孙 晋,胡 法,胡砚磊,武志军
(中国石油化工股份有限公司北京化工研究院,北京 100013)
摘要:研究了冷却速度、挤出速度和拉伸比等不同挤出工艺对管材物理性能及残余应力的影响,结果表明,随着冷却和挤出速度的增加,PE管材纵向回缩率增大,静液压和SCG破坏时间逐渐降低。通过盲孔应变法研究了不同挤出工艺对管材内外层的释放应变和残余应力分布的影响,研究表明,采用理想化的均匀分布模型不适用于残余应力的定量评价,采用非均匀应力分布模型计算得到的管材外层的残余应力随着冷却和挤出速度的增加而增大,而管材内层的残余应力变化较小,由于管材沿壁厚方向冷却速度的不均匀,内外层残余应力分布存在差异。最终,通过对管材内中外层分别进行拉伸、密度和结晶度等物理性能试验,进一步证明了盲孔法定量评价残余应力的有效性。同时试验发现,当挤出拉伸比太高时,分子链取向严重,管材纵向回缩率增大,静液压和耐SCG性能下降,管材外层残余应力的最大值为14.6MPa,与材料拉伸屈服强度相比,提高了50%。
关键词:挤出工艺;残余应力;盲孔应变法;非均匀应力分布;分层测试
0 引言
近年来,随着聚烯烃材料聚合技术的不断创新和大型生产设备的改进,塑料管道的应用规格越来越大,其应用已经从传统的市政燃气、供水和建筑领域发展到工业领城,例如市政中水输送、废水处理和输送、海水淡化、核工业等。开发高强、轻质、耐磨、耐冲击、耐腐蚀的大口径塑料管道是未来塑料行业的主要发展方向之一[1-3]。但是,由不少实际案例可知,大口径厚壁管材挤出加工产生的残余应力造成管材开裂,使用寿命缩短,给工程带来重大隐患。研究管材残余应力的产生原因,并且从理论上分析、计算残余应力的分布,对于模具设计、工艺优化和提高产品质量均具有重要的意义[4]。
残余应力是衡量产品质量的重要指标之一,对产品的疲劳强度、抗脆断能力、抗应力腐蚀开裂及高温蠕变开裂能力和使用寿命等均具有十分重要的影响。许多结构或零件的损坏并不是由外加载荷引起的,而是由存在不合理的残余应力造成的。残余应力测试方法可分为2类,分别为非破坏性无损伤的物理测量法及具有一定损伤性的机械释放测量法[5-6]。物理测量法对样品表面要求较高,设备较复杂、价格昂贵。目前,盲孔法已成为应用最广泛的机械释放测量法之一,主要用于测量机械零部件和构件制造工艺过程中产生的残余应力[7-10]。残余应力测试方法的研究主要集中在金属材料和少量工程塑料领域,而聚烯烃高分子材料的残余应力测试方法的研究较少。文章通过系统地研究不同挤出工艺对聚乙烯管材物理性能和残余应力的影响,建立一种聚乙烯管材残余应力分布的定性和定量评价方法。
1 实验部分
1.1 主要原料
高密度聚乙烯(HDPE )管材料 :PE100级,黑色,其物理性能如表1所示,市购。
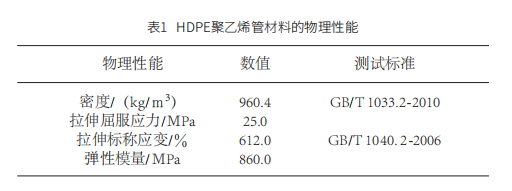
1.2 主要仪器及设备
管材螺杆挤出机:BBC1-90-30,Battenfeld-cincinnati公司;
盲孔法残余应力测试仪:MTS3000,意大利SINT公司;
管材液压试验机:1676,德国IPT公司;
