沈忠良 1,2,3,张强 1,郑子军 3,欧长劲 3,孙圣 2,邓益民 1
(1. 宁波大学机械工程与力学学院,浙江宁波 315211 ; 2. 宁波欧琳厨具有限公司,浙江宁波 315000 ; 3. 浙江工商职业技术学院,浙江宁波 315012)
摘要:以聚对苯二甲酸乙二酯 (PET) 薄膜为研究对象,自制了板式辐射加热装置辅助的模内与模外装饰一体的 超高压成型机,采用控制变量法,在 6 种不同加热温度下进行高压成型实验,研究了 PET 薄膜对温度变化的敏感性, 探讨与分析了温度对高压成型件周向厚度分布和回弹的影响。结果表明,在拉伸作用下,材料沿拉伸方向流动,高压 薄膜厚度减薄明显,温度对薄膜的减薄有显著影响。当加热成型温度在 160°C时,周向厚度的减薄率出现最大值,为 47.6% ;当温度为 60°C时,出现最小值,为 29.6%,并且减薄率和温度的升高成正比。回弹量在 160°C时出现最大值, 为 6.3 mm ;60°C时出现最小值,为 0.7 mm,且回弹量和温度的升高成正比。另外,实验发现,在温度超过 100°C时, 回弹量的增长会骤然加快;在凹模圆角及其周边厚度减薄较小,回弹也较小。
关键词:聚对苯二甲酸乙二酯薄膜;厚度;回弹;温度;高压成型
高聚物薄膜的成型特性研究是模内装饰 (IMD) 技术的重要技术支撑 [1],而在高聚物薄膜的成型特 性的影响因素中温度是重要参数 [2],厚度变化与回 弹变化是仅次于成型过程中褶皱与破裂的关键实际问题 [3],因此,开展温度对高聚物薄膜成型过程厚度 变化与回弹变化的研究具有重要意义。
国内外学者在高聚物薄膜成型特性方面开展 了各有特色的研究,主要的研究方法包括:基于厚 度测试仪 [4–5]、万能拉伸机 [6–8] 等实验设备的实验研 究;基于有限元软件的数值实验研究 [9] 和基于本构 模型等原理的理论研究 [10] 等。 J. H. Yoon 等 [11] 探 讨了由于注塑过程引起高温而导致的高聚物薄膜变 形 ( 局部撕裂 ) 特性研究,采用单向耦合的方法对 聚合物膜的注射成型过程进行了数值模拟,给出了 一种分析与预测薄膜变形的有效方法,同时从机理 与微观角度给出了研究高聚物薄膜受温度变化影响 的实验手段 [12]。Y. H. Lin 等 [13] 整合了万能拉伸机 测试获得的塑料薄膜的力学特性,通过有限元数值 实验的方式探讨了温度变化、温度的不对称性对高 聚物塑料薄膜在 IMD 领域应用时成型特性的影响, 结果表明,薄膜在温度不对称情况下引起的结晶度 差异是导致薄膜变形与翘曲的主要原因。
