李欢1,樊华2
(1.陕西华臻车辆部件有限公司,陕西 西安 710200;2.陕汽集团商用车有限公司,陕西 宝鸡 722400)
摘要:文章从吸塑发泡地板垫的结构要求、成型工艺、模具结构进行分析,并采用三维软件 Catia设计一款重卡PVC吸塑发泡地板垫,通过样件制作、装车验证其设计的合理性及批量生产要求。
关键词:吸塑成型;PVC皮革;地板垫;结构设计
1 引言
未来汽车内饰发展的主要趋势为安全、环保及轻量化,目前汽车内饰的轻量化实现途径集中在设计和材料方面[1]。地板垫作为汽车内饰的主要零部件,其目的是提升驾驶室舒适度和安全性,同时满足环保、防滑、阻燃、耐脏等要求。
为提升驾驶舒适度,重卡的地板垫产品现已普遍采用背部发泡的多层材料压制而成,以提升触感。做好地板垫结构设计是实现内饰产品高品质发展的前提,也是成型工艺高效作业的保障。
文中借助Catia三维软件完成一款重卡地板垫的设计, 从产品结构、成型工艺、模具制造等多方面分析,指导地板垫吸塑模具开发,缩短开发周期。
2 重卡地板垫的结构设计
该地板垫成型工艺定义为吸塑发泡成型,其材料为:表皮PVC发泡革+PU软发泡+PVC黑膜,所用PV表皮厚度为2.5±0.2mm。
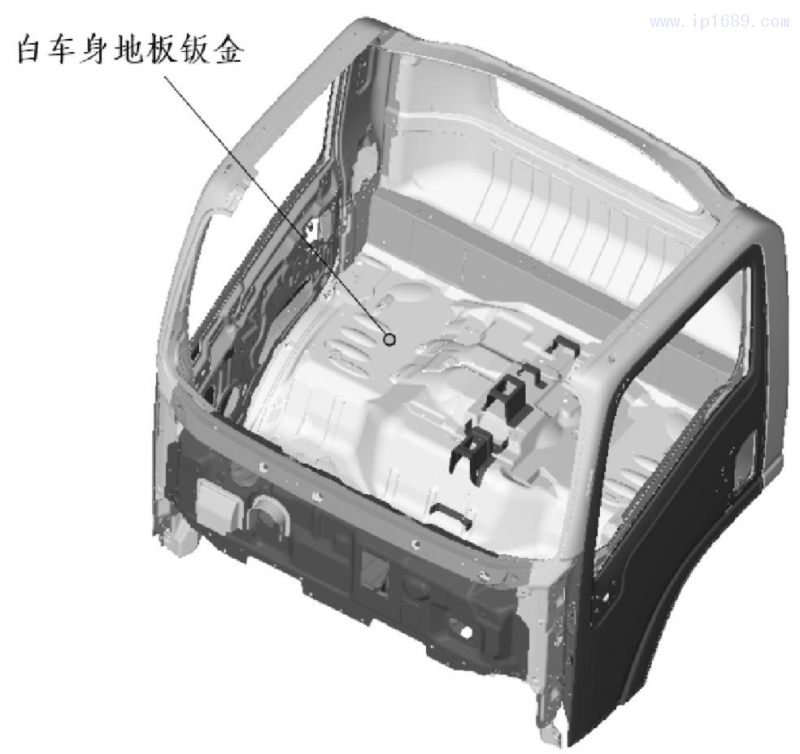
整体布局:地板垫位于白车身地板钣金上。根据常规配置,在地板垫两侧会安装左/右门槛压条,中间有手控阀护罩、操纵装置等,中间偏后位置布置有座椅及副座椅,前部则安装有环绕式仪表台。
