任重1,2,黄兴元3,柳和生4
1 江西科技师范大学光电子与通信重点实验室,南昌 330038 2 江西科技师范大学光电检测与信息处理重点实验室,南昌 330038
3 南昌大学机电工程学院,南昌 330031
4 东华理工大学化学生物与材料科学学院,南昌 330013
为了解决传统塑料微管挤出产生的挤出胀大、熔体破裂和挤出变形等问题,本工作采用内外双层气体辅助技术开展了塑料微管气辅挤出实验,并将其与传统挤出实验结果进行了对比。为了进一步揭示气辅技术可以消除传统挤出产生上述问题的机理,利用有限元方法对塑料微管气辅挤出和传统挤出进行了数值模拟和对比分析。实验结果表明,气辅技术不仅很好地克服了挤出胀大和挤出变形,而且使得挤出的塑料微管表面平整度、光泽度和透明度均有很大提高。数值结果表明,气辅技术较好地减小了熔体在口模流道内尤其是口模出口处的压力、剪切和法向应力差分布,使得塑料微管熔体在口模内的流动从黏着无滑移剪切流动转变为完全滑移无黏着流动,并且在口模出口处流速分布均匀且无突变和径向流速,从而较好地克服了塑料微管传统挤出方式产生的问题。
关键词 塑料微管 挤出成型 气辅技术 有限元分析
0引言
塑料微管在医学、光纤通信和汽车油路等领域中的应用越来越广泛,尤其是在医学领域,如冠状动脉导管、造影导管和心胸、泌尿等外科手术中的各种微管等。据报道,近年来我国每年消费的各类微管费用达数亿美元,具有巨大的经济市场[1-2]。但是,在传统塑料微管挤出过程中,由于高分子塑料熔体本身固有的高黏弹特性,加上在高速螺杆旋转推动下,熔体在口模流道内与口模壁面相互作用,使得熔体分子链产生了取向并存储了较大的弹性能。当熔体被挤出口模时,由于弹性储能恢复、应力突变和流速不均等因素,使得被挤出口模的熔体产生明显的挤出胀大、熔体破裂和挤出变形等问题[3-7],严重影响了塑料微管产品的品质,造成巨大的人力、财力和物力浪费。
为了解决上述问题,本工作提出将气辅技术[8-9]应用于塑料微管挤出,并将一定压力的气体导入到塑料微管挤出口模的环形熔体与口模内壁面和芯棒外壁面之间[10],形成内外双层的稳定气辅层,使得塑料微管熔体以完全柱塞状的方式挤出[11-13],最终消除塑料微管挤出产生的上述三个问题[14-15]。为了实现上述目标,首先本工作搭建了一套塑料微管气辅挤出实验装置,对塑料微管气辅挤出和传统挤出进行了实验研究和对比分析。然后,利用有限元方法对塑料微管传统和气辅挤出进行了数值模拟,并且对气辅技术可以消除传统塑料微管挤出产生的挤出胀大、熔体破裂和扭曲变形进行了机理分析。
1实验
1.1设备和材料
为了实现塑料微管气辅挤出,构建了一套塑料微管气辅挤出实验装置,如图1所示。该装置主要包括:塑料微管挤出子系统、塑料微管气辅挤出口模和气体辅助子系统。
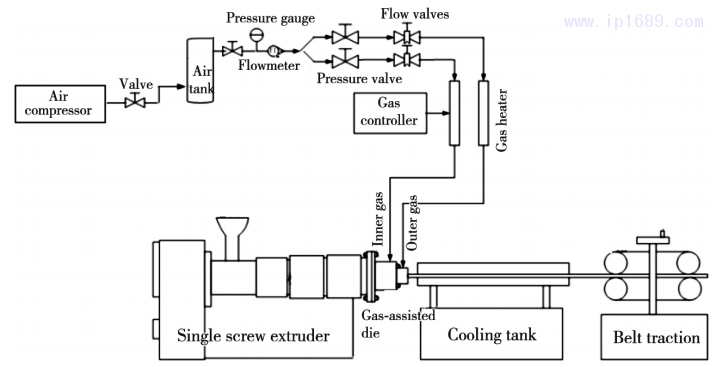
