贺柳操1 ,肖国华2 ,沈忠良2 ,卞 平3
( 1. 湖南机电职业技术学院机械工程学院,湖南,长沙 410151;
2. 浙江工商职业技术学院现代模具学院,浙江,宁波 315012; 3. 湖北工业职业技术学院机电工程系,湖北,十堰 442000)
摘要 : 结合产品的注塑成型过程,设计了一模两腔两次分型二板模模具结构,单个模腔浇注采用1个侧浇口进行浇注。针对产品脱模困难问题,设计4种脱模机构,实现了难脱模特征的脱模,4种机构分别为定模弹簧型针先抽 芯脱模机构、定模推板斜顶脱模机构、曲连杆驱动旋转脱模机构、定模油缸抽芯机构。曲连杆驱动旋转脱模机构的设计中,运用模具模板的开闭动作驱动弯管型芯进行旋转抽芯,实现了弯管内壁的脱模,合理利用了模具模板的运动功能,降低了机构设计对模架结构的要求,降低了旋转抽芯机构的复杂性,有效地节省了模具制造成本。
关键词 : 斜孔抽芯;前模斜顶;弯管抽芯;结构设计; 注塑模具
0 引言
脱模机构的设计是模具结构布局中机构设计的重点,也是难点[1-5],特别是对于脱模比较困难的产品而言,脱模机构在模 具结构中的布局及机构本身的结构布局,都需要进行较多的结 构创新设计[6-9],文章针对某医疗导流管头脱模困难的实际生产问题,针对性地设计了1种两板式冷流道侧边浇口注塑模具,模具采用假三板模架结构,分两次分型打开。模具结构中,采用弹簧驱动型针实现了产品上斜孔的先抽芯脱模;通过在定模侧设置推板推出前模斜顶机构,实现了产品上型腔一侧倒扣孔的先抽芯脱模 ;利用模具主分型面打开的动力,驱动弯管抽芯机构,实现了产品一端弯管内壁的抽芯脱模;在前模定模板设置油缸抽芯机构,实现了产品一端长内孔壁的抽芯脱模。脱模机构设计中,特别是弯管抽芯机构的设计,机构结构设计新颖,能有效 降低模具的生产制造成本;模具整体布局合理,机构动作可靠,能较好地满足产品的自动化生产要求,具有较好的设计借鉴意义。
1 塑件特征分析
某医疗导流管头产品如图 1 所示,产品材质采用工程改性塑料合金 ABS + PC,缩水率 0. 5%;影响产品脱模的特征包括如图所示的 F1 ~ F5 共5个特征。F1 、F2 为位于左边的2个侧孔,两者都为长距离深孔,且 F1 为阶梯孔,F2 为细长孔;F3 、F4 位于管壁上端,F3 为短距离孔,F4 为斜孔;F5 为细弯管孔,弯管扇形角度27°。以上特征,都是难脱模特征,结合产品的分型设计, 综合分析特殊的分型及脱模机构设计,可以实现产品的自动化注塑生产。
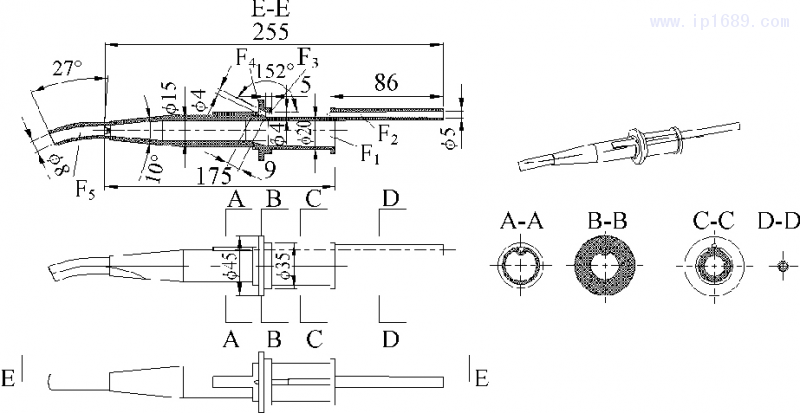
图 1 产品结构(单位 : mm)
F1 ~ F5 -特征
2 分型设计