耐慢速裂纹增长制样机:德国IPT公司;
万能材料试验机:Instron4466,美国Instron公司;
高低温试验箱:ZM-10KA,广州爱斯佩克公司;
密度梯度仪:BHM-2,北京化工研究院;
电子天平:AL104,梅特勒;
X射线衍射仪:X'Pert MPD,PHILIPS公司。
1.3 样品的制备
为了得到不同残余应力的管材样品(dn250,SDR11),按照熔体和冷却水的温度差值以及挤出速度,设计了管材在不同冷却和挤出速度下的工艺参数(A~D),如表2所示。其中,与工艺A和B相比,工艺C冷却速度最小,并且挤出速度最慢,工艺条件相对优化。同时工艺A、B、C采用常规的dn250口模和dn250芯模,挤出拉伸比为1.43。工艺D采用特殊的dn250口模和dn200芯模,挤出拉伸比增加至2.23,进一步提高了样品的残余应力水平。
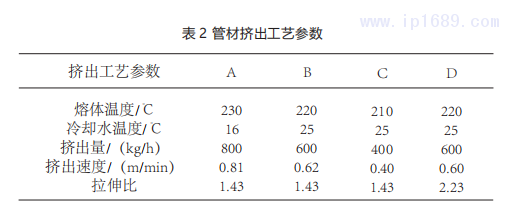
1.4 性能测试与结构表征
纵向回缩率测试:按照GB/T6671—2001进行测试,测试温度为110℃,样品放置4h后冷却至室温,计算3个平行试样的算术平均值。
断裂伸长率测试:管材专用料断裂伸长率按照GB/T1040.2—2006进行测试,样品类型1B;管材样品断裂伸长率按照GB/T8804. 3—2003进行,样品类型I;拉伸速率均为50mm/min,计算5个平行试样的算术平均值。
静液压强度测试:按照 GB/T6111 —2003 进行,采用A型封头,试验温度为20℃,环应力分别为12.4 和13.5MPa,记录管材在恒压下的破坏时间。
SCG性能测试:按照GB/T 18476—2001进行,试验温度80℃ ,试验压力0.92MPa,记录管材在恒压下的破坏时间。
管材分层拉伸测试:为了进一步分析管材沿壁厚方向外、中和内层的性能差异,按照GB/T 8804.3—2003采用机械加工方法沿壁厚方向平均铣削为3层,制取哑铃型试样(类型1)。试验分别测量管材外、中和内层的拉伸性能,拉伸速率为50mm/min。
密度测试:采用密度梯度法,按照 GB/T 1033.2—2010进行试验。
结晶度测试:采用 PHILIPS公司X射线衍射仪进 行结晶度分析。扫描速度为0. 02°/s,扫描范围为15°~30°。采用衍射峰的积分面积来计算试样的结晶度,如式(1) 所示。
结晶度=晶相积分面积/( 晶相积分面积+非晶相积分面积) × 100%
(1)
管材残余应力测试:按照 ASTM E837—2013a 钻孔法分别测量管材内外层沿壁厚方向上的残余应力分布[11]。为了避免钻孔在测量区域产生热量,钻头转速很低(250r/min) ,进给速度很缓慢(0. 2 mm/min) ,最大程度地减少对残余应力的影响。在钻孔过程中,记录得到管材3个方向上的释放应变随着钻孔深度的变化曲线,最终,计算得到管材内外层的Von Mises 等效残余应力σvon 。
2 结果与讨论
2. 1 不同工艺对管材物理性能的影响
