闫竹辉,刘斌
华南理工大学聚合物成型加工工程教育部重点实验室,聚合物新型成型装备国家工程研究中心,广州 510640
摘要:设计了一种一模一腔两板注塑模具用于汽车空调出风口壳体塑件的注射成型。针对汽车空调出风口壳体的使用要求,选用聚丙烯作为注塑材料。根据产品性能及工艺特点的要求,对空调出风口壳体的成型结构特征进行深入剖析,选择采用热流道两点进胶的成型方式保证模腔的可靠充填。针对塑件多处细节特征的脱模难题,设置了多个方向的滑块抽芯机构实现脱模,并针对产品局部无法一次抽芯完成的细节特征,相应地在滑块中设置二次抽芯机构、斜导柱液压组合式二次抽芯机构。此外,在动模侧设有16根圆顶杆、1个斜顶以保证制品顺利顶出。实践证明,设计的模具结构合理,动作可靠,成型的塑件质量良好,可为同类塑件的注塑生产提供有益借鉴。
关键词:汽车空调出风口壳体;注塑模具;二次抽芯机构;模具结构
汽车空调出风口壳体具有引导风向、调节风量等功能,属于整个汽车空调系统中极为重要的一类零件。由于汽车空调出风口壳体需与仪表盘及其它汽车零部件装配,其外形结构复杂,尺寸精度要求高,给汽车空调出风口壳体注塑模具的设计带来诸多难点。笔者以某汽车空调出风口壳体为例,针对不同位置处的细节特征,采取了多个方向的滑块抽芯机构以保证产品顺利脱模,有效解决了汽车空调出风口壳体注射成型等难点。
01 塑件结构特点
某汽车空调出风口壳体结构如图1所示。该塑件材料为金发科技的聚丙烯(PP)TD40,平均收缩率为0.7%。该材料具有耐高温、耐寒、低收缩、耐冲击、加工流动性好等特点,广泛用于汽车、电器、水处理等行业。由UG10.0测得塑件体积为108.9cm3,质量为149.4g,平均壁厚为1.5mm。塑件表面质量要求较高,不能有熔接痕、气泡和银纹。