何和智1,2,3,高琦1,2,3,张涛4
(1.华南理工大学机械与汽车工程学院,广州510000;2.聚合物成型加工工程教育部重点实验室,广州510000;3.广东省高分子先进制造技术及装备重点实验室,广州510000;4.广东伊之密精密注压科技有限公司,广东佛山528000)
摘要:随着现代生产生活中航天、汽车、国防及医疗等领域对大型注塑制品应用需求的增长,高效、节能、智能的大型注塑机设备及其制造技术迅速发展。本文介绍了现阶段国内外大型注塑机的发展概况,以合模装置为主线总结了大型注塑机在轻量化方向的发展历程,以动力驱动系统为主线介绍了大型注塑机在节能化方向的发展情况,并结合工业4.0的发展环境总结了智能注塑的发展趋势。
关键词:大型注塑机;轻量化;节能化;智能化;发展现状
前言:塑料以其轻质、耐用、易加工等优点,被广泛应用在当代生产生活的国防、航空、输运、建筑、农业、文教及卫生的各个领域。我国塑料制品总产量从1989年的352.3万吨增长到2021年的8003.98万吨,增加了22.72倍,年利润总额现已增长至1295.8亿元,塑料加工行业的发展充满活力[1⁃2]。其中,约83%的塑料制品通过注塑加工成型[3]。作为塑料加工的主要方法之一,注射成型不仅生产效率高、尺寸精确,而且对不同特性的材料表现出较强的适应性[4]。将塑料熔体在高温高压条件下快速注入到成型模具型腔中,冷却后即可获得表面结构复杂的塑件,或中空、薄壁制件及带嵌件的样品。而注射成型所依赖的加工设备——集机械、液压、电动自动化于一体的注塑机,更是被视为现代制造业的“生产母机”,是塑料加工工业中十分重要的基础成型设备之一。各个国家注塑机技术的发展水平与速度能够很大程度上反映出其在机械制造、液压装备和自动化控制等基础工业领域的综合实力[5⁃7]。
注塑机最初是借助金属压铸机原理发展而来的,其诞生最早可追溯到1849年德国STURGISS发明的Celluloid注塑机。1932年德国FRANZ.BRAUN工厂率先打造出第一台全自动柱塞式卧式注塑机。随着螺杆作为聚合物塑化核心部件的大规模使用,1956年世界上首台液压驱动的往复式螺杆注塑机问世,奠定了当代注塑机的基础特征[8]。随后,借助大规模集成电子技术和微处理器系统发展,搭载微机闭环自适应控制功能的高附加值注塑机应运而生。自问世起,中小机型就占据了注塑机研发与应用的绝大部分领域。直到20世纪70年代后期,随着工程塑料在汽车、船舶、宇航、通讯、机械及大型家用电器等方面的广泛应用,大型注塑机才相应迅速发展起来。
1 大型注塑机的国内外发展水平
1.1 大型注塑机的定义
按照额定容量及所需锁模力的大小,注塑机被划分为微型至特型几个级别,见表1。其中,大型注塑机是指额定容量在4000~24000 cm3,且锁模力超过10000 kN的机型。通常,1台大型注塑机主要包括注射系统、合模装置、液压传动系统、电气控制系统等主要功能单元,以及机身、加热冷却装置和加/取料等辅助功能单元[9],如图1所示。
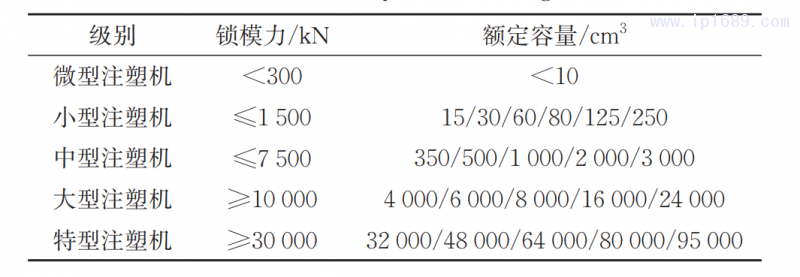
表1不同注塑机级别的划分[10]
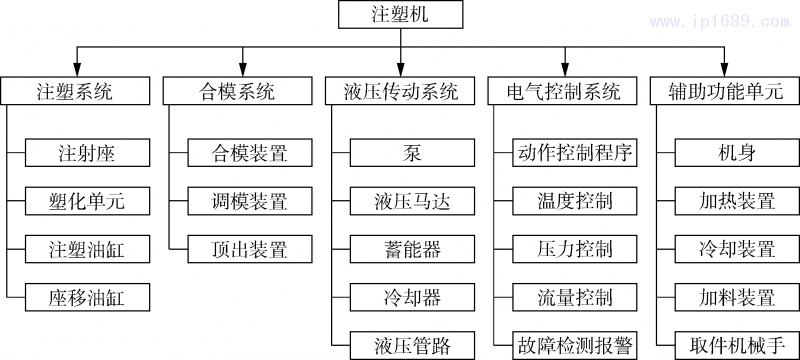
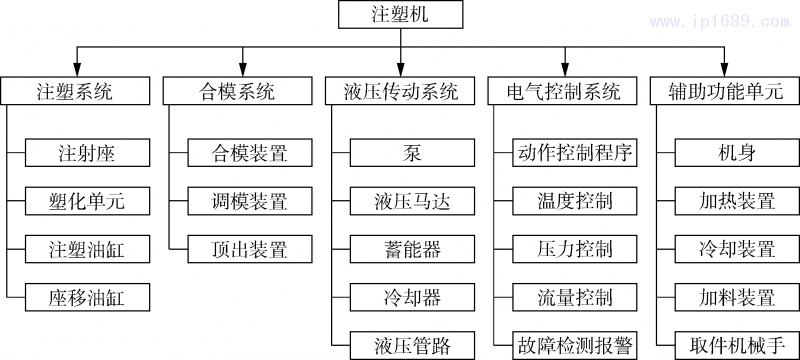