结合产品的特点,对产品进行如下的布局及分型设计,如图 2 所示,模具采用一模两腔布局,单腔的分型设计为:(1)主分型面采用 PL1 分型线所在的分型面,将产品外壁的成型件一分为二,为上、下成型镶件,即图中所示的 C1 型芯主镶件和 C2 型腔主镶件2 个成型块;(2)在 C1 型芯镶件的侧边分离出 F1 、F2 2 个特征的侧抽芯滑块头镶件 I1 ;实施对 F1 、F2 特征的脱模;(3) 在 C2 型腔镶件上再分割出 I3 、I4 2 个镶件,用于 F3 、F4 特征的成 型与脱模;(4)在 C1 型芯成型镶件和 C2 型腔镶件内再分割出 I1 滑块,实施对产品弯管内壁上的 F5 特征的脱模。产品采用四点 侧浇口方式进行浇注。
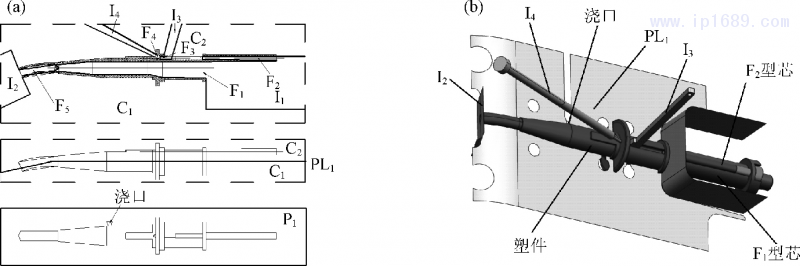
图 2 分型设计
(a)分型分区 (b)分型面 3D 图
F1 ~ F5 -产品特征 PL1 -分型线 C1、C2 -成型镶件块编号 I1 ~ I5 -分割成型镶件编号
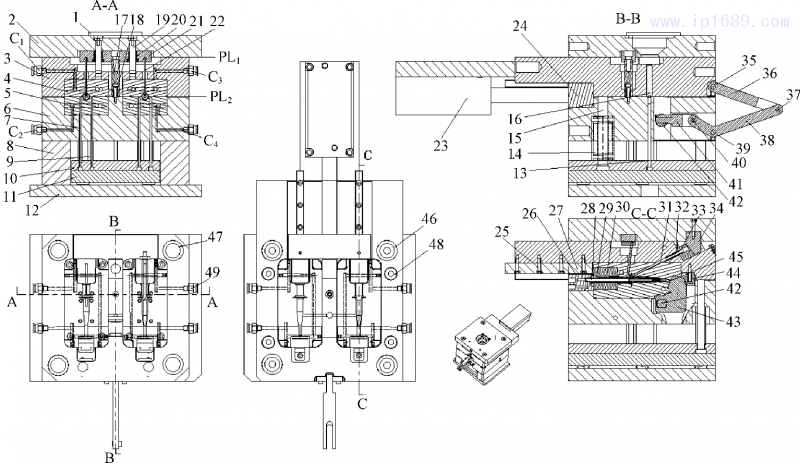
图 3 模具结构
1 -定位圈 2 -面板 3 -定模板 4 -定模镶件 5 -动模镶件 6 -动模板 7 -顶针 8 -模脚 9 -支撑柱 10 -推板盖板 11 -推板 12 -底板 13 -拉料杆 14 -复位弹簧 15 -复位杆 16 -浇口衬套 17 -拉杆 18 -尼龙扣 19 -前模推板导柱 20 -前模推板导套 21 -前模推板 22 -前模斜顶杆 23 -前模油缸 24 -前模滑块 25 -导轨螺丝 26 -滑块镶件 27 -导轨 28 -长型芯 29 -小型芯 30 -侧镶件 31 -斜抽芯针 32 -斜型芯弹簧 33 -斜型针滑块 34 -斜针 滑块驱动块 35-定模转销 36-定模连杆 37-连杆销 38-动模曲连杆 39-动模转销 40- 曲连杆驱动销 41- 曲连杆驱动滑块 42-驱动转轴 43-旋转滑块 44 -旋转滑块锁紧块 45 -弯管型芯 46 -模具导柱 47 -模具导套 48 -定模板限位拉杆 49 -快速水嘴 C1、C2、C3、C4 -水路编号 PL1、PL2 -模具开模面
3 模具设计
依据上述分型设计,模具整体结构如图 3 所示。模具模架采用龙记标准模架 LKM CI 型标准模架。模具模腔布局为一模两腔。模具采用两板模假三板模架结构,分两次分型打开,模具分型面有2个,分别为 PL1 和 PL2 。浇注系统采用冷流道侧边浇口浇注,流道开设于型芯镶件 5 和动模板 6 上,流道直径8mm,侧边浇口为扇形浇口,浇口尺寸为 2 mm ×4 mm × 3 mm;定 位圈 1 和浇 口衬套16采用标准件,其规格分别为 LRB120、SBC20。冷却采用水冷方式,冷却管道直径采用 8 mm 管道;2 个型芯镶件5和2个型腔镶件4上单独开设 2 条水路;长型芯 28 上单独开设水井式水路进行冷却。
