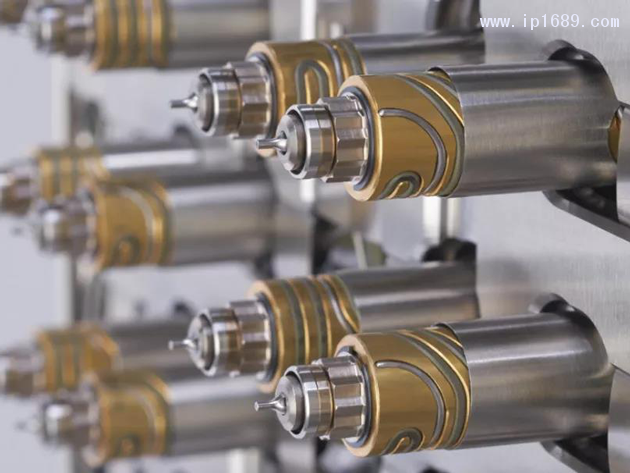
作为最初的熔体输送系统,冷流道仍然在注塑成型中占有一席之地,但随着市场对塑料零件的需求、以及所需产量上升时,转向热流道可以解锁并带来诸多优势。
在注塑成型过程中,模具最重要的功能之一是将熔体从料筒输送到型腔。熔体输送管理对注塑产品的最终质量和生产线的终极成功有着极大影响。树脂流量、压力和温度的精准控制至关重要。对这一点的充分理解则直接影响熔体输送系统的设计,因此针对热流道和冷流道解决方案进行深入的比较与解析,意义非凡,极为必要。
冷流道是在模具分型面加工若干通道而随之形成的,为熔融树脂流经浇口进入型腔提供通道。熔化的树脂冷却并变硬,与注塑部件一起推出,紧接着运行下一个生产周期,周而复始,循环往复。冷流道系统通常对模具起始成本或初始资金支出的影响较低。它们通常应用于生产运行期间较短或不频繁,以及型腔数较少的模具中。
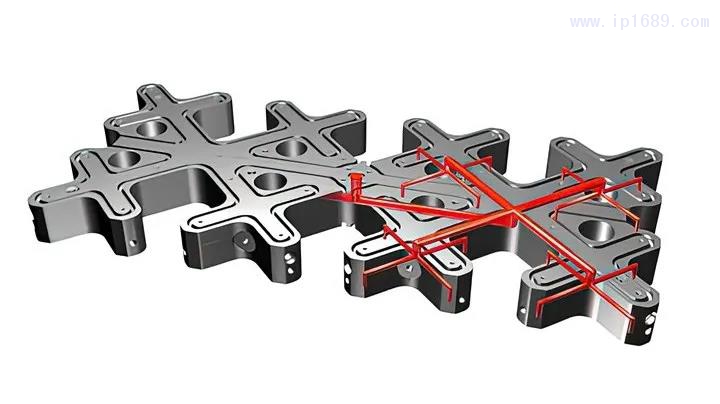
典型热流道的分流板
熔融树脂流经封闭熔体通道而形成的流动路径用红色标记
随着一些注塑部件市场需求的攀升,制造解决方案逐步朝着更高腔位的模具过渡。当这种情况发生时,冷流道则对加工和成本产生更大影响。更大的流道系统意味着可以注入、冷却和处理更多的树脂。冷流道的布局可能很复杂,而且为了容纳流道,型腔之间必须保持较大的间隔距离。
针对高产量和产品使用周期长的应用,热流道的使用所带来的益处最为显著;而对于较低腔位模具而言,情况同样如此,因为速度和一致性对持续改进非常重要。
由于在充填阶段熔体仍然不断输送到型腔,因此冷流道还会延长生产周期。冷流道的厚度通常比注塑部件的厚度更大,所以,冷却并达到足够安全的操作条件所需要的时间最长。此外,冷流道的浇口熔渣可能需要更长的合模行程才能去除,这又增加了每个生产周期的耗时。当模具打开时,需要花费时间将流道从模具中卸下——要么通过重力,要么通过拆卸工具。当下一个生产周期开始时,冷流道依然如此。这意味着不得不报废流道,或者通过重新研磨循环使用于其他加工中,亦或便宜卖掉。
另一个途径
升级换代的熔体输送系统就是热流道。其功能类似于冷流道,因为它为熔融树脂提供了一条路径,使其流过精心设计、精准加工的系统,而绝不允许熔融树脂凝固。配送网络完全包覆在钢制分流板中,而不会暴露在空气里。分流板将熔融树脂分配到注嘴,注嘴提供了通向浇口和型腔的通道。分流板和注嘴由热电偶和加热器调节,保持熔融塑料的温度。打个比方,冷流道就像是露天的城市街道,而热通道则更像是一条地铁隧道。