不同工艺挤出管材的纵向回缩率、静液压性能和耐慢速裂纹增长SCG等物理性能测试结果如表3所示。由管材纵向回缩率可知,在热历史影响下,管材沿纵向尺寸变化的稳定性侧面反映了管材加工冷却过程产生的残余应力值。由于取向的高分子链占据较大的自由体积,处于较高的能态,仍有向低能态发展的趋势(如松弛、卷曲、缠绕或重结晶等),在二次加热过程中发生尺寸收缩,取向程度降低。因此,可采用纵向尺寸回缩率初步衡量管材残余应力水平,即纵向尺寸回缩率越高,残余应力水平越高。通过比较工艺 A、B和C可知,工艺A的冷却速度和挤出速度最大,纵向尺寸变化率最大(纵向回缩率 1.2%),其残余应力水平最高;而工艺C冷却速度和挤出速度较低,纵向回缩率较低(0.82%),因此,残余应力水平较低。同时,工艺D的纵向回缩率最大,其值为1.6%。这是由于,拉伸比最高,PE分子链取向程度最大,残余应力水平提高。因此,采用纵向回缩率可以初步判断管材残余应力水平,但是,即使是工艺不合理的A和D,其纵向尺寸回缩率仍满足产品标准GB/T13663. 2—2018的要求(≤3%) ,因此,其仅能作为定性的比较方法。
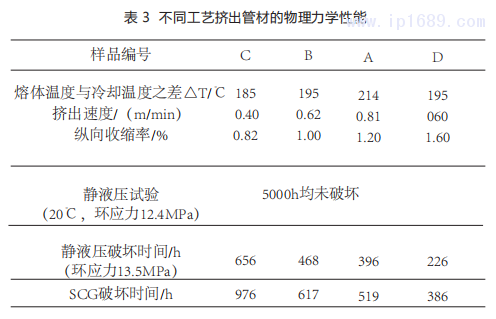
按照 GB/T 13663. 2—2018标准要求(20℃、环应力12. 4MPa) 进行管材静液压试验,不同工艺挤出管材的物理力学性能如表3所示。 由表3可知,4种管材在恒压5000h后均未发生破坏。因此,常规条件的静液压试验难以衡量不同工艺对管材静液压性能的影响。将环应力增加至13.5MPa后,所有管材均在1000h以内发生韧性破坏。因此,随着冷却和挤出速度的增加( C-B-A),PE管材的静液压破坏时间逐渐降低,这表明,挤出冷却过程中产生的残余应力差异对于管材耐静液压性能的影响。而由于工艺D的拉伸比太大,聚乙烯分子链沿管材轴向上取向严重,管材环向承压能力降低,其静液压破坏时间最短。
慢速裂纹增长导致的破坏属于典型的脆性破坏,PE材料在低应力下,晶区间的系带分子链发生解缠结和松弛[12-14]。而系带分子链的解缠速度主要受其缠结密度、分子量及分布和晶体结构等参数的影响。对于同一种管材料而言,不同工艺影响了材料的结晶和取向行为,导致其结晶度降低或结晶不完善,系带分子链缠结密度降低,管材耐SCG性能逐渐下降。由表3 可知,随着冷却和挤出速度的增加(C-B-A),PE管材的SCG破坏时间逐渐缩短。工艺A冷却和挤出速度较快,其结晶较不完善,由此所引起的残余应力也较大,系带分子链的解缠结速度较快,导致工艺A下管材的SCG破坏时间最短。证明了冷却和挤出速度对于管材残余应力的影响。同时由于较大的拉伸比所导致的取向,工艺D管材SCG破坏时间逐渐降低。
2. 2 不同工艺对管材残余应力的影响
文章采用盲孔应变法分别测量不同工艺( A ~ D) 挤出管材内外层沿壁厚方向上的残余应力分布。在钻孔过程中,在钻孔周围的残余应力得到释放,该过程中产生的微应变被粘贴在试样上的应变计记录下来,得到管材3个方向上的释放应变与钻孔深度的关系曲线。应变计粘贴的位置和方向如图1所示。从图 1 中可以看出,第一方向为沿管材挤出的轴向方向,第二方向与管材轴向成45°夹角,第三方向为与管材轴向成90℃夹角的环向方向。最终,计算得到管材内外层的最大主应力σmax、最小主应力σmin、最大主应力角度β和Von Mises 等效残余应力σvon等。最大主应力角度β为最大主应力和应变计第一方向的顺时针夹角。图2~4 为管材内外层在3个方向上的释放应变与钻孔深度的关系。由图2可知,在第一方向(轴向) 上,管材外层的释放应变均随着钻孔深度的增加逐渐变大。
