查 燕,郑方莉,肖 剑,杨卫民,谢鹏程∗
(北京化工大学机电工程学院,北京 100029)
摘 要: 为提高复合材料注塑件的仿真准确性,基于多尺度联合仿真方法,以汽车发动机正时链条导轨为例,根据导轨纤维配向以及结构应力分布情况,设计了导轨减量化结构,在保证整体应力水平在安全范围内的同时,最大应力降低了12 %,质量减轻了4 %,实现了汽车发动机正时链条导轨的减量化设计。
关键词: 减量化;联合仿真;复合材料;注射成型
前言
数据显示,我国固体废物年产生总量超 1×1010 t,其中废弃塑料约为6. 3×107 t,由于塑料的化学结构稳定,难以自然降解,回收成本过高,不当使用和处置致使环境污染指数递增[1]。针对解决这一现象,减量化理念应运而生。减量化设计的原则是通过巧妙的结构设计,在保证产品强度等安全性能的同时,减少原材料的用量,从源头节约资源,减少废弃物的产生[2],是实现资源有效利用,塑料污染源头防治的有效途径之一。
复合材料作为综合性能优异的轻质材料替代了传统钢材被广泛应用于汽车制造行业,具有质轻、高强度和比模量等优点,其中复合材料的力学性能是由基体和增强相复合后显现的综合特性,但由于纤维和基体在力学性能上相差很大,加之纤维形状和分布的随机性,导致复合材料的宏观力学性能非常复杂[3]。目前,有限元仿真分析被广泛应用在产品设计及性能评价中,但传统的结构分析软件是假设材料各向同性,忽略了由于材料成型工艺所导致的材料各向异性对于结构性能评价的影响,在结构设计中常存在优化盲区、保守设计等局限性,导致产品呈现厚重、系统容积大等问题。