赵永刚
(郑州电力职业技术学院,郑州 451450 )
摘要: 目的针对传统建模方法在预测的翘曲变形位置与实际偏差较大的问题,开展基于Moldflow的注塑成型制品翘曲变形优化建模分析研究。方法通过数据模拟分析预处理、浇注体系模型构建、基于Moldflow的注塑成型制品翘曲变形过程模拟等手段,实现对注塑成型制品曲面参数优化。结果通过对比实验证明,新的建模方法与传统建模方法相比预测翘曲变形位置偏差更小,预测结果更准确。结论在实际应用中,该建模方法能够辅助塑件加工厂提升注塑成型制品生产质量。
关键词: Moldflow;注塑;成型;制品;翘曲变形
在计算机辅助工程分析中,最具代表性的软件是Moldflow软件,在对成型模具进行实际加工操作之前,通过利用Moldflow软件对模具的三维模型进行虚拟注塑,以此完成对整个注塑过程的模拟分析,得出在不同情况下制品的材料分布趋势、翘曲变形等条件[1]。利用Moldflow软件进行分析后,能够让设计者在第一时间找出模具及后续制品在制作过程中可能出现的问题,从而及时对模具进行更改。这一过程不仅能够有效提高制品加工和生产的效率,同时也能够有效降低制品加工和生产的成本,减少原材料的损耗[2]。
注塑成型是塑料材料制品成型和加工中一项十分重要的环节,当前除少数几种材料特殊的塑件以外,几乎所有塑件的生产和加工都是通过注塑成型完成。在塑件加工厂中,注塑成型技术的应用能够一次性完成对各类复杂结构、精密尺寸以及带金属嵌件制品的制作,同时其后期还具备修整次数少、成型周期短等优势[3]。在注塑成型过程中,由于不同材料本身具有一定的特殊性,加之复杂的加工条件和工艺流程,材料参数和边界条件的复杂性都使当前注塑成型制品极易出现翘曲变形的问题。
为进一步提高注塑成型制品的加工质量,文中开展基于Moldflow的注塑成型制品翘曲变形优化建模分析。
1 注塑成型制品翘曲变形优化建模
1.1 数据模拟分析与处理
在对数据模拟分析与处理前,首先建立注塑成型制品的三维造型模型。在三维造型软件UG5.0.1环境下,结合注塑成型的特征以及操作要求进行建模。根据不同特征可采用旋转成型或逐层拉伸的造型方法[5],后续在利用Moldflow软件对三维模型进行网格划分的过程中,若模型中存在较小的特征结构,则会出现网格划分异常的现象,严重影响后续优化的效果。因此,在进行对注塑成型制品的三维造型时,为了能够避免这一现象的产生,文中需要对较小的特征结构进行倒圆处理。
以上述模型为基础,针对注塑成型制品的外形特征和结构尺寸进行分析,并完成对所有数据模拟分析的预处理[4]。对三维造型的网格结构进行划分,将通过上述2种造型方式得到的三维模型转换为stl格式文件,并将其导入到Moldflow软件中,完成网格划分。通常情况,网格的大小取值为1.25~1.55mm时,能够得到最优网格匹配率[6]。与此同时根据成型的实际情况,在对网格进行划分时,其目标边长一般为塑件壁厚度的1.5~3倍。为方便论述,文中以壁厚为1mm的塑件为例,在对该塑件进行网格划分时,可将网格目标边长设定为2.5mm。在完成划分后,还需要对水平方向和垂直方向比例较大的网格进行修订。根据上述论述,得出的网格结构对应参数如表1所示。
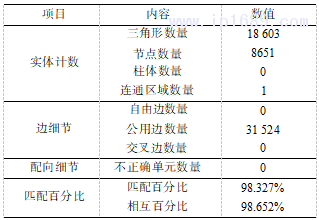
表 1 网格结构对应参数
一般情况下,需要在完成划分的网格匹配率达到85%及以上时,Moldflow软件才能够得到更加可信的分析结果。
1.2 构建浇注体系模型