图1注塑机的各组成部分
1.2 大型注塑机的国内外发展趋势
大型注塑机具有物料适应范围广、生产模具更换便捷及生产效率高等独特优势。德国、奥地利和美国等西方国家在大型注塑机生产与研制方面已积累了大量经验,日本名机公司已生产出锁模力达120000 kN,注射量92000g的超大型注塑机[11]。我国注塑机行业的发展起步虽较晚,但已由最初的测绘仿制阶段升级为了自主创新、探索阶段,注塑机企业的发展基本上满足了国内外市场的需求,稳步成长为注塑机制造大国。
香港震雄集团与顺德新力集团合资创办的震德塑料机械厂是国内首批引入卧式加工中心与震雄全套技术的企业,开创了我国注塑机行业向高档、大型变革之先河。海天机械有限公司目前已成为我国最大的塑料机械生产基地,其MARS系列机型(锁模力600~33000kN)的产品畅销全球,JUPITER系列机型(锁模力4500~66000kN)和IAPETUS系列机型(锁模力1200~18500kN)系列产品的开发丰富了我国大型注塑机自行研发的经验与自主创新的能力。2022年,广东伊之密精密机械研制出了我国生产的注塑机中锁模力最大的首台产品,即最大锁模力达90000 kN的超大型注塑机,它不仅在设备吨位上创造了国内之最,还集成了精密微开控制、双射台同步塑化及注射和注射压缩控制等先进技术,对整个大型注塑机行业的技术开发起到引领作用[12]。此外,浙江塑料机械总厂、利源公司以及山东震华塑料机械生产的系列注塑机均具备可靠的加工能力与使用寿命。
目前针对大型注塑机的开发投资成本通常较大,且设备能耗高而控制水平低,因此为了进一步推广与应用,轻量化、节能化和智能化逐渐成为当下大型注塑机的主流改造方向。
2 大型注塑机的轻量化进展
合模装置的类型及性能直接影响着注塑制品的精度、质量以及注塑机的惯性、寿命、效率等。1套性能良好的合模装置须能够提供额定的锁模力,模板具有足够的力学强度、刚度以及平行度,合模响应高效、平稳、噪音小,并能够保持较高的位置精度和重复精度[13⁃14]。
2.1合模装置的分类与特点
目前合模装置的类型繁多,可按照模板数目、驱动力源及传动方式等不同标准进行分类[15]。例如,按照传动方式可分为全机械式、机械连杆式、全液压直压式以及肘杆式(液压机械式)等,如图2所示;按照模板数目可分为二板式和三板式,如图3所示。一般地,三板式合模装置分为三板曲肘式和复合稳压式。三板曲肘式合模装置结构复杂,锁模时肘杆机构的动作误差直接反应在锁模力上,易导致模具弹性变形,形成制品缺陷。日精NS系列注塑机目前仍少量使用闸板稳压式三板合模装置。大型注塑机中三板式合模装置的应用整体较少。
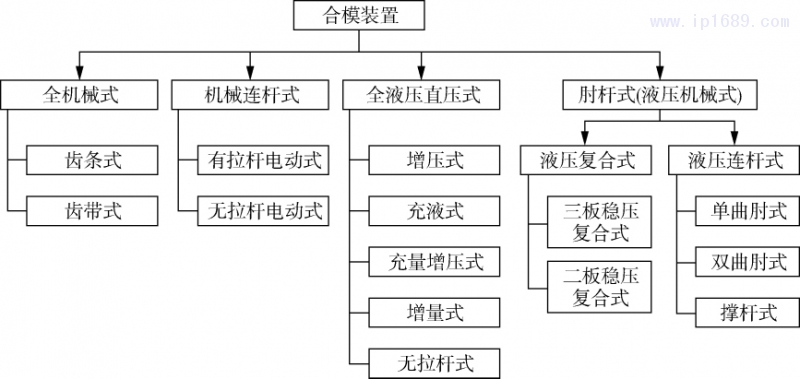
图2 合模装置(按照传动方式分类)
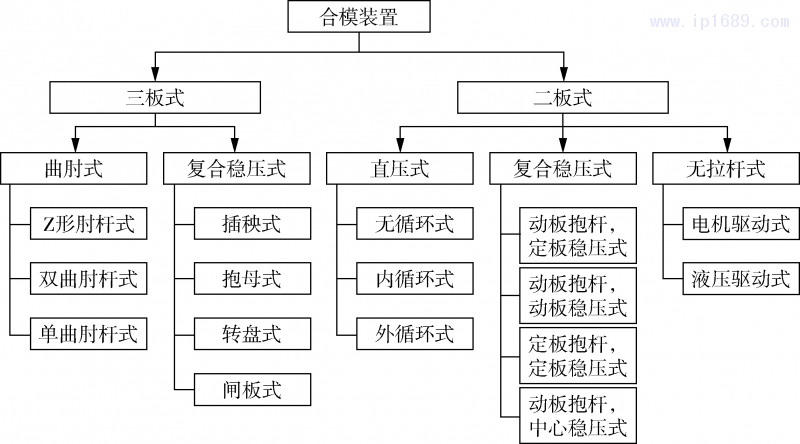
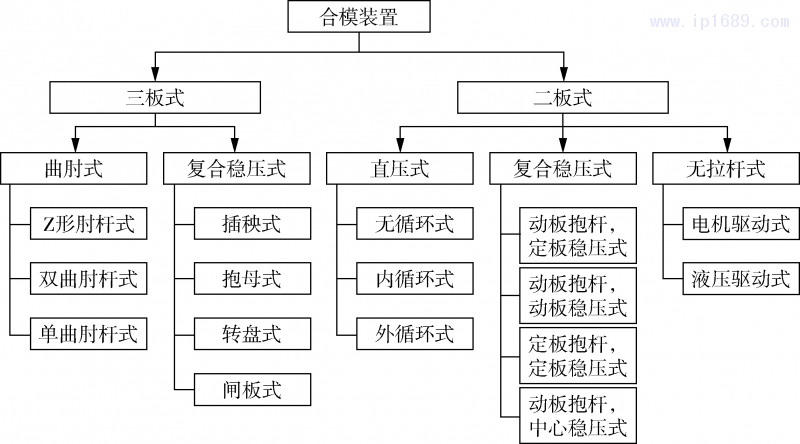
图3 合模装置(按照模板数目分类)
2.2大型注塑机中二板式合模装置的应用
目前绝大多数大型注塑机均采用的是结构简单、锁模精度高、性能稳定可靠且洁净度高的二板式合模装置,其在医疗卫生、食品包装和精密制造等领域已逐渐成为主流应用。
不同于三板式合模装置,二板式合模装置有直压式和复合式2类,在大型注塑机上普遍采用后者[16]。直压式二板合模装置可划分为无循环式、内循环式和外循环式3种,无需机械转换直接高压锁模,其结构如图5所示。而复合式二板合模装置则须通过机械转换二次动作进行锁模,其结构如图6所示。
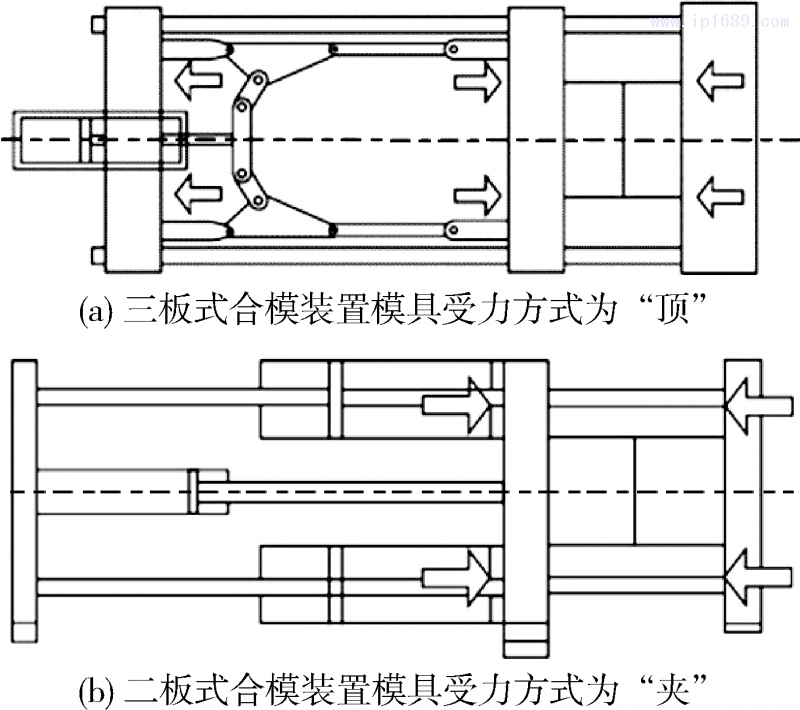
图4合模装置的受力方式示意图[17]
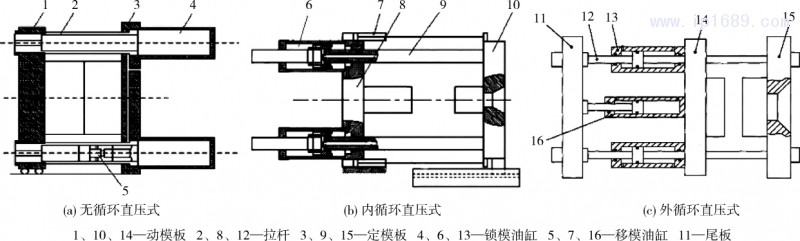
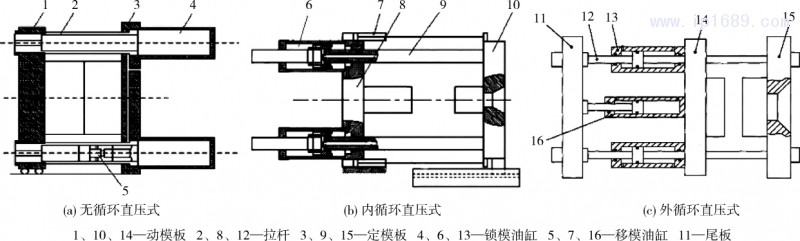
图5直压式二板合模装置[16]
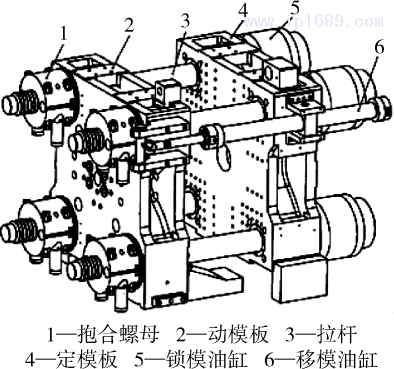
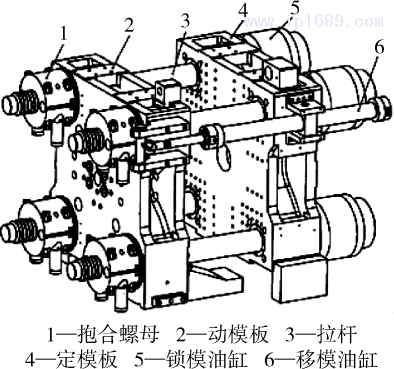
图6复合式二板合模装置[16]
二板式合模装置主要具有以下特点:(1)拉杆无径向载荷,直径加粗且长度大大缩短,整体机构刚性高;(2)结构紧凑,仅约为肘杆式合模机构长度的2/3,制造成本较低;(3)锁模效率高,无二次复合动作,空循环时间短;(4)合模精度高,对各模板或模具之间的平行度误差能自适应调节并消除熔体溢料和胀模时产生的尺寸误差;(5)调模方便,低压模保功能和移模速度控制功能更强;(6)4个液压缸均衡提供锁模力,避免了合模装置受力偏载损坏;(7)合模行程增减操作便捷,通过增减合模缸尺寸及拉杆长度即可实现一机多用;(8)直压式合模装置能够在锁模油缸行程的任意位置建立锁模压力,适合成型深腔制品。搭载了二板式合模装置的大型注塑机,生产周期大大缩短,关键零件受力均匀,设备灵活易操控,整机减重可达20%,机身总长减少约25%,容模量同比增长可超过10%[18]。上述这些综合性特点使得二板式合模装置在大型、超大型注塑机领域具备得天独厚的开发潜力。
首先研发推出大型二板式注塑机的主要是欧洲及日本企业[19],如克劳斯玛菲的MC系列机型(锁模力为400~40000 kN),宇部兴产的大型注塑机(锁模力为20000~40000 kN)以及意大利MIR公司的Compact系列机型(锁模力为11000~60000 kN)。
我国二板式注塑机的制造已逐渐发展成以海天机械、伊之密、博创、东华、泰瑞、震雄等在内的企业群体规模,可媲美国际领先水平的同类机型。2016年伊之密已自主研发出最大锁模力超过40000kN而循环周期不超过8s的高效节能大型二板式注塑机,其注塑制品的重复精度误差不超过±3‰,且设备的一级能耗低于0.4kW·h/kg[20]。这台大型注塑机搭载的内循环二板式合模装置,其4个锁模油缸进出油口相互连通,锁模时各缸活塞两侧的压力能保持一致,大大提高了制品的合格率。上述由广东伊之密精密机械最新研制的里程碑式8500吨超大型注塑机产品如图7所示。与国内外同类型产品相比,这台产品的开合模定位精度达到了0.3 mm,搭配了射出重量超过80kg的注射系统,能够一次性成型外形复杂、透光率高、尺寸精确、质地紧密且可带有金属嵌件的超大型透明塑料零件,不仅解决了国内超大型透明塑件的成型难题,也创下了国内超大型精密注塑机的纪录。这台超大型二板式注塑机的诞生实现了我国大型注塑机制造的关键技术突破,在全球同行中也处于领先地位。至此,我国注塑机制造厂商已研发并稳定制备了锁模力为4500~85000 kN的高性价比系列机型。
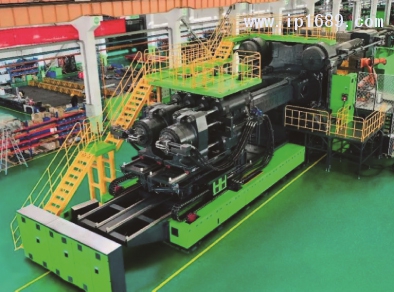
图7 伊之密公司生产的DP8500超大型二板式注塑机[12]
2.3大型注塑机中无拉杆合模装置的应用
不同于其他类型的合模装置,无拉杆合模装置采用无拉杆结构,降低了应力分布,容模空间大,模板面积利用率高,锁模力大小易于调节,模板平行度保持良好,模板形变大大降低[21]。恩格尔公司率先推出了名为“e⁃motion”的首台无拉杆电动注塑机(锁模力分别有600、1100、1650 kN)标志着无拉杆合模装置的发展。在FTP 2014展会上该公司继续推出了为无尘室设计的无拉杆ENGEL e⁃victory 160 combi型油电混合注塑机,展示出了无拉杆合模装置大幅提高生产效率的独特优势,如图8所示。目前无拉杆式注塑机已从中型吨位向大型吨位领域发展。
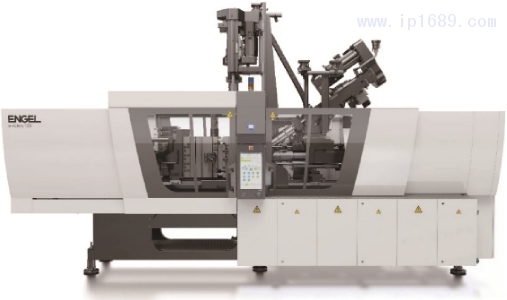
图8 恩格尔公司生产的搭载无拉杆式合模装置的注塑机
3 大型注塑机的节能化进展
注射成型装备的节能化,即节能降耗,是对二板式注塑机与全电动注塑机的探索。以锁模力40000 kN的注塑机为例,机器长度缩短25%~30%,整机重量减轻500 kN,堪称符合国家产业政策的节能型注塑机典范[22]。
3.1大型注塑机的全电动化研究
作为新型注塑机的全电动注塑机表现出杰出的节能性[23]。不同于使用液压油和液压元件作为驱动力来源的液压注塑机,全电动注塑机利用永磁式或感应式交流伺服电机作动力源,驱动滚珠丝杠副、齿形带以及齿轮等机械元件以实现注射、塑化及合模等各个功能装置单元的精密配合运动。
相比于液压式注塑机,全电动注塑机更加节省能源、清洁环保,不仅能够将注塑循环中的减速运动阶段释放的能量转化为电能再次利用,还可以避免液压注塑机中普遍存在的液压油泄露和污染问题。基于伺服电机的速度控制范围宽、响应性好,通过料量微调能够使得最终制品尺寸满足公差要求,生产成本低、效率高,制品精度与重复性好。如生产LED灯罩,全电动注塑机可比同类型的伺服液压注塑机节能43%~65%[24]。全电动注塑机与液压注塑机的性能对比见表2。
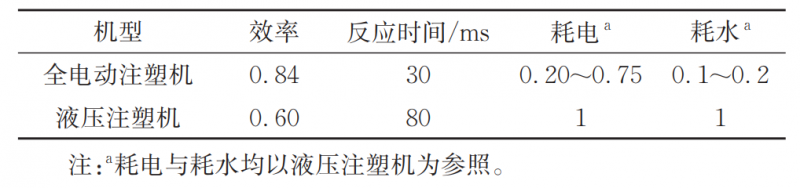
表2 全电动注塑机与液压注塑机的性能对比[24]
目前全电动注塑机在国际市场上的占有率大幅提升,日本企业主要发展以精密注射与高循环速度(短循环周期)技术为主的全电动注塑机,欧美企业则致力于研发液压计量与电动组合的混合式机型。我国对于全电动式注塑机的研究仍处于初级阶段。
如何实现全电动注塑机的大型化是注塑机节能发展的1个关键课题。整体而言,目前大型全电动注塑机的发展较缓慢。若要在全电动注塑机中实现较高的锁模力,合模装置的丝杆与电机负荷均需相应增大,1个电机无法满足需要,往往需要2个电机来共同完成。这就要求2个工作电机之间实现高度同步,即2个电机的启动、运转、停止必须一致,否则将导致机器运行不稳定与部件损坏。因此针对双电机的同步控制理论仍需发展完善。郭小龙等[25]基于现有伺服电机驱动技术,提出了双电机复合驱动注射系统的设计方案,如图9所示。虽然双伺服电机能够顺利完成指定的加、减速运动,保持良好的信号跟随性能,但其工作状态仍存在拉扯导致同步性能下降的现象。周长攀[26]通过对双三相永磁同步电机进行数学建模、谐波电流抑制及容错控制等方法进行深入的理论研究,为双电机驱动提供充足的理论支撑。李方俊等[27]针对大惯量运动平台刚度不足,无法实现系统快速运行与稳定控制之间平衡的问题,研究并提出了基于速度曲线规划的双电机同步消隙控制策略,有效抑制了大惯性挠性结构的快速运行抖动问题,为大惯量运动平台的快速稳定控制提供依据。此外,由于电机控制系统、大功率电机定制、装配工艺及工作惯性等对成型精度和工艺重复性的干扰,大型全电动注塑机的研究成本高,其节能优势反而降低。相较于产品系列已覆盖了从微型机型到锁模力超过80000 kN机型的液压注塑机而言,目前投入商业化应用的全电动注塑机的锁模力较小,一般均在10000 kN以下。
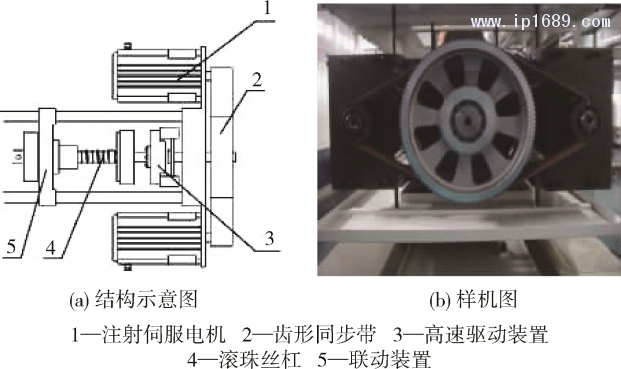
图9 双电机驱动结构[25]
日本的宇部兴产率先突破了机型的限制,造出了首台锁模力可达20000 kN的全电动成型机[28]。该设备用1台交流伺服电机驱动塑化,2台电机驱动肘杆锁紧,3台电机驱动注射,以及1台电机驱动顶出。随后,三菱重工研制出了世界首台30000 kN锁模力的大型化电动注塑机[29],实现了世界上最快的大型塑料零件(如汽车保险杠)高循环生产,如图10所示。该大型设备搭载了三菱重工特有的二板式合模结构及混合电力系统,并且它所配备的中心压板能够利用电气控制模具内的压力波形,因此具有空间占用率低,生产节能化程度高,制品飞边与毛刺少以及运行成本低的优势。
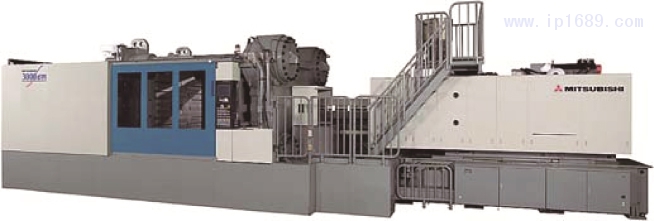
图10 日本三菱重工公司研制的30000 kN锁模力大型全电动注塑机[29]
全电动塑机目前以智能化和超高速化作为发展的新方向。除了设备单元自动控制、参数闭环控制、过程联运在线反馈控制等电子计算机技术,基于控制计算机设备(PC)的开放式、模块化控制技术越来越被各大制造商青睐[30]。同时,虚拟实现技术的高速发展也为注塑机生产厂家实行虚拟合作设计与制造提供了空间环境,蕴藏着巨大的经济效益[31]。虽然全电动注塑机市场发展迅速,但是国内全电动注塑机的主要配件(如伺服电机、滚珠丝杠等)与核心技术(如专用控制系统等)均依赖进口,再加上与欧美日相近甚至更高的零件成本,国内全电动注塑机的自主研发及其大型化技术仍亟待探索。
3.2 大型注塑机中节能液压系统的应用
注塑机节能的重点是提高驱动系统的能耗效率,即驱动系统输出功率与执行机构动作功率实现自适应调节,二者之间的能量利用率越高,系统越节能。在传统的液压式注塑机中,液压系统的能耗可高达加工耗能的70%,因此如何合理设计与选配液压系统是注塑机节能化的又一关键课题。由于注塑机在工作循环中大部分处于部分负载或待机状态,若能实现液压系统对压力与流量的快速响应和灵活调控将能有效促进注塑机的节能化发展。目前,广泛应用于注塑机的液压系统按照不同的控制实现方式可划分为4种类型,其组成及特点详见表3。显然,组合使用定量泵和变量泵能够同时兼顾成本和节能的要求。
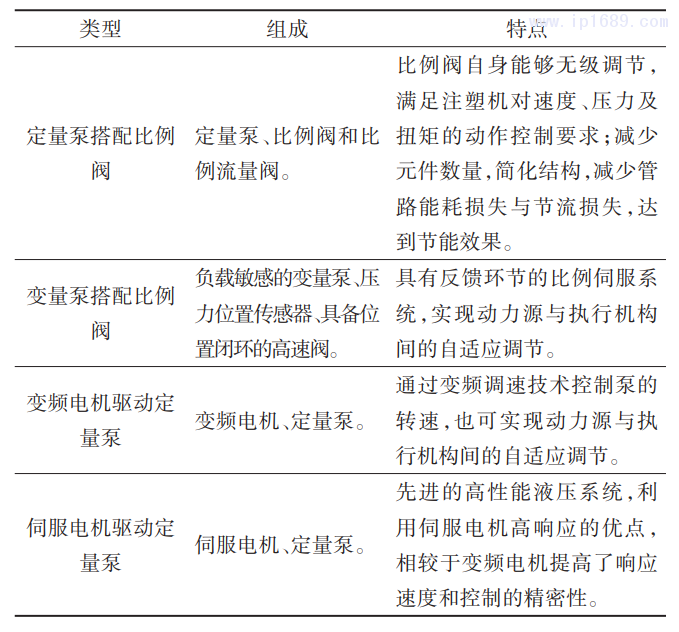
表3 不同类型液压系统的组成及特点[32⁃39]
液压系统从过去利用流量和压力比例控制的原理发展到利用上述的变量或定量控制、变频调速以及伺服控制技术,整机能耗降低到传统机型的仅30%。采用变频伺服技术的注塑机,能耗仅为传统机型的50%。工作节奏加快,制品周期缩短,生产效率普遍提高超过24%。我国的海天机械目前已成功研发了搭载第三代技术平台ZE2300F⁃830h的集成伺服液压驱动系统的节能型电动注塑设备,如图11所示[40]。液压元件集成化、机电液一体化、控制系统自动化与智能化、环保清洁、密封良好等特性将成为注塑机液压系统节能技术的发展目标。
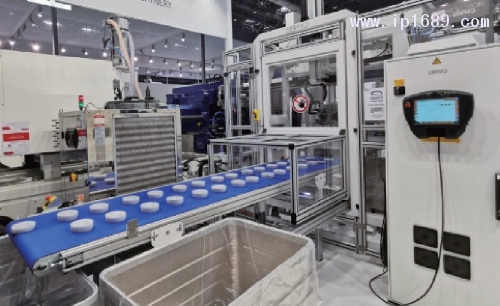
图11 海天公司研制的第三代全电动注塑机生产单元[40]
4 大型注塑机的智能化进展
自60年代末美国费洛斯公司首先应用计算机控制技术开始,注塑机的控制技术高速发展,目前已经形成了包括熔体温度、注射压力、注射速度、保压时间、冷却过程及液压回路参数等的多因素集成微处理器控制系统。智能化俨然成为注塑机控制技术发展的必然追求。
智能化表现在多个方面:(1)高精度化。注塑机的控制系统需实现对温度、压力、流量以及位置的高精度闭环控制,以满足对精密产品生产过程参数的严格控制。现阶段半闭环的位置控制已在国内使用,而全闭环控制器仍需进口。(2)全自动化。人工智能理论与实践的丰富能够实现注塑生产过程的柔性化和自动化,降低操作的人力成本,提高管理的自动化与信息化程度,同时配备辅助性功能部件,如自动加料机和国外比较广泛使用的取件机械手等,能够基本实现注塑过程的全自动化。(3)网络化。通过网络来实现单台注塑机的在线诊断、下载升级等功能,或多台注塑机的集中控制、程序调用等功能,能够保障生产计划的及时调度安排与反馈,也大大节省了人力成本。(4)一体化与复合化。所谓一体化,是指将从加入原料到取出制品之间的所有工序尽可能安排在同一系统中协调完成。而复合化是指1台注塑机在进行简单调整后能够满足多种加工需求,减少设备调换产生的浪费与误差,提高控制精度和生产效率,缩短注塑工期。
在物联网、大数据、云制造发展背景下,注塑行业智能化发展日益丰富。在2014年举行的塑胶展上,威猛巴顿菲尔企业以“走向智能化”为主旨,通过Smart Power注塑机呈现了智能注塑与现代工艺之间的协作生产[41]。欧洲塑料与橡胶机械制造商协会提出了1种面向工业4.0的新工业规范EUROMAP77,帮助注塑机与计算机或工厂的制造执行系统(MES)进行数据交换。恩格尔公司从智能机器、智能生产和智能服务3个层面开发了“Inject 4.0”智能成型方案,如图12所示[42]。阿博格公司展现了多种工业4.0的应用新方式,在2016年利用空间分割技术制造了个性化的“智能”行李箱标牌,即把客户的个人信息与从云端获取的制造过程信息同步写入近场通信(NFC)芯片,再对标牌激光加工。2019年其又提出了增强现实(AR)辅助售后功能,如图13所示。
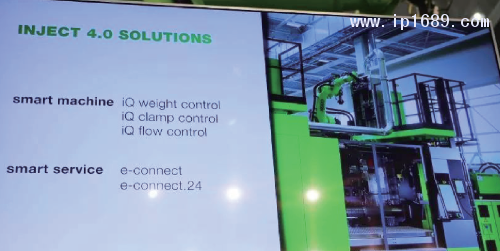
图12 恩格尔公司展示的“Inject4.0”智能成型方案[42]
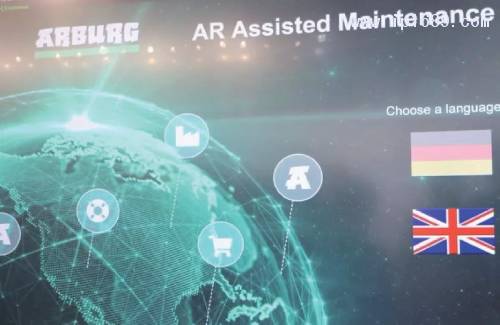
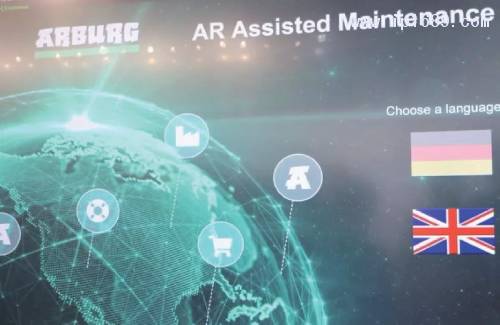
图13 阿博格公司提出的AR辅助售后功能[42]
我国伊之密公司基于其精密的I⁃factory4.0技术,推出了搭载SmartClamp智能锁模系统的UN500DP两板式注塑机,同时集成了聚氨酯(PUR)设备和InPUR“1+2”模具技术,实现了一步法成型带局部高光表面的汽车发动机盖板零件,如图14所示。海天机械为每一台注塑机安装了用于搭建注塑智能系统的智能化模块,同步采集注塑生产车间内机器的信息后汇聚到网关并传送到云端,以此搭建注塑云平台。泰瑞机械自主研发了基于Linux系统的多协议多功能控制平台,同时使用分流集流阀简化了抱闸液压机构的液压油回路,打造了基于纯二板注塑机的智能化升级产品。博创公司的工业4.0主要以其新一代大型二板智能注塑机BU900⁃II为主体,强调交钥匙与智能化方案,采用了国内首创的电动熔胶新技术,搭配横走式机械手、视觉检测、自动称重以及输送等功能性辅助模块,助力生产线智能化,如图15所示。力劲公司研发出1套节能表现优异的二板式注塑生产系统,集成了当前先进的伺服节能技术、单缸射胶技术、强力锁模技术、模具保护技术以及大数据存储分析功能,在生产大型垃圾桶、水桶等深腔容器类产品中表现优异,其产品如图16所示。震雄公司的iChen4.0系统则主要关注制造流程中的监视、管理与智能化服务等。
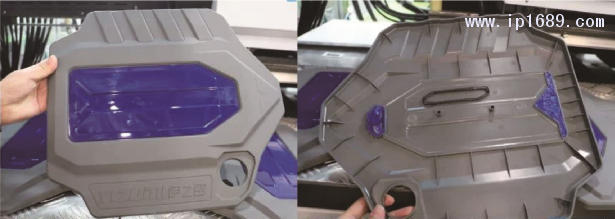
图14 伊之密公司研制的UN500DP两板式注塑机成型汽车发动机盖板[40]
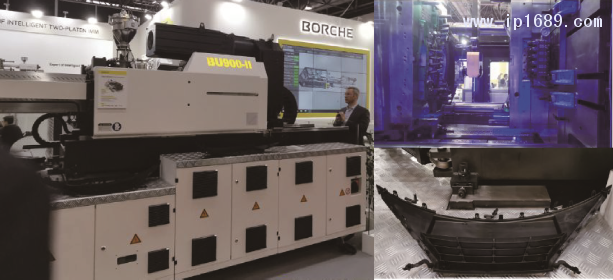
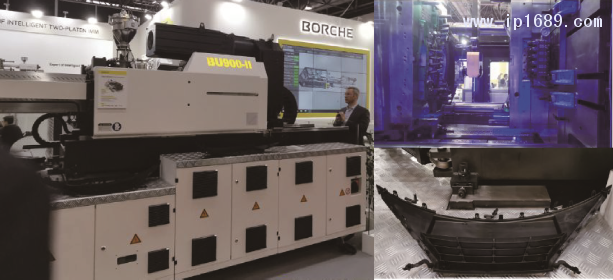
图15 博创公司提出的注塑系统智能交钥匙解决方案[40]
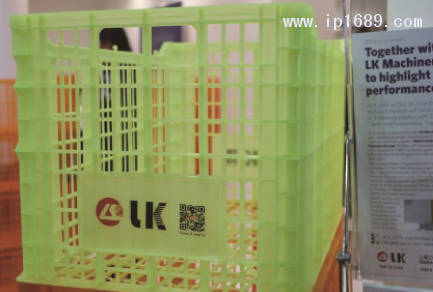
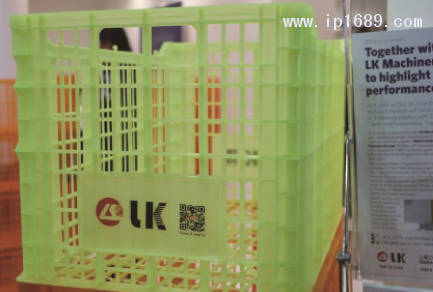
图16 力劲公司生产的大型深腔容器产品[40]
广东工业大学[43]提出了1种基于云制造的区块链技术,为系统提供在不信任环境中的安全性标准与协议,使存储在私有云中的注塑模具设计制造知识得以安全共享,对于模具的再设计具有重要的现实意义。德国亚琛工业大学[44]利用计算机断层扫描技术实现了注塑模具的自动校正,通过网络实现CAD模型与点云的数据交换,同样丰富了工业4.0的发展。
整体而言,可靠的网络控制平台、高精度的硬件配置与合理的软件控制方案是实现注塑过程优化的必要元素,注塑控制系统正朝着高精度化、高可靠性、信息交互网络化、一体化、复合化与开放化的智能化控制迈进[30]。将来的注塑工厂应当是设备、制造与服务多位一体的智能化注塑。
5 结语
大型注塑机作为当代国际高端注塑机型而备受各大制造商青睐,其主流发展趋势主要集中在轻量化、节能化与智能化3个方面。轻量化主要通过采用二板式合模结构或无拉杆合模结构以简化设备,节省空间,提高生产效率;节能化方面的发展一边致力于突破全电动注塑机大型化的瓶颈,尤其需要克服双电机驱动的同步性问题,另一边则针对目前市场占比高的液压式注塑机,降低整机能耗中占比最高的液压系统的能耗以满足节能化需求;随着工业4.0的发展与电子信息技术不断升级,注塑机控制系统日益更迭,智能化注塑已成为了各种类型注塑机集成化管理与改进的新方向。
参考文献:
[1]塑料加工业确立“三化一微+智能化”绿色发展新方向[J].塑料科技,2019,47(10):122.
[2]马占峰,牛国强,芦珊.中国塑料加工业(2021)[J].中国塑料,2022,36(6):7.
[3]中国塑料加工工业协会.中国塑料工业年鉴[M].北京:中国轻工业出版社,2021.
[4]徐柯.注塑机模板的有限元分析及优化设计[D].北京:北京化工大学,2009.
[5]杨卫民.高分子材料先进制造的微积分思想[J].中国塑料,2010,24(7):1-6.
[6]PunK-F,HuiI-K,Lewis W G,et al.A multiple-criteria environmental impact assessment for the plastic injection molding process:a methodology[J].Journal of Cleaner Production,2003,11(1):41-49.
[7]王兴天.国内注塑机发展概述[J].塑料科技,2000,2:28.
[8]北京化工大学.塑料机械设计:第二版[M].北京:中国轻工业出版社,1995.
[9]陈世煌.塑料成型机械[M].北京:化学工业出版社,2006.
[10]唐志玉.大型注塑模具设计技术原理与应用[M].化学工业出版社,2004.
[11]赵延召.高精密注塑机合模机构的有限元分析与拓扑优化[D].南昌:华东交通大学,2012.
[12]广东伊之密精密机械股份有限公司.8500吨超大型高精度注塑成型机[EB/OL].2022⁃02⁃24.https://content.foshanplus.com/newsDetails.html?newsId=673997&memberId=212264.
[13]赵攀峰.二板式全液压型注塑机关键技术研究[D].杭州:浙江大学,2012.
[14]刘晓彬.1300KN全电动注塑机合模机构设计及其优化分析[D].北京:北京化工大学,2016.
[15]尹辉,陆国栋,王进,等.注塑机合模机构分析及其发展趋势[J].中国塑料,2009,23(11):1⁃6.
[16]高世权,韩志忠,谢鹏程,等.大型二板式注塑机技术发展浅论[J].塑料,2016,45(4):73⁃76,80.
[17]冯刚,江平.二板式注塑机的特点研究及发展新动向[J].塑料工业,2011,1:5.
[18]焦志伟,谢鹏程,严志云,等.全液压内循环二板式注塑机[J].橡塑技术与装备,2010,1:4.
[19]Kelly A,Woodhead M,Coates P J P E,et al.Compari⁃son of injection molding machine performance[J].Poly⁃mer Engineering & Science,2005,45(6):857⁃865.
[20]侯永平.智能数字化大型二板式注射成型机[Z].江苏省,伊之密精密机械,2016⁃12⁃01.
[21]刘泽宇,张志洪.注塑成型技术进展[J].塑料制造,2009,4:3.
[22]焦志伟.内循环二板式精密注塑机关键技术的研究[D].北京:北京化工大学,2012.
[23]胡静.新型全电动注塑机合模机构的设计及性能分析[D].北京:北京化工大学,2011.
[24]叶巴丁,陆晨风,储能奎,等.全电动注塑机研究进展及在汽配电子行业中的应用[J].中国塑料,2020,34(10):6.
[25]郭小龙,陈邦锋,傅南红,等.双电机驱动在全电动注塑机中的应用[J].塑料,2013,42(5):3.
[26]周长攀.双三相永磁同步电机驱动及容错控制技术研究[D].哈尔滨:哈尔滨工业大学,2016.
[27]李方俊,王生捷,李俊峰,等.车载大惯量运动平台双电机驱动控制策略[J].兵工学报,2022,5:1⁃11.
[28]张友根.功能化注塑机的科学发展研究及自主创新[J].橡塑技术与装备,2015,41(16):10⁃33.
[29]Matsuo S,Bessho M,Kato N,et al.World’sfirst 3,000 ton mold clamping force electric injection molding machine[J].Technical Review,2006,43(3):1⁃6.
[30]张友根.注塑设备智能化的研究(上)[J].橡塑技术与装备,2013,39(9):13⁃19.
[31]金波,宁德胜,许明,等.注塑机控制系统的现状及发展趋势[J].液压气动与密封,2006,1:4.
[32]刘海丽.基于AMESim的液压系统建模与仿真技术研究[D].西安:西北工业大学,2006.
[33]吴根茂.新编实用电液比例技术[M].浙江大学出版社,2006.
[34]张弓,于兰英,吴文海,等.电液比例阀的研究综述[J].流体传动与控制,2008,6:5.
[35]黄新年,张志生,陈忠强.负载敏感技术在液压系统中的应用[J].流体传动与控制,2007,5:31⁃33.
[36]张友根.注塑机节能技术的分析研究(上)[J].橡塑技术与装备,2008,3:52⁃60.
[37]张友根.注塑机节能技术的分析研究(下)[J].橡塑技术与装备,2008,34(4):9.
[38]马俊彪.伺服电机液压单元在微发泡注塑机上的应用[J].黑龙江科技信息,2008,26:8.
[39]Wang Y.The investigation of hydraulic servo system de⁃sign for high⁃speed injection molding[D].Jhongli,Tai⁃wan:MS thesis,Chung Yuan University,2001.
[40]艾邦团队.2019年德国K展总结二:中国展商风采[EB/OL].2019⁃11⁃04.https://mp.weixin.qq.com/s/1M7EUk1j7Czd6buD34jIrw.
[41]新型注塑机走向智能化[J].塑料制造,2014,(11):1.
[42]艾邦团队.2019年德国K展总结精华版[EB/OL].2019⁃11⁃01.https://mp.weixin.qq.com/s/W0sX9FFAX9qxTTwlrCigvQ.
[43]Li Z,Liu L,Barenji A V,et al.Cloud⁃based manufactu⁃ring blockchain:Secure knowledge sharing for injection mould redesign[J].Procedia CIRP,2018,72:961⁃966.
[44]Richter Katharina P M,Schmitt Robert H. Use the com⁃puted tomography for the automatic tool correction of the mould injection process[C]//European Society for Preci⁃sion Engineering and Nanotechnology,Conference Pro⁃ceedings⁃19th International Conference and Exhibition.Bilbao:EUSPEN,2019:352⁃355.