为了很好地解决这些问题,多尺度联合仿真成为首要选择。张立强等[4]基于多尺度联合仿真对汽车前罩进行刚度仿真,验证了多尺度联合仿真方法具有更高精度和可靠性。张玉丽等[5]基于联合仿真技术实现了复合材料注塑零件轻量化设计。综上,本文基于多尺度联合仿真技术对复合材料注塑成型进行研究,以汽车发动机正时链条导轨为研究目标,进行汽车发动机正时链条导轨的减量化设计。
1 多尺度联合仿真技术
传统的仿真方法在进行结构性能分析时将实验所得的材料参数直接赋予整体结构,也就是认为制件的材料属性处处相等,从而忽视了成型工艺导致的材料各向异性对于结构性能评价的影响,这样所得到的仿真结果往往与实际不符,甚至存在很大误差[6],最终无法准确有效地对制品进行性能评价。随着复合材料被广泛应用于汽车注塑零件,相比较传统仿真方法,联合仿真技术能够综合考虑复合材料非线性特征、注射成型工艺特点等因素,从而更可靠地预测产品的力学性能。
本研究所采用的多尺度联合仿真技术是通过Mol-dex3D模流分析软件、Digimat 材料建模软件和Abaqus 性能分析软件综合评价,保留注射成型工艺特点,分析制件微观纤维配向及分布与宏观力学性能之间耦合关系,从而更合理可靠地预测制件的力学性能,为进一步优化结构达到减量化设计提供可靠的技术支撑。其中联合仿真技术路线如图1所示,首先通过三维建模软件建成正时链导轨模型导入Moldex3D软件,划分工艺仿真网格,并进行正时链导轨注射成型过程分析,获得导轨的纤维分布和配向信息,并通过Digimat-MAP 模块将纤维分布和配向信息映射到 Abaqus 结构分析网格中;最后将Digimat-MF模块建成的材料模型连同Digi-mat-MAP模块得到的映射模型同时导入到 Abaqus进行结构力学性能仿真分析。