C. O. Phillips 等 [14] 基于万能拉伸机所获得的 材料力学性能数据与 ( 电子 ) 油墨印刷过程的相关 参数,分析和探讨了适合油墨均匀印刷的关键技术、 油墨印刷过程对高聚物薄膜成型特性的影响,之前 他们 [15] 还基于有限元数值模拟的方法开展了 IMD 工艺下高聚物薄膜的成型特性研究,利用拉伸试验 数据建立的材料模型,对该键盘表面覆膜高压成型 过程进行了仿真。结果表明,模具和薄膜之间的摩 擦防止了薄膜的畸变,上述两者的界面是有效控制 薄膜成型特性的关键界面。G. Kim 等 [16] 认为,薄 膜插入成型 (FIM) 是提高产品表面功能或美学质量 的方法之一,并采用黏弹性本构关系描述了聚合物 膜的流变行为,采用恒速单轴高温拉伸试验方法获 得了流变学参数,提出了一种可视化的模式变化预 测方法,并与实际产品的分析结果进行了比较,验证 了该方法的有效性。
T. Azdast 等 [17] 以聚甲基丙烯酸甲酯 (PMMA) 片材作为研究对象,通过有限元数值模拟方法,利用 自由成型和插塞辅助成型进行了高聚物变形过程中 材料厚度的变化研究,研究了不同温度下自由成型 和插塞辅助成型方法的不同组合,并根据每种方法 在最终成型件总高度中所占的比例进行了最优化研 究。 S. C. Chen 等 [18] 探讨了 0.125~0.2 mm 厚度 的 IMD 成型用高聚物薄膜深拉伸成型与模具温度、 预涂膜加热温度、插塞速度、插塞保温时间、插塞热 成型深度等的影响关系,研究了薄膜的壁厚变化规 律和壁厚分布规律,结果表明,结晶温度对膜的拉伸 比和膜厚变化率影响最大。
综上所述,温度对高聚物薄膜成型特性的影响是塑料件 IMD/模外装饰 (OMD) 成型的关键问题, 且影响成型特性的因素较多,存在一定的相互作用 关系。上述研究已给出了温度对高聚物薄膜成型影 响的基本研究方法,但是,研究尚未明确给出温度对 高聚物薄膜成型特性影响的作用关系。同时,表征 高聚物薄膜的本构模型所采用的参数多数为常温下 获取,并不能准确表征随着温度变化引起的高聚物 薄膜力学参数变化对成型特性带来的影响。
笔者在上述研究的基础上,以聚对苯二甲酸乙二酯 (PET) 薄膜为研究对象,通过自主研制的超高 压 IMD/OMD 一体高压成型机进行成型实验,开展了高聚物薄膜的厚度与回弹性对温度变化敏感 性的研究,探讨了温度变化对薄膜厚度、回弹量的影响,同时探讨了薄膜成型结构对薄膜温度敏感性的影响。
1 实验方法
1.1 主要原材料
单 面 加 硬 防 刮 花 PET 薄 膜:T60,厚 度 为250 μm,表面无明显彩虹纹,拉伸强度 ≥ 160 MPa,标称加热收缩率≤ 1%,日本东丽株式会社。
1.2 主要仪器与设备
高压 IMD/OMD 气体成型一体机:HPFM– 350C 型,自制; 千分尺:103–137型,精度为±2 μm,日本 Mitutoyo 公司。
1.3 实验方法