该装置中,塑料微管挤出子系统由小型单螺杆挤出机、冷却定径水槽和皮带牵引机(GRQ-25PVC,科劳斯)构成。其中,挤出机螺杆直径为25mm,长径比为25:1,螺杆转速可调范围为0~100r/min。冷却定径水槽长2m,为不锈钢材质。皮带牵引机为变频电机驱动的皮带牵引装置,牵引速度范围为0~30m/min。
同时,本研究还设计了一款塑料微管气辅挤出口模,如图2所示。该气辅口模主要由口模连接法兰、多孔板、机头体、分流锥、内气辅芯棒、外气辅口模、外气辅圆筒和压圈等构成。
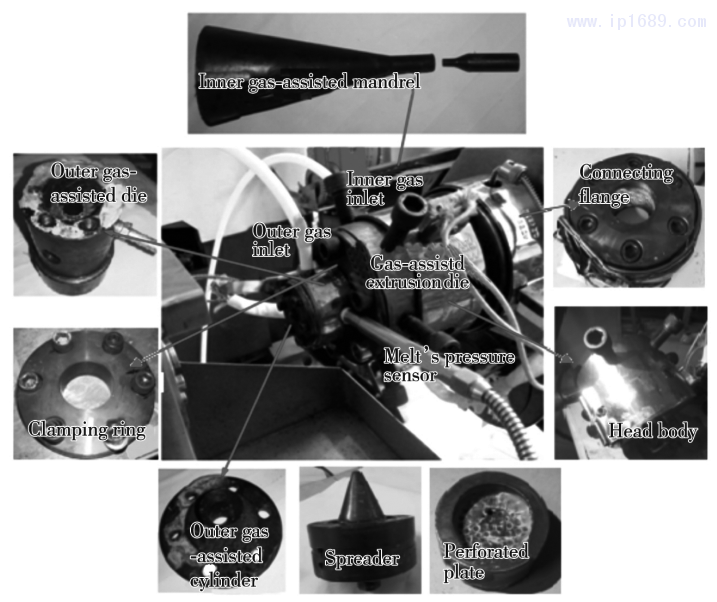
体辅助子系统由空压机(飓霸LD-800×3-80L,台州)、阀门、储气罐(型号:1V-3/8,0.4m3)、减压阀(AFC2000,中国台湾)、流量计、三通阀、精密调压阀(IR1000-01BG,武汉百灵)、流量调节阀(ASC-06,昆山凯意隆气动有限公司)、气体加热器(1000W,上海涞恒电热电器有限公司)、温度控制器、输气管和接口等组成。其中,储气罐最大压力值为0.8MPa,其作用是存储高压压缩气体,并减小塑料微管气辅挤出过程中气体的压力波动。
1.2实验步骤
(1)开启挤出机电源开关,将熔体温度加热到230℃。为了使塑料原料能快速熔融又不至于在机筒进料段产生过热降解,可以将挤出机的三段区域和挤出口模的两段区域按照表2逐级递增的方式进行温度设置,挤出机和口模开始加热,预计加热时间为30~40min。(2)在挤出机和口模加热期间,打开气辅子系统中空压机和储气罐之间的阀门,启动空压机将空气压缩并存储于储气罐中直至达到储气罐最大压力(0.7MPa)时,空压机自动停止。(3)待挤出机和口模温度达到设定值后,开启储气罐出口阀门,并通过减压阀将气体压力适当降低至0.3MPa,再经过三通阀将气辅气路分为内气辅气路和外气辅气路,当两路气体分别经过精密调压阀和流量控制阀后,利用气体加热器将两路气体加热至与熔体温度相同。(4)由输气管道将加热后的内外气辅气体通过进气接口流入到塑料微管气辅挤出口模的内外气辅通道中。(5)开启挤出机电机电源开关,将挤出机电机频率设定在一定值后,挤出机螺杆转动对熔融的塑料进行挤出,同时开启冷却定径水槽和皮带牵引机,挤出的塑料微管经过水槽冷却后在皮带牵引机的牵引下开始进行塑料微管气辅挤出实验。(6)通过内外气辅气路中的精密调压阀和流量控制阀来调节内外气辅气体压力或流量,当内外气辅层气体输出稳定以及塑料微管表面质量稳定后,则最终可以实现稳定的塑料微管气辅挤出。

2实验结果
2.1气辅挤出对塑料微管挤出胀大的影响
塑料微管内外壁面均不施加气辅层时,塑料微管的挤出属于传统挤出,挤出得到的塑料微管如图3a所示。而当塑料微管内外壁面均施加气辅层且内外双气辅稳定时,得到的气辅挤出塑料微管如图3b所示。
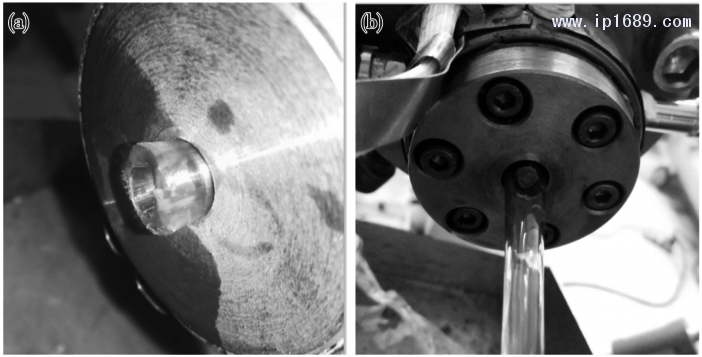