图1 多尺度联合仿真技术路线
2 多尺度联合仿真模型的建立
以汽车发动机正时链导轨为研究对象,导轨的强度和刚度对整个发动机的稳定运行和寿命存在很大影响[7-9],按照多尺度联合仿真技术路线,针对汽车正时链导轨进行联合仿真模型建立及分析,具体流程如下。
2. 1 分析前处理
通过建模软件 Solidworks 建立汽车发动机正时链条导轨的三维模型,如图2所示,并将其导入到模流分析软件 Moldex3D划分工艺仿真网格,如图3 所示。
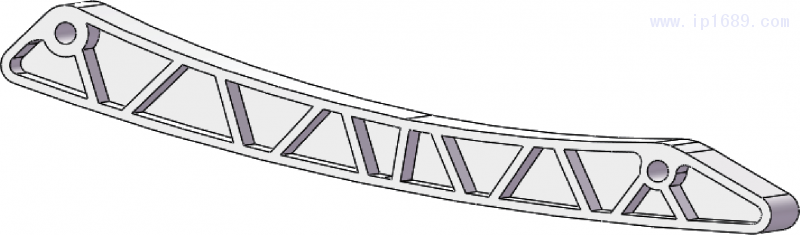
图2 汽车发动机正时链条导轨的三维模型
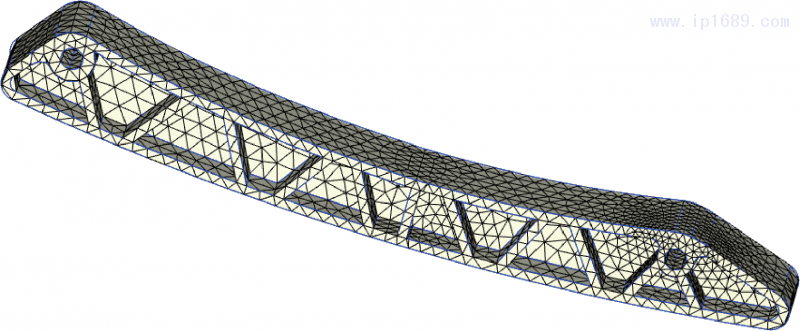
图3 汽车发动机正时链条导轨的工艺仿真网格
2. 2 模流分析
汽车发动机正时链条导轨的材料采用巴斯夫股份公司的Uitramid A3WG6(聚酰胺 66+30 % 玻璃纤维),浇注系统采用一点进浇。根据制件要求与材料属性设置工艺参数:模具表面温度设为85℃,熔体温度为290℃。当控制条件充填体积达到98 %时进行速度/压力切换,保压时间持续8. 3 s,其余参数采用 Mold-ex3D 系统默认。