为使汽车空调出风口壳体与仪表盘等其它零件精确装配,要保证尺寸公差为±0.05mm。由图1可知,汽车空调出风口壳体其外形特征复杂,主体外围部分存在接插薄壁、吸气通孔、接插位、盲孔螺柱位、接插条、限位薄壁、定位插孔等特征。此外,空调出风口壳体前端有多段斜槽,内侧有直径为8mm的通孔。这些特征决定了该塑件的成型模具必须进行复杂的内、外侧抽芯结构设计[1–3]。
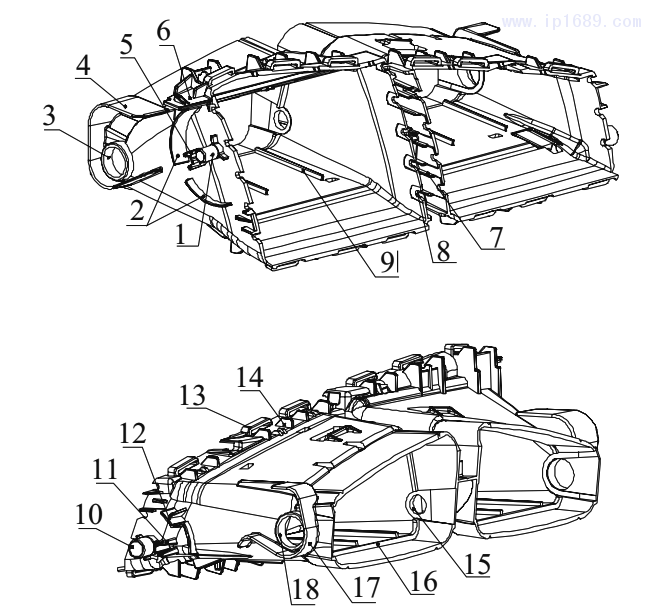
02 注塑模具结构及设计
2.1分型分析
分型面的类型、形状及位置选择是否恰当,不仅直接关系到模具结构的复杂程度,而且对注塑成型质量和生产操作等问题都有影响。为了保证制品的质量要求,使其顺利脱模,选取制品断面轮廓最大的部位作为分型面[4–6]。该分型面可使塑件成型收缩后留在型芯上,且便于抽芯,能保证塑件外观和质量的要求。
基于上述分型设计原则,待产品主分型面设定后,将侧抽芯分型区域模具平面设置为4个侧抽芯方向,即X+,X–,Y+,Y–方向[7],如图2a所示。X+侧抽芯方向所对应的侧抽芯滑块为N4滑块,X–侧抽芯方向所对应的侧抽芯滑块为N7滑块,Y+侧抽芯方向所对应的侧抽芯滑块为N1,N2,N3滑块,Y–侧抽芯方向所对应的侧抽芯滑块为N5,N6滑块,其中N1与N6对应、N3与N5对应共同成型Y方向的两个风口。此外,N1,N3滑块完成了图1中制品上、下共12处特征13定位插孔的成型,N1,N3滑块内部存在制品前端特征8斜槽的二次抽芯滑块,N5,N6滑块内部存在制品内侧特征15内侧通气孔的二次抽芯滑块,N2滑块完成了制品共6处特征7接插条的成型,N4滑块完成了特征12,17,18的侧抽芯,并且N4滑块内部存在二次抽芯滑块用以成型与X轴方向存在角度的特征10,11,N7滑块完成了特征2,3,4的成型,并且N7滑块内部存在二次抽芯滑块用以成型图1中与X轴方向存在角度的特征1,5,如图2b所示。
