摘要:针对方金属板材在成形过程中易破裂问题,以方锥台为试验制件,设计响应曲面试验方案,对多点渐进成形过程进行数值模拟,借助Design⁃Expert,将成形工具头直径、进给量、成形角、板厚作为分析因子,厚度减薄率φ与成形深度h作为响应因子,建立多元回归破裂预测模型,对预测模型得到的最优与最差工艺参数进行数值模拟与试验,并对得到的结果进行对比分析。结果表明:预测结果、数值模拟结果、试验结果在数值上非常接近,以方锥台为对象构建的破裂预测模型,可用于金属板材破裂的预测,提高金属制件成形质量。
关键词:多点渐进成形;预测模型;响应曲面;数值模拟
DOI:10.15938/j.jhust.2018.01.005
中图分类号:TG306 文献标志码:A
文章编号:1007-2683(2018)01-0023-07
引言
破裂是金属板材在渐进成形过程中最常见的问题[1]。针对该问题,国内外众多学者对板材破裂进行了大量的研究。李军超等[2]通过采用均布策略和顺逆相间的加工方式,有效的避免了在数值模拟过程中由于采用G代码加工轨迹所造成的板材破裂等失稳现象。文[3-4]阐述了缩颈在单点渐进成形中的产生,并对比了两点和单点渐进成形这两种成形工艺下制件的成形精度和成形极限,指出破裂成形极限曲线相比传统的成形极限曲线更能准确的描述破裂。Duc⁃ToanNguyen等[5-6]结合混合硬化法则和Oyane韧性破裂准则通过数值模拟探讨了工具头直径和下压量对镁合金韧性断裂的影响,发现混合硬化法则能更加准确的预测成形极限。Ja⁃cobSmith等[7]通过对比SPIF和ADSIF两种成形工艺,发现ADSIF板材破裂的产生要滞后于单点渐进成形。李磊等[8]通过四组破裂仿真和试验所得到的应力应变数据,有效的预测了LY12(M)硬质铝板的成形极限。
本文采用了响应曲面法,建立多元回归方程,提出一种多参数预测金属板材破裂的预测模型。并将成形深度h作为评价指标,对以成形深度h为数学模型建立的过程进行详细分析。并对破裂预测模型进行验证和寻优,通过试验和数值模拟的结果来验证预测模型及寻优所得的工艺参数组合的正确性。
