林建铭1,王嘉硕1,肖建华1,尹志强2,宋仕强1,王锦成1
(1.上海工程技术大学,化学化工学院化学实验中心,上海201620;2.南昌航空大学,材料科学与工程学院,江西,南昌330063)
摘要:采用3D打印制备CF/ABS试样,置于在模具内进行TPU注塑成型,形成注塑层全包裹或半包裹3D打印层的复合结构。结果表明,与全包裹的芯壳结构相比,半包裹的上下叠层结构更稳定,成型过程更容易控制,成型质量更高。其拉伸强度和断裂伸长率分别为16.47MPa和464%,与全包裹式相比,分别提高了18%和40%。3D打印与注塑复合成型的上下叠层制件表面平整,3D打印层与注塑层层间粘接效果较好,拉伸前未出现分层现象。
关键词:3D打印;注塑成型;复合成型;芯壳结构;上下叠层结构
引言
注塑成型和3D打印是复杂聚合物制品成型的主要加工方法。注塑成型表面光滑、力学强度高、适合大规模生产;3D打印适用于复杂模型的个性化定制。
国内外研究者将注塑成型和3D打印2种技术进行对比研究。付汝兴等[1]通过注射和3D打印2种方式加工乙烯-酸酸乙烯共聚物改性聚乳酸(PLA/EVA)发现,3D打印的试样拉伸强度是注塑成型的60%。Cevdet等[2]研究发现,与注射成型的试样相比,3D打印的PLA和聚氨酯改性聚乳酸(PLA/TPU)的拉伸强度、弯曲强度和断裂伸长率均较低。Gerardo等[3]发现,3D打印制的丙烯腈-丁二烯-苯乙烯(ABS)拉伸强度均为注塑成型制得试样的75%,3D打印的聚对苯二甲酸乙二醇酯-1,4-环己烷二甲醇酯(PETG)拉伸强度是注塑成型得到试样的90%;并且,ABS和PETG由注塑成型改为3D打印后,断裂伸长率下降了80%。Elena等[4]采用注射和3D打印加工了短碳纤增强聚酰胺(CF/PA),结果表明,在3D打印中,短纤维沿喷嘴方向取向,提高了3D打印制品的强度;而短纤维在注射制品中仅表层是高度取向的,内部呈无序叠放状态,因此,短CF/PA通过3D打印和注塑成型制品的力学性能较相似。Ameya等[5]通过29.5%回收碳纤维增强HDPE,注射成型试样拉伸强度提高了188.0%,3D打印件拉伸强度提高了160.7%。
3D打印技术可用于复杂注塑模具的快速制造。3D打印技术应用于注塑模具的设计和加工,其具有成本低、可自由设计、便于快速制造等特点[6]。Qian等[7]研究发现,注塑充模时受高温高压及开模时脱模力的作用,3D打印出的PLA注塑模具核心零部件,注塑成型30次出现裂纹,60次发生完全破坏,因此,3D打印的注塑模具适用于小批量的生产。Khurram等[8]通过比较3D打印的注塑模具与金属铝制的注塑模具发现,制得的试样的拉伸应力、最大力、刚度、硬度及尺寸精度均较接近,证明了3D打印在注塑模具设计和加工中具有可行性,可以推广应用于复杂注塑模具的设计和加工,有望进一步降低模具加工费用和时间。刘绘龙等[9-10]采用光固化3D打印制造注塑模具,注塑高熔点聚醚醚酮(PEEK)制备下颌骨关节窝植入物,结果表明,注塑件组织致密,无空隙和缺损,且保形性好、尺寸精度高,尺寸误差主要来源于模具的制造误差和注塑过程中模具热胀冷缩产生的形变误差,满足医用个体化植入物的精度要求。
