摘要:针对常规的管材液压成形技术需要昂贵的专用设备及模具、生产效率低等不足,开发了一种简单实用、可在冲床或压力机上使用的管材冲击液压成形装置,可用于薄壁金属管材的自然胀形、轴压胀形和异形截面中空件的冲击液压成形。该装置无需外部高压供给系统和专用液压成形设备,通过撞击轴压头挤压容腔中液体的方式来为管材提供液压力和轴压力。通过设计轴压头的行程和调节溢流阀的溢流压力值等来实现最大液压力和轴向进给量的合理匹配,并以304不锈钢毛细管和H65黄铜毛细管为试验管材做了相关试验。研究结果表明:该装置结构简单、操作方便;可实现最大液压力与轴向进给量的协调控制;合理的载荷匹配能显著地提高管材冲击液压成形的成形性能;H65黄铜毛细管破裂时所需的液压力小于304不锈钢毛细管破裂时所需的液压力。
关键词:管材;冲击液压成形;最大液压力;轴向进给量;载荷匹配
冲击液压成形技术(Liquid Impact Forming,LIF)是在管材液压成形技术(Tube Hydro- Forming,THF)的基础上进行改进的。THF是用于生产截面形状复杂的薄壁管状零件的一种先进、特殊、精密(半精密)的净成形技术,具有成本低、工序少、质量轻、刚度高等特点,但是常规的THF技术需要昂贵的专用设备及模具,而且生产效率低(只有传昂贵的专用设备及模具,而且生产效率低(只有传统冲压方法的1/3)[1-3]。针对THF技术的不足,美国Greenville Tool&Die公司最近提出一种新型成形技术—LIF技术。LIF技术是一种通过结合冲击和液压成形,将薄壁管或薄壁板成形为不同形状零件的成形技术,其原理是液体介质受到高速运动的冲击体挤压,瞬时变为高压液体而作用于零件表面,进而获得期望的胀形件。该技术因具有成形速度快、成形质量高、成本低等特点而被应用于汽车、航空工业领域[4]。
在LIF中,动能、电能、化学能等可为冲击的动力源,因其能量利用率高而在其他文献中称之为高能率冲击液压成形。目前,关于冲击液压成形的研究较少,鲜见相关文献。在国外,白俄罗斯Chachin V N等[5]用压缩空气为动力源的设备研究了冲击液压成形技术。南非的Kosing O E等[6]开展了冲击液压成形的工艺参数理论和实验研究。这些国外学者所使用的设备或装置都是以压缩气体作为动力源。在国内,中国科学院金属研究所徐勇等[7]研究员已开始研究相关高能率冲击液压成形技术。桂林电子科技大学Huang C M等[8]开展了相关冲击液压成形装置的研究,其装置是以电能为动力源。目前,该技术虽然在工业上已得到应用,但尚未得到推广。管材LIF技术是一项极具发展潜力的先进成形技术,因此,开发一种管材LIF装置可挖掘管材LIF技术的研究和应用价值。
针对现有的LIF装置存在结构复杂、操作不便等不足,本文开发了一种新型的管材LIF装置,该装置不仅不需复杂的外部液压供给系统,而且无需螺钉等连接零件,更便于试验操作。
1.管材冲击液压成形装置的设计
1. 1结构设计特点及要求
本文开发的管材冲击液压成形装置示意图如图1a所示,其主要结构特点及要求如下。
(1)高压液体的生成。在管材冲击液压成形中,在管材内腔形成高压液体是管材成形的必要条件。如图1所示,安装有Y型密封圈的轴压头在外载荷S的作用下,高速挤压容腔内的液体,使其内部液压力急剧升高,高压液体同时通过轴压头的通液孔进入两段密封的管材内腔,进而使管材得到成形所需的液压力。为保证管材能达到预期的变形程度,容腔内的液体体积的变化应大于管材塑性变形后内腔容积的变化,当管材内部的液压力达到预定的溢流压力值时,溢流阀开始溢流。
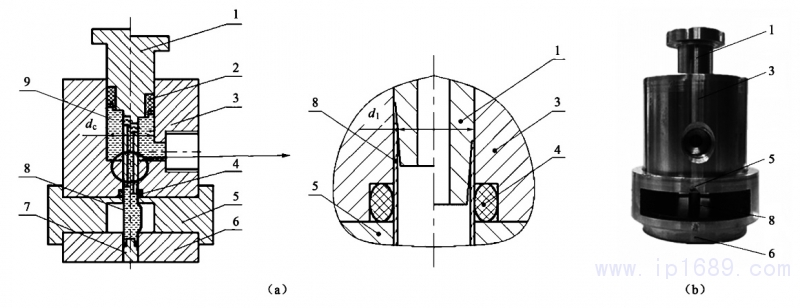
图 1管材冲击液压成形装置的示意图 ( a)和实物图( b)
1. 轴压头 2. Y 型密封圈 3.容腔 4. 管材 5. 模腔 6. 密封柱 7. 定位圈 8. O 型密封圈 9. 液体
(2)实验装置的密封。实验装置的良好密封性是决定管材达到预期成形效果的一个重要因素,因此,在管材两端必须要有良好的密封。在本成形装置中,管材两端的密封原理一样,区别在于O型密封圈的密封点不同。安装于容腔中的O型密封圈对管材上端外壁进行密封,而安装于密封柱中的O型密封圈对管材下端内壁进行密封,当轴压头挤入装满液体的容腔中后,由管材两端的O型密封圈对管材内部形成了初始密封。轴压头受到撞击而推动管材下移,管材两端部分别被挤到轴压头、密封柱中的锥形台阶上,与O型密封圈共同作用,实现了管材两端的再次密封。
(3)轴向进给量的控制。管材在成形过程中,为防止管材出现屈曲、弯曲等成形缺陷,成形区需要得到有效地补料,而在冲击液压成形中,轴向进给量是补料量的决定因素。轴压头的轴肩顶在管端,推动管材下移,轴压头下移量与管材的轴向进给量成正比。本装置先通过在装置下面放置垫块初步调整装置距冲头的距离,再通过微型冲床的行程调整螺进行微调,从而准确地控制管端轴向进给量。
(4) 最大液压力与轴向进给量的协调控制。在LIF过程中,合理的加载路径可以有效地挖掘潜在的管材成形性能,本装置可以通过垫块等控制轴向进给量,但由于成形过程所需要的时间极短而导致液压力难以控制,而安装在溢流口处的溢流阀可以有效地控制管材胀形过程中的最大液压力。本装置通过调节行程调整螺和设置溢流阀中的溢流压力值,来实现最大液压力与轴向进给量的协调控制。
1.2 主要参数的确定
本装置的主要参数是设置在容腔中的液压腔尺寸及设置在轴压头中的通孔直径大小,可根据下述方法来确定。
1.2.1液压腔的尺寸
液压腔的尺寸设计是基于文献[9]中所述的方法来确定。
(1)液压腔直径。根据文献[9]所述,液压腔体积V的减小应大于管材塑性变形后管材内腔体积的变化量V变与液压腔中所密封的空气之和。本装置中,在轴压头挤入液压腔的过程中,将容腔中的空气排尽。因此,液压腔体积V只要满足式(1)即可。