构建的浇注体系是否合理关系到最终注塑成型制品的性能、尺寸、外观等因素[7]。同时建筑体系模型构建的合理性,关系到Moldflow软件最终得出的分析结果。
图1a和1b分别为初始阶段和经过细化处理后的三维网格模拟浇注体系浇口,可知,三维流动模拟的过程中,在网格结构模型中选择注塑成型其中一个浇口时,在翘曲变形分析过程中,初始阶段给出的默认浇口大小包含在其各个点周围,并且涵盖了所有邻近的网格区域[8]。
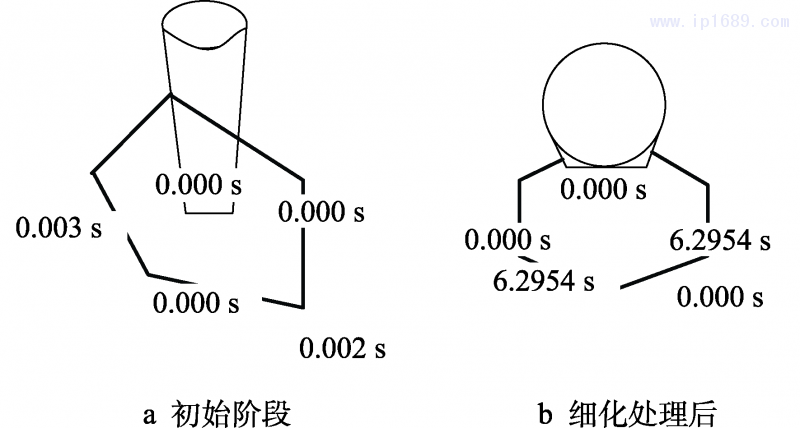
图 1 三维网格模拟浇注体系浇口位置时间信息
考虑到初始阶段得出的结果与实际模具设计阶段的浇口大小不符,因此,需要对初始阶段浇口模型及相应的网格结构进行细化处理。利用Moldflow软件提供的局部细化功能,将浇口网格结构中最大对角长度控制在1.5mm左右,以此构建新的浇注体系,从而得到更加准确的模拟结果[9-10]。由于模具中各个塑件的型腔均相同,因此在Moldflow软件模拟分析过程中,需要尽可能地减少网格计算量,并去除对称型腔,仅将其中一个型腔作为Moldflow软件模拟分析的依据。
1.3 基于Moldflow的注塑成型制品翘曲变形过程模拟
注塑成型制品出现翘曲变形的主要原因是塑件的几何形状与注塑成型模具的设计存在不合理或工艺参数设置有误等问题[11]。因此,文中结合Moldflow软件在对注塑成型制品翘曲变形过程模拟时,首先明确制品出现翘曲变形与塑件本身收缩不均匀有着密切的联系[12]。原材料在流动方向的收缩率与垂直方向上的收缩率相差较大,是导致注塑成型制品出现翘曲变形的主要原因[13]。除此之外,影响注塑成型制品翘曲变形还包括浇注位置不当、冷却系统设计不合理、注塑保压参数错误、浇注流速等原因。
根据上述分析,得出制品在发生翘曲变形过程中应力和应变的关系如式(1)所示:
{σ} = [D](ε - a)∇T - {σi } (1)
式中:{σ}为注塑成型制品翘曲变形应力大小( MPa );[D]为翘曲变形过程中的弹性模量(MPa ); ε为弹性应力大小(MPa );a为注塑成型制品材料热传导系数(W/(m2·℃));∇T为温度差值(℃);{σi} 为由剪切流动引起的初始应力大小(MPa )。根据式(1),结合节点自由度的有限元分析方法,对已知注塑成型制品的上表面和下表面的温度以及加工过程中周围环境等参数的变化情况进行分析[14]。
1.4 注塑成型制品曲面参数优化
根据上述论述内容,完成对注塑成型制品翘曲变形的模拟,文中针对影响注塑成型制品翘曲变形的模具浇口、冷却系统进行调整,实现对其参数的优化。
首先,针对模具浇口参数进行调整。当熔体从主流道进入,并经过分流道进入到浇口时,其浇口的截面面积会突然缩小,为了防止在这一过程中出现翘曲变形的问题,需要通过提升剪切速度、降低粘度的方式,确保熔体在浇口位置上能够得到最理想的状态[15]。浇口的宽度尺寸计算公式如式(2)所示:
b = (2)
式中:b为浇口宽度尺寸;A 为注塑成型制品外侧表面积。
h = 0.3δ (3)
式中:h为浇口厚度大小;δ为浇口位置上注塑成型制品壁厚度。
d = 0.06 (4)
式中:d为浇口位置横截面直径。根据上述公式设定浇口参数,以此确保注塑成型制品在不出现翘曲变形的基础上完成浇注。
