引言
注塑机具有能一次成型外型复杂、尺寸精确或带有金属嵌件的质地密致的塑料制品,被广泛应用于国防、机电、汽车、交通、建材、包装、农业及日常生活各个领域。注射机二板合模装置作为20世纪90年代欧洲推出的革新性结构,相比曲肘式锁模结构,具有容量大、受力理想、结构刚性好、占空间小等特点,使其在大型、超大型领域具有得天独厚的优势。
在国内,大型二板注塑机技术较为落后,设备市场竞争力稍显薄弱,主要体现在合模系统工作的适应性和稳定性,设备运行的节能环保以及液压控制系统的高效调控等方面。国内规模以上注射机生产厂商主要集中在浙江,如宁波海天、宁波海达、泰瑞机器(杭州)等。近几年,相关注塑机厂商与研究机构合作,围绕二板注射机合模机构,在优化设计[1-4]、抱闸设计[5]、性能评价[6-8]、液压控制[9-10]等方面进行了大量研究,取得了很多成果。
由于合模机构涉及装配零件较多,影响复杂,工作时的实际受力状态难以简单计算,导致合模机构锁模寿命无法准确预测,进而严重影响了合模机构可靠性评价和判断。本文正是针对以上技术难题,借助有限元数值计算方法,对合模机构进行多体力学有限元建模和分析,明确其锁模时各部件的应力和变形情况,为下一步研究打下基础。
1.二板式注射机合模机构
二板合模机构有几种形式,原理基本一致。图1所示为一典型二板复合式合模机构,主要由定模板、动模板、锁模油缸、拉杆、抱闸、闸板驱动油缸、移模油缸组成。合模动作过程:首先移模油缸驱动动模板沿拉杆移动,直至模具闭合;闸板驱动油缸驱动抱闸两半闸板闭合,抱紧拉杆末端螺纹;锁模油缸驱动拉杆相对于定模板运动,锁紧模具。
泰瑞机器股份有限公司研究开发了大型二板注射机产品,如图2所示。采用挤注式注塑系统、二板直压式合模系统、节能的伺服电机定量泵液压系统技术。但是,考虑到水平装模和加工装配工艺性,动模板孔与拉杆间隙配合,无滑动支撑作用。动模板后方的抱闸两半合闭时,抱紧拉杆。
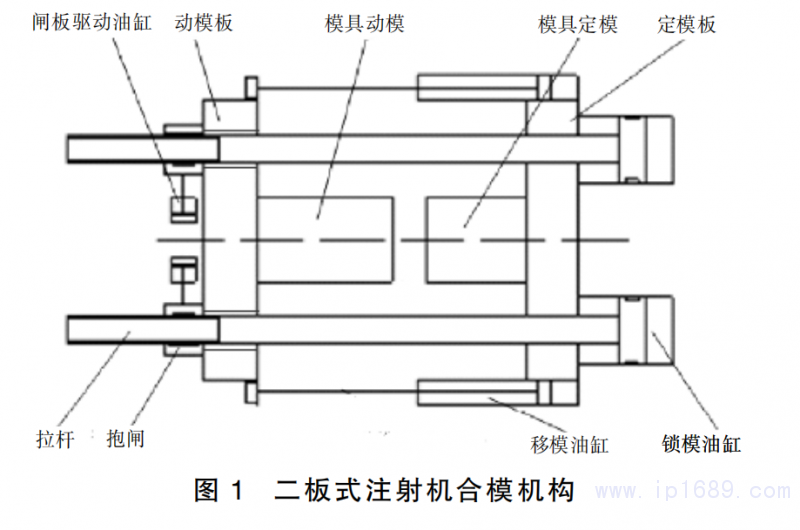
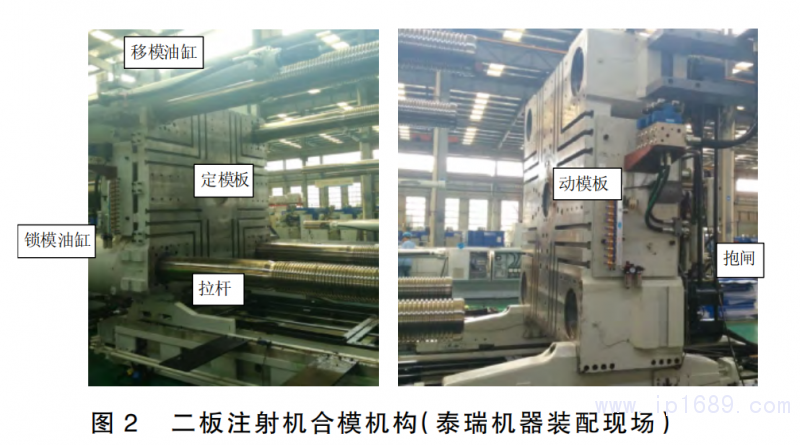