从图3a可知,传统挤出的塑料微管在口模出口处产生了明显的挤出胀大现象,壁厚增厚。而对气辅挤出而言,如图3b所示,可以清楚地看出,塑料微管环形熔体与口模内壁面之间存在明显缝隙,说明气垫膜层已经形成,且气辅挤出的塑料微管尺寸均匀一致,没有产生挤出胀大现象。这表明气辅挤出技术很好地消除了传统塑料微管挤出产生的挤出胀大和挤出变形问题。
2.2气辅挤出对塑料微管熔体破裂的影响
经过冷却和牵引后,得到了传统和气辅条件下挤出得到的塑料微管,分别如图4a、b所示。
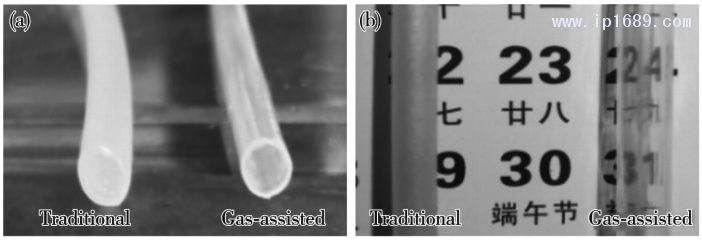
图4a可知,在相同工艺条件下,相比于传统挤出的塑料微管,气辅挤出的塑料微管外径稍小,内径稍大,壁厚更薄。此外,从图4b可以清楚地看出,气辅挤出的塑料微管的表面平整光滑、光泽度和透明度较好,质量优于传统挤出塑料。
利用电子显微镜(XSP-37XB,上海缔伦光学仪器有限公司)分别对传统挤出和气辅挤出得到的塑料微管内外壁面进行微观表征,结果如图5所示。
从图5a、b的微观表征可知,传统挤出的塑料微管内外壁面均出现了粗糙和破裂纹理,其表面平整度和透光性差。而从图5c、d可知,通过气体辅助作用挤出的塑料微管内外壁面没有出现明显的褶皱和破裂纹理,其表面光滑度、平整度和透光性相比于传统挤出塑料有了很大提高。
3数值分析
3.1模型
本工作利用有限元数值方法[10]来揭示气辅技术应用于塑料微管挤出可以克服传统塑料微管挤出产生的挤出胀大、熔体破裂和挤出变形等问题的机理。塑料微管入口横截面形状和尺寸如图6a所示,其外直径为3mm,内直径为2mm。由于塑料微管呈轴对称几何结构,为了提高计算效率,本研究利用1/4部分的塑料微管几何结构来进行数值模拟,其三维几何结构如图6b所示。其中,AA'BB'CC'DD'为口模内区域,其长度为10mm。CC'DD'EE'FF'为口模外熔体自由区域,其长度为10mm。AA'BB'为熔体入口面,CC'DD'为口模出口面,EE'FF'为熔体末端面,ABCDEF面为塑料微管外壁面,A'B'C'D'E'F'为塑料微管内壁面,AA'CC'EE'和BB'DD'FF'为塑料微管熔体对称面。
3.2控制方程
连续方程和动量方程见式(1)、式(2):

于聚合物熔体为黏弹流体,本研究采用能很好反映黏弹流体特性且应用较多的Phan-Thien-Tanner(PTT)微分黏弹本构方程[16-17]来描述聚合物熔体的流动特性。该本构方程为:
式中:ηr=η2/η为黏度比,其中η2为偏应力张量纯黏性部分对应的黏度、η为熔体总黏度,其满足关系式η=η1+η2,η1为熔体的非牛顿黏度;λ为熔体松弛时间;ε为与熔体拉伸特性有关的材料参数;ξ为与熔体剪切黏度有关的材料参数;τ和τ分别为偏应力张量 τ 的上随体导数和下随体导数; D 为熔体形变速率张量。
3.3边界条件
