技术性热塑性材料具有优异的热稳定性和出色的电绝缘性能,因此被广泛应用于电气行业。但在热塑性材料性能达到应用极限时,热固性材料也可能成为合适的替代品。将热固性材料与热塑性材料巧妙地结合在双组分部件中,还可以避免材料脆性断裂行为的发生。
真实的试验部件为各个系列的实验提供了依据,例如:研究对经过不同表面改性的冲压毛坯进行包覆成型的热固性材料的性能(© Kunststoff-Institut Südwest)
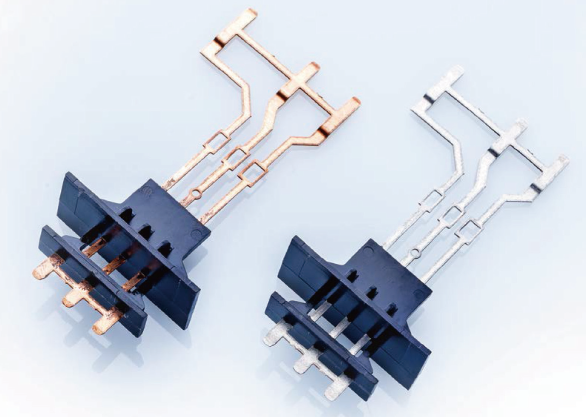
目前,热固性材料逐渐在市场上复兴。因为在各种应用中,尤其是在汽车工业,例如在内燃机小型化及由此带来的耐高温需求增加的进程中,热固性材料作为混合部件的可能组成成份,越来越多地融入到人们的各种讨论中。
利用热塑性材料对嵌件进行包覆成型的技术已很成熟并被广泛应用。但是,该行业仍然面临着各种各样的挑战,例如:不断增加的成本压力和部件小型化趋势。后者经常成为嵌件移位或密封性差等问题的根源。
在电气应用中利用热塑性材料进行包覆成型
当利用热塑性材料对嵌件进行包覆成型时,200-700 bar的型腔压力并不罕见。嵌件的载荷在多数情况下都非常高,因此需要极大的努力才能避免变形。解决这一问题的方法之一是进行多阶段包覆成型:首先,将预成型的嵌件固定在模具中;然后,在后续包覆成型操作中用塑料完全包覆。这种策略通常会造成两种包覆成型材料粘结性不足,原因之一是第一个组件在第二个加热阶段没有充分融化。
如果不想产生额外的财务成本,还可考虑使用含活动型芯的包覆成型模具来固定嵌件。包覆成型工艺的结果在很大程度上取决于型芯的活动和最后产生的部件的密封性,靠近浇口的区域通常比远离浇口的区域更易泄漏。此外,因批次波动或湿气影响等引起的粘度波动也会影响工艺的重现性,并因此影响到生产出包覆成型密封部件的目标。
关于热固性材料应用的新思路
我们应重新认识一下热固性材料。如今该材料已取得了很大的进展,原料制造商已做好应对材料特殊要求的准备。他们根据客户要求提供定制配方的热固性材料,通常这些材料的附加价值是热塑性材料所不具备的。
与热塑性材料加工相比,根据这些要求生产的热固性材料能够轻松地处理低于50 bar的型腔压力——这是热塑性材料加工商所熟知的热熔加工的压力范围。通过这一方式,组装好的电路板可以利用热固性材料进行包覆成型——即使壁厚不同,也不会导致嵌件变形或移位。
热固性材料加工的常见缺点是毛边。塑料加工行业和模具制造商早已习惯了这个问题,它可以通过仿真法、溢流腔、最新的模具技术和全自动的二次加工技术来解决。仿真所需的数据集目前在市场上很少见,但德国的Kunststoff-Institut Lüdenscheid公司已成功生成了该数据集。
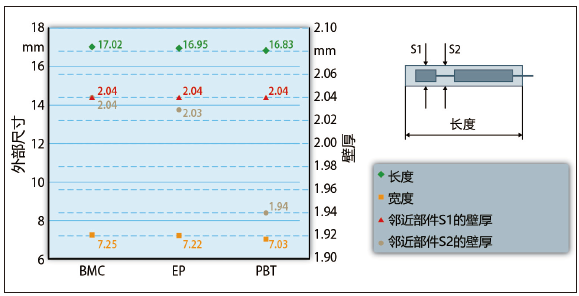
图1 包覆成型传感器的外部尺寸和示意图。BMC、EP和PBT的比较结果显示,热塑性材料的收缩率比热固性材料高,导致嵌件的载荷也更高(© Kunststoff-Institut Lüdenscheid)
基体的这种低粘度(造成分型线毛边的主要原因)可用于完全包覆电子部件、线圈架等。壁厚为零点几至几毫米的部件都能够可靠地填充,因此与热塑性材料相比更具价值。此外,热固性模塑材料的低收缩率(图1)减少了包覆成型后作用于电子部件的内部应力,正如EP和BMC模塑材料与PBT的比较结果所显示的那样。
与电路板封装在外壳中相比,包覆成型工艺更具经济优势。一步式工艺省去了数分钟的封装应用以及固化区域。凭借更简单的工艺技术,相同的密封性或耐环境性要求均能得到满足,因此进一步增强了其经济优势。
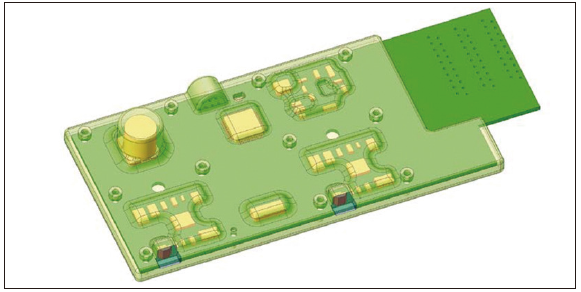
图2 电子模块试验:导体板(深绿色)用塑料(半透明)完全包覆成型,以确保获得可靠的测试结果(© Kunststoff-Institut Lüdenscheid)