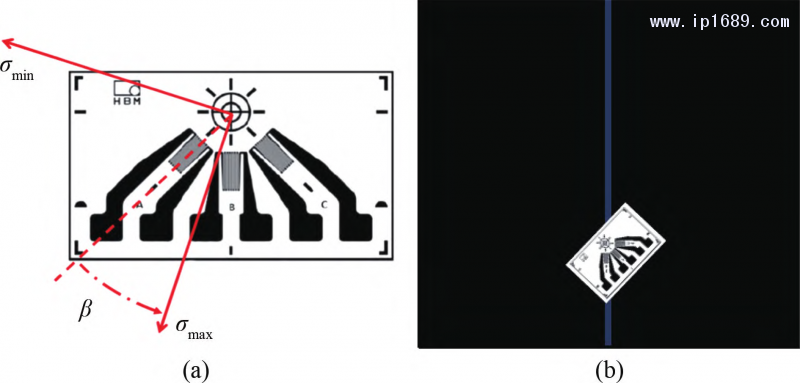
图 1 应变计的类型( a) 和粘贴位置( b )
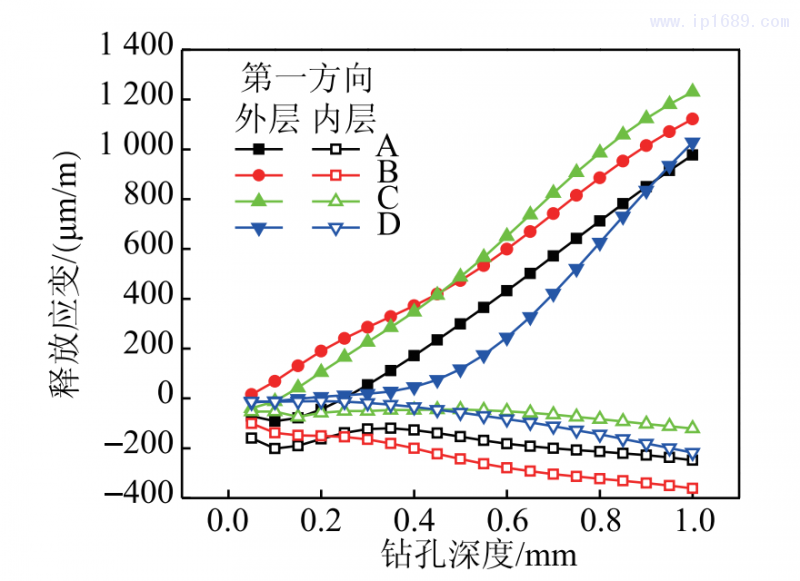
图 2 管材内外层的释放应变与钻孔深度的关系( 第一方向)
而管材内层的释放应变相对较小,并且变化趋势较小。由图3可知,在第二方向(与轴向呈 45°角)上,不同工艺管材内外层的释放应变变化趋势与第一方向类似,管材外层释放应变逐渐增大,但是,管材内层的释放应变相对较小。由图4可知,在第三方向(环向),不同工艺( A、B和C) 管材内外层的释放应变值与第一方向相比均较小,但是,工艺D管材的释放应变随着钻孔深度的变化相对较大。这是由于,挤出拉伸比太大,环向上的残余应力较大。
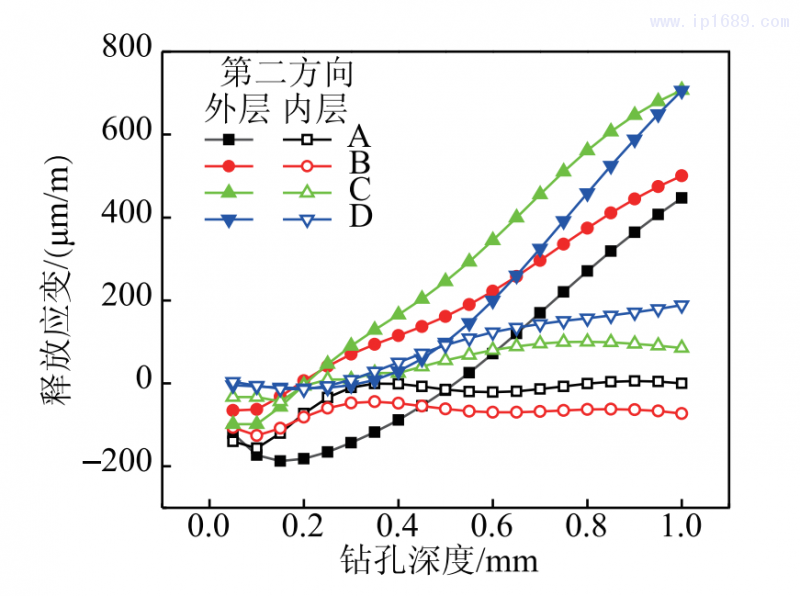
图 3 管材内外层的释放应变与钻孔深度的关系( 第二方向)
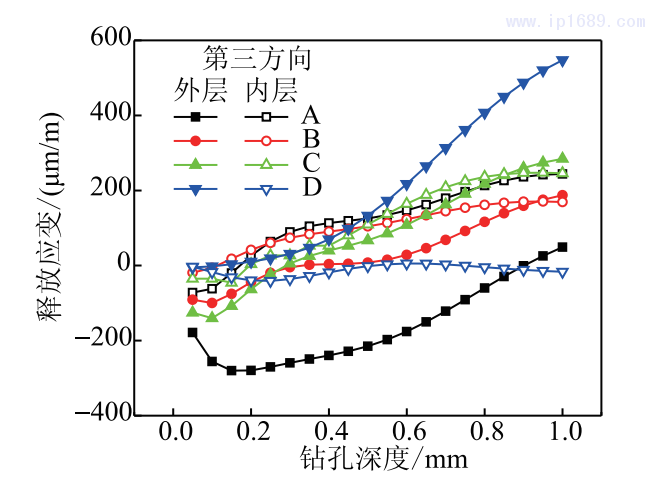
图 4 管材内外层的释放应变与钻孔深度的关系( 第三方向)
按照 ASTM E837 方法和理想化的应力均匀分布模型计算得到管材内外层的最大主应力σmax、最小主应力σmin、最大主应力角度β和Von Mises 等效残余应力σvon,如表4所示。应变计第一方向为沿管材轴向,因此,管材内层最大主应力方向是以轴向为主,这表明,内层残余应力主要是由分子链沿挤出方向取向。而管材外层最大主应力方向是以环向为主,这表明,外层残余应力主要是由冷却不均匀。但是,不同工艺挤出管材内外层残余应力均约为 1~3MPa,并且差异较小,这与实际情况不一致。因此,理想化的均匀分布模型不适用于PE管材残余应力的测量。
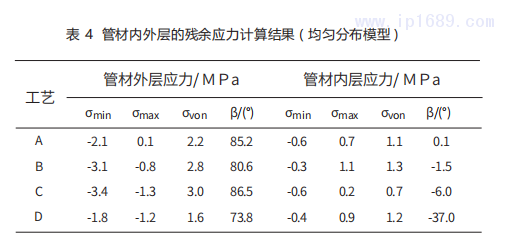
按照 ASTM E837 方法和理想化的应力均匀分布模型计算得到管材内外层的最大主应力σmax、最小主应力σmin、最大主应力角度β和Von Mises 等效残余应力σvon,如表4所示。应变计第一方向为沿管材轴向,因此,管材内层最大主应力方向是以轴向为主,这表明,内层残余应力主要是由分子链沿挤出方向取向。而管材外层最大主应力方向是以环向为主,这表明,外层残余应力主要是由冷却不均匀。但是,不同工艺挤出管材内外层残余应力均约为 1~3MPa,并且差异较小,这与实际情况不一致。因此,理想化的均匀分布模型不适用于PE管材残余应力的测量。
2. 3 管材分层试验验证