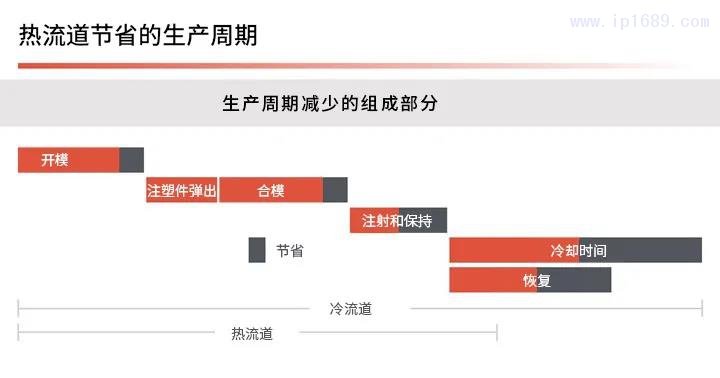
典型的注塑周期及其步骤分解
冷流道模具和热流道模具所需时间的对比
热流道通常被认为是注塑成型过程中最精密的系统之一。各种材料及其特性有助于整体工程设计和最终工艺执行。根据树脂和应用情况,浇口设计和温度控制有多种选项可供选择。浇口既可以选用热点式注嘴,也可以选择机械控制的阀针式注嘴。如何与模具互动,这些都有其设计要求。温控器可用于过程监控、控制和微调。
不再需要处理冷流道
热流道无需在加工前、加工中和加工后处理冷流道。不再需要耗费时间、通过工作人员或机器人来拆卸固化的热流道或重新研磨,所有这一切都意味着成本降低——减少设备维护,更好地利用宝贵的场地空间,节省宝贵的时间。
缩短生产周期可以增加产量。一些注塑生产环境和工具室还贴着宣传海报,上面写着:“将生产周期从10秒减至9秒,产量增加11%。”要估算生产周期变化对产出的影响,请用当前时间除以所需时间(以相同单位)。这给出了一个在任何时间范围内都能使用的乘数。下方表格提供了生产周期和所得出的乘数。增加的产量以绿色突出显示,减少的产量以红色显示。
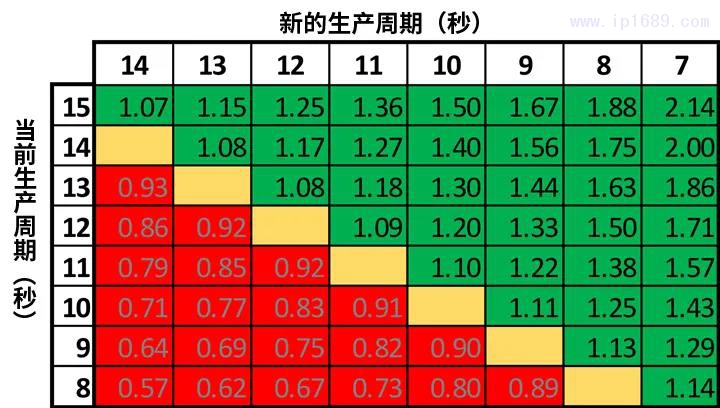
达到新的生产周期后,用于预估产量的生产周期和乘数表。
提升以绿色突出显示,而减少则以红色标记。
临界点
以一个64腔冷流道模具为例,假设生产周期为14秒,一天三班倒,一周七天。如果正常运行时间约占90%,每年它将运行大约200万个生产周期,制造大约1.293亿个注塑部件。重量2克的注塑部件以及重约192克的冷流道的射出总重量相当于320克。
这种射出重量每年几乎要耗费656,900kg材料,但其中仅有259,000kg为制造出的合格产品。剩下的60%必须重新循环、处理、盘点和运输。如果相同的注塑部件采用64点热流道直接浇注,那么需要采购的材料就会大大减少,而且生产周期也会更快。以10秒为一个周期,一年有可能运行280万次,制造1.811亿个注塑部件。在工作单元所占空间不变的情况下,产生如此的生产力提升并不少见。
加强控制