3D打印在医学、航空等复杂结构件难成型的问题中显示越来越多的优势。Yang等[11]3D打印2个金字塔倒接的复杂支撑结构,与PP注塑成型相比,拉伸强度提高了50%,断裂伸长率降低了90%,3点弯曲强度降低了20%。Balaji等[12]采用3D打印将纳米甲壳素增强聚己二酸/对苯二甲酸丁二醇酯(PBAT-NC30%)制备为个性化头盖骨,用于植入式头颅修复手术;Yuan等[13]3D打印注射模制PEEK月状假体,在治疗月骨坏死Ⅲ期病临床中,术后无手腕疼痛和功能丧失。Wang等[14]在有机塑料板内制备加强筋,将2种聚合物材料复合得到一个整体;Boros等[15]通过注射-注射、注射-3D打印、3D打印-3D打印、3D打印-注射4种组合方式,制备大型T型件,T型撕裂强度测试均表明,4种复合成型的界面在低结晶聚合物中获得了较好的界面粘接力。
文章将碳纤增强CF/ABS材料通过3D打印成型得到哑铃型试样,置于注塑机的模具中,通过注射低结晶度的TPU将3D打印件包裹,形成半包裹和全包裹2种方式,研究3D打印和注射复合成型的可行性及包裹方式对复合材料力学性能及断裂方式的影响。
1 实验部分
1.1 主要原料
TPU:TecoflexⒸLM-95A,美国Lubrizol公司;
CF/ABS3D打印丝:1.75MM,HC-9030#,金骆驼有限公司。
1.2主要仪器及设备
立式注塑机:DRV4-251,深圳市德润器业有限公司;
微机控制电子万能试验机:WDW-50,扬州市源峰试验机械厂;
电子显微镜:AM204,OEM;
3D打印机:DK160MAXS,深圳大昆三维科技有限公司。
1.3 试样的制备
1.3.1 CF/ABS复合材料3D打印
使用Solidworks三维软件建立拉伸试样哑铃型模型,导入切片软件中进行切片,然后,导入3D打印机中使用CF/ABS材料打印。再进行3D打印,打印材料为CF/ABS 1.75mm、取向角为45°、打印温度为235℃、打印速度为50mm/s、喷嘴直径为0.40mm、层厚为0.10mm、填充率为100%、热床温度为50℃。
1.3.2 CF/ABS与TPU材料复合注塑成型
将TPU树脂置于80℃真空干燥箱中,干燥4h;注塑机3段温度分别设置为190、190、185℃,将3D打印得到的CF/ABS试样放入注塑机的模具中,将着色的TPU粒料倒入注塑机的料筒中,进行二次注塑复合成型,黑色部分为3D打印的CF/ABS,蓝色部分为注塑的TPU材料。
1.3.3 复合成型的设计方式
在复合成型中,设计了2种不同的包裹形式,分别为半包裹式和全包裹式。半包裹式的注塑成型和3D打印试样尺寸一致,呈现相同尺寸的上下叠层结构;全包裹式的3D打印部分为内芯,注塑成型部分为外壳,形成芯壳结构。
1.3.4 复合成型技术
在半包裹式复合成型中,根据注塑机模具尺寸,设计厚度为模具尺寸的1/2,用CF/ABS材料3D打印出试样,然后,将其放置在注塑模具中,注塑机合模后经高温高压注塑成型,熔融的热塑性TPU熔体在45MPa压力推动下热粘接在3D打印件的上表面,成型冷却后形成上、下2层的结构。在全包裹式复合成型中,为保证3D打印件固定在注塑模具的中间位置,在3D打印件的两端设计了厚度为模具高度1/4的底座,与3D打印件一体打印成型,然后,将3D打印件置于模具中,注射成型时,熔融TPU材料通过流动包裹中间的3D打印部分,形成全包裹形式的芯壳结构。
1.4 性能测试
按照GB/T31290—2014,用微机控制万能电子试验机,以50mm/min的拉伸速率将3D打印和注塑复合成型的材料进行拉伸测试。
将AM204 数码显微镜连接电脑,打开Gaosuo 软件,将复合成型的材料断裂面放于试验台上,置于显微镜于试样上方并调整焦距,拍照。
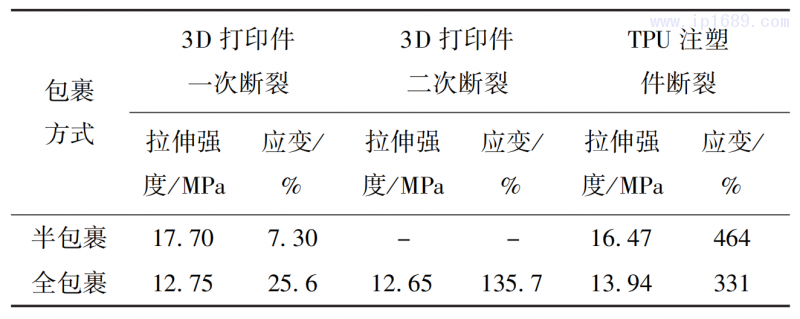