将管材样品按照壁厚方向平均铣削为3层,分别进行拉伸、密度和结晶度等试验,其测试结果如表5所示。从表5中可以看出,管材各层(内外中)的断裂伸长率差异较小,但是,中间层的拉伸屈服强度、密度和 结晶度最高,内层其次,外层最低。这是由于,管材外层的冷却速度较快,结晶相对不完善,相应的拉伸屈服强度、结晶度和密度逐渐降低。这与采用盲孔法测量PE管材外层残余应力大于内层残余应力的结果一致,证明了盲孔法定量评价残余应力的有效性。
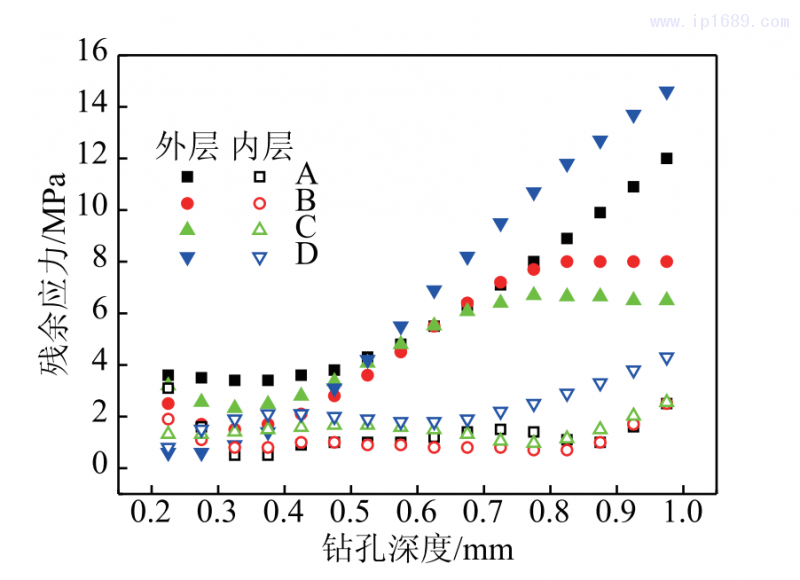
图 5 管材内外层沿钻孔深度方向上的残余应力分布曲线(非均匀分布模型)
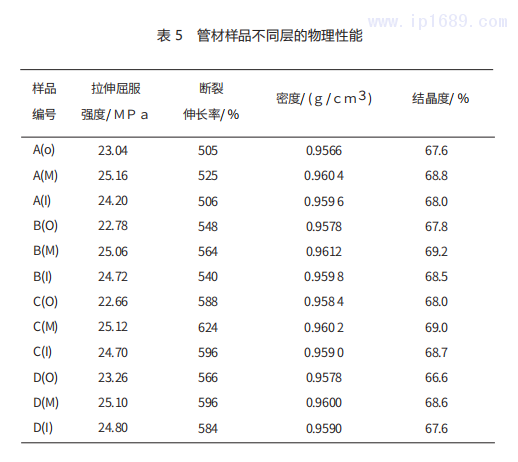
3 结论
(1)通过研究不同挤出工艺对管材物理性能的影响,分析了不同管材残余应力的差异。通过试验发现,随着冷却和挤出速度的增加,管材纵向回缩率逐渐增大,静液压强度和SCG破坏时间逐渐降低。同时随着挤出拉伸比的增大,PE分子链冷却取向程度增大,导致管材的纵向回缩率增加,静液压和耐SCG性能下降。
(2)采用盲孔应变法对不同工艺管材样品内外层进行了残余应力的定量评价,结果表明,采用理想化均匀分布模型计算得到所有样品的残余应力分布差异较小,不适用于PE管材残余应力的定量测试。采用非均匀应力分布模型计算得到管材外层的残余应力随着冷却和挤出速度的增加而增大,而管材内层的残余应 力变化较小(<4MPa)。这是由于,管材内外层冷却速度的不均匀分布残余应力分布产生差异。
(3)采用分层评价法对聚乙烯管材的外层、中间层和内层样品分别进行拉伸、密度和结晶度等试验,结果表明,管材外层的拉伸屈服强度、密度和结晶度最低。这与残余应力的定量评价结果一致,进一步证明了盲孔法定量评价残余应力的有效性。
参考文献:
[1] 王占杰,赵艳,郭晶.中国塑料管道行业“十二·五”期间发展状况及“十三·五”期间发展建议[ J] .中国塑料,2016,30( 5 ):1-7.
[2] 刘斌,崔志杰.大直径塑料管道成型牵引装置开发进展[J] .塑料,2018,47 (3):113-117.
[3] 王登勇,张玉川.大直径塑料压力管发展探析[J] .国外塑料,2011 ,29 (4 ):38-43.
[4] BEECH S H ,BURLEY C ,BUNN H C.Residual stress in large diameter MDPE water pipe [C] .Plastics Pipes VII ,University of Bath PRI London 1988.
[5] HAUK V.Structural and residual stress analysis by nondestructive methods[M] .Amsterdam:Lausanne,New York:Elsevier,1997.
[6] 刘金娜,徐滨士,王海斗,等.材料残余应力测定方法的发展趋势[J] .理化检验( 物理分册) ,2013 ,49 ( 10 ):677-682.
[7] CHOI S,BROUTMAN L J.Residual stresses in plastic pipes and fittings I.methods for experimental analysis[ J ] .Polymer( Korea) , 1997,21 (1):71-82.