液压腔为圆柱体,其体积为:


式中:h为轴压头在液压腔工作时滑动的高度,mm;dc为液压腔直径,mm;d1为轴压头处在液压腔液体中的轴直径,mm,其值取试验管材外径D0。
管材塑性变形后管材内腔体积的变化量为:


式中:K1为修正系数,取1~2;R0为管材内半径,mm,R0=d0/2;d0为管材内径,mm;R2为管材胀形区两端部的圆角半径,mm,R2=R1-R0;R1为管材最大胀形半径,mm;l1为管材胀形区长度,mm。
为提高装置的稳定性,可降低装置重心,则h=dc,将式(2)、式(3)代入式(1)中即可得到液压腔直径:
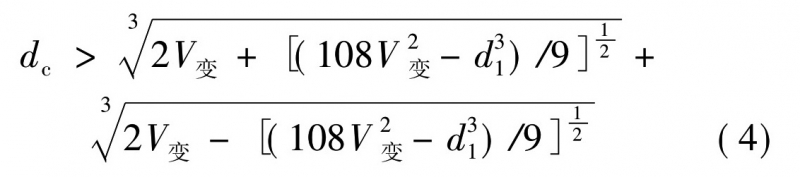
(2)液压腔深度。轴压头与容腔中的液压腔为滑动配合,轴压头需对容腔导正,则液压腔深度为:


式中:l2为容腔中液压腔的导正长度,mm,根据经验,取l2=h/4。
1.2.2 轴压头中通孔直径
在管材成形过程中,液压腔中的液体应能有效地补给到管材胀形区内,否者管材因得不到充分的胀形而影响成形质量。在管材冲击液压成形中,在轴压头受到撞击时到管材胀形成形结束这段时间t内,轴压头中通孔允许液压腔中液体进入管材内腔的最大的体积量V进应大于管材塑性变形后管材内腔体积的变化量,即:


液压腔中液体通过轴压头中通孔进入管材,其进入液体体积为:


式中:d2为轴压头中通孔直径,mm;v为轴压头挤压液体的速度,(mm•s-1)。将式(3)、式(7)代入式(6),可得:


1.3 装置主要工作方式
(1)自然胀形。将轴压头设计为凸型块(即不需要轴压头中通孔部分,使得轴压头与管材无接触)并安装Y型密封圈,将其挤入容腔中,轴压头下行,高压液体通过轴压头中的通液孔进入管材内腔中,管材胀形区因受急剧增大的液压力开始自然胀形。
(2)轴压胀形。将轴压头设计为图1a中所示阶梯轴式,将其挤入容腔中,轴压头受到撞击,高压液体通过轴压头中的通液孔进入管材内腔中,管材在轴压头施加的轴向力和高压液体的液压力共同作用下,进行轴压胀形。
(3)轴向进给量、最大液压力对成形极限的影响规律。调节行程调整螺设置不同轴向进给量,通过设置溢流阀的溢流压力值(即最大液压力),则可研究最大液压力与轴向进给量的协调控制下对管材成形极限的影响规律。
(4)成形异形截面中空件。将成形模腔安装在如图1a所示装置的容腔和定位圈,采用(1)或(2)工作方式即可成形出各种异形截面中空件。
2.试验验证
2.1试验条件
将管材冲击液压成形技术应用于微型管成形中,将会获得更加高效、省时的生产方法[10-11]。本试验管材为304不锈钢毛细管和H65黄铜毛细管,其几何参数如表1所示。取修正系数K1=2,将表1中相应参数代入式(4),得dc>5.57mm。由于所选的Y型密封圈外径为Φ17mm,依据所安装Y型密封圈的槽形圈尺寸标准要求,取dc=16mm,代入式(5),得h'=20mm,结合容腔通孔直径为Φ6mm、Y型密封圈高度为5.8mm,则容腔内液压腔的实际深度为29mm。本试验在TUB-5T微型冲床上进行,其冲头的平均速度为轴压头挤压液体的速度,为20mm•s-1,代入式(8)得d2为2mm(为加工方便,取整数)。垫块高度及溢流阀设置为:(1)垫块高度不变,取溢流压力值为最小值、中间值、最大值,其试验组编号分别为1、2、3;(2)将溢流压力值设置为最大,在前面的试验基础上,根据试验经验添加一块厚度为2mm的垫块,其试验组编号为4。
表1 4管材几何参数