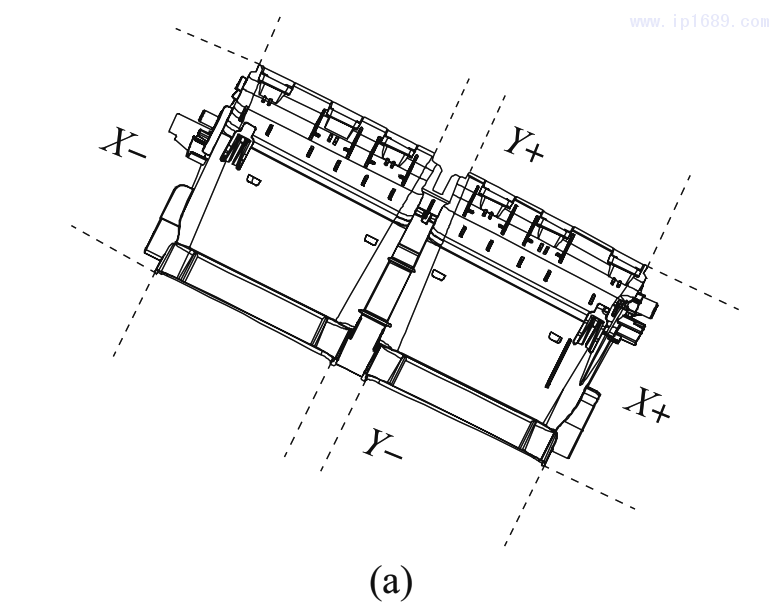
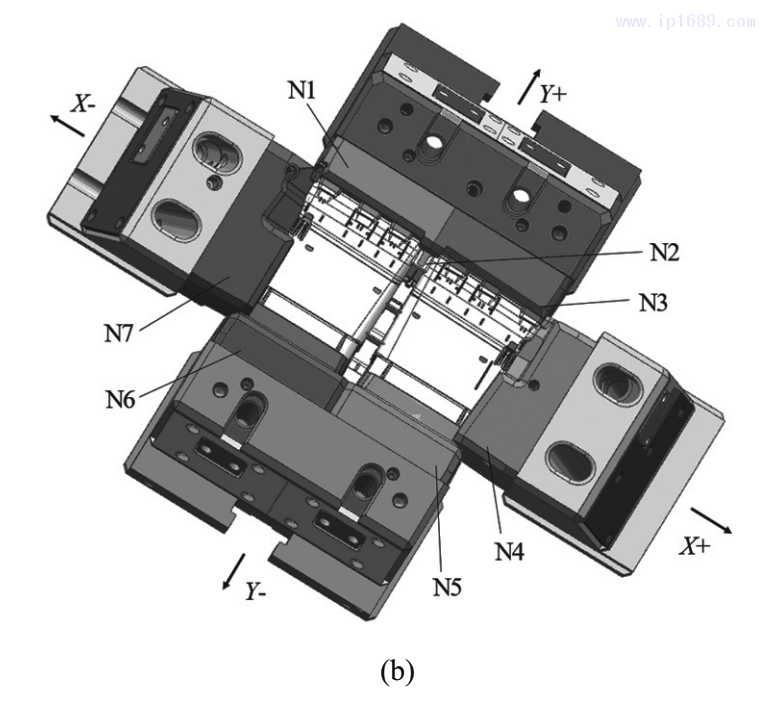
2.2 模腔布局及制品浇注
塑件为中批量生产,由UG10.0测得塑件外形尺寸为 245mm ×113mm×82mm,产品外形尺寸较大,并且考虑到制品四周都存在侧抽芯机构,为避免模具尺寸太大,综合考虑后,采取一模一腔布局较为合适,浇注系统选用热流道两点式成型方式,模具为单分型面注射模。浇注位置依据图3模流分析结果并结合模具结构设置要求来协调处理得到[8],最终浇注系统设计如图4所示。
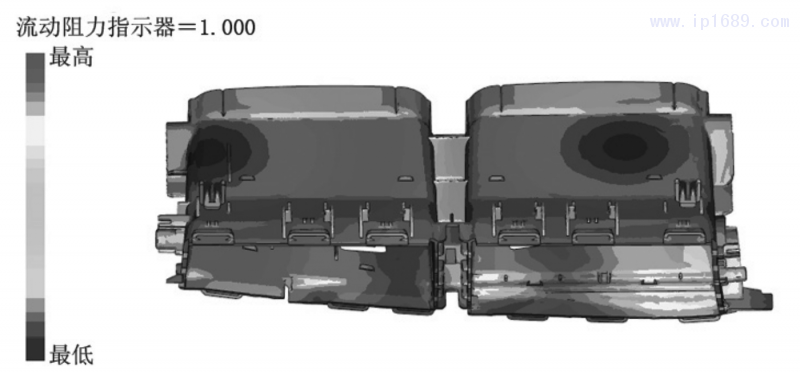
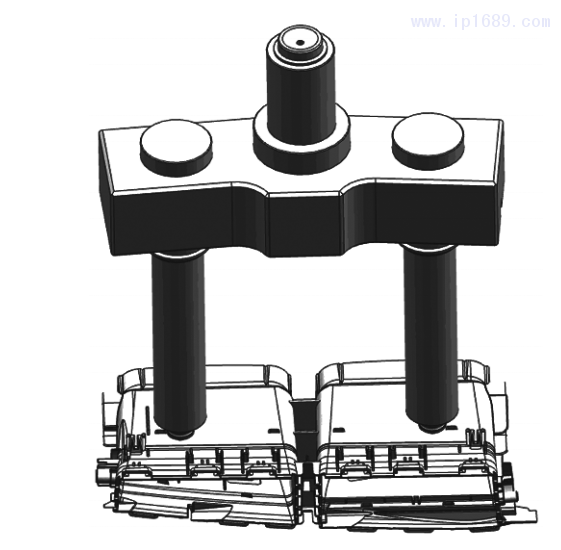
2.3 侧向抽芯机构设计
N2滑块的侧抽芯结构相对简单,常规的斜导柱侧滑块机构即可满足要求。N1,N3,N5,N6的滑块机构因一次抽芯无法实现制品前端斜槽、内侧通气孔特征的抽出,且用以成型Y 方向的两个风口的侧抽芯距离较长,成型面积较大,最终均采用一种斜导柱液压组合式二次抽出结构,以完成制品脱模。而N4,N7的滑块机构因一次抽芯无法实现制品两个侧面上与X轴存在角度的盲孔螺柱位、接插位特征的抽出,且抽芯距较小,最终均采用一种在滑块中设计滑块的二次抽出结构即可完成制品脱模。现针对其中N5,N6,N7的滑块机构进行详细介绍。
(1) 斜导柱液压组合式二次抽芯结构。
