用daisyPH10T 型柔性三维激光扫描仪对试制产品进行点云扫描,获 得 点 云 数 据 模 型,如 图 4(B)所 示。将点云数据模型及原始三维模型导入 GEoMagiC软件中,以点云数据为测试模型,原始三维模型为参考模型,在 GEoMagiCQualiFy中将测试模型与参考模型进行比较,得 到 如 图4(C)所 示 的 尺 寸 检 测 云 图。由图4(C)可以看出,翘曲变形主要出现在手机后盖四角处,耳机插孔旁的翘曲变形量最大,为0.530MM,与有限元模拟结果基本吻合。
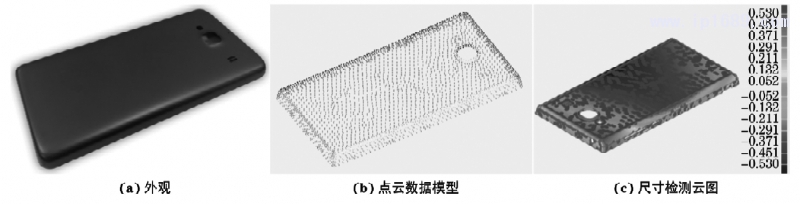
4 结 论
(1)应用正交法模拟得到影响手机后盖薄壁制件翘曲变形的工艺参数的主次顺序为注射时间、熔体温度、模具温度、保压压力;随着注射时间的延长和熔体温度的降低,最大翘曲变形量降低;随着模具温度的升高,最大翘曲变形量先降低后增大;随着保压压力的增大,最大翘曲变形量先增大后降低。
(2)模拟得到手机后盖薄壁制件的最佳注塑工艺参数为注射时间0.40s,熔体温度280 ℃,模具温度72℃,保压压力60MPa,此时制件的最大翘曲变形量最小,为0.5090 MM,翘 曲 变 形 主 要 出 现 在 手机后盖四角处,耳机插孔旁的翘曲变形量最大;在优化工 艺 参 数 下 试 制 产 品 的 最 大 翘 曲 变 形 量 为0.530MM,且翘曲变形位置与有限元模拟结果一致,这验证了有限元模拟的可靠性。
参考文献:
[1] SIN LT,RAHMAN W A W A,RAHMAT A R,et al. Computer aided injection moulding proces analysis of polyvinyl alcohol-starch gren biodegradable polymer compound[J].Journal of Manufacturing Proces,2012,14 (1):8-19.
[2] 蔡厚道,陈云.LCD外壳注塑成型缺陷 CAE分析与工艺优化 [J].塑 料 科 技 ,2017,45(4):84-88.
[3] 肖 国 华 ,董 彦 ,张 适 ,等 .Ipad 平 板 电 脑 面 壳 成 型 CAE 优 化 分 析 [J ] . 塑 料 工 业 , 2 0 1 3 , 4 1 (8 ) : 6 6 -7 1 .
[4] 孟兵,徐静,苏艳红,等.角落效应对塑料件翘曲变形的影响 [J].工 程 塑 料 应 用 ,2015,43(7):67-69.
[5] 赵 龙 志 ,陈 炳 辉 ,杨 敏 ,等 .Moldflow 在 注 射 成 型 翘 曲 优 化 中 的 应 用 [J].中 国 塑 料 ,2010,24(5):78-80.
[6] 江舜成,文劲松,谢海玲,等.基于 MoldFIow MPI软件的注 射 阶 段 能 耗 研 究 [J].中 国 塑 料 ,2015,29(4):70-74.
[7] 王树勋.基于 Moldflow的薄板塑件翘曲成因与改善措施[J]. 模 具 工 业 ,2010,36(6):10-13.
[8] KITAYAMA S,YAMAZAKI Y,TAKANO M.Numerical and experimental investigation of proces parameters optimization in plastic injection molding using multi-criteria decision making [J].Simulation Modeling Practice and Theory,2018,85:95-105.
[9] KOVACS J G,SIKLO B.Investigation of cooling efect at corners in injection molding[J].International Communications in Heat and Mas Transfer,2011,38:1330-1334.
[10] AZAMAN M D,SAPUAN S M,SULAIMAN S.Shrinkages and warpage in the procesability of wood-filed polypropylene composite thin-waled parts formed by injection molding[J]. Materials & Design,2013,52:1018-1026.
[11] SINGH G,PRADHAN M K,VERMA A.Multi response optimization of injection moulding proces parameters to reduce cycle time and warpage [J]. Materials Today: Procedings,2018,5:8398-8405.
[12] OKTEM H,ERZURUMLU,UZMAN T I.Application of Taguchi optimization technique in determining plastic injection molding proces parameters for a thin-shel part[J]. Materials & Design,2007,28(34):1271-1278.
[13] CHAKRAVORTY S. PVT testing of polymers under industrial proces sing conditions[J].Polymer Testing,2002, 1(3):313-317
[14] SIN LT,RAHMAT A R,RAHMAN W A W A,et al. Rheology and thermal transition state of polyvinyl alcohol- casava starch blends[J].Carbohydrate Polymers,2010,81 (3):737-739.
[15] 丁永峰,胡仕杰.基于正交试验的瓶盖注塑成型数值模拟及 工 艺 优 化 [J].塑 料 科 技 ,2018,46(7):91-94.
[16] 王 建 ,杨 卫 民 ,谢 鹏 程 ,等 .聚 合 物 PVT 关 系 在 线 测 试 技 术 [J].塑 料 工 业 ,2008,36(10):28-30.
[17] 徐 戊 矫 ,丁 永 峰 ,邹 明 平 ,等 .大 型 厚 壁 封 头 热 锻 成 形 中 降 低 成 型 载 荷 的 策 略 [J].热 加 工 工 艺 ,2011,40(7):76-78.
[18] 丁 永 峰 .基 于 CAD/CAE 的 止 鼾 舌 套 注 塑 模 设 计 [J].塑 料 科 技 ,2018,46(10):100-103.
[19] 王冠,王旭林,寇琳媛,等.基于多因子交互作用的 PP/ EPDM 复 合 材 料 注 射 成 型 工 艺 优 化 [J].机 械 工 程 材 料 , 2018,42(3):87-94.
[20] OLIAEI E,HIDARI B S,DAVACHI S M,et al.Warpage and shrinkage optimization of injection-molded plastic spoon parts for biodegradable polymers using Taguchi,ANOVA and artificial neural network methods[J].Journal of Materials Science & Technology,2016,32(8):710-720.
[21] BIRAT K C,FARUK O,AGNELLI A M ,et al.Sisal-glas s fiber hybrid biocomposite:Optimization of injection molding parameters using Taguchi method for reducing shrinkage[J]. Composites Part A: Applied Science and Manufacturing, 2016,83(1):152-159.
[22] CHEN C P,CHUANG M T,HSIAO Y H,et al.Simulation and experimental study in determining injection molding proces parameters for thin-shel plastic parts via design of experiments analysis[J].Expert Systems with Applications, 2009,36(7):10752-10759.