2.2 试验装置
试验装置装配好后的实物图如图1b所示。轴压头上端部设有法兰,与容腔上表面相距12mm,以便有足够的距离使轴压头下降以及安装和卸载。成形模腔外形为T形状,便于其安装及容腔和定位圈的定位,成形模腔接触容腔底面的表面起到支撑容腔和定位O型密封圈的作用,成形模腔开设有喇叭口且不限制管材胀形区的变形(即自由胀形),便于观察管材变形过程,其高度(即管材的胀形区长度)为10mm。压力表和溢流阀组件通过接头与容腔连接,压力表和溢流阀的工作压力范围分别为0~100MPa和60~100MPa。由于受到微型冲床的高速撞击,装置中的液压力会产生波动,若用一般的压力表,则会导致指针不能归零,故为得获得基准的液压力值选用抗震压力表。
2.3 试验过程
试验时,将管材置入由容腔、成形模腔和定位圈所形成的型腔中,向容腔中注满液体,将轴压头置入容腔的环形凹槽中,调定好溢流阀溢流压力值后,将试验系统放置在微型冲床上。启动微型冲床,冲头以25mm•s-1左右的速度撞击轴压头,管材内部的液压力急剧增大,冲头推动轴压头下移所设定的轴向进给量后,轴压胀形结束。卸载装置,取出管材,试验结束。
2. 4试验结果
图2为采用该装置进行相关试验得到的试件实物图。表2、表3分别为4个试验组所获得304不锈钢毛细管和H65黄铜毛细管的试验结果,表2和表3中的“/”表示因屈曲而不可获得最大胀形高度。从图2可知:在同一进给量下,3种不同的溢流压力值中,304不锈钢毛细管的胀形效果不一样,溢流压力值为中间值时效果最好,最小值时并未胀形,最大值时管材破裂; 在溢流压力值设置为最大、垫块高度合适时,试样管材都发生了破裂,而且其胀形轮廓是一条光滑曲线,而垫块高度过高时,试验管材不仅胀破还发生了屈曲,该原因是由于轴向进给量过大,在液压力共同作用下导致试验管材屈曲严重。而对于H65黄铜毛细管,在溢流压力为最小值时,就已破裂,由此可知,H65黄铜毛细管的塑性比304不锈钢毛细管差。
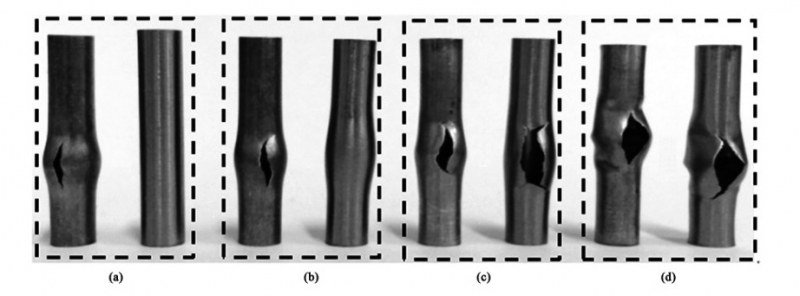
图 2.胀形后相应试验编号所得到的管材实物图
( a) 试验组 1 ( b) 试验组 2 ( c) 试验组 3 ( d)试验组 4
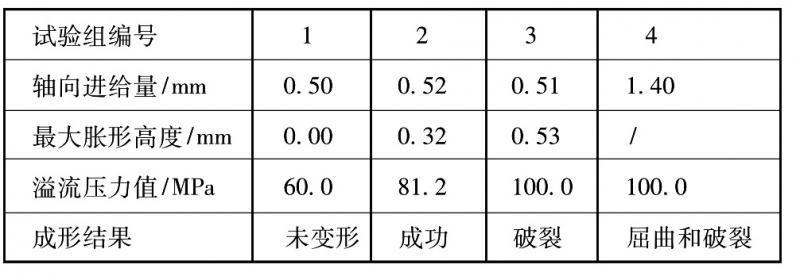
表2 各试验组所得304不锈钢毛细管的试验结果
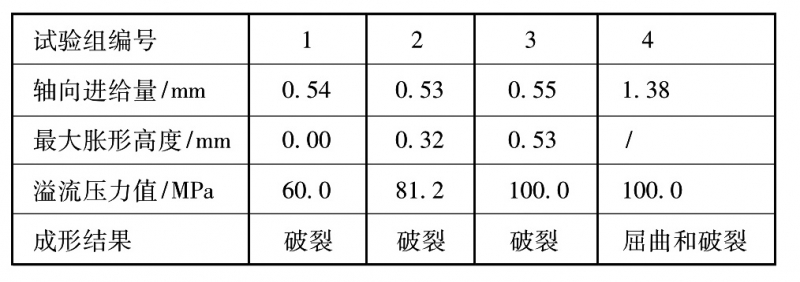
表3 各试验组所得H65黄铜毛细管的试验结果
3.结论
(1)开发了一种新型的管材冲击液压成形装置,在普通的冲床、压力机上即可实现最大液压力与轴向进给量协调控制,并进行管材冲击液压成形试验,获得管材的成形性能参数。
(2)试验结果表明,该装置在微型冲床上进行管材轴压胀形,顺利地完成了高压液体的生成、管端的高压密封、轴向进给量的控制和最大液压力与轴向进给量的协调控制,工作稳定可靠。
(3)试验分析表明,最大液压力和轴向进给量可以有效地提高管材的成形性能,防止管材屈曲、破裂等成形缺陷;在H65黄铜毛细管和304不锈钢毛细管为试验管材时,H65黄铜毛细管破裂时所需的液压力小,使用溢流阀时,易获取胀形成功的304不锈钢毛细管。