塑胶的粘度及条件对粘度的影响
熔融塑料流动时大分子之间相互摩擦的性质称为塑料的粘性。而把这种粘性大小的系数称为粘度,所以粘度是熔融塑料流动性高低的反映。粘度越大,熔体粘性越强,流动性越差,加工越困难。
工业应用上,比较一种塑料的流动性并不是看其粘度值,而是看其熔体流动指数大小(称MFI):所谓MFI,就是在一定熔化温度下,熔体受到额定的压力作用下,单位时间内(一般为10分钟)通过标准口模的熔体重量。以g/10min表示,如注塑级的PP料,牌号不同,MFI的值可以从2.5~30间变化,塑料的粘度并非一成不变,塑料本身特性的变化,外界温度,压力等条件的影响,都可促成粘度的变化。
1. 分子量的影响
分子量越大,分子量分布越窄,反映出来的粘度愈大。
2. 低分子添加济的影响
低分子添加济可以降低大分子连之间的作用力。因而使粘度减小,有些塑料成型时间加入溶济或增塑 剂就是为了降低粘度,使之易于模成型。
3. 温度粘度的影响
温度对大多数熔融塑料的粘度影响是很大的,一般温度升高,反映出来的粘度越低,但各种塑料熔体粘度降低的幅度大小有出入:
PE/PP类塑料,升高温度对提高流动性,降低熔体粘度作用很小,温度过高,消耗加大,反而得不偿失
PMMA/PC/PA类等塑料,温度升高粘度就显著下降,PS ABS升高温度对于降低粘度于成型亦有较大好处
4. 剪切速度的影响
有效的增加塑料的剪切速度可使塑料粘度下降,但有部分塑料,如PC亦有例外,其粘度几乎不受螺杆转速的影响。
5. 压力的影响
压力对粘度的影响比较复杂,一般PP&PE类粘度受压力的影响不是很大,但对PS的影响却相当显著,实际生产中,在设备较完善的机器上,应注意发挥高速注射,即高剪切速度的作用,而不应盲目地将压力提高。
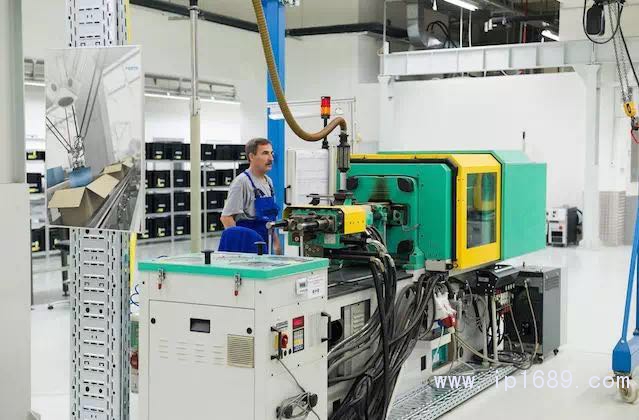
注射温度的控制对成型加工的影响
所谓炮筒温度的控制是指塑料在料筒内如何从原料颗料一直均匀地被加热为塑性的粘流体,也就是料筒烤温如何配置的问题。
1. 料筒温度的调节
应保证塑料塑化良好,能顺利注射充模又不引起分解。
这就要求我们不能因受制于塑胶对温度的敏感性而有意识地降低塑化温度,用注塑压力或注射速度等办法强行充模。
2. 塑料熔融温度
主要影响加工性能,同时也影响表面质量和色泽。
3. 料温的控制
与制件模具有关,大而简单的制件,制件重量与注射量较接近的,需用较高的烤温,薄壁。形状复杂的也要用高烤温。
反之,对于厚壁制件,某些需要附加操作的,如装嵌件的,可以使用低的烤温,鉴别塑料溶体温度是否得宜可以用点动动作在低压速下对空注射观察,适宜的料温应使喷出来的料刚劲有力,不带泡,不卷曲,光亮连续。
4. 料温
一般都是从进料段到出料段依次递升,但为了防止塑料的过熟分解和制件颜色的变化也可略低于中段,料温配置不当有时会造成卡螺杆故障--螺杆不转或空转,这还可能是注射压力过大或螺杆止逆环(介子)失效造成料筒前端的稀薄熔料向进料区方向反流。
当这些反流的料灌进螺纹端面与料筒内壁间的微小间隙而受到较低温度冷却时,将冷固成一层薄膜紧紧卡在两个壁面之间,使螺杆不能转动或打滑。从而影响加料。
此时,切勿强行松退或注射,建议加料口冷却水暂时关闭,强化升高加料段温度直至比塑料熔点高30~50摄氏度,并同时地出料段温度降低至熔化温度附近,待10~20分钟后,小心地转动螺杆,能转动时才重开机,然后缓慢加料。
注射周期中压力的控制
1. 实际施用的压力应比充满型腔压力偏高,在注射过程中,模控压力急剧上升,最终达到一个峰值,这个峰值就是通常所说的注射压力。注射压力显然要比充满型腔压力偏高。
2. 保压压力的作用:模腔充满塑料后直到浇口完全冷却对闭前的一段时间,模腔内的塑胶仍然需要一个相当高的压力支持,即保压,其具体的作用是:
补充靠近浇口位置的料量,并在浇口冷凝对闭以前制止模腔中尚未硬化的塑料在残余压力作用下,向浇口料源方向倒流。
防止制件的收缩,减少真空泡。
减少因制件过大的注射压力而产生粘模爆裂或弯曲变形的现象。所以保压压力通常是注射压力的50%~60%。
保压压力或时间太长太大的话有可能将浇口及流道上的冷料挤进制件内,使靠近浇口位置上添上冷料亮斑,同时毫无好处地延长了周期。
3. 注射压力的选择
根据制件形状、厚薄选择
针对不同的塑料原料选择。
在生产条件和制件质量标准许可的情况下,建议采用就温低压的工艺条件。
4. 背压压力的调节
背压所代表是塑料塑化过程所承受的压力。有进也称之为塑化压力。
颜色的混和效果受背压的影响,背压加大,混和作用加强。
背压有助于排除塑料件的各种气体,减少银纹和气泡现象。
适当的背压可以避免料筒内局部滞料现象,所以清洗料筒时往往将背压加大。
注射速度的控制
1. 速度高低的影响:低速充模优点是流速平稳,制件尺寸比较稳定,波动较小,制件内应力低,内外各向应力一致性较好,缺点是制件易出现分层结合不良的熔点痕,水纹等,高速充模可采用较低的注射压力,改进制品的光泽度和平滑度,消除了接缝线现象及分层现象,收缩凹陷小,颜色更均匀一致。
缺点是易产生”自由喷射”,即出现滞流或涡流。温升过高,颜色发黄,排气不良及有时脱模困难。粘度高的塑料有可能产生熔体破裂,制件表面产生雾斑,同时也增加了由内应力引起的翅曲和厚件沿接缝线开裂的倾向。
2. 采用高速高压注射的情况
塑胶粘度高,冷却速度快,长流程制件
壁厚太薄的制件
玻纤维增强的塑料
3. 多级调速的应用
由于浇道系统及各部位几何条件不同,不同部位对于充模熔体的流动(特别是速度)提出要求,这就出现了多级注射,我们可以根据制品的形状,对相对薄壁的,形状复杂的部分实行快速充模;
而对于入水口和易烧焦处用低速或中速充模。大部分产品都可以采用低速—高速—中速充模过程,从而达到改变制品表观和内在质量的目的。(文章来源于网络)