表1 3D打印与注射复合成型试样的拉伸过程中的特点
2 结果与讨论
2.2 高温高压对制件断面结构的影响
为了进一步观察拉伸试样断裂后的情况,采用数字显微镜观察拉伸试样断面。图1为复合材料拉伸断裂后,2层材料的断面结构。
图1a中为注塑模具浇口位置,当聚合物熔体流经小浇口时,小尺寸产生剪切生热和摩擦生热效应对熔体起到增温增速作用。注塑件浇口附近出现黑色的3D打印材料,因此,在注塑浇口处的高温高压作用下,注塑和3D打印层界面之间的扩散、渗透和粘接作用较好,而且,界面层间的热粘接作用大于3D打印件表层与内层之间的内聚强度,热塑性树脂材料与黑色3D打印层表层融合为一体,3D打印与注塑复合成型的2种材料的界面粘接达到理想状态(界面粘接力大于被黏物的强度)。在TPU注塑件远离浇口的位置,受到注塑浇口的增温增速效果较小,无明显变色情况,这表明,此处界面热粘合作用低于3D打印件内聚强度。
由以上对断面结构的观察和分析可知,注塑过程中,高温高压有利于提高3D打印注塑复合成型的试样界面粘接力,在工艺许可的范围内,进一步提高热塑性树脂的注射温度和注塑压力或对3D打印件进行表面预热处理等,均能有效地提高2种材料的界面粘接力。
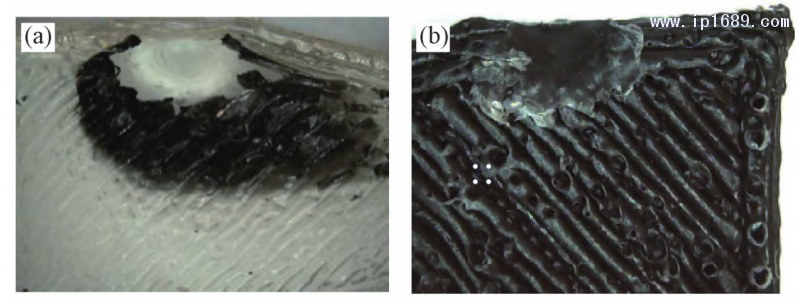
图1拉伸后的断面结构
(A)拉伸断裂后的注塑件(B)拉伸断裂后的3D打印件
2.3 聚合物结晶度对制件翘曲变形的影响
实验选取通用型热塑性树脂HDPE与TPU进行对比研究。图2a、2b分别为采用TPU材料、HDPE材料进行注塑复合成型得到的翘曲变形图。
从图2中可以看出,采用TPU材料复合成型的制品相对平整,而使用HDPE材料复合成型的制品有明显的翘曲变形。这是由于,HDPE材料的结晶度大于65%,而TPU为透明材料,结晶度为5%。注塑成型之后,随着结晶度的增大,尺寸收缩率逐渐增大,注塑层发生明显的冷却收缩,尺寸减小,而3D打印部分在注塑前后未发生明显的温度变化,且尺寸稳定,高结晶度的复合制品出现一层长(3D打印层)一层短(注塑层),2层热覆合在一起发生收缩引起的翘曲变形。
因此,在3D打印与注塑复合成型中,为避免成型后试样出现明显的翘曲变形,应尽量使用低结晶度或无定型的聚合物进行复合注塑成型。
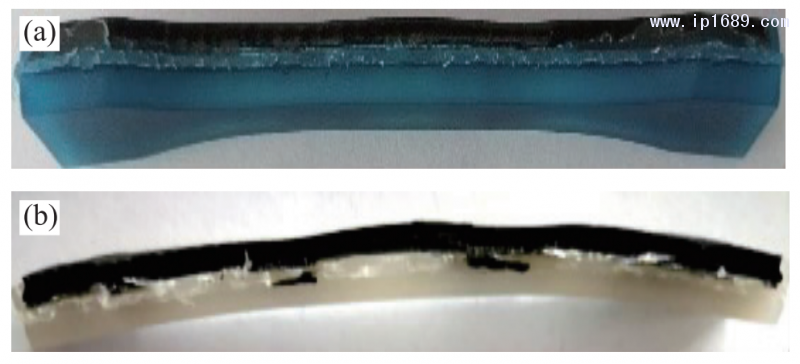
图2 3D打印件与热塑性注塑件双层材料的翘曲变形
(A)TPU(B)HDPE
3 结论
(1)将3D打印件置于在注塑模具中,进行热塑性材料的复合注塑成型,得到2种聚合物复合材料。
(2)在3D打印与注塑复合成型过程中,采用半包裹和全包裹方式对材料的性能有影响。半包裹式的拉伸强度为16.47MPA,断裂伸长率为464%;全包裹式的拉伸强度为13.94MPA,断裂伸长率为331%。因此,与采用全包裹式相比,采用半包裹式成型的样品的拉伸强度和断裂伸长率较高。
(3)断面结构观察结果表明,高温、高压条件有利于改善注塑件与3D打印件之间的层间粘接效果。
(4)TPU为透明性高分子材料,结晶度低注塑成型后,收缩率较小,与3D打印件复合成型后,制品无明显翘曲变形,外形尺寸平整。因此,3D打印与注塑复合成型技术适用于低结晶度或无定型高分子材料。
参考文献
[1] 付汝兴,郑凯鸣,王梓郡.注塑和 3D 打印聚乳酸/乙烯 - 醋酸乙烯共聚物共混物形态和韧性[ J] . 高分子材料科学与工程,2019 ,35(3) : 114 - 119.