因此,设计地板垫结构时,为保证舒适性,可将脚踏区域的地板垫厚度保证在20-22mm左右;门槛压条安装位置处,在保证门槛压条与地板垫装配无间隙情况下将发泡逐渐减薄,见图2;座椅安装位置处可将背部发泡厚度较薄,方便座椅安装,保证表面皮革无拉裂现象;所有开口位置为防止露白,设计发泡层开口处较皮革层周圈缩进3-5mm左右。
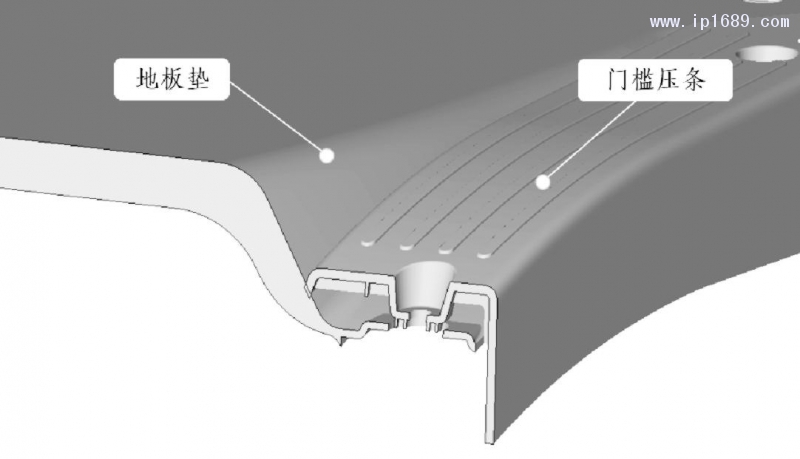
根据以上设计注意事项,最终完成的地板垫设计数模见图3。
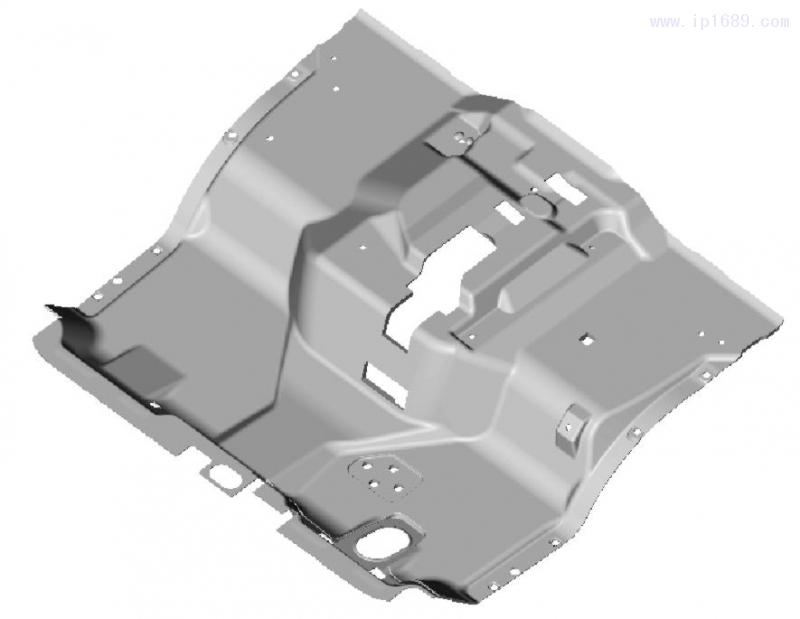
3 吸塑发泡成型工艺
吸塑发泡成型工艺步骤包括PVC皮革加热、黑膜夹持、真空吸附、浇注发泡料、闭模成型、冷却冲孔等主要工序,其工艺流程见下图4。
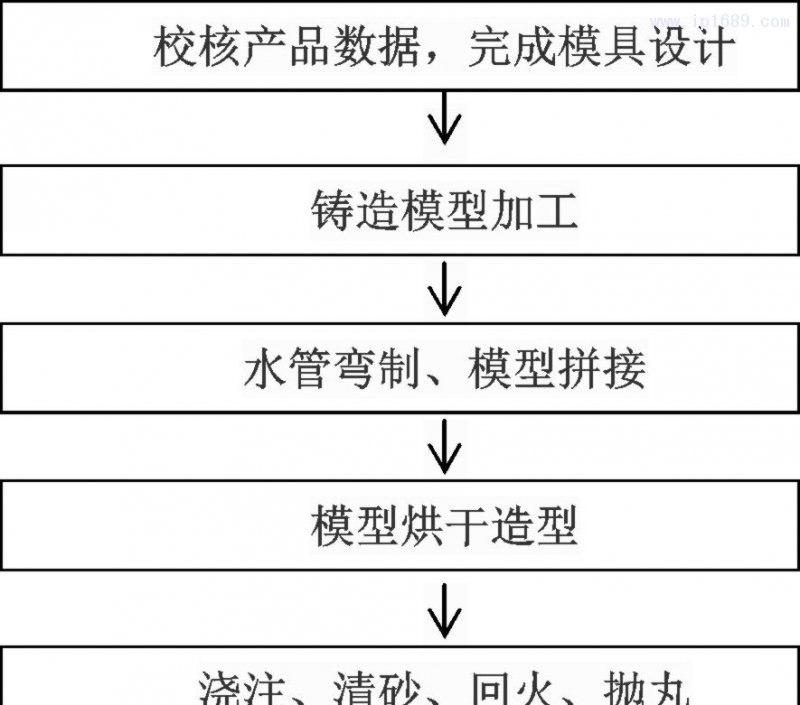
通常生产的地板垫随放置时间长会出现收缩现象,其影响因素主要有地板垫表面的PVC皮革材料、成型工艺、模具等方面[2]。PVC皮革材料的配方不同,会导致材料具有高压缩形变量;成型因素如加热温度及时长、冷却时长会导致“表-芯”出现温度差而产生收缩;模具在 X、Y、Z 方向的缩放比及吸附孔的数量、分布等因素也会影响地板垫与白车身地板钣金的服帖程度。
因此地板垫收缩现象是多方面因素导致的结果,车间在生产时需采取适当放大地板垫皮革的下料尺寸、合理控制成型温度及加长时长、制作定型工装等措施保证地板垫产品质量。