采用一种斜导柱液压组合式二次抽芯结构来成型汽车空调出风口壳体的特征15内侧通气孔,其结构示意图见图5。其中,侧滑块的具体连接为N5,N6滑块紧固在滑座Ⅰ上,二次侧抽滑块Ⅰ嵌在N5滑块内,二次侧抽滑块Ⅱ嵌在N6滑块内,侧抽滑块Ⅰ、侧抽滑块Ⅱ嵌在滑座Ⅰ内,且侧抽滑块Ⅰ和Ⅱ分别与二次侧抽滑块Ⅰ和Ⅱ采用燕尾槽配合,配合角度为70°。经测量内侧通气孔深度为2.5mm,为保证塑件顺利脱模,需加上2~3mm的安全距离[9],经计算取整得侧抽滑块的一次抽芯距为12.5mm。
抽芯机构工作原理如下:当模腔打开时,N2滑块、N5滑块、滑座Ⅰ固定不动,定模侧斜导柱Ⅰ驱动侧抽滑块Ⅰ和Ⅱ在滑座Ⅰ中沿Y轴负向滑动,由于N5滑块、N6滑块的限制作用,二次侧抽滑块Ⅰ在侧抽滑块Ⅰ带动下只能沿X 轴正向运动,二次侧抽滑块Ⅱ在侧抽滑块Ⅱ带动下只能沿X 轴负向运动,当侧抽滑块Ⅰ和Ⅱ由位置A运动到位置B时,内侧通孔的一次抽芯动作完成。同时,斜导柱Ⅰ完全脱离侧抽滑块Ⅰ和Ⅱ,定模侧顶锁与B位置顶锁孔接触阻止侧抽滑块Ⅰ和Ⅱ与滑座Ⅰ的再次相对滑动。之后在液压油缸Ⅰ的带动下,整个侧滑块沿Y轴负向运动84.5mm,挡块Ⅰ碰到行程开关Ⅰ触电位置,液压油缸Ⅰ停止运转,二次抽芯动作完成。
(2) 滑块中设计滑块的二次抽芯结构。
采用一种滑块中设计滑块的二次抽芯结构,来成型汽车空调出风口壳体的盲孔螺柱位、接插薄壁、吸气通孔,结构示意图见图6。
2.3 侧向抽芯机构设计
N2滑块的侧抽芯结构相对简单,常规的斜导柱侧滑块机构即可满足要求。N1,N3,N5,N6的滑块机构因一次抽芯无法实现制品前端斜槽、内侧通气孔特征的抽出,且用以成型Y 方向的两个风口的侧抽芯距离较长,成型面积较大,最终均采用一种斜导柱液压组合式二次抽出结构,以完成制品脱模。而N4,N7的滑块机构因一次抽芯无法实现制品两个侧面上与X轴存在角度的盲孔螺柱位、接插位特征的抽出,且抽芯距较小,最终均采用一种在滑块中设计滑块的二次抽出结构即可完成制品脱模。现针对其中N5,N6,N7的滑块机构进行详细介绍。