当熔体前沿以近似相等时间到达型腔的各个末端被视为良好的充填过程,流动波前时间分析结果如图4所示,充填时间大约为1. 227s,整体充填顺畅;其中汽车发动机正时链条导轨的纤维配向分布情况如图5所示,其中纤维配向最大值为0. 99 无限趋近于1,已知纤维配向张量越接近于1,纤维在此区域沿流动方向的取向程度越高,所以该导轨模型的整体纤维配向程度较高,只在肋板和销轴处出现配向张量较低的情况,所以纤维增强效果明显,结构力学性能可能提高。
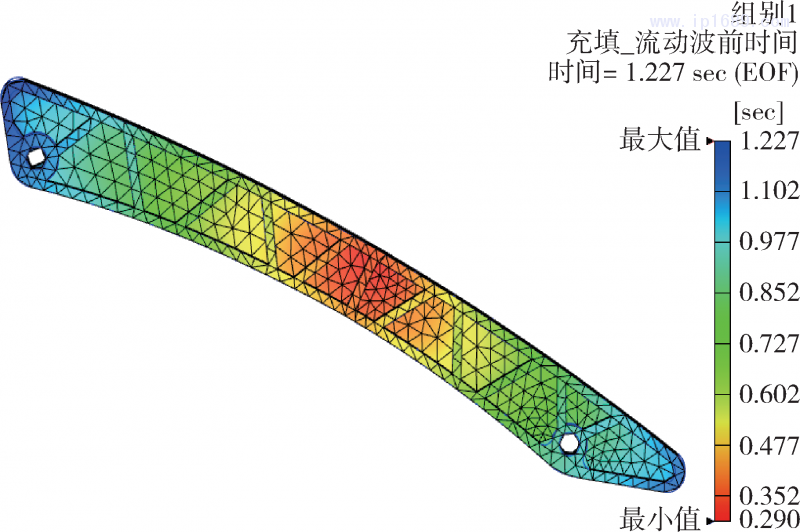
图4 流动波前时间
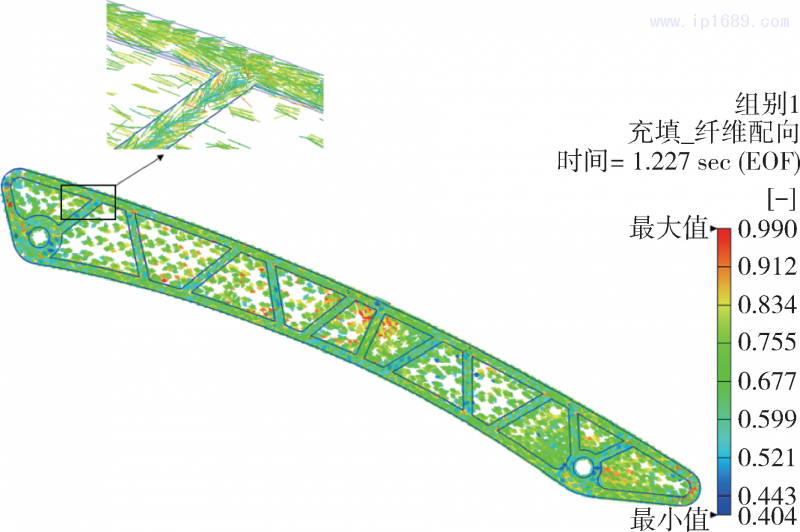
图5 微观纤维配向分布图
2. 3 复合材料模型建立及结构分析设置
在Digimat-MF模块建立起30%玻璃纤维增强聚酰胺66复合材料的材料模型。并通过 Digimat-MAP 模块将模流分析所得的纤维配向和分布信息映射到Abaqus结构分析网格上实现不同类型网格之间的信息交换。最终将Digimat中生成的材料模型及映射模型同时导入Abaqus进行力学性能分析。
如图6所示,通过Abaqus 进行力学性能分析时,导轨的约束条件为:在固定导轨的销轴处约束6个方向的自由度(即完全约束)。由于链条和导轨间的摩擦因数很小,所以在只考虑导轨上惯性力与链条张力的作用,其加载条件为:在接触面加 1~3 MPa 均载。
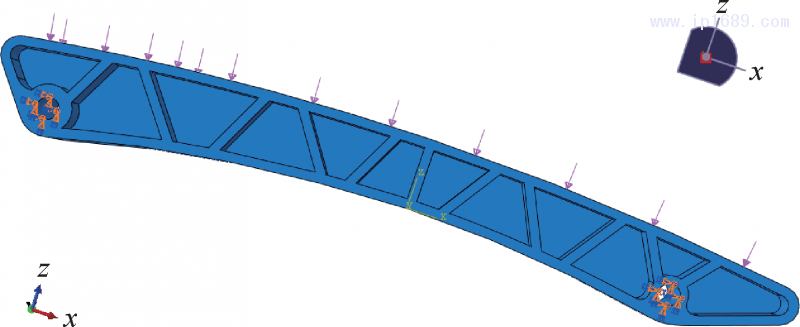
图6 汽车正时链条固定导轨上受力及约束情况
2. 4 计算结果分析