除了减少浪费和提高产量外,热流道还能更好地控制注塑部件品质、尺寸精度和表面光洁度。浇口位置不必再局限于周边,且可以移动并以一种更好的方式引导熔体流,这种方式对关键尺寸或受填充特性影响的其它特征产生更有利的影响或作用。还有可能缩短总流动长度,从而降低型腔填充压力要求和影响注塑部件变形的其它工艺要件。预计的总面积和锁模吨位要求也可能随之降低。
注塑成型过程中发挥作用的所有设备之中,在对模具中独立型腔产生影响的调整方面,热流道提供了最大的灵活性。虽然冷流道也可以调校,但除非模具的设计允许快速拆卸或更换冷流道镶块,否则调查、调整和检验可能会有很长的准备时间。更改往往是手工进行的,使其具有迭代性,且难以替换。恢复到原始状态可能相当耗时。可以通过焊接添加钢材,但需要修磨,且材料抗疲劳性能可能受损。
如果没有绝佳的浇口设计和摆位,我们熟知和推崇的一些标志性包装和消费类电子部件或将永远无法实现。
注塑料筒和机器锁模影响全部过程。更换模腔需要排空冷却液,并且机械强度大,特别是在高腔位模具上。热流道的注嘴头可以迅速更换,无论加热器位置的改变,亦或区域温度的调整,其对整体品质的影响可以即刻做出评估。
给予注塑部件更大的设计自由度
表面光洁度是终极差异化因素。设计精良的浇口位置可以制造功能性更强的部件,且具备更好的表面光洁度。由于浇口可以重新定位到注塑部件上的任何位置,因此可以消除流道修整、二次操作及一致性不佳等问题。
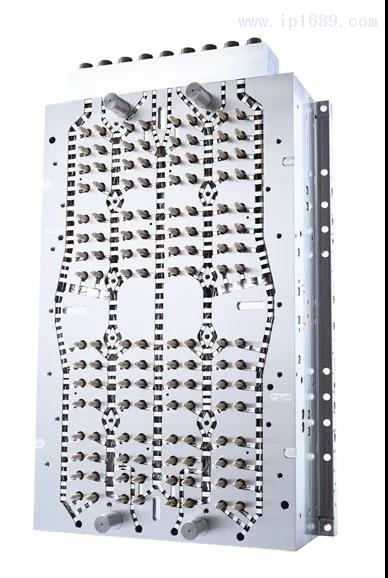
配置在热半模上的高腔位热流道
这对于冲洗等应用而言,尤为重要——在冲洗过程中,单个水滴的流量均受控;在医疗领域,必须将外科医生医用手套于浇口痕迹上撕裂的风险降至最低;在卫生保健方面,导管则必须尽可能地顺滑。如果没有绝佳的浇口设计和摆位,我们熟知和推崇的一些标志性包装和消费类电子部件或将永远无法实现。
针对高产量和产品使用周期长的应用,热流道的使用所带来的益处最为显著;而对于较低腔位模具而言,情况同样如此,因为速度和一致性对持续改进非常重要。最终,通过出色的熔体控制和加工性能令成型工艺得到优化,进而得以制造更高品质的注塑部件,并获得更高的产能。
随着热流道技术的进步,我们发现从冷流道向热流道转变的势头持续强劲。伴随塑料部件设计不断突破界限,降低树脂用量继续成为所有模塑商的头等大事,注塑成型领域的面临的挑战仍在增加。我们可以预见到:在先进、复杂的热流道技术加持下,熔体输送管理将在注塑工艺中发挥越来越重要的作用。