排气主要采用镶件间间隙排气位置,镶件间闭合间隙控制 在0. 005 ~0. 015 mm,以便排气。单模腔产品的顶出采用四根顶针7进行顶出,顶针7与型芯镶件5的上端配合段长度12 mm,配合间隙 0. 01~0. 015 mm,顶针中段与动模板6的壁孔间隙单边为 0. 5 mm,底端与推板11的避空间隙为0. 05 mm。模具导向由导柱 46和模具导套47的轴套滑动配合进行导向;导 柱导套有4副,其中,针对模具基准角位置的导柱导套进行了偏心设计,以防止定模、动模装配过程中装错而损坏模具成型零件。成型的冷却过程依靠4条环绕型水路进行,为C1 ~ C4 4 条水路,其中,C1 、C2 对应于第一模腔的冷却,C3 、C4 对应于第二 模腔的冷却;4 条水路的管道直径一样,都采用 8 mm 圆形管道;管道在模板和成型件界面处的密封采用“O”形橡胶圈进行密封,橡胶圈的放置槽开设于模板上,不能开设于成型件上。模具中,定模部分设置3个特殊的斜向脱模机构,动模部分设置1个特殊侧向抽芯脱模机构,可以实现塑件上特殊特征的抽芯脱模;模具动模、定模的动作原理为:模具的开模按 PL1 →PL2 依次 分型打开;结合图 2a 中的分型设计,第一次开模为 I4 斜型芯 (斜抽芯针 31)的先抽芯 ;第二次开模为塑件被 I3 镶件(前模斜 顶杆 22)从定模镶件 4 中顶出脱模,使塑件留在动模镶件5上, 以及动模侧2个特殊滑块抽芯机构的滑块锁紧的解除;模具打开后,动模一侧设置的2个特殊侧抽芯机构的油缸动作,分别驱动I1成型镶件(侧镶件 30)、I2成型镶件(弯管型芯45)实现侧抽芯脱模,塑件的最后顶出为顶针推板推动顶针7 将塑件从动模镶件5上顶出而完全脱模。脱模机构是本模具设计的重点和难点,机构的设计如第 4 节所述。
4 脱模机构
综上所述,为实现 F1 ~ F5 特征的脱模,依据第 2 节所述的 分型布局设计,采用 4 种不同的脱模机构可以实现[10- 15] 。4 种 机构分别为:(1)定模油缸抽芯机构;(2)定模弹簧型针先抽芯脱模机构;(3)定模侧推板斜顶脱模机构;(4)动模曲连杆驱动旋转脱模机构。各机构的 3D 结构图如图 4 所示。
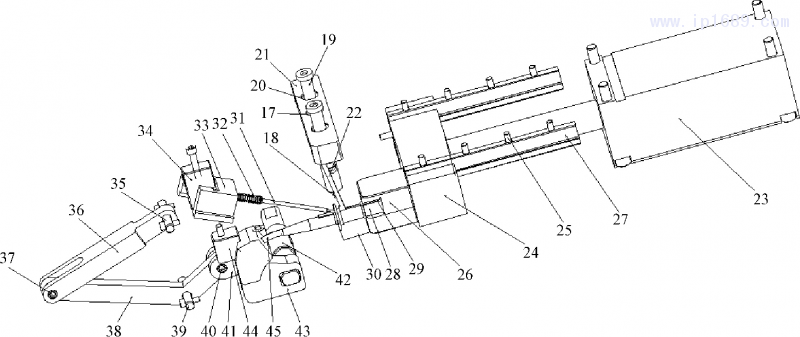
图 4 脱模机构
17 -拉杆 18 -尼龙扣 19 -前模推板导柱 20 -前模推板导套 21 -前模推板 22 -前模斜顶杆 23 -前模油缸 24 -前模滑块 25 -导轨螺丝 26 -滑块镶件 27 -导轨 37 -连杆销 28 -长型芯 29 -小型芯 30 -小镶件 31 -斜抽芯针 32 -斜型芯弹簧 33 -斜型针滑块 34 -斜针滑块驱动块 35 -定模转销 36 -定模连杆 38 -动模曲连杆 39 -动模转销 40 - 曲连杆驱动销 41 - 曲连杆驱动滑块 42 -驱动转轴 43 -旋转滑块 44 -旋转滑块锁紧块 45 -弯管型芯
4. 1 定模油缸抽芯机构