浇注完成后基于Moldflow的注塑成型制品翘曲变形过程模拟结果,对冷却系统进行优化。对于粘度低、流动性良好的塑料品种而言,其注塑成型工艺的模具温度要求相对较低,可通过温水或冷水的方式对模具进行冷却。但针对粘度高、流动性较差的塑料品种,若仍然采用上述冷却系统,则会造成制品翘曲变形问题。因此,针对这一类型塑料品种,其温度需要控制在155~200℃,以达到模具的加热条件。在冷却时,采用ABS作为辅助材料,对其进行25℃水冷却处理,以此确保在冷却阶段注塑成型制品不会出现翘曲变形现象。
2 实验论证分析
2.1 实验准备
以塑件加工厂中尺寸为55mm×45mm×15mm的塑件制品为例,针对上述通过理论论述的方法设计出的基于Moldflow的注塑成型制品翘曲变形优化建模,对其在实际应用中的性能进行研究。为确保实验具有可对比性,文中选择将文献[4]基于CAE与正交实验的建模方法作为实验对照组,将文中建模方法作为实验组,开展如下对比实验。
2.2 制作塑件制品
实验中塑件制品的制作要求包括:表面平滑、不允许出现明显擦伤、缺口等外部缺陷,不允许出现严重的翘曲变形现象。该塑件制品的最小厚度为1.2mm,最大厚度为2.8mm。为保证最终得出的实验结果具有客观性,在使用2种建模方法时,其注塑成型工艺的参数均设置为默认值,塑件制品注塑成型工艺参数如下:①模具表面温度变化范围为55~75℃;②溶体温度范围为120~220℃;③顶出时温度为90℃;④最大剪切应力为0.45MPa;⑤最大剪切速率为45000s−1;⑥最大注射压力为155MPa;⑦最大锁模力为5710.26N。
2.3 实验数据采集
根据上述塑件制品注塑成型工艺参数设定,将其分别引入到2种建模方法中,对变形参数每隔10min采样1次,注塑成型制品翘曲变形参数分布如下。
注塑成型制品测点区:0→0.45σcon(初应力变形荷载)→σcon应变荷12min→优化。注塑成型制品的受拉区:0→0.34σcon (载荷力)→1.34σcon(结构损伤)→持续载荷30min→σcon优化,其中σcon表示注塑成品应力。根据上述过程,完成对5个该塑件制品的注塑成型模拟,得到2组不同的建模结果。文中将2种建模方法得出的预测注塑成型制品翘曲变形位置的精准度作为实验评价指标,为方便验证,文中将实验组和对照组2种建模方法下预测得出的具体翘曲变形位置进行记录,并将其与完成注塑成型后制品的实际翘曲变形位置进行对比。
2.4 结果与分析
根据上述实验完成对比实验,将得出的实验结果记录如表2所示。
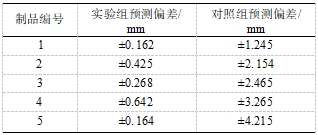
表 2 实验组与对照组实验结果对比表
从表2中2组建模方法的实验结果可知,实验组建模后预测出的翘曲变形位置与实际位置之间偏差均低于±0.642mm,而对照组建模后预测出的翘曲变形位置与实际位置之间偏差均高于1.245mm,由此可知文中方法的翘曲变形偏差较小,能够更加准确地预测出在后续注塑成型阶段,制品存在的翘曲变形位置。同时,通过文中建模方法能够对具体影响该位置出现翘曲变形的原因给出明确的结果,通过对影响其发生翘曲变形的参数进行优化,能够使最终加工生产得到的塑件制品质量达到标准规定要求,提高塑件加工厂的生产效率。
3 结语
在注塑成型制品中,是否出现翘曲变形现象是判断产品质量的重要指标,当前塑料制品的精细化和功能化程度不断提升,加之部分零件变形能力低等因素的影响,使当前注塑成型制品的生产质量受到严重影响。针对这一问题,提出了一种对注塑成型制品翘曲变形的建模方法,并结合Moldflow软件实现变形预测。在后续研究中,还将针对这一方法在实际应用中的广泛性进行优化,从而使文中方法能够应用于对更多不同材质产品的变形预测中。