4 吸塑成型模具
4.1 吸塑模具分类
吸塑成型模具分为金属材质模具、玻璃钢模具、木模三种[4]。目前市场上常用的发泡地板垫金属模有钢模和铝合金模具两种,钢模成型效果佳、寿命长,可将吸塑及冲切工艺一体化,效率高,但其制造成本较高,约为铝合金模具成本的二倍。铝合金模具因其良好的导热和散热快性能也被市场广泛使用,其制造成本比钢模低,不足之处是材质本身较软,需依次经历“吸塑成型→产品冷却→手工冲切孔”工序。
一般在大规模工业化生产中,以金属模具为主,而在小批量生产中以玻璃钢模具为主[3]。玻璃钢模具寿命短,受热容易变形[4]。
木模主要用于产品试制阶段,一般用于主机厂短时间内验证产品T0阶段的装车效果。模具精度差且寿命最短,但开模周期短,约一周左右即可完成,成本低,满足主机厂时间节点。
4.2 铝模的制作步骤
综合考虑产品结构、市场销量等,本文定义正式模具开发为铝膜,材质为ZL104。其模具制作的主要步骤如图5所示。
4.3 铝模的制造要求
(1)要求模具型腔表面及分型面光滑,无毛边,沙眼,气孔,缩凹,裂纹,加工痕等缺陷。
(2)因下模为吸塑模,故要求型面壁厚最小厚度不得小于25mm,其内设冷却系统,采用循环水冷却,需预埋不锈钢管。
(3)产品开孔需手工冲裁,故其切割边界及孔位应在模具上加工压痕,模具所有孔位做成可拆卸式,方便调整位置。
(4)吸塑孔可采用标准气塞,合理布置吸塑孔的位置以及数量,气塞,需大小统一,分布均匀。