通过进行不同温度下的高压成型实验研究高聚物薄膜热成型的规律。超高压 IMD/OMD 气体 成型一体机的红外辐射加热部件的工作原理如下: 以高熔点的合金材料作为辐射体,通电后由电阻发 热而产生热辐射作为辐射源 [13]。与传统的加热方 式相比,红外辐射加热可以透入薄膜表面一定深度, 在薄膜厚度只有 0.25 mm 的情况下,具有非常好的 加热效果。此外,红外辐射加热装置结构简单,设备 维护方便,加热方式易于控制,并且加热的速度快、 热量散失小,因此具有很高的加热效率。
膜片的加热需要一定的加热面积,因此在设计 加热装置时,选用板式加热方式,将辐射元件按一定 的秩序排列在一块方形板上,板式辐射使得膜片受 热均匀,且结构简单,具体的结构简图如图 1 所示, 加热装置共有 6 排辐射元件,每排 5 个,共 30 个,每 个辐射元件的温度都可以单独控制,在实验时,通过不断调整各区域的温度,以达到膜片最好的成型状 态。
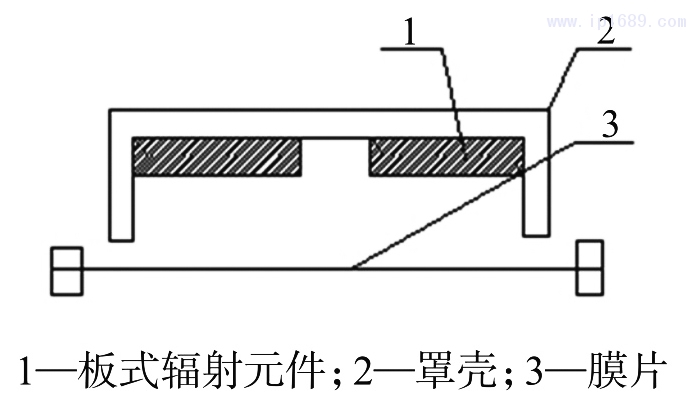
实验采用的 PET 薄膜的玻璃化转变温度为 79°C,而热成型工艺温度通常控制在 100~150°C 之间 [14],因此在进行高压成型实验时,选择的膜片 加热温度分别为:60,80,100,120,140,160°C,实验 过程中,上、下模的温度分别始终控制在 140°C和 130°C。
图 2 是高压成型实验的流程图,具体的实验步 骤如下:
(1) 放膜。首先将膜片放置在型腔中,并用夹边 模具固定,利用夹边模具上的定位销定位,利用 Y 型密封圈实现装置的密封;
(2) 加热膜片。弹出加热板,所有温度均采用红 外辐射的方式来控制,同时可以实现分区控制;
(3) 合模。利用液压缸控制开模、合模,并提供 所需要的合模力;
(4) 吹高压。合模完成后,通过气压泵向模具内 吹高压,高压吹气压力为 30 MPa ;
(5) 保压。高压保压时间为 4 s ;
(6) 泄压开模。达到保压时间后,泄压 5 s,之 后开模取件,更换膜片。保持其它工艺参数不变,仅 改变加热温度,继续进行实验。
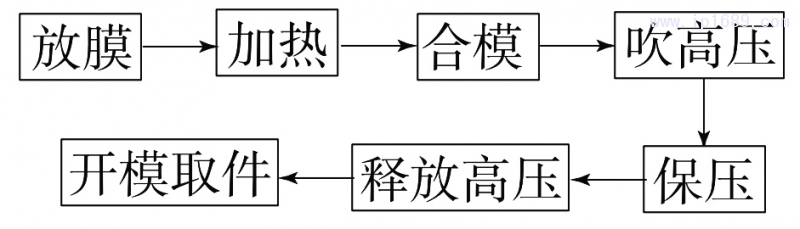
图 2 高压成型实验流程图
2 结果与讨论
2.1 温度对厚度的影响
为了研究温度对高压成型件厚度的影响,定义 减薄率 (m) 为:

式中:d0——高聚物薄膜的原始厚度;
d——高聚物薄膜成型后的厚度。
以 某 产 品 成 型 件 为 例 ,将 其 沿 周 向 切 开 ,选 取 40 个测量点,如图 3 所示,分别测量这 40 个点所在位置的壁厚。成型件薄膜的原始厚度为 0.25 mm,选用千分尺作为测量工具。为了减小误差,每个点 需要进行两次测量然后取平均值,记录并统计各个 温度下壁厚的测量值。不同加热温度下高压成型件 壁厚的分布如图 4 所示,其减薄率数据列于表 1。