(1) 斜导柱液压组合式二次抽芯结构。
采用一种斜导柱液压组合式二次抽芯结构来成型汽车空调出风口壳体的特征15内侧通气孔,其结构示意图见图5。其中,侧滑块的具体连接为N5,N6滑块紧固在滑座Ⅰ上,二次侧抽滑块Ⅰ嵌在N5滑块内,二次侧抽滑块Ⅱ嵌在N6滑块内,侧抽滑块Ⅰ、侧抽滑块Ⅱ嵌在滑座Ⅰ内,且侧抽滑块Ⅰ和Ⅱ分别与二次侧抽滑块Ⅰ和Ⅱ采用燕尾槽配合,配合角度为70°。经测量内侧通气孔深度为2.5mm,为保证塑件顺利脱模,需加上2~3mm的安全距离[9],经计算取整得侧抽滑块的一次抽芯距为12.5mm。
抽芯机构工作原理如下:当模腔打开时,N2滑块、N5滑块、滑座Ⅰ固定不动,定模侧斜导柱Ⅰ驱动侧抽滑块Ⅰ和Ⅱ在滑座Ⅰ中沿Y轴负向滑动,由于N5滑块、N6滑块的限制作用,二次侧抽滑块Ⅰ在侧抽滑块Ⅰ带动下只能沿X 轴正向运动,二次侧抽滑块Ⅱ在侧抽滑块Ⅱ带动下只能沿X 轴负向运动,当侧抽滑块Ⅰ和Ⅱ由位置A运动到位置B时,内侧通孔的一次抽芯动作完成。同时,斜导柱Ⅰ完全脱离侧抽滑块Ⅰ和Ⅱ,定模侧顶锁与B位置顶锁孔接触阻止侧抽滑块Ⅰ和Ⅱ与滑座Ⅰ的再次相对滑动。之后在液压油缸Ⅰ的带动下,整个侧滑块沿Y轴负向运动84.5mm,挡块Ⅰ碰到行程开关Ⅰ触电位置,液压油缸Ⅰ停止运转,二次抽芯动作完成。
(2) 滑块中设计滑块的二次抽芯结构。
采用一种滑块中设计滑块的二次抽芯结构,来成型汽车空调出风口壳体的盲孔螺柱位、接插薄壁、吸气通孔,结构示意图见图6。

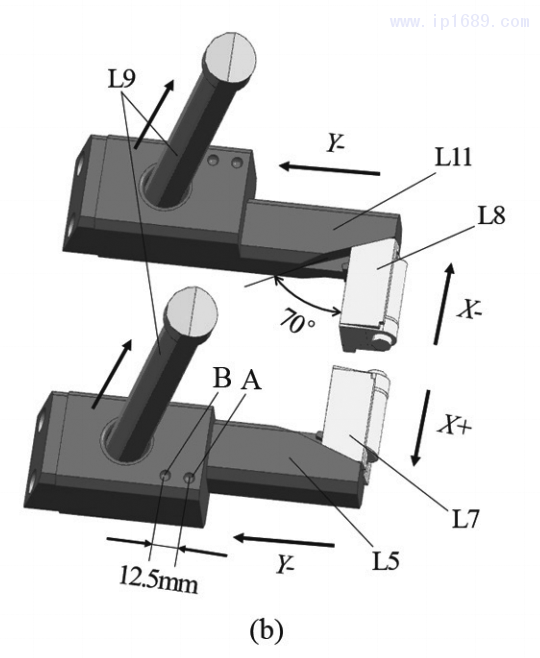