由传统仿真与多尺度联合仿真分析发动机正时链导轨力学性能,其应力分布对比图,如图7 所示,通过传统仿真分析结果显示,应力最大值为103. 1MPa,最大应力位置出现在导轨销轴处,这是因为传统仿真认为材料是各向同性,当结构受载时,其固定部位应力最大。采用多尺度联合仿真模型分析所得结果,最大应力降低为70 MPa,高应力水平集中在销轴和肋板处,其最大应力出现在靠近销轴的肋板内测,由于在充填过程熔体在到达肋板处发生分流导致纤维配向杂乱,如图5 所示,从而在横向加载时力学性能削弱导致应力集中,同时也侧面说明了制件微观纤维配向及分布与宏观力学性能之间对应关系,所以多尺度联合仿真结合了材料成型工艺,更合理可靠的预测了结构的力学性能,已知30% 玻纤增强聚酰胺66的断裂应力为145MPa,所以整体应力水平在安全范围内。
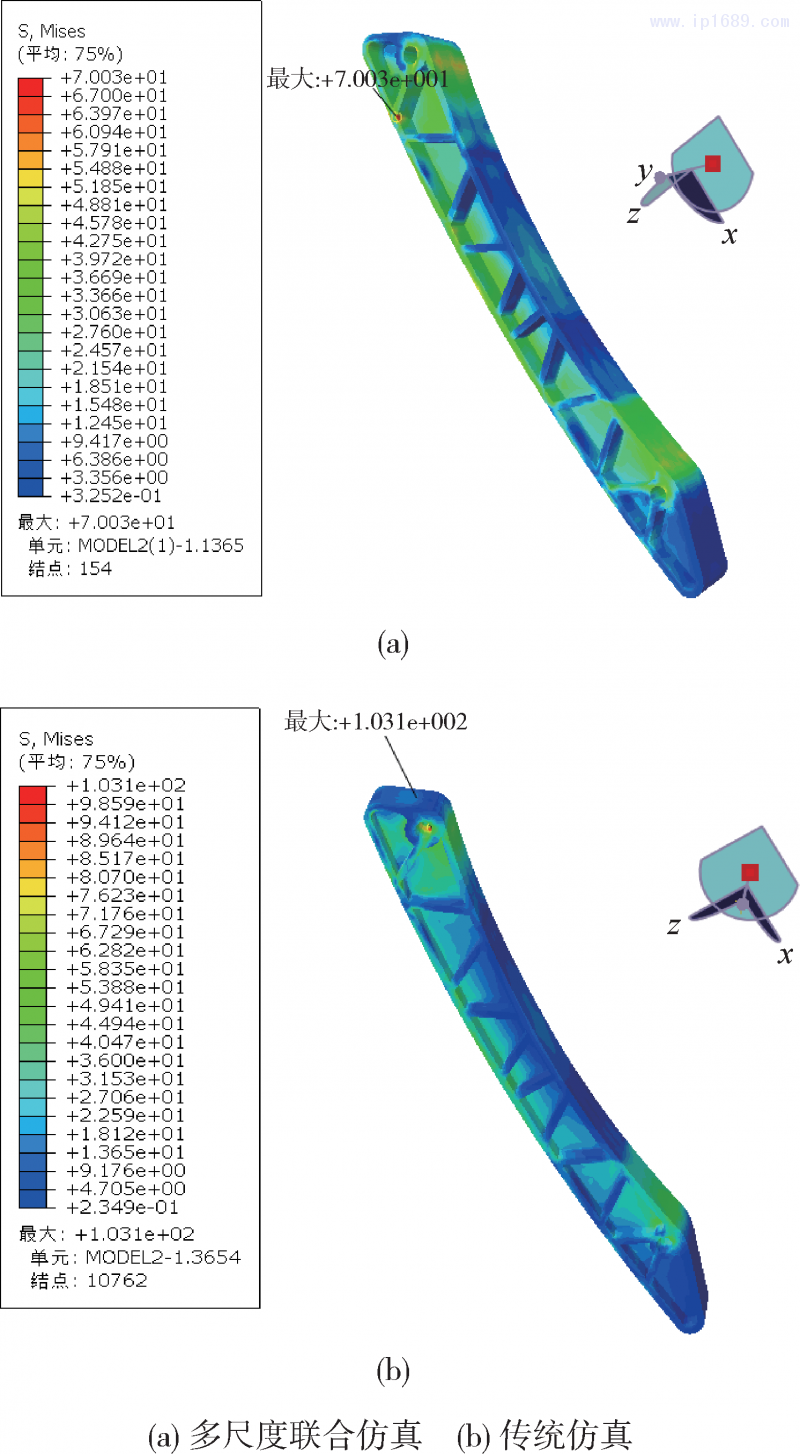
图7 传统仿真和多尺度联合仿真的应力分布对比图
相比较传统仿真方法,多尺度联合仿真技术对于复合材料注射成型制品的性能评价具有更高精度。这是因为多尺度联合仿真规避了传统仿真假设材料是各向同性的这一局限性,保留了注射成型工艺特点,充分考虑了导轨材料的各向异性特征,使材料属性更加贴近实际材料,因此能够更合理可靠的预测制件的力学性能,从而为产品优化以及生产提供更精准的技术支持。
3 正时链导轨结构的减量化设计
由上述分析结果可合理推测该汽车正时链导轨在保证结构可靠性的前提下可以进一步结构优化以达到注塑零件减量化设计的目的。在设计正时链传动系统过程中,固定导轨被设计成内凹形式作用在链条紧边位置,如图7所示,导轨肋板和上壁面接触处分布应力值较大,所以优化方案是将导轨上壁面由原来的2mm增加至3mm,由于导轨下壁面及中间肋板整体应力水平较低,所以可以在导轨下壁面中间位置进一步设计内凹形式以达到减量化设计目标,内凹距离为3. 3 mm,合理缩短肋板长度,结构优化后的正时链导轨,如图8所示。