(5)模具导向装置要求使用“导柱+导套”的导向方式,且满足自润滑。
(6)模具上下模合模后密封性良好,无溢料,产品边缘和冲孔处不能露白。
(7)模具外表面防锈处理,模具须有起吊装置和锁模装置,方便模具的吊运。
5 制造的吸塑模具及产品实物
结合产品设计数据,制作成型模具并生产输出产品样件,吸塑模具实物见图6,地板垫产品实物见图7。
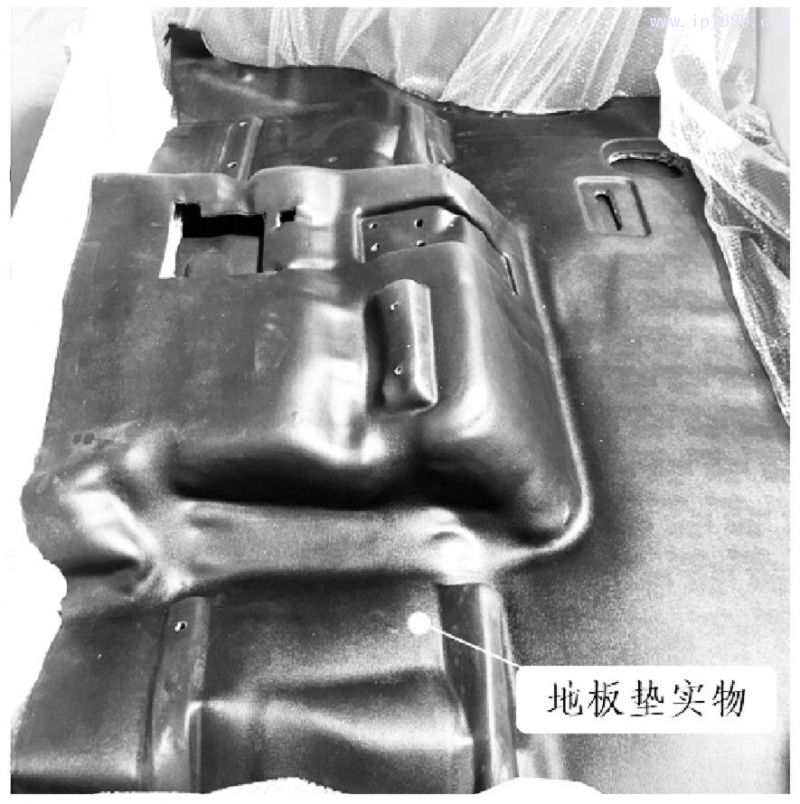
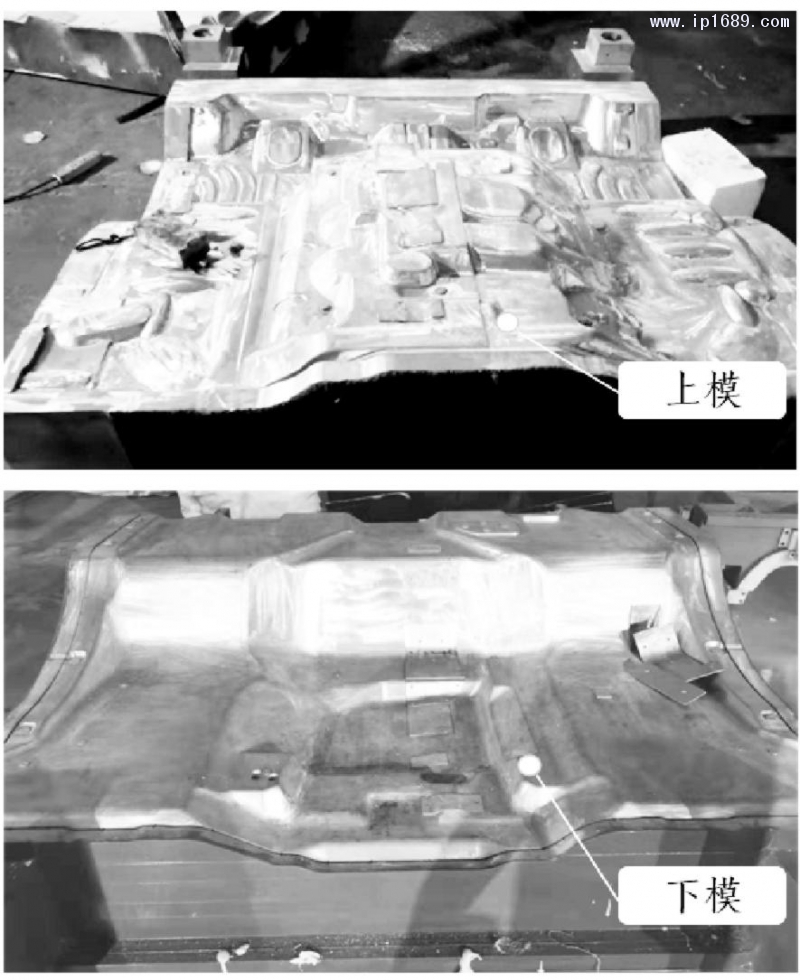
通过样件装车验证,地板垫实物外观平整、无褶皱,装车效果好,与白车身钣金服帖,满足批量生产要求。
6 结语
地板垫为汽车内饰产品的重要组成部分。本文借助Catia三维软件从专业角度分析产品结构,设计完成一款重卡发泡地板垫,简要说明吸塑成型工艺的注意事项及模具制造的细节要求,并通过模具制造、样件试制、装车验证等环节,验证产品设计的合理性,满足批产要求。
参考文献
[1] 杨冰冰,焦小甫,翁明胜.浅谈汽车内外饰结构设计及成型工艺[A]. 第十二届河南省汽车工程科技学术研讨会,277.
[2] 杨诗润,程涛.汽车PVC发泡地垫革高温收缩问题的分析及解决[J].汽车工艺与材料,2015(8):47-50.
[3] 曾毅,汪祥.吸塑成型工艺在军车内饰开发中的应用[J].汽车工艺与材料,2018(5):29-32.
[4] 欧永杰.吸塑成型在客车上的应用[J].商用汽车杂志,2006(1):104-105.