为便于表达内部结构,在图6b中隐去N7滑块,并对滑座Ⅱ做透视处理。其中侧滑块的具体连接为M2镶针嵌在镶块内,M5和M6镶针嵌在二次抽芯小滑块Ⅰ内,镶块嵌在N7滑块内,二次抽芯小滑块Ⅰ嵌在滑座Ⅱ内,且二次抽芯小滑块Ⅰ上有与安装在滑座Ⅱ上的销钉配合的插槽。二次抽芯小滑块Ⅰ的抽芯距应满足盲孔螺柱位、接插位侧型芯中最大的一个,考虑安全距离后,计算取整得抽芯距离为13mm。
抽芯机构的工作原理如下:当模腔打开时,定模侧斜导柱Ⅲ首先驱动二次抽芯小滑块Ⅰ在滑座Ⅱ中沿K方向滑动13mm,滑动距离由安装在滑座Ⅱ上的销钉保证。当滑座Ⅱ上的销钉由C位置移动到D位置时,斜导柱Ⅲ接触到滑座Ⅱ,定模侧顶锁Ⅱ与顶锁孔接触阻止二次抽芯小滑块Ⅰ与滑座Ⅱ的再次相对滑动。之后在斜导柱Ⅱ和斜导柱Ⅲ共同驱动下,整个侧滑块沿X 轴负向移动43mm时,斜导柱Ⅱ和Ⅲ完全脱离滑座Ⅱ,动模侧顶锁Ⅰ与顶锁孔接触阻止滑座Ⅱ滑动,二次抽芯动作完成。
2.4 冷却水道设计
在模具内设置冷却系统是控制模温的有效措施。合理的冷却系统能够实现塑件的迅速脱模,进一步提高塑件的定型质量和生产效率[10]。由于该套模具采用了热流道系统,并且侧抽滑块较长,为保证塑件的均匀冷却,除应在型腔、型芯侧设有冷却水路外,热流道热嘴处、侧抽滑块内部也应设有专门的冷却水路。综合本套模具结构,热流道热嘴处设置了1条冷却水路,在型腔设置了2条,型芯设置了2条,侧抽滑块设置了2条,共7条冷却水路,其位置布置方式如图7所示,进水口为IN,出水口为OUT,非进出口用螺塞堵住,水路直径均为10mm,以实现对塑件的均匀充分冷却。
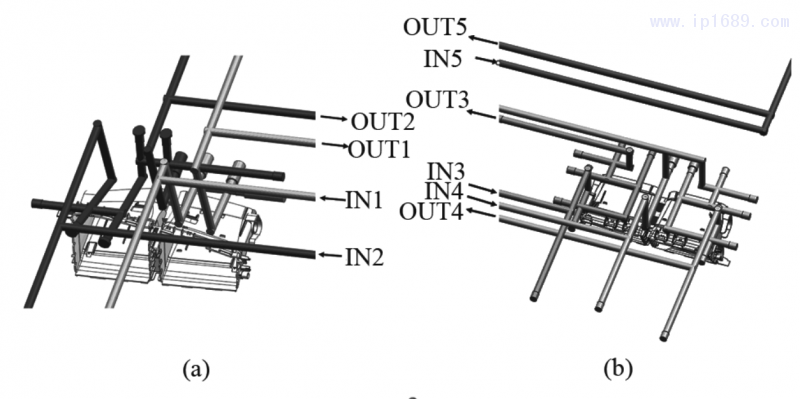
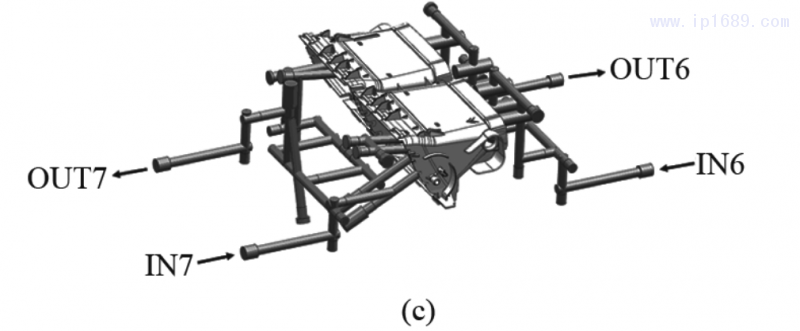
2.5 顶出机构设计