机构用于 F1 、F2 特征的先抽芯脱模,可通过普通型油缸抽芯机构实现,机构整体倒装于定模板3 一侧,其机构组成零件包括件23~件30;长型芯28用于F1 特征的成型,小型芯 29 用于 F2 特征的成型。长型芯 28、小型芯 29 通过侧镶件30 合并安装于滑块镶件26上,通过前模油缸23驱动前模滑块 24,实现了产品上 F1 、F2 特征的脱模。机构的动作在PL1开启前完成,便于塑件从定模镶件4 中被前模斜顶杆22顶出。装配过程中,滑块镶件26 安装于导轨27上,便于滑块镶件26 的灵活抽芯运动,滑块镶件26设置楔紧槽,便于闭模时,动模板上的楔紧块对其 进行锁紧,以防止前模油缸23 的锁紧力不够,导致高压注塑压力对长型芯 28、小型芯29进行冲击时,滑块镶件 26 出现松退,使塑件产生飞边缺陷。
4. 2 定模推板斜顶脱模机构
机构用于F3特征的成型件-前模斜顶杆22,在定模镶件4 内的先顶出侧向抽芯;可通过定模推板推出机构的结构形式实现,机构组成零件包括件17 ~ 件22;机构中,前模推板导柱19通过压板及螺钉紧固安装于面板2上,其下端插入定模板 3 对 应的导柱孔内,以保证其导向的稳定性,其导柱本体通过与前模 推板导套20 滑动配合为前模推板21的运动提供导向。拉杆 17通过螺钉紧固安装于前模推板21上,尼龙扣18通过螺钉紧固安装于动模板6上,两者在闭模时吸紧,当 PL1打开时,尼龙扣18通过吸紧拉杆17拉住前模推板 21,使其保持静止,从而保证 PL1 开模面打开时,前模斜顶杆 22 在定模镶件 4 内无相对顶出 动作。直到模具在 PL2 打开时,由于定模镶件4 对塑件的包紧力小于动模镶件 5 对塑件的包紧力,从而使塑件在 PL2 开模面 打开时,将留于动模镶件5上;与此同时,尼龙扣18 拉紧拉杆17,使驱动前模推板 21 向下推出,前模推板21通过驱动安装于其上的前模斜顶杆 22 将产品从型腔镶件4中同步顶出,从而实 现 F3 特征在定模镶件 4 内的先顶出侧向抽芯脱模。
4. 3 定模弹簧型针先抽芯脱模机构
机构用于 F4 特征的斜向抽芯脱模,可通过带 T 型槽楔紧块 驱动滑块实施斜侧向抽芯的结构形式实现,机构的组成零件包 括件31~件34;斜抽芯针31 套装斜型芯弹簧 32 后,其前端参与 F4 特征的成型,尾端安装于斜型针滑块33上,斜型针滑块33与斜针滑块驱动块34通过T型槽滑动配合联结;机构由斜针滑块驱动块34在模具的PL1 分型面打开时驱动斜型针滑块33实施抽芯动作,完成F4特征的脱模。抽芯动作时,斜型芯弹簧32反弹辅助斜针滑块驱动块34驱动斜抽芯针 31和斜型针滑块33;PL1 开模面闭合时,则由斜针滑块驱动块 34 对斜型针滑块33进行压紧锁紧定位,PL1 打开时,斜型针滑块33在斜型芯弹 簧32反弹推动下由其尾端的滑块限位螺丝挡住而限位,以保证复位时,斜针滑块驱动块34 能准确地插入斜型针滑块33背面的T型槽内,并对其进行复位驱动。
4. 4 动模曲连杆驱动旋转脱模机构