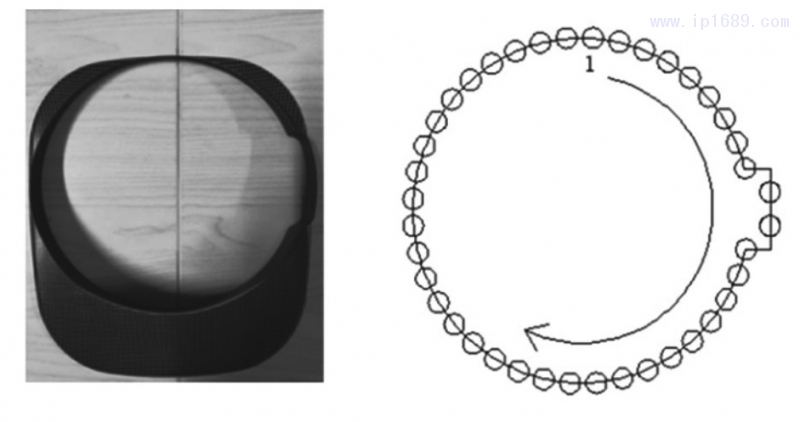
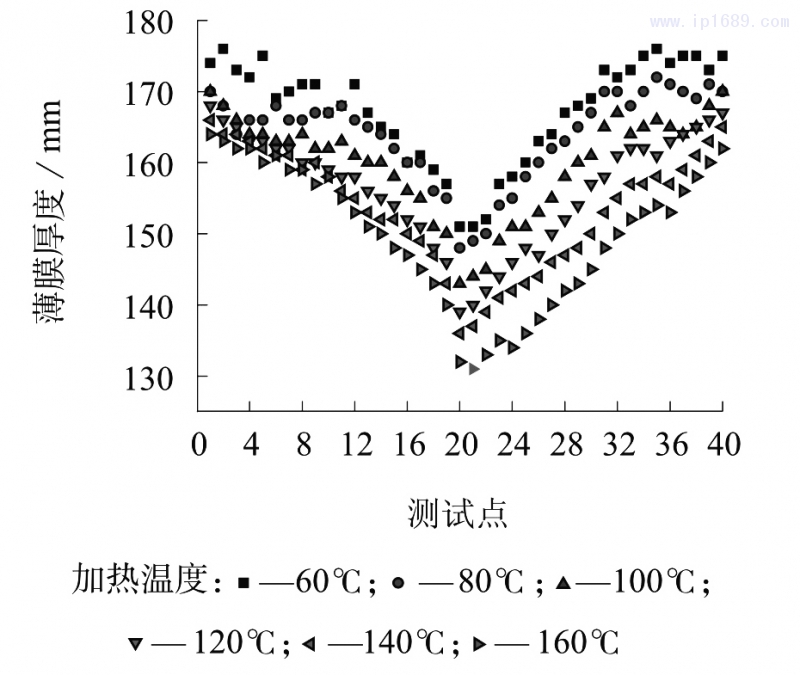
图 3 成型产品与测量点分布
图 4 不同加热温度下高压成型件壁厚的分布
表 1 不同加热温度下高压成型件壁厚减薄率数据
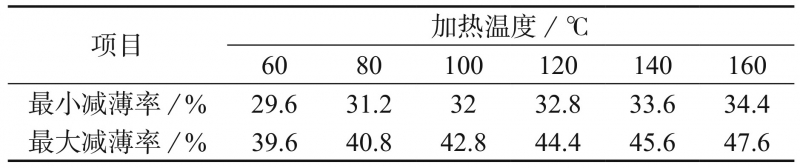
由图 4 和表 1 可以看出,随着加热温度的升 高,高压成型件壁厚的减薄率越来越大,最小减薄 率发生在 60°C时,最小减薄率为 29.6% ;最大减薄 率发生在 160°C时,最大减薄率为 47.6%。在高压 成型件的成型高度最高处,60°C下成型后的厚度为 0.151 mm,160°C下的厚度为 0.131 mm,由此可见, 温度对高压成型件壁厚的影响较大。
通过对 6 种不同加热温度下高压成型件壁厚分 布曲线进行对比分析,可以得到如下结论:
(1) 温度越高,高压成型件的厚度越来越薄,因 此,最大减薄率和最小减薄率都随之升高;
(2) 材料在成型时受到来自各个方向上的拉应 力,通过厚度分布可以得出最容易产生破裂的区域, 在工业生产中,该区域是需要重要关注的位置;
(3) 分析高压成型件壁厚最薄处的成型情况,发 现该区域材料的成型高度最高,由于拉伸作用,沿拉 伸方向流动,在材料一定的情况下,该区域的厚度也就变得薄。
2.2 温度对回弹性的影响
高压成型后部分产品会出现起皱,这是由于材料的回弹造成的,因此在研究薄膜的起皱现象时,实 际上是在研究材料的回弹现象。材料的回弹性是一 个相对复杂的过程,受到各种因素的影响,例如模具 的形状、材料的厚度以及性能、摩擦力等众多因素。 在成型完成后,当压力被卸载,累积在薄膜材料中的 弹性能都会释放出来,使得零件的尺寸发生变化。 在高压成型时,薄膜会发生弯曲作用,根据弯曲性能 原理 [15],一定会产生回弹现象,只是回弹的程度有 高有低。因此,如何预测回弹是控制高压成型件质 量的关键环节。
在预测和控制回弹方面,常用的方法有解析 法、数值模拟法以及实验法。在运用解析法时,首先 通过理论分析研究材料成型的过程,然后依靠数学 模型揭示回弹产生的机理,但解析法在应用时有很 大的局限性,只能适用于简单的冲压成型,对于复杂 的成型,数学模型难以建立,计算太庞大,对技术人 员的要求过高,且不适用于生产实际。数值模拟法 通过建立模型进行计算机仿真研究,本质上也是从 理论上研究问题,加工的环境过于理想化,经常与生 产实际不符合。而实验法与前二者不同,实验法立 足于生产实际,理论结合实践,通过在实验中获取不 同的工艺参数对回弹的影响,分析实验数据来研究 回弹的规律。综上所述,实验法是研究回弹基本规 律的可靠手段。