顶出机构是注塑模的重要组成部分,它由一系列顶出零件和辅助零件组成,可以具有不同的顶出动作。顶出零件应有足够的强度、刚度、硬度用以克服制品与模具之间的摩擦力,并且顶出机构的设计应尽量结构简单,降低模具的制造成本。为满足要求,该模具的顶出零件材质均选用SKD61模具钢,并进行氮化处理增加其耐磨性。共设有6根Φ6mm的圆顶针、9根Φ8mm的圆顶针、1根Φ5mm的圆顶针和1个厚度为11mm、角度为5° 的斜顶同时推出塑件,如图8所示。
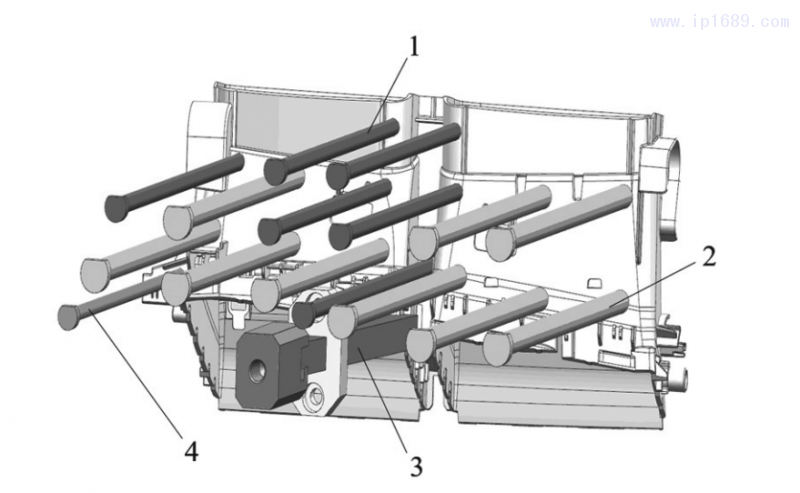
2.6 模具三维装配图
通过上述设计与分析,利用UG10.0设计软件完成的该套模具的三维结构见图9。
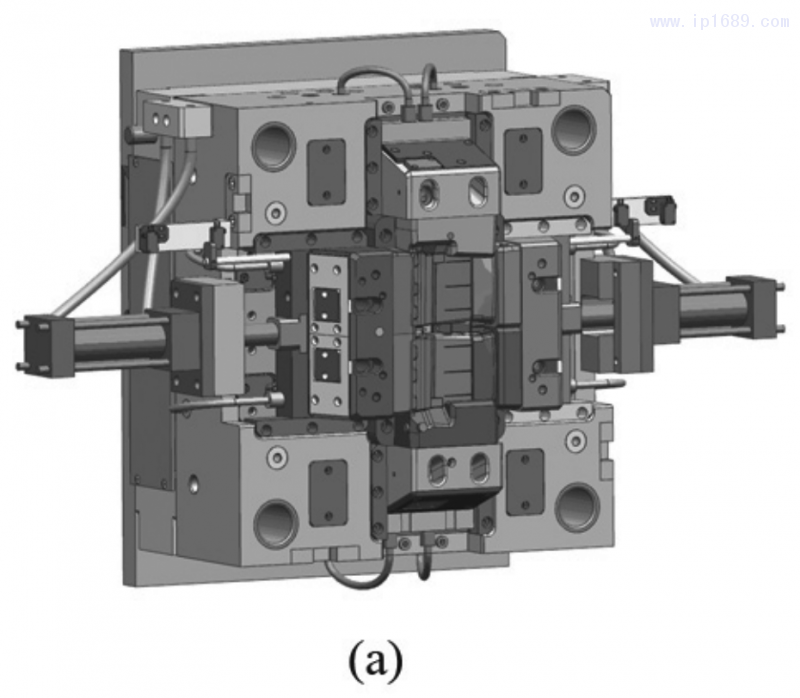
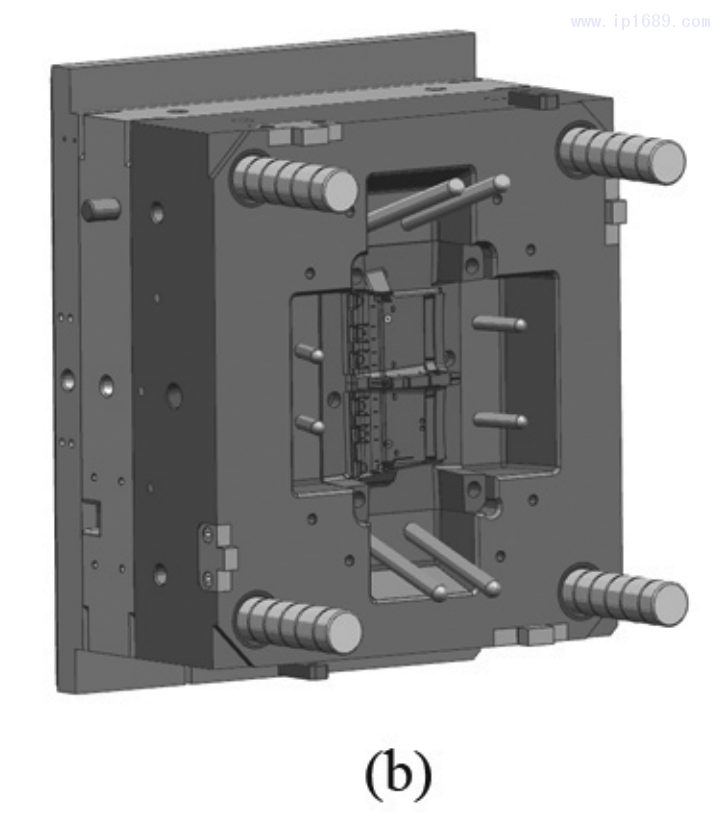
根据给定的注塑机参数及规格,最终选择的模架幅面尺寸为700 mm×550 mm×657mm。模具结构见图10。
模具的基本工作过程如下:注射时,通过热流道系统对模腔进行填充,高温熔体通过点浇口进入模腔,保压冷却之后开模。依靠开模力,斜导柱首先驱动侧抽滑块、二次抽芯小滑块完成图1中盲孔螺柱位、接插位、斜槽、内侧通气孔等特征的一次抽芯动作。随后,N4,N7方向上的斜导柱接触到滑座,斜导柱驱动二次抽芯开始,过程如图6的设计分析所示,N1,N2,N3,N5,N6方向上的斜导柱完全脱离滑座,液压油缸驱动二次抽芯开始,过程如图5的设计分析所示。抽芯完成后,注塑机顶杆推动推杆固定板,从而驱动顶针、斜顶完成注塑件的顶出。合模时,液压油缸先驱动N1,N2,N3,N5,N6 方向上的滑座复位,之后模具闭合,顶出机构由复位杆实现复位,由斜导柱驱动滑座完成最终复位合模,准备下一次成型。
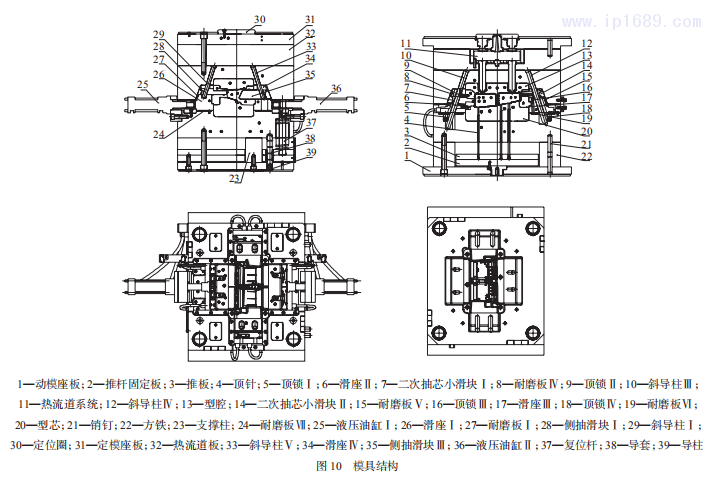
04 结语