机构用于F5特征的旋转抽芯脱模,可通过连杆驱动弯管型芯旋转实施旋转侧向抽芯的结构形式实现,如图 5 所示,机构的组成零件包括件35~件 45;定模连杆36的上端通过定模转销35铰接安装于定模板3上,定模连杆36的上端可以绕定模转销35的中心 O1 转动;定模连杆 36 的下端、动模曲连杆 38 的上端通过连杆销 37 铰接连接,两者的转动中心为 O2;动模曲连杆 38 的中部通过动模转销 39 铰接安装于动模板 6 上,以动模转销 39 的中心 O3 为转动支撑点;动模曲连杆 38 的尾端通过曲连杆驱动销 40 与连杆驱动滑块 41 的右端铰接连接,两者的转动 中心为 O4 ;连杆驱动滑块 41 的左端制成圆柱侧边削平形状,插入驱动转轴 42 的扁平孔内,使驱动转轴 42 发生转动,驱动转轴 42 的转动中心为 O5;驱动转轴 42 的两端各紧固连接一个旋转滑块 43,驱动转轴42 绕O5 转动,驱动旋转滑块 43 转动,从而实现弯管型芯 45 的旋转脱模。
机构工作原理为:模具在 PL2 开模面打开时,定模连杆 36 被动模曲连杆 38 拉住,使其绕 O1 中心,并朝 T1 方向转动,反之,定模连杆 36 拉动动模曲连杆38,使其绕O3 沿 T2 方向转动, 因而,动模曲连杆 38 可以驱动滑块 41 在驱动转轴 42 的扁平孔 内一边滑动,一边绕中心 O5 沿 T3 方向转动,从而使驱动转轴 42 带动其两端的旋转滑块 43 转动,达到驱动弯管型芯 45 沿 T3 方 向旋转脱模的目的,实现 F5 特征的弯管抽芯脱模。闭模时,由旋转滑块锁紧块 44 对弯管型芯 45 进行锁紧,以防止因其注塑 转动而导致塑件成型失败。
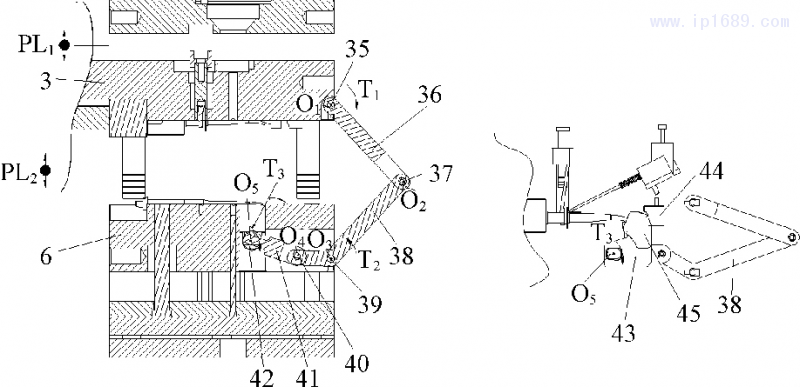
图 5 弯管抽芯机构工作原理
3 -定模板 6 -动模板 35 -定模转销 36 -定模连杆 37 -连杆销 38 -动模曲连杆 39 -动模转销 40 - 曲连杆驱动销 41 - 曲连杆驱动滑块 42 -驱动转轴 43 -旋转滑块 44 -旋转滑块锁紧块 45 -弯管型芯 PL1、PL2 -模具开模面 O1 ~ O5 -旋转中心 T1 ~T3 -转动方向
5 模具工作原理
模具开模时,结合图 3、4、5 所示,产品的脱模动作主要包括 以下几个步骤:
(1)注塑完毕。前模油缸 23 先动作,对长型芯 28、小型芯 29 进行抽芯驱动,先完成 F1 、F2 特征的脱模。
(2)PL1 打开。动模后退,流道废料从浇口衬套 16 中拔出, 留于动模一侧;斜针滑块驱动块34驱动斜抽芯针31和斜型针滑块 33,完成F4特征的脱模。
(3)PL2 打开。动模继续后退,尼龙扣 18 拉紧拉杆17,驱动 前模推板21同步后退,从而推动前模斜顶杆 22,将产品从型腔 镶件4中顶出,从而实现 F3 特征的先脱模。同步地,动模板6 上的动模曲连杆 38 被定模连杆 36 拉住,驱动动模曲连杆38 转动,从而驱动转轴 42 转动,使驱动弯管型芯 45 发生旋转,实现 了 F5 特征的脱模。开模过程中,在 PL2 打开前,模具需满足 F1、F2、F4 特征完成脱离制件的要求 ;PL2 打开后,定模推板斜顶脱 模机构和动模曲柄连杆机构同步动作,完成了 F3 特征的脱模和 F5 特征的脱模。
(4)顶出。分型面完全打开后,注塑机顶杆驱动四根顶针7,将产品及流道废料从型芯镶件5上顶出,实现产品的完全脱模。