入口面:假设熔体在进入定型段后,其流动基本已经充分发展。故熔体在入口面边界满足如下关系:vx=vy=0,其中vx、vy和vz为塑料微管熔体在口模内沿x、y和z方向上的流速。
壁面:对传统挤出而言,熔体壁面满足无滑移(No-slip)边界条件,即vn=vs=0,其中vn和vs分别表示熔体的法向速度、切向速度。而对气辅挤出而言,采用完全滑移边界条件(Full-slipcondition),即vn=0,fs=0,其中fs为熔体的切向应力。
自由界面:在外界无压力和表面张力附加的情况下,满足的动力学边界条件为fn=0,fs=0和vn=0,其中fn为熔体的法向应力。
对称面:满足的边界条件为fs=0,vn=0。
末端面:塑料微管熔体末端未施加任何牵引力,则满足如下关系,即fn=0和vs=0。
3.4物性参数
采用PTT本构方程来描述塑料微管熔体的属性,其物性参数[18]如表3所示。
4数值结果与分析
4.1挤出胀大
通过上述有限元数值模拟,得到了气辅条件和传统条件下塑料微管的挤出成型效果,如图7a、b所示。同时,为了更加准确地表现出气辅挤出和传统挤出造成的塑料微管挤出胀大现象,模拟了传统和气辅时塑料微管的入口和末端截面形状,如图7c、d所示。
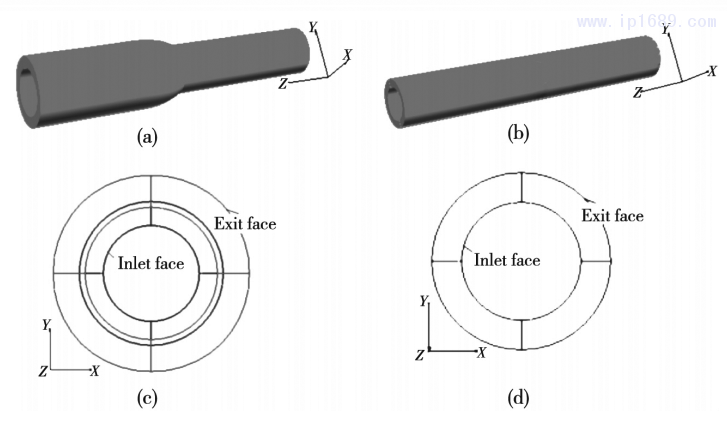
从图7a、c可知,传统塑料微管出现明显的挤出胀大现象。按照式(6)—式(8)可以分别计算得到塑料微管的内径、外径和壁厚的挤出胀大率(wi、wo和wt),即:
wi=(ri'-ri)/ri×100% (6)
wo=(ro'-ro)/ro×100% (7)
wt=(rt'-rt)/rt×100% (8)
式中:wi、wo和wt为塑料微管入口截面的内半径、外半径和壁厚;wi'、wo'和wt'为塑料微管挤出口模后末端截面的内半径、外半径和壁厚。
经计算得到传统挤出制备的塑料微管内半径、外半径和壁厚的胀大率分别为38%、37.6%和36.8%。而从图7b、d可以看出,气体辅助技术制备的塑料微管内半径、外半径和壁厚的胀大率基本为0,即塑料微管未发生任何挤出胀大和变形现象。
4.2流速分析
图8a、b分别为传统和气辅条件下塑料微管熔体在口模出口截面上的径向流速及沿轴向的Z流速分布曲线。
从图8a可知,对传统挤出而言,塑料微管靠近外壁面的熔体向外层膨胀(流速为正值),而靠近内壁面的熔体向内层膨胀(流速为负值),这种流速分布是传统塑料微管挤出口模时的流速体现。而对塑料微管气辅挤出而言,由于气辅作用,塑料微管熔体在口模出口没有产生径向流速,表明气辅技术消除了塑料微管径向的挤出胀大现象。另外,从图8b可知,对传统挤出而言,沿轴向方向,熔体在口模流道内壁面上的流速为0,为无滑移流动方式;而在口模出口处,熔体流速产生了一个巨大的突变,这种突变是熔体受到快速拉伸以及熔体流速迅速重排的表现。此外,在实际挤出生产中,这种流速突变极易使得塑料微管表面产生熔体破裂现象。从图8b还可以看出,引入气辅技术后,熔体在轴向上的流速分布均匀一致;在出口处也未产生流速突变现象,材料熔体破裂问题得到改善。