[2] CEVDETK , VARSAVAS S , DENIZ B. Performance comparison ofthe 3D⁃printed and inj ection⁃molded PLA and its elastomer blend and fiber composites[ J] . Journal of Thermoplastic Composite Materials ,2018,32(4) :867 - 878.
[3] GAMBOA G , MAZUMDER S , HNATCHUK N. 3D⁃printed and inj ection molded polymer matrix composites with 2D layered materials [ J] . Journal of Vacuum Science and Technology A , 2020 , 26 (6 ) : 121 - 127.
[4] ELENA V T , JUANA C S , ALBERTO M M. Investigation of a short carbon fibre⁃reinforced polyamide and comparison of two manufacturing processes: fused deposition modelling ( FDM ) and polymer inj ection moulding ( PIM) [ J] . Materials ,2020 ,672(13 ) : 1 - 13 .
[5] AMEYA B , ANDREAS H , ZAN S , et al. A comparison of mechanical properties of recycled high⁃density polyethylene/waste carbon fiber via inj ection molding and 3D printing [ J ] . Polymer Compsites ,2021 ,672(9) :2408 - 2418.
[6] JOHN R C , DIZON A D , VALINO L S. Three⁃dimensional⁃printed molds and materials for inj ection molding and rapid tooling applications [ J] . Materials Research Society Communications ,2019 ,147(9) : 1267 - 1283 .
[7] QIAN Z , WU A , KEEFE M. Additive manufacturing of multi⁃ directional preforms for composites: opportunities and challenges [ J] . Materials Today ,2015 , 18(9) :503 - 512.
[8] KHURRAM A , UUAID Q , AHMAD M. Performance analysis of enhanced 3D printed polymer molds for metal inj ection molding process[ J] . metals ,2018 ,433(8) :2 - 16.
[9] 刘绘龙,孙文森,刘亚雄,等. 3D 打印树脂模具注塑聚醚醚酮成形精度研究[ J] . 西安交通大学学报,2021 ,55(12) :64 - 69.
[10] 刘绘龙,刘亚雄,孙文森,等.个性化聚醚醚酮植入物的制造工艺研究[ J] . 西安交通大学学报,2019 ,53(12) :72 - 79.
[11] YANG K M , PARK J H , CHOI T G. Analysis of mechanical characteristics of polymer sandwich panels containing inj ection molded and 3D printed pyramidal kagome cores[ J] . Elastomers and Composites ,2016 ,51(4) :275 - 279.
[12] BALAJI S , DEVI R , RAGHAVACHARI D. Scale⁃up of non⁃toxic poly ( butyleneadipate⁃co⁃terephthalate) ⅣChitin based nano composite articles by inj ection moulding and 3D printing [ J ] . International Journal of Biological Macromolecules ,2020 , 165(7) :3145 - 3155.
[13] YUAN C S , TANG Y , XIE H Q. Application of 3 dimension⁃printed inj ection⁃molded polyether ether ketone lunate prosthesis in the treatment of stage Ⅲ Kienböcks disease: a case report [ J] . World Journal of Clinical Cases , 2022 ,24 :8761 - 8767.
[14] WANG Q , SUN L Y , LI L J. Experimental and numerical investigation on microstructure and mechanical properties of hybridfiber reinforced thermoplastic polymer [ J ] . Polymer Testing, 2018 ,70(7) :215 - 225.
[15] BOROS R , KANNAN P , RAJAMANN J. Combination of 3D printing and inj ection molding: Overmolding and overprinting [ J ] . Express Polymer Letters ,2019 , 13(10) :889 - 897.