(5)复位。复位时,动作过程完全相反,模具闭合,等待下 一个注塑循环过程。
6 结论
结合某医疗导流管头产品的注塑成型过程,设计了一模两腔、4个侧浇口浇注、两次分型二板模模具结构。针对产品多个特征的脱模困难问题,设计了4种脱模机构实现了难脱模特征的脱模。4种机构中,包括前模弹簧型针先抽芯脱模机构、定模侧推板斜顶脱模机构、曲连杆驱动旋转脱模机构、前模油缸抽芯机构;模具脱模机构设计中,特别是曲连杆驱动旋转脱模机构,充分地利用模具模板的开闭动作驱动弯管型芯进行旋转抽芯,实现了弯管内壁的脱模,机构无需另外设计动力机构,合理利用了模具模板的运动功能,减小了机构设计对模具模架结构的要求,降低了旋转抽芯机构的复杂性,有效地节省了模具制造成本。模具布局合理,结构简单实用,机构设计新颖,有较好的设 计借鉴意义。
参考文献 :
[1] 吴晋,李国富,邱梦宁,等.轿车左前灯灯座本体注塑模具结构设计[J].工程塑料应用,2017,45 (10) :70 -75.
[2] 高瑾,周建军.汽车内饰条多行位脱模机构及双色注塑模具设计[J].塑料工业,2016,44 (12) :55 -58.
[3] 张建卿.L10 面条机主体盖前模多重脱模机构及其注塑模具设计[J].塑料,2016,45 (5) :83 -86.
[4] 许傲.斜度头洗发液瓶盖脱模机构及模具设计出[J].塑料,2017,46 (4) :102-105.
[5] 王成.薄壁螺纹弧形抽芯塑件的模具结构设计[J].中国塑料,2014,28 (9) :97-102.
[6] 卞平.热流道双叠层注塑模具设计[J].塑料工业,2017,45 (10) :65-68.
[7] 曹争.自动抽液瓶盖抽芯机构及模具设计[J].模具工业,2017,43 (5) :47-51.
[8] 黄诗君,方耀华.铰链式塑料瓶盖自动卸螺纹注塑模设计[J].工程塑料应用,2005,33 (4) :50 -52.
[9] 汪哲能.医用输液泵体多层式复合脱模机构与注塑模具结构设计[J].工程塑料应用,2017,45 (11) :81 -87.
[10] 张建卿.汽车暖风机下壳体 CAE 优化与模具设计[J].工程塑料应用,2016,44 (5) :65 -69.
[11] 欧阳波仪.汽车仪表罩倾斜式多种脱模机构及其注塑模具设计 [J].塑料工业,2016,44 (9) :70 -75.
[12] 徐新华,郑子军,徐生,等.油缸浮动顶出脱模机构结构优化与注塑模具设计[J].工程塑料应用,2017,45 (5) :85 -90.
[13] 许傲,黄力.医用接插头前模四面抽芯脱模注塑模具设计[J].塑料,2017,46 (2) :110 -113.
[14] 王怀奥,肖国华.熟食机主体壳注塑模具结构设计[J].塑料工业,2017,45 (11) :79 -84.
[15] 苏海云,安珂,郝革红,等.一种新型外抽芯倒脱模结构在车用灯具注塑模具的应用[J].轻工科技,2014,30 (5) :102.