4.3压力分析
为了揭示上述熔体流速分布现象,得到了熔体在传统方式和气辅方式下塑料微管熔体的压力及应力等分布情况,其中压力分布如图9所示。从图9中可知,在传统挤出条件下,熔体入口处产生了很大的入口压力;而对塑料微管气辅挤出而言,其入口压力非常小。因此,传统条件下塑料微管挤出容易在口模出口处残留压力降,使得易出现挤出胀大现象。而气辅条件下的入口压力很小,且随着熔体流出口模,口模出口处的多余压力降基本消失,因此挤出胀大等现象得到了改善。
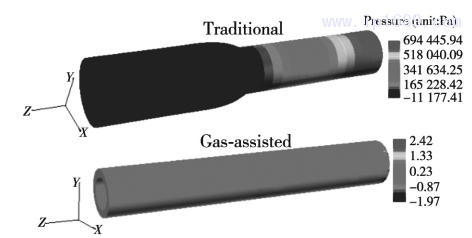
4.3压力分析
为了揭示上述熔体流速分布现象,得到了熔体在传统方式和气辅方式下塑料微管熔体的压力及应力等分布情况,其中压力分布如图9所示。从图9中可知,在传统挤出条件下,熔体入口处产生了很大的入口压力;而对塑料微管气辅挤出而言,其入口压力非常小。因此,传统条件下塑料微管挤出容易在口模出口处残留压力降,使得易出现挤出胀大现象。而气辅条件下的入口压力很小,且随着熔体流出口模,口模出口处的多余压力降基本消失,因此挤出胀大等现象得到了改善。
4.4应力分析
图10a、b分别为沿轴向方向上传统挤出和气辅挤出方式制得的塑料微管熔体在内壁面、外壁面上的剪切应力及第一法向应力差分布曲线。
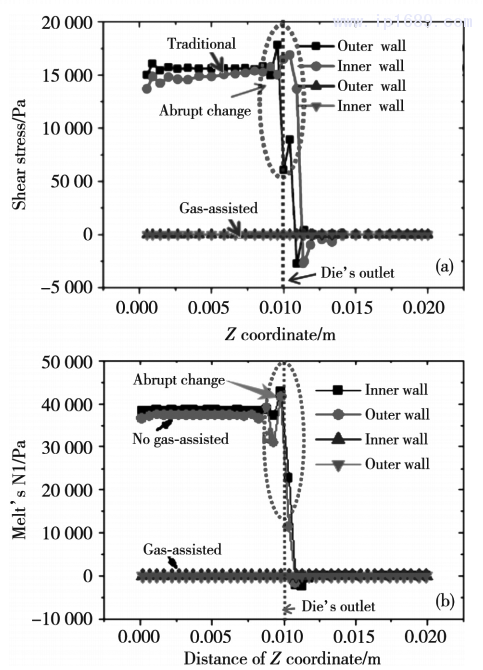
图10a、b可知,传统塑料微管挤出在口模流道内、熔体内壁面和外壁面上均产生了较大的剪切应力和第一法向应力差。此外,在口模出口处,剪切应力和第一法向应力差突然增大。这种较大的剪切应力和第一法向应力差使得流道内的熔体分子链产生了取向效应,并存储了较大的弹性能。当熔体从口模出口挤出时,熔体之前所存储的弹性能将释放回复,使得塑料微管熔体的内壁面和外壁面均向内外径向方向产生膨胀,从而引发塑料微管直径和壁厚的增大,这是传统挤出方式中引发熔体在口模出口处产生径向流速分布并进而产生挤出胀大的主要原因[19]。而对气辅挤出而言,塑料微管气辅挤出在熔体的内壁面和外壁面上产生的剪切应力及第一法向应力差非常小,对熔体存储弹性能几乎没有影响,在整个流动过程中熔体均处于无弹性能存储和分子链松弛的状态。故当熔体被挤出口模时,不产生任何挤出胀大和变形现象。
5结论
(1)需要在塑料微管内外壁面与口模壁面之间建立内外双层气体辅助层,才能较好地消除塑料微管挤出产生的诸多问题。
(2)内外气体辅助层的引入不仅极大减小了口模流道内熔体所受到的压力,而且使得熔体与口模壁面之间的剪切应力和第一法向应力差也得到了极大消除。