[8] BEGHINI M ,BERTINI L.Recent advances in the hole drilling method for residual stress measurement [J] .Journal of Materials Engineering and Performance,1998,7 (2):163-172.
[9] MAXWELL A S,TURNBULL A.Measurement of residual stress in engineering plastics using the hole⁃drilling technique [J] .Polymer Testing,2003 ,22 ( 2 ):231-233.
[10] JANP,JAROSLAV K,PAVEL H,et al.Residual stress distribution in extruded polypropylene pipes [J] .Polymer Testing,2014,40:88-98.
[11] ASTM Committee. Standard test method for determining residual stresses by the hole-drilling strain⁃gage method:ASTM E837-2013a [S] .West Conshohocken:ASTM International,2013.
[12] NIE M,WANG Q,BAI S B.The effect of cooling mode on slow crack growth resistance of polyethylene pipe [J] .Journal of Macromolecular Science,Part B:Physics,2010,49:640 -651.
[13] BROWN N.Intrinsic lifetime of polyethylene pipelines[ J] .Polymer Engineering & Science,2007,47(4):477-480.
[14] HAMOUDA H B H,SIMOES⁃BETBEDER M,GRILLON F,et al.Creep damage mechanisms in polyethylene gas pipes[J] .Polymer, 2001 ,42:5425-5437.
[15] 孙晋,华晔,者东梅.挤出工艺对聚乙烯管材残余应力分布的影响[J] .中国塑料,2019,33 (5):56-60.
[16] JANP ,PAVEL H ,JAROSLAV K ,et al. Residual stress in polyethylene pipes[J].Polymer Testing,2016,54:288-295