1、试验模型及方案
1.1 试验模型
以方锥台制件为目标成形件,制件形状参数毛胚边长L0=300mm、成形区最大边长L=200mm、高度H=60mm、成形角θ=45°,方锥台制件示意图如图1所示。
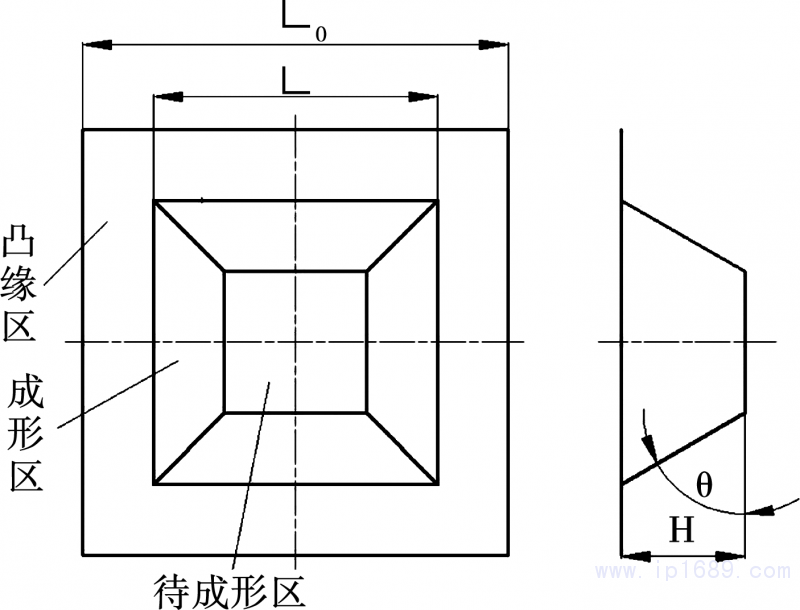
图1方锥台制件示意图
1.2、试验方案设计
将成形工具头直径D、进给量ΔZ、成形角θ、板厚t0作为分析因子,将厚度减薄率Φ和成形深度h作为响应因子[9]。由于渐进成形工艺中进给速度v对成形质量影响较小[10],在节省时间的前提下,进给速度v设置为2500mm/min。
采用BBD工具箱来进行试验设计寻优,根据前期研究可知当方锥台制件成形到15mm,韧性值I=4时[11],能够较好的预测制件的破裂情况。因此当方锥台制件成形到15mm时,统计制件厚度减薄率φ;当制件韧性值I=4时,统计制件成形深度h,如表1所示。
表1试验设计
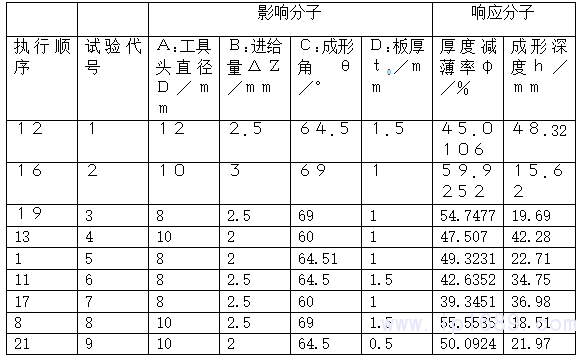
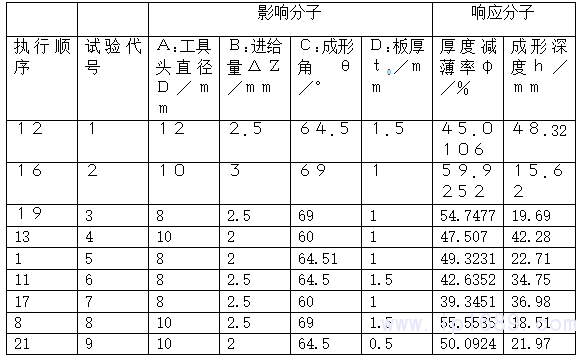
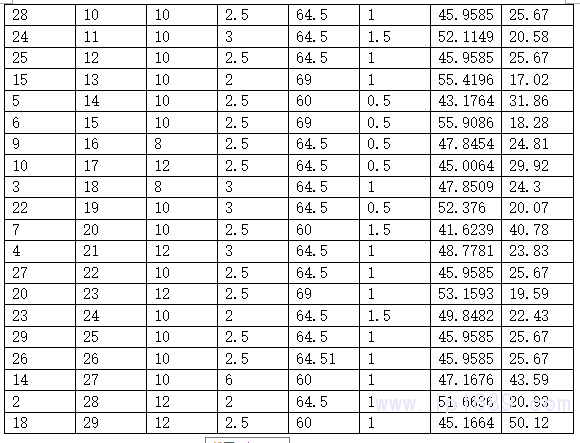
2、破裂预测模型建立
2.1.响应模型方差分析
选取二次方模型作为成形深度h的响应模型,并对成形深度h二次方差响应模型进行方差分析,具体如表2。
表2模型的方差分析
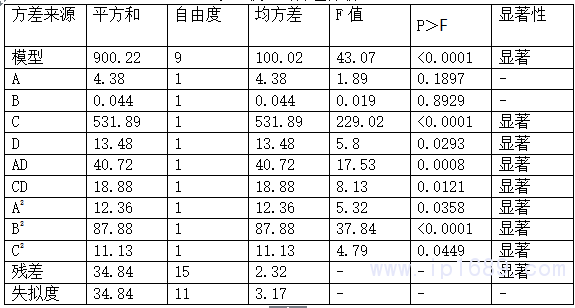
由表2可知,F值为43.07意味该模型是显著的,同时P>F值小于0.0001,表明模型只有0.01%的机会受到外界较大的干扰,因而该响应模型可靠。C和B2的“P>F”值均小于0.0001,表明在板材多点渐进成形中,成形角和进给量对方锥台制件所能达到的成形深度影响最大;一次项中各因素的“P>F”值从小到大排列依次为:C