不同加热温度下高压成型件壁厚的回弹性如 图 5 所示。
由图 5a 可以看出,随着加热温度的升高,高压 成型件壁厚的回弹量增大。当加热温度低于 100°C 时,回弹量的增长较为缓慢,当加热温度超过 100°C 后,回弹量的增长会骤然加快。60°C时的回弹量为 0.7 mm,160°C时上升到 6.3 mm,表明加热温度对 高压成型件壁厚的回弹量有显著的影响。
回弹百分比按式 (2) 计算 :

式中:w——回弹百分比;
h——回弹量;
h0——高压成型件设计高度。
由图 5b 可以看出,高压成型件壁厚的回弹百分比与加热温度成正比,加热温度越高,回弹越严重。
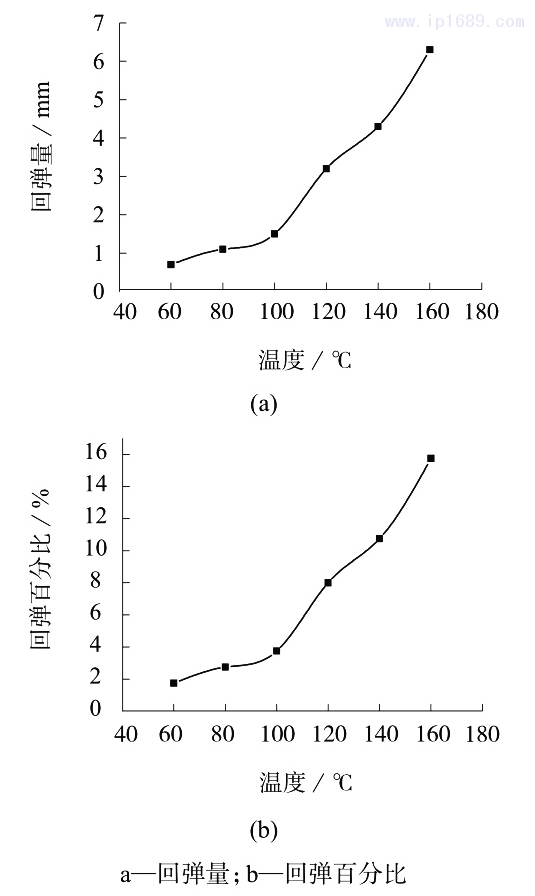
a—回弹量;b—回弹百分比
图 5 不同加热温度下高压成型件壁厚的回弹性
高压成型件壁厚回弹的本质是:高压成型件成 型后,卸载高压空气,在成型过程中储存的弹性变形 能需要释放,从而引起内应力的重新分布,导致高压 成型件的外形尺寸发生了相应的改变,如图 6 所示。
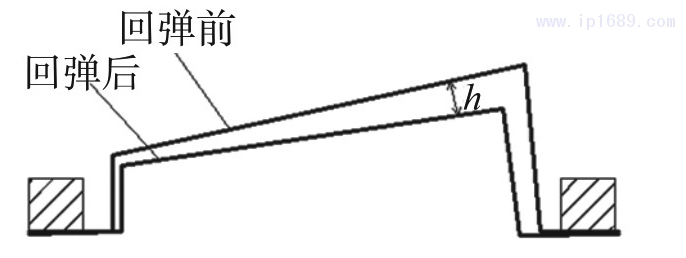
图 6 高压成型件壁厚回弹示意图
随着高压成型过程中腔内的压力越来越大,在成型高度越高的位置,薄膜的减薄越严重,该位置也 是变形最大的位置。高聚物薄膜的成型方式是高压 吹气成型,现有的技术基本能保证厚度的均匀分布, 但在变形区域较大、成型高度较高的位置,成型完成 后残余的内应力越大,当高压卸载完成后,该区域的 应力得到释放,导致在变形较大的区域回弹越明显。 但在凹模圆角及其周边的厚度减薄和变形程度则没 有那么严重,卸载后,产生的回弹量较小。
3 结论
通过实验研究温度对高聚物薄膜成型件厚度分布和回弹的影响。设计了膜片加热装置,使用自 制超高压 IMD/OMD 气体成型一体机,对 6 种不 同加热温度下的高压成型进行实验,得到如下结论:
(1) 在拉伸作用下,材料需要不断沿拉伸方向补 足,并且材料是定量的,因此在成型高度越高的位置,厚度越薄,随着温度的升高,高压成型件的厚度 变薄,在 160°C下具有最大减薄率,在 60°C时具有最 小减薄率,通过分析厚度的分布情况,得到薄膜最易 产生破裂的危险区域。
(2) 保压 4 s 后泄压,由于腔内持续高压,产生 的内应力需要释放,因此成型件厚度出现回弹,在成 型高度越高的位置,成型件厚度的变形量越大,产生 的内应力越大,回弹量也越大,在凹模圆角及其周边 厚度减薄较小,卸载后,回弹也较小。
参考文献
[1] 卢剑 . 基于薄膜外部成型工艺的模腔机构整体设计 [J]. 塑料工 业,2017,45(2):54–57.