参考文献:
[1] 谭安平, 刘克威. 基于Moldflow的PC/ABS汽车后视镜翘曲变形优化分析[J]. 合成树脂及塑料, 2020, 37(1): 67-72.
[2] 王尚英, 秦宇志, 周川. 基于MoldFlow的汽车导风板注射模优化设计[J]. 模具制造 , 2021, 21(1): 50-54.
[3] 阮婷, 汪伟东. Moldflow在汽车挡风网基座注塑成型过程中的应用[J]. 内燃机与配件 , 2021(1): 85-86.
[4] 陈艳艳, 刘兵. 基于CAE与正交实验的汽车玻璃升降器钢丝绳支架注塑工艺参数优化 [J]. 机械工程师 , 2021(2): 131- 133.
[5] 刘锋 , 孟海涛, 庞建军, 等. 基于RE-RP/Moldflow/UGNX技术的注塑模具快速设计[J]. 塑料工业 , 2020(12): 105- 109.
[6] 黄小娣. 基于Moldflow的数控机床接触式滚轮传感器的注塑模具设计与优化分析[J]. 塑料科技, 2021, 49(2): 74-77.
[7] 陈显冰, 黄震东. 基于Moldflow技术的监控器底座注塑模具设计[J]. 工程塑料应用, 2019, 47(11): 94-98.
[8] 王金荣, 王权, 赵笑梅. 基于Moldflow的洗衣机波轮盖翘曲分析与优化[J]. 塑料工业 , 2020, 48(5): 72-75.
[9] 张栩梓, 康顺成. 基于Moldflow的商用车高架箱上本体浇口位置优化设计[J]. 装备制造技术, 2020(5): 106- 110.
[10] 赵战锋. 基于Moldflow的新能源汽车手柄气辅成型工艺优化[J]. 塑料, 2020, 49(4): 73-77.
[11] 谭安平, 尹小燕, 刘克威. 基于Moldflow的双色成型数值分析及正交法优化 [J]. 合成树脂及塑料, 2020, 37(4): 38-42.
[12] 鄢天灿, 梅益, 罗宁康, 等. 基于Moldflow和BP神经网络的MP3088连接器壳体注塑工艺优化[J]. 塑料工业 , 2020, 48(9): 56-60.
[13] 朱俊杰, 陆展科, 张鑫程. 基于Moldflow的LED平板灯后壳成型分析及应用[J]. 日用电器, 2020(4): 64-70.
[14] SPOERK M, SAVANDAIAH C, ARBEITER F, et al. Optimization of Mechanical Properties of Glass- Spheres-Filled Polypropylene Composites for Extru- sion-based Additive Manufacturing[J]. Polymer Com- posites, 2019, 40(2): 638-651.
[15] LUGHOFER E, ZAVOIANU A C, POLLAK R, et al. Autonomous Supervision and Optimization of Product Quality in a Multi-Stage Manufacturing Process based on Self-Adaptive Prediction Models[J]. Journal of Process Control, 2019, 76: 27-45.