为了获得可靠的结果,Kunststoff-Institut正在用试样进行注塑成型试验(图2)。在成型过程中,部件的性能通过在线测量系统(功能测试)记录,并随后进行气候适应性测试。其目的是使试验结果能够用于改进对应的一次注射部件的设计。
含金属和热塑性材料的热固性混合部件
根据材料基体的不同,有些热固性材料能与金属产生化学连接。采用热固性材料对金属嵌件进行包覆成型的另一个优势是在连续使用时具有相同的膨胀系数,这也确保了分界面较低的固有应力可能性和较强的密封性——这一效果使该方法对插头的包覆成型非常有用。对包覆成型插头(标题图)的研究表明,长度4mm和壁厚0.4mm的部件经过包覆成型后可获得能通过氦质谱检漏仪验证的密封性。使用热塑性材料时,若要达到这种密封等级通常需要极大的努力,例如使用助粘剂或高性能热塑性材料。
此外,热固性材料的特点是在连续使用时耐热性至少达到150℃。而在热塑性材料中,可与之相比的仅有改性聚酰胺(PA)、聚苯硫醚(PPS)和聚醚醚酮(PEEK),而这种热固性材料的价格也与改性聚酰胺相近。
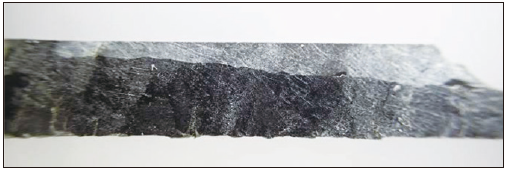
图3 PPS(下)和BMC(上)的分界面显示的轮廓几乎一样,这也反映了粘结部件出色的粘结强度(© Kunstsstoff-Institut Lüdenscheid)
但是,由于热固性材料是一种坚硬且相对不灵活的材料,因此其不能用于弹性功能元件的生产,如弹簧钩。而热固性材料与热塑性材料的组合则是这种应用的适用方案。利用粘结工艺产生的这种组合运用了最先进的技术。不过,Kunststoff-Institut Lüdenscheid公司的研究表明,通过注塑成型也可以进行两种材料的接合(图3和4)。
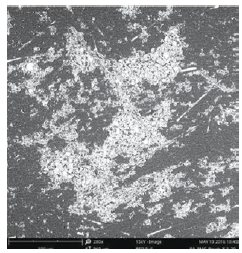
图4 通过转换工艺生产的位于拉伸棒断裂点热塑性聚酰胺(黑色)之上的B M C 热固性材料(块状模塑料,浅色) 的微观图( ©Kunststoff-InstitutLüdenscheid)
热塑性材料和热固性材料的部件组合是塑料行业的一个利基,但目前仍有许多基本问题需要解决。例如,其需要合适的材料组合以及生产顺序:是先加入热固性材料再加入热塑性材料,还是按相反的顺序进行?专为此生产的试样的最初研究(图5)表明,PA66-GF30与自由流动环氧化物包覆成型的组合所获得的粘结强度较低,会导致热固性材料的粘结断裂。
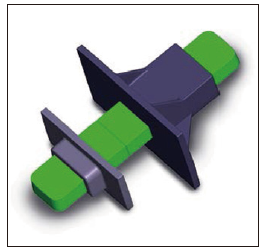
图5 “DuroVerbund II”项目生产的含热塑性嵌件(绿色)和热固性包覆成型(灰色)的双组分混合部件用于对材料粘结强度和密封性进行最终测试(© Kunststoff- Institut Lüdenscheid)
研究结果(图6)表明,这种组合所获得的粘结强度并未通过预处理工艺得到显著改善。最新成型的部件(基于固体棒)的粘结强度降低了10-20%,可能是因为选择的试样形状引发了部件的切口效应,最终导致热固性材料过早断裂。按热塑性预制件和热固性定型件的顺序所获得的结果大有可为,它证明了该材料组合的潜力。但是,当前研究(“DuroVerbund II”项目)的重点在于相反的顺序,因为这对于行业来说更具吸引力。
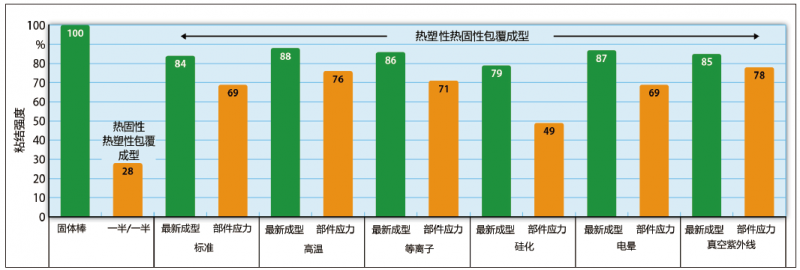
图6 聚酰胺预制件与酚醛树脂包覆成型之间的粘合强度取决于酚醛树脂固体棒的百分比强度(©Kunststoff-Institut Lüdenscheid)
结语
对在高温应力条件下也不会影响自身性能的耐化学性材料的强劲需求,为热固性材料的应用打开了新天地。这种材料适用于低壁厚一次注射敏感部件的包覆成型,因为热塑性材料的高压加工并不总能满足这一要求。将热塑性材料作为包覆成型部件,还可进一步减弱材料的易碎性。
这种潜力已得到了市场的认可,并且第一批部件也已投入批量生产。目前的问题是如何将这种技术传递给更多人。为此,Kunststoff-Institut提出了多个项目,如“DuroVerbund”和“Overmolding Electronics”。(文章来源于网络)