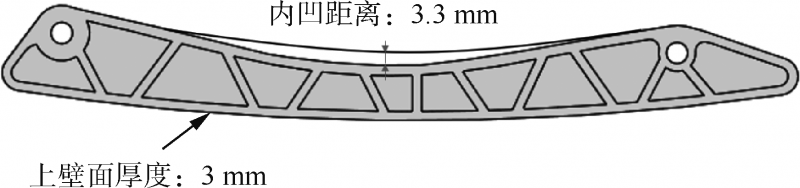
图8 汽车正时链条导轨优化结构
经过减量化设计之后,导轨质量减轻了4 %,优化前后正时链条导轨应力分布对比结果如图9所示,其中低应力水平有小幅度升高,但高应力水平大幅度降低,其中最大应力减小到61. 63 MPa,比原结构降低了12 %,且整体应力水平处于安全工作范围内,满足设计要求。
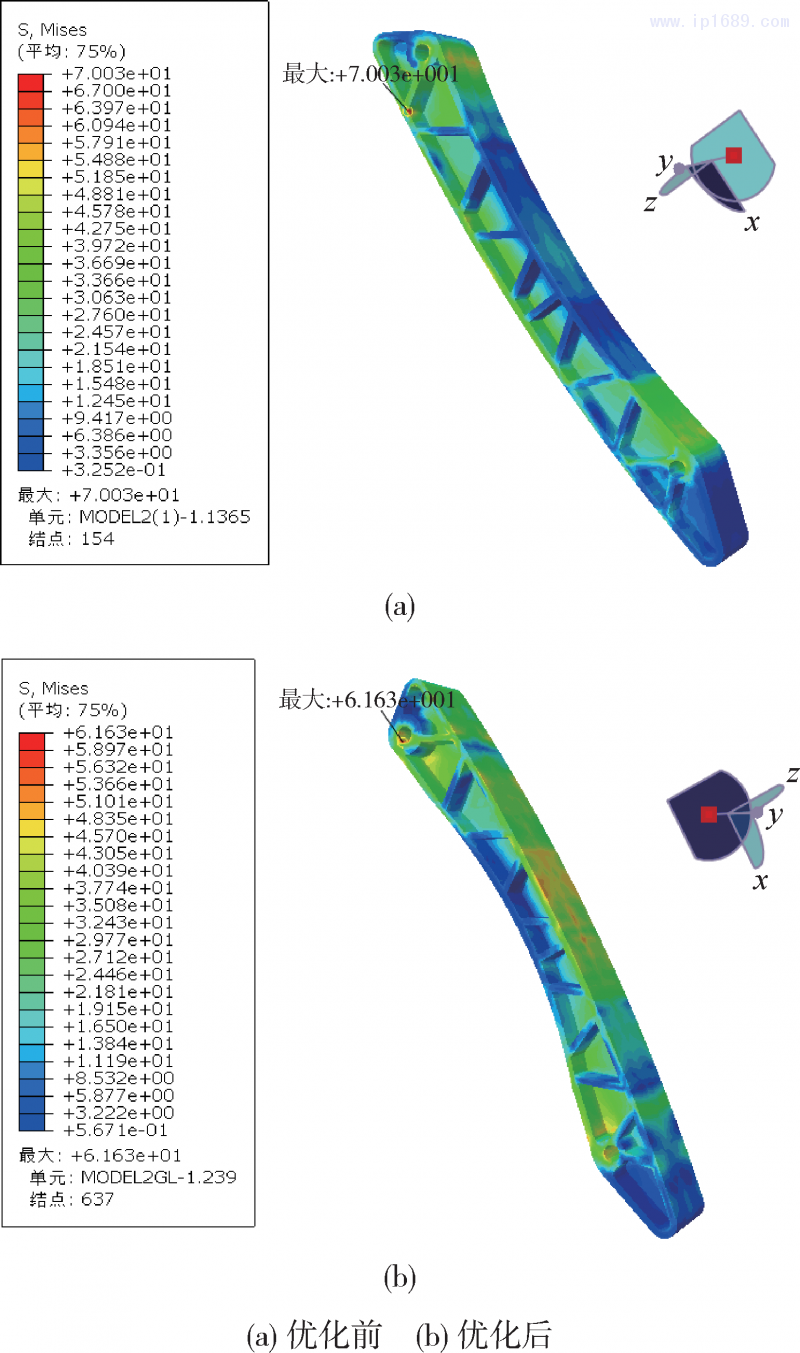
图9 正时链条导轨结构优化前后应力分布对比图
为进一步通过联合仿真技术模拟正时链条导轨减量化设计前后结构的刚度,结果如图10所示,原始设计中正时链条导轨的最大位移量为1. 009 mm,减量化设计后正时链导轨的最大位移量为1. 036 mm,由于整体变形量不大,可以认为优化前后正时链条导轨的刚度没有发生明显变化。所以得出结论是,在满足刚度不变的前提下,提升了结构的强度,并且实现了汽车发动机正时链条导轨的减量化设计。
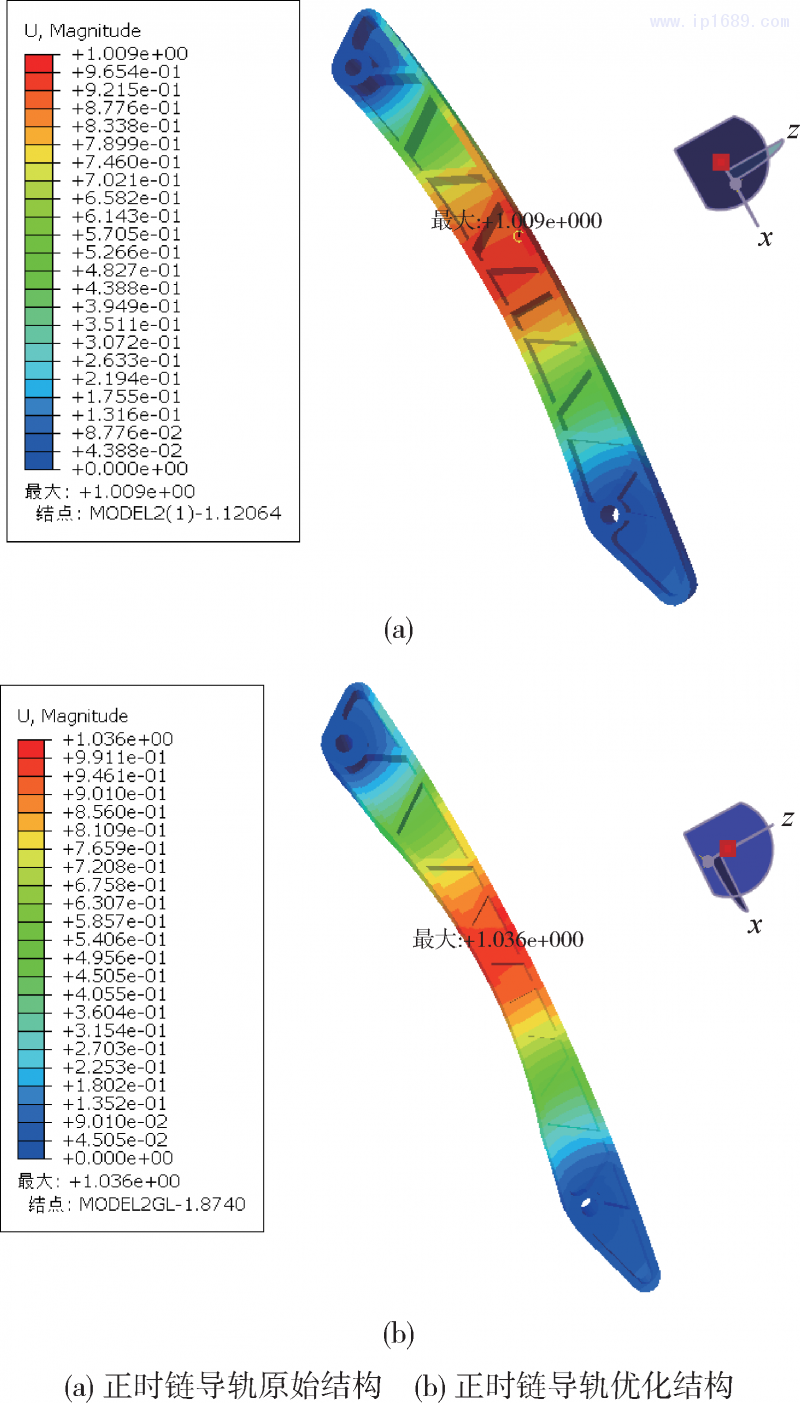
图10 正时链导轨结构变形量云图
4 结论
(1)导轨较高应力集中在肋板处,与注射成型所得结构纤维配向的分布情况相吻合,验证了多尺度联合仿真技术在复合材料注射成型研究中的可靠性;
(2)正时链条导轨减量化设计后,总质量减轻了4 %,最大应力值降低了12 %,保证整体应力水平处于安全工作范围,在提升结构强度的同时,实现了汽车发动机正时链条导轨的减量化设计;