[2] 何丹辉 . 薄膜表面装饰成型设备控制系统设计 [J]. 塑料,2017, 46(1):105–108.
[3] 沈忠良,郑子军,欧长劲,等 . 基于双向拉伸的温度对高聚物薄膜热成型性能的影响研究 [J]. 塑料工业,2018,46(5):81–84,88.
[4] Nagarajan B,Castagne S,Wang Z,et al. Influence of plastic de- formation in flexible pad laser shock forming–experimental and numerical analysis[J]. International Journal of Material Forming, 2017,10(1):109–123.
[5] Bonfanti A,Syngellakis S,Bhaskar A. Response and residual curvature of bent-stretched circular rods with applications to metal forming:Closed-form solutions for elastic-perfectly plastic and hy- perbolic hardening materials[J]. International Journal of Mechanical Sciences,2017,123:340–349.
[6] 郭康丽,张一辉,张一铭,等 . 聚合物阻隔薄膜及其发展应用 [J]. 工程塑料应用,2018,46(1):128–133.
[7] 宋清华 . IMD 膜成型后变形问题研究 [D]. 杭州 : 浙江工业大学, 2019.
[8] 徐生,肖国华,黄继军 . 汽车空调触摸面板 IMR 成型组合模具设计 [J]. 塑料科技,2018,46(1):90–96.
[9] Zecevic M,Knezevic M. Modeling of sheet metal forming based on implicit embedding of the elasto-plastic self-consistent formula- tion in shell elements:Application to cup drawing of AA6022–T4[J]. Jom,2017,69(5):922–929.
[10] 苏占伟,孟正华,王辉,等 . 装饰薄膜对模内嵌膜产品力学性能 的影响规律 [J]. 工程塑料应用 .2018,46(10):51–56.
[11] Yoon J H,Hur N,Bae A H,et al. Coupled analysis of injection molding and film forming for identifying film deformation in IMD process[J]. Journal of Computational Fluids Engineering,2013, 18(3):20–25.
[12] Yoon J,Hur N,Bae A H,et al. A numerical analysis on the behav- iors of polymer film and resin in an in-mold decoration process[C]// Conference proceedings of ASME 2013 fluids engineering division summer meeting. Incline Village,NV,USA:ASME Fluids Engi- neering Division. doi:10.1115/FEDSM2013-16399.
[13] Lin Y H,Chen H L,Chen S C,et al. Effect of asymmetric cool- ing system on in-mold roller injection molded part warpage[J]. International Communications in Heat and Mass Transfer,2015, 61:111–117.
[14] Phillips C O,Beynon D G,Hamblyn S M,et al. A study of the abrasion of squeegees used in screen printing and its effect on performance with application in printed electronics[J]. Coatings, 2014,4(2):356–379.
[15] Phillips C O,Bould D C,Claypole T C,et al. Finite element modelling of low temperature forming of polymer films with ap- plication in in-mould decoration[J]. Materials & Design,2009, 30(3):537–550.
[16] Kim G,Lee K,Kang S. Prediction of the film thickness distribu- tion and pattern change during film insert thermoforming[J]. Poly- mer Engineering & Science,2009,49(11):2 195–2 203.
[17] AzdastT,DoniaviA,AhmadiSR,etal.Numericalandexperi- mental analysis of wall thickness variation of a hemispherical PMMA sheet in thermoforming process[J]. The International Jour- nal of Advanced Manufacturing Technology,2013,64(1–4):113– 122.
[18] Chen S C,Huang S T,Lin M C,et al. Study on the thermoforming of PC films used for in-mold decoration[J]. International Commu- nications in Heat and Mass Transfer,2008,35(8):967–973.