(3)由于气辅作用下熔体的压力和应力得到消除,减小了熔体在口模流道内的弹性储能和口模出口处的流速突变分布,最终较好地消除了传统挤出所产生的挤出胀大、熔体破裂和挤出变形等问题。
参考文献
11.1.吴大鸣,李晓林,刘颖.塑料,2003(1),26.
12.2.王翔,王惠明,许忠斌.中国塑料,2015,29(10),1.
13.3. Tian H Q,Zhao D Y,Wang M J,etal.Journal of
14.Materials Processing Technology,2015,225,357.
15.4. Ansari M,Derakhshandeh M,Doufas A A,etal.Pol-
16.ymer Testing,2018,67,266.
17.5.任重,黄兴元,柳和生.中南大学学报(自然科学版),2016,
18.47(4),1128.
19.6. Liang J Z.Polymer,2001,42(8),3709.
20.7. Hayden T,Yvonne S,Heike E H.Journal of Fluid
21.Mechanics,2017,810,127.
22.8. LiangRF,Mackley MR.Journal of Rheology,2001,
23.45(1),211.
24.9.Ren Z,Huang X Y.Materials Science Forum,2019,
25.956,253.
26.10.任重,黄兴元,柳和生,等.四川大学学报(工程科学版),
27.2016,48(1),200.
28.11.黄楚晔,柳和生,黄兴元,等.塑料工业,2015,43(10),
29.44.
30.12.Ren Z,Huang X Y.Materials Science Forum,2016,
31.861,189.
32.13.黄益宾,余忠,熊爱华,等.中国机械工程,2017,
33.28(7),877.
34.14.Ren Z,Huang X Y,Liu H S,et al.Journal of Applied
35.Polymer Science,2015,132(42),1.
36.15.邓小珍,柳和生,黄益宾,等.中南大学学报(自然科学版),
37.2016,47(7),2227.
38.16.Thien N P,TannerRI.Journal of Non-Newtonian Fluid
39.Mechanics,1977,2(4),353.
40.17.DhadwalR,Banik S,Doshi P,et al.Applied
41.Mathematical Modelling,2017,47,487.
42.18.何建涛,柳和生,黄兴元,等.中国塑料,2014(5),64.
43.19.Mitsoulis E,Heng F L.Rheologica Acta,1987,26,
44.414.