(3)多尺度联合仿真技术保留了注射成型工艺特点,提高了复合材料注塑制品仿真的精确度,这对复合材料注塑制品的性能评价以及减量化设计具有重要意义。
参考文献:
[1] 王 琪,瞿金平,石 碧,等 . 我国废弃塑料污染防治战略研究[J]. 中国工程科学,2021,23(01):160⁃166.
[2] 曾凤彩,王雯婷,王富晨 . 论减量化设计方法在可持续发展战略中的重要性[J]. 设计,2014(02):185⁃186.
[3] 王人杰 . 纤维增强复合材料横向弹性常数[J]. 复合材料学报,1996(02):98⁃104.
[4] 张立强,刘 飞,薛志刚,等 . 基于多尺度联合仿真的汽车前罩刚度分析[J]. 塑料工业,2019,47(04):73⁃77+82.
[5] 张玉丽,邱 炜,傅南红,等 . 基于多尺度联合仿真的注塑制品轻量化设计[J]. 中国塑料,2018,32(09):130⁃134.
[6] 柏 宏,刘 晶,彭 丹,等 . 基于联合仿真分析的复合材料尾门轻量化设计[J]. 时代汽车,2020(14):128⁃130.
[7] 董成国 . 汽车正时齿形链系统设计方法与仿真分析及试验研究[D]. 长春:吉林大学,2010.
[8] 张国勇,任小鸿,张加洪,等 . 汽车发动机正时链条套筒开裂仿真分析研究[J]. 设备管理与维修,2020(6):89⁃91.
[9] 李一民 . 曲轴及正时系动力学特性对发动机 NVH 性能影响研究[D]. 杭州:浙江大学,2012.