汽车空调出风口壳体的结构复杂,不利于脱模,首先对其侧抽芯进行分区设计。综合考虑产品外形尺寸、模具结构等影响因素,采取一模一腔布局设置,浇注系统选用热流道两点式成型方式成型。为保证产品顺利脱模,针对产品局部特征设有斜导柱液压组合式二次抽芯结构和滑块中设计滑块的二次抽芯机构。经实践检验,模具运行过程稳定可靠,成型的制品质量良好,为同类产品的模具设计提供了一定的有益借鉴。
参考文献
[1] 陈黎明,熊建武,沈忠良 . 内壁六面包围框形塑料件脱模机构及模具设计[J].工程塑料应用,2019,47(9):87–93.
[2] 许傲,黄力 . 医用接插头前模四面抽芯脱模注塑模具设计[J].塑料,2017,46(2):110–113.
[3] 黄力 . 侧向与斜向二次抽芯注射模设计[J].模具工业,2011(7):47–49.
[4] 赵战锋 . 汽车中央扶手主壳脱模机构及热流道注塑模具设计[J].工程塑料应用,2019,47(1):82–87.
[5] 黄继战,陈炜,范玉 . 气缸感应开关壳体注塑模具设计[J].工程塑料应用,2019,47(12):79–85.
[6] 杨军,曾霞文,王雪红,等 . 烟花塑料底座多向斜抽芯注射模设计[J]. 模具工业,2016,42(12):45–47.
[7] 张建卿 . 汽车送风机前罩壳多行位注塑模具设计[J]. 塑料,2016,45(3):112–116.
[8] 肖国华,程方启,卢星星,等 . 汽车后视镜面壳热流道二次侧抽芯滑块模具结构设计[J]. 工程塑料应用,2014,42(10):79–83.
[9] 闵志宇,石念峰,张杰,等 . 带复杂曲面结构手机夹注塑模具设计[J]. 工程塑料应用,2017,45(4):83–86.
[10] 孙肖霞 . 冰箱门把手注塑模具设计[J]. 制造技术与机床,2017(5):32–34.