2.有限元模型
2.1几何模型
本文以泰瑞1700吨二板注射机合模机构为例进行分析。其关键外形尺寸见表1。
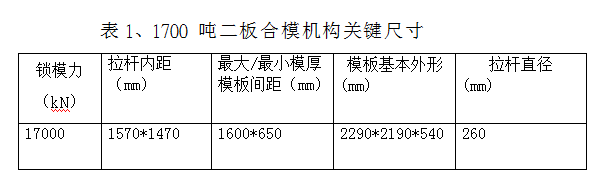
由于大型二板式合模机构整体结构非常复杂,为了使分析更加简洁又不失真,现对关键零部件作必要假设和简化。去除零件中圆角、螺纹、台阶、螺纹孔等细节,去除了调模装置和顶出机构。根据表1中基本尺寸,利用Solidworks三维软件对定模板、动模板、拉杆等进行三维建模,并进行装配,两模板间距取1000mm,如图3所示。将零部件保存为.igs格式文件,导入ABAQUS有限元软件,作为数值模拟的几何模型。
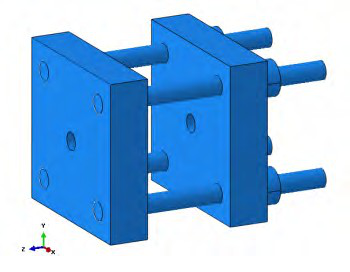
图3.简化几何模型
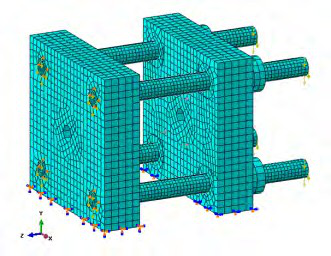
图4有限元模型
2.2材料参数及网格划分
若进行受力分析,需给定零件模型相应的物理力学参数。由于此处模板、拉杆在受力状态下只产生弹性变形,所以不需要塑性应力应变数据。此外,拉杆可能会由于悬臂状态产生自重下垂变形,故这里将给定密度值。几种零件的性能参数如表2所示。
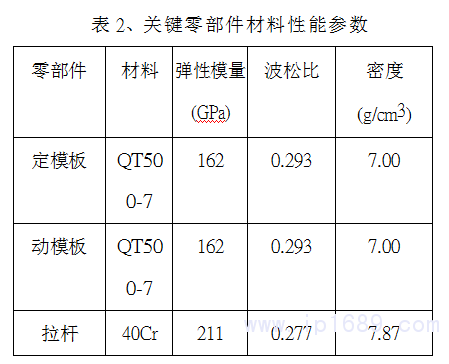
合模机构三维几何建模较为复杂,在Abaqus中选取C3D8R减缩实体单元为划分网格的单元类型,可提高计算速度。综合考虑到模型三维尺寸大小和模拟计算精度,模板选择网格大小为100mm,拉杆网格大小为50mm。有限元模型网格划分情况如图4所示。
2.3边界条件和载荷
设置定义各零件之间的接触条件。拉杆通过铜质精密滑动轴承安装于定模板孔中,两者之间摩擦较小,忽略其大小,摩擦系数取为0。抱闸安装于动模板背面,将抱闸装置与动模板简化为同一结构体,拉杆与抱闸接触处施加“绑定”(Tie)约束条件,使其具有相同的轴向行为。
考虑到二板合模机构受力复杂,这里突出关键因素,忽略次要因素(如模板的温度),对模型施加必要的边界约束和载荷,如图4所示,具体如下:
(a)定模板固定在床身上,底部固定处可作为完全约束处理;
(b)动模板在轴向可沿导轨上滑动,在竖直方向存在位移约束;
(c)为了模拟锁模油缸工作时的情况,在拉杆靠近前模板的端面上施加轴向位移约束;
(d)假设模具和模板安装面积为1000mm*1000mm,锁模力为17000KN,在定模板和动模板安装面积上分别加载均布载荷17MPa的压强;
(e)对四根拉杆施加重力载荷,在y方向上添加重力加速度-9800mm/S2。
最后,建立Step-1分析步,进行有限元模拟计算。
3.模拟结果与分析
3.1.变形分析
在考虑拉杆重力的情况下,二板合模机构的变形分布图如图5所示。由图可见,合模机构的最大变形量为0.994mm,发生在定模板的顶部内侧。这是因为定模板底部完全定位受限,动模板和连杆是固联的,在定动模板受到模具处的压力时,定模板变形特别是上部变形最大。
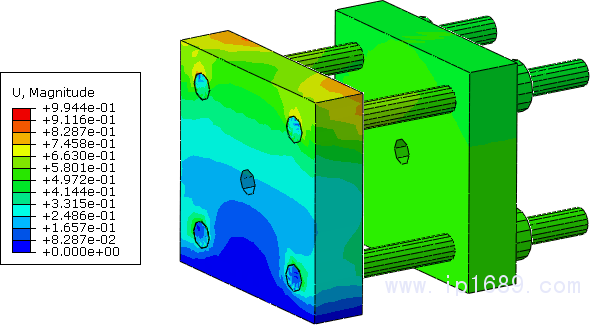
图5.合模机构变形分布图
此外,定模板上与拉杆的配合连接处,相比于周围,孔边出现了较大的变形量。上面两孔最大变形在0.8mm,下面两孔最大变形在0.5mm,这是因为拉杆与孔有相互力的作用。动模板的变形情况比较均匀。
3.2.应力分析
图6为合模机构的应力分布图。最大应力为211MPa,发生在拉杆上,集中于拉杆与前模板的连接处。根据拉杆材料强度,该应力值不足以使拉杆发生塑性变形和破坏,所以合模机构是安全的。但是,当合模机构在频繁的进行合模锁模注塑动作时,拉杆将成为最有可能发生疲劳破坏的部件。
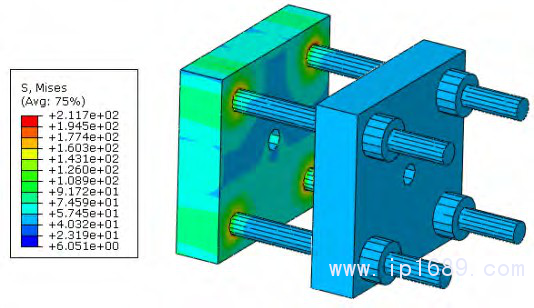
图6.合模机构应力云图
根据以上合模机构变形和应力分析,前模板在前端面设计连接时可以适当加强。另外,可考虑改善拉杆与前模板的连接配合方案,以减小应力集中。
4.结语
对合模机构的零部件进行适当简化,根据其工作原理,建立了有限元模型;通过有限元模拟分析发现,最大变形发生在定模板顶部,集中应力发生在拉杆与定模板孔连接处;该模拟分析结果,为进一步优化设计提供依据,也为合